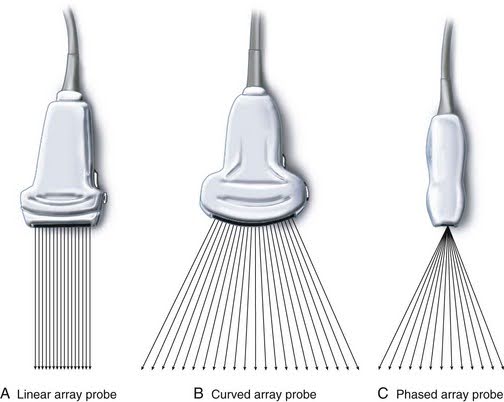
NDT systems enable industries to inspect materials for safety purposes particularly within aerospace manufacturing environments and production facilities. Phased Array Ultrasonic Testing (PAUT) provides its users with precise results while maintaining flexible operation along with enhanced testing speed.
The process of selecting a suitable linear phased array transducer remains difficult because different options display distinct parameters involving frequency levels and element configurations and observation area dimensions. The performance factors for inspections determine weld analysis while also affecting composite material testing along with examinations of difficult geometries.
The guide presents fundamental knowledge for finding the appropriate transducer which meets NDT requirements. Inspection criteria understanding helps both decision quality and produces reliable testing results.
Basic Functionality
A linear phased array transducer functions through separate control of many piezoelectric elements. Independent control of transducer elements lets users generate ultrasonic waves at different angles by maintaining transducer station. An ultrasonic beam direction, focus and shape can be dynamically adjusted through time delay variations in the activation of individual elements. The system enables precise imaging of internal structures because of its ability to generate detailed images.
Benefits of Phased Array Technology
- The system performs inspections with increased speed because it uses electronic beam steering instead of mechanical positions.
- Phased array provides better accuracy because it enables real-time imaging along with exact measurements.
- Complex geometric surfaces become accessible due to the beam steering functionality which enables improved inspection efficiency.
Applications in NDT
Linear phased array transducers serve numerous Nondestructive Testing applications across different industries.
- NDT applications involving weld inspection guarantee the structural integrity of pipelines along with pressure vessels and structural components.
- Material Thickness Measurement: Assessing the uniformity and thickness of materials such as metals and composites.
- Linear phased array transducers detect internal defects which include cracks together with voids as well as inclusions that occur in industrial components
Essential Considerations for Selecting a Linear Phased Array Transducer
When selecting a linear phased array transducer, it’s important to understand the role that various NDT equipment play in ensuring accurate and efficient inspections. For example, frequency and beam angle selection are critical in achieving optimal results.
Frequency
Transducer operating frequency plays a crucial role in defining its performance capabilities during NDT applications. The resolution ability of higher frequencies surpasses lower frequencies yet their penetration depth remains less than lower frequencies that offer lesser resolution ability.
- Linear Phased Array transducers with frequencies exceeding 10 MHz will detect small flaws while maintaining strong scanning capabilities of thin sections.
- The 5-10 MHz Medium-Frequency Transducers remain suitable for standard inspection activities.
- Low-Frequency Transducers (1-5 MHz) are Ideal for inspecting thick or highly attenuative materials.
Beam Angle
The width of the emitted sound waves from the transducer determines its effectiveness for detecting flaws that occur in various directions. The choice of appropriate beam angle benefits detection of defects to the fullest extent.
- Narrow Beam Angles (0-30 degrees): Suitable for subsurface defect detection and straight-line inspections.
- The detection of welds and different depth-based flaws works best with transducer beam angle settings between 30 to 60 degrees.
- A wide beam angle range from 60 to 90 degrees enables the detection of flaws on surfaces and immediately beneath them.
Size and Shape of The Transducer
The proper geometry of the transducer device determines how well it connects to the test material during inspection.
- Small, Flexible Transducers: Best for inspecting components with limited access, such as inside pipes or tight corners.
- Larger Transducers: Provide broader coverage for flat surfaces and large components.
Material Compatibility
The selected transducer depends on the test material. Wave propagation behavior varies among different materials because each substance exhibits its own acoustic properties.
- Metals Require transducers with good penetration and sensitivity.
- Composites testing requires sensors with high resolution abilities to reveal delamination together with voids inside components.
- Plastics receive better wave transmission when lower-frequency transducers are used.
Resolution and Sensitivity
When high-precision applications demand detection the transducer needs full resolution capabilities and extreme sensitivity levels.
- The detection of small flaws becomes possible with high-resolution transducers which produce detailed imaging results.
- High-Sensitivity Transducers are Useful for low-contrast defect detection in difficult materials.
Aligning The Transducer with Specific NDT Needs
Weld Inspection
A transducer which performs effective weld inspection needs to possess several characteristics:
- Medium to High Frequency (5-10 MHz) helps producer detect small weld flaws effectively.
- The device provides a flexible beam angle mechanism which allows users to inspect welds at any position.
- Findings show that its compact size makes the transducer easily accessible within limited areas.
Thick Materials vs. Thin Materials
- Thick Materials (e.g., steel plates, castings): Require lower-frequency transducers (1-5 MHz) for deeper penetration.
- The examination of thin materials including aluminum sheets and pipelines works best with transducers having frequencies above 10 MHz for superior resolution capabilities.
Complex Geometries and Curved Surfaces
Flexible transducers together with Variable Beam Steering provide effective detection of defects on components with diverse curved and irregular surfaces.
- Flexible Transducers accommodate surface variations.
- The Variable Beam Steering functionality safeguards defect detection by maintaining consistent results.
- Custom Wedges serve to enhance both touch between transducer and material surface and signal transmission effectiveness.
Considerations For Practical Use
Ease of Handling and Portability
The optimal transducer used for field applications needs to fulfill the following criteria:
- The transducer should have lightweight ergonomic features that reduce operator fatigue.
- Wireless or Easily Connected for better mobility.
- The device includes features for efficient setup to enhance practical operational procedures.
Durability and Maintenance
The rough exterior casing safeguards the instrument from physical impacts together with demanding environmental conditions.
- Waterproof and Oil-Resistant Designs: Enhance longevity in industrial settings.
- Regular Calibration and Care: Ensures consistent performance over time.
Compatibility with Equipment
- You should check that the transducers work with current NDT instruments and software that already exist.
- The system requires verifying that cables and connectors follow the specified system requirements.
- A wide range of software compatibility options should be considered when selecting transducers to facilitate simple operational integration.
Conclusion
To achieve successful NDT outcomes one must choose a linear phased array transducer while assessing combinations between its frequency range and beam angle along with size demands and material adaptability together with operational convenience requirements. The understanding of these vital characteristics will help improve both performance and accuracy and efficiency of your inspection processes. Reliable results derive from choosing a linear phased array transducer which perfectly aligns with the requirements of the particular application during weld testing or material thickness evaluation or flaw detection procedures.
More Stories
Professional vs. DIY Tinting: What You Should Know
New updated edition of “PXIMate” reference guide for T&M engineers available from Pickering Interfaces
5 Mistakes That Can Ruin Your Car Accident Claim