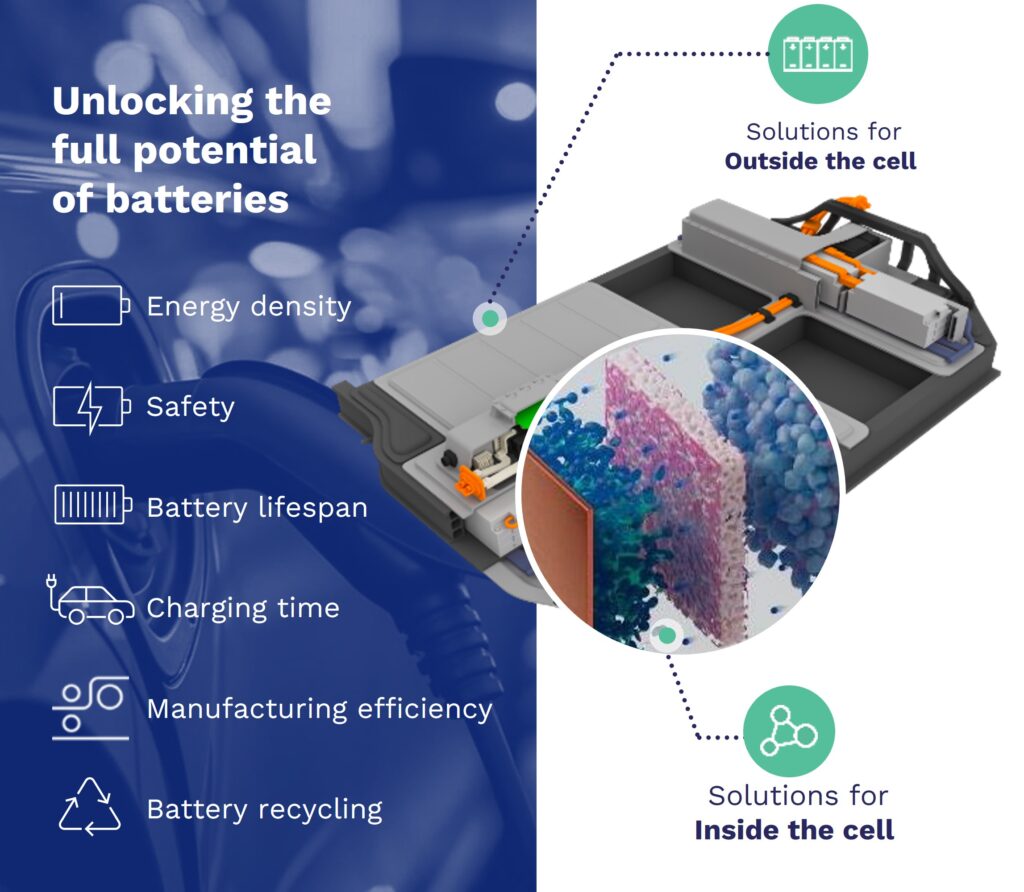
Breakthroughs in the understanding of the chemistry underpinning energy storage systems is powering the shift to electric vehicles.
Collaboration across the electric vehicle (EV) and energy storage system (ESS) value chains is driving innovation. One of the companies which has been part of the evolution of EVs is Arkema, which has been supplying the chemistry used in EVSand ESS battery applications for around four decade.
Through acquisitions and its own research and development (R&D), the company now provides solutions for both inside and outside of the battery cells. It is working with customers and other companies to push the boundaries of lithium-Ion processes and develop new technologies such as solid state, semi-solid and sodium ion storage systems, as well as new manufacturing methods such as dry processing.
Automotive Industries (AI) asked Woldemar d’Ambrières, Global Market Manager, Batteries at Arkema, how the company helps battery manufacturers to improve battery performance and safety.
d’Ambrières: We have been present in this industry since the beginning of lithium ion battery cell production. It started with cell phones, in the form of really small lithium ion battery cells.
And then the technology developed at scale in China, which was the first to tackle cars and busses at much larger scale. In order to scale up we have made a lot of improvements and innovations in our materials.
Our flagship and historic application is electrode binder materials, which are essentially the glue that holds the cell together. We have been working a lot with clients to co-develop binder material solutions in order to need less binder for similar or better performance, which then improved the energy density of the cell.
We also work on the safety of the cells with the development of specific products and solutions to add a separator layer between the cathode and the anode to ensure that there is no perforation of the separator over the lifespan of the cell. Any perforation would result in a short circuit and the death of the cell.
AI: How does material science drives innovation the automotive sector?
d’Ambrières: EV cars are, of course, driven by an electric power train, which is powered by a lithium-ion cell. Basically, the cell is pure chemistry, and for that there is a lot of innovation that relies on the ability of specialty chemical players like us to develop new solutions to improve the performance of the cell.
You improve the performance of the cell by altering the chemistry. This reliance on suppliers of specialty raw materials is something quite new in the industry, which was previously driven by internal combustion engines. Arkema is really well positioned to bring solutions to the EV value chain, as well as ESS applications.
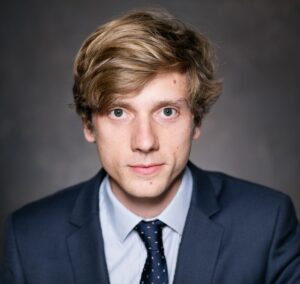
One of the latest innovations which will improve the performance of EVS is the next generation of cells such as semi-solid or all solid-state batteries. Arkema is developing solutions for these applications through the acquisition of a majority share in Proionic, a leading start-up in the production and development of ionic liquids, which are key components for the next generation of lithium-ion batteries.
Due to their combination of electrical conductivity and non-flammability, these ionic liquids are key components in the formulation of electrolytes for the next generation of solid batteries. They can also be used in gel form to make flexible batteries.
We are also developing specific binders suitable for solid state batteries.
Then there are sodium-ion batteries, which are very interesting developments. Arkema has invested in French start-up Tiamat to help them to scale up the pioneering work they are doing in sodium-ion technology, which will benefit the whole market.
AI: What is the importance of developing new materials as well as investing in startup companies for advancing the industry?
d’Ambrières: It is very important for a big specialty chemical company like Arkema to invest in start-ups like Tiamat. The investment will accelerate the scaling up of the technology and deepen our own understanding of the application downstream. By working very closely together we will develop the chemical solutions needed to make this solution competitive and scalable.
Our main objective therefore is not to sell the technology ourselves. Giga factories such as the one planned by Tiamat for 2025 remain downstream in the value chain.
AI: How are those initiatives influenced by market factors across geographies worldwide?
d’Ambrières: Arkema is a global company, with a good balance of activities in Asia, Europe and North America. Our target is to be able to serve our clients wherever they are, with research and development facilities in all three regions.
At present the market leaders are in China in Korea, but there is a lot happening in Europe and North America. We work very closely with the European and North American ecosystems to bring solutions to them and develop some specific technologies for them.
AI: Does Arkema’s portfolio of solutions for EV and ESS batteries cover both inside and outside the cell?
d’Ambrières: Our portfolio includes products for both. For inside the cell we have binders for cathodes and anodes, a comprehensive range of polymers for separator coatings and Foranext® electrolyte salts to increase battery life.
External solutions provided by our Bostik adhesive division include bonding, cell-to-cell and cell-to module assembly and encapsulation. They cater for all cell type assemblies to provide mechanical integrity between the cells and ensure their safety and reliability as well as thermal management. The Bostik solutions are designed to protect battery cells and modules from moisture intrusion, various chemical fluid leaks and exposure to the outside environment.
AI: How close do you work with your customers and other companies to explore both existing lithium-ion processes and new technologies such as solid state, semi-solid and sodium ion?
d’Ambrières: It is very important for us to have a close relationship with the downstream companies which are our customers, to be able to develop and co-develop solutions with them for the current and the next generation of battery technologies.
AI: Are you looking at new manufacturing methods such as dry processing?
d’Ambrières: Yes, absolutely. Dry processing is very attractive for the industry because it helps to reduce energy consumption. After manufacturing electrodes using the current wet process, you need to dry them.
The footprint of the dryers is up to 80 meters long, which represents a big investment in capex and, of course, increases the energy consumption of the plant. The dry process therefore saves the cell manufacturer capex and energy costs while reducing the CO2 footprint of the battery.
Arkema’s support for the dry process includes existing binders for the electrodes, and we are scaling up our R&D facilities in Europe, the US and Asia to provide additional solutions.
AI: What’s next for Arkema?
d’Ambrières: To start, we remain committed to our ambitious growth targets in our battery portfolio, despite some of the headwinds faced by the sector in 2024.
Through the support we provide our clients we have witnessed very good growth in the battery sector. EVs are still selling well in Asia, with more than 30% growth in volumes this year. North America has not been too bad, with double-digit growth in EV sales.
Europe has been a bit slower, but we believe in the mid-and-term potential of this market.
We will also continue to expand our portfolio by developing solutions for clients, especially for the next generation of batteries, such as solid-state sodium-ion technology.
These exciting developments will be on show at the major battery shows in 2025. AI readers are invited to meet us to discuss how we can meet their needs.
More Stories
DuPont materials science advances next generation of EV batteries at The Battery Show
How a Truck Driver Can Avoid Mistakes That Lead to Truck Accidents
Car Crash Types Explained: From Rear-End to Head-On Collisions