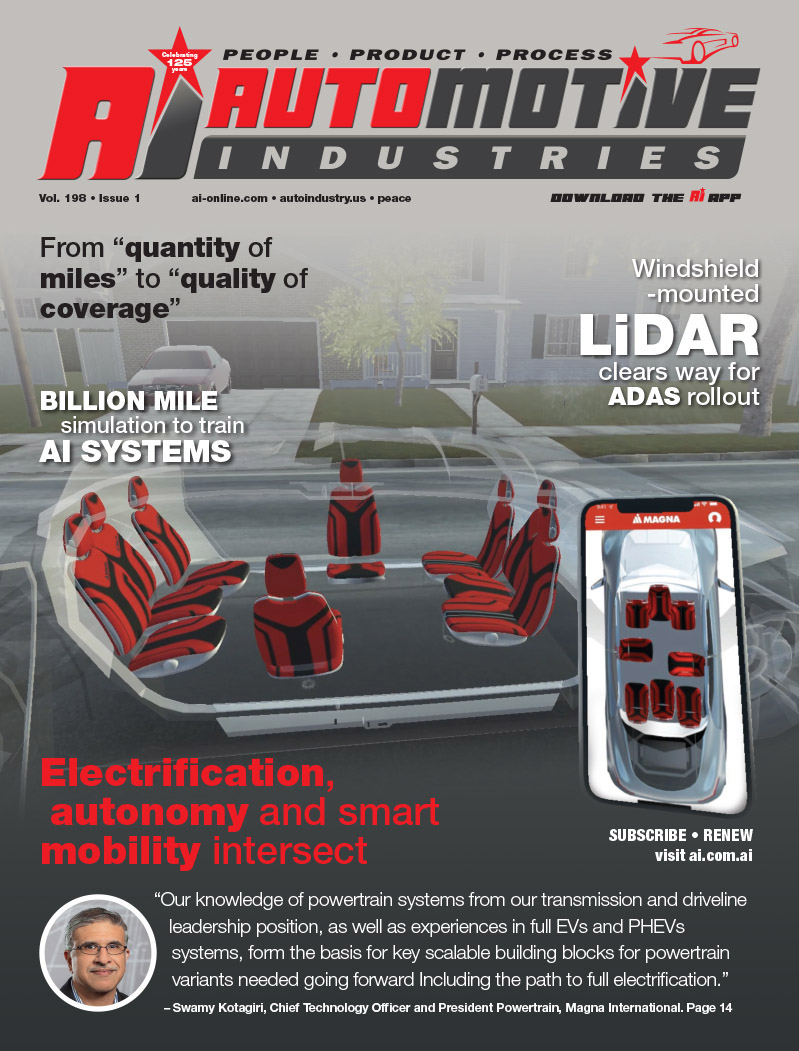
Renault F1 Teams extraordinary back-to-back victories in the FIA Formula One Drivers and Constructors World Championships demonstrate the teams exceptional skills both on and off the track. The team of composite design engineers and technicians who designed and manufactured the R25 chassis were a significant part of that excellence, according to Steve Luby, president and CEO of Vistagy. Their rapid development process and innovative use of composite materials for the chassis serves as an example to automotive companies as they explore methods of incorporating composites into commercial automotive designs.
Racing to excellence
The design team at Renault was required to meet strict specifications for the R25 front wing and chassis, among them ensuring that the parts would be strong and lightweight. But the front wing had complex curves that could cause unexpected shifts in plies as they were laid up, resulting in weak spots. The team also needed to make the parts as rapidly as possible, and in the case of the chassis, that would be difficult. The chassis was a typical composite “sandwich” with inner and outer skins made up of woven laminated plies. Lay-up for the outer skin alone involved more than 200 plies.
Tools in Vistagys FiberSIM software for composites design and manufacturing system enabled Renault engineers to simulate ply lay-up on both parts to determine an optimum ply lay-up that ensured part strength, according to Luby. It also enabled them to automatically generate flat pattern data for the ply shapes and laser projection data to guide ply lay-up. Renault F1 Team engineers documented a 30% reduction in the time needed to create flat pattern templates and a 62% increase in the rate of ply lay-up.
FiberSIM was a key ingredient in enabling Renault F1 Team to meet their goals in composites design. The teams success in finding the best means to make the strongest parts in the shortest time is an example of how automotive OEMs and suppliers would benefit from taking a fresh look at using composites to manufacture their products.
The next challenge: composites in commercial cars
Composite materials, according to Luby, offer a number of design advantages to automotive designers: They are strong, corrosion resistant, ultra-light, and they offer excellent fatigue resistance compared with most metals. Composites offer designers the opportunity to reduce part count by combining old assemblies into a single, more complex but efficient part. They allow a wider range of shapes than steel does, giving designers the chance to create new and innovative products. And they can even be manufactured with attractive colors and surfaces, eliminating the need for painting processes.
Traditionally, the commercial automotive industry has confronted several practical challenges to the use of composite materials in large-scale production:
– High cost of materials
– Time-consuming manufacturing processes
– High perceived risk of not achieving performance specifications
– Lack of experience designing for composite materials and processes
For these reasons, the significant use of composites in commercial vehicles has seemed like a faraway dream. But innovative companies, lured by the benefits that composites promise, have been chipping away at the challenges. Today, we are closer than ever to widespread use of composites in the automotive industry, because of:
More competitive materials cost: The price of steel is going up, but the cost of composites, once high, is coming down. For instance, materials engineers have taken a new look at carbon-fiber composites common in aerospace and have achieved significant savings by introducing new material forms such as no-crimp fabrics (NCF) and intermixing high-cost carbon and less-expensive fiberglass fibers in the material.
Emerging manufacturing processes: Evolving technologies such as sheet molding composites and resin transfer molding, and new processes such as resin film infusion offer manufacturing strategies that are more cost effective than steel at production volumes ranging from 10,000 to 100,000 units per year. Specifically, the initial tooling costs of composite materials are considerably less than those in some traditional metals processes such as progressive die stamping, for which a single part frequently requires multiple tools. Clearly, composite materials arent just for specialty, high-performance sports cars any more.
Reduced Risk. More and more, finite-element-analysis tools and other software can assess the strength of composite designs prior to testing. As the Renault F1 Team has shown, FiberSIM software can simulate the as-manufactured part, confirming part strength and enabling designers to verify manufacturability. The wealth of experience that has come out of composite designs for racecars, concept cars, and low-production automobiles is providing greater comfort with these materials.
Increased expertise: Composite materials are following the lead of other technologies, such as electronic ignitions and computational fluid dynamics (CFD) software, that established a foothold in the racing world and then moved into the commercial industry once they were better-known quantities. For a number of years, composites have been a popular material for concept cars.
The 2000 Chrysler/Dodge Viper GTS/R, for example, sported a one-piece, carbon fiber body. The 2005 Mercedes-Benz Vision SLR goes it one better, featuring a body that includes fiber-reinforced composites and carbon fiber bucket seats.
Given these changes, it seems that we are on the verge of being able to create composite parts in higher production volume for the automotive industry.
Navigating the future
A major reason that Renault F1 Team achieved success with composites is that they didnt simply swap out steel for a new material. Instead, they explored the unique characteristics and capabilities of composites. As a result, Renault designed the best racecar parts that the materials could produce. Mainstream automotive engineers are well aware of the design freedom that composite materials provide. However, designers need the right tools to effectively use composites, inexpensively and without risk, he says.
FiberSIM software, which can predict the manufacturability of composite parts, enables commercial automobile designers to optimize car parts and to minimize design and manufacturing costs. FiberSIM provides engineers with quick, accurate feedback as they explore these new materials and processes.
The ability to design rapidly for composite materials will help produce highly innovative vehicles for popular niche markets. Once these tools, materials, and processes have proven out in the niche markets, they will quickly migrate to high-volume commercial automotive production. Each new composite design will expand knowledge and promote technology and production breakthroughs in the industry.
Companies that pursue composites aggressively will, like Renault F1 Team, race toward the winners circle, according to Luby.
More Stories
8 Best Plastic Welding Techniques for Automotive Manufacturing
5 Big Reasons to Choose LED Bulbs for Your Car Headlights
How much does it cost to ship a car on Amtrak Auto Train?