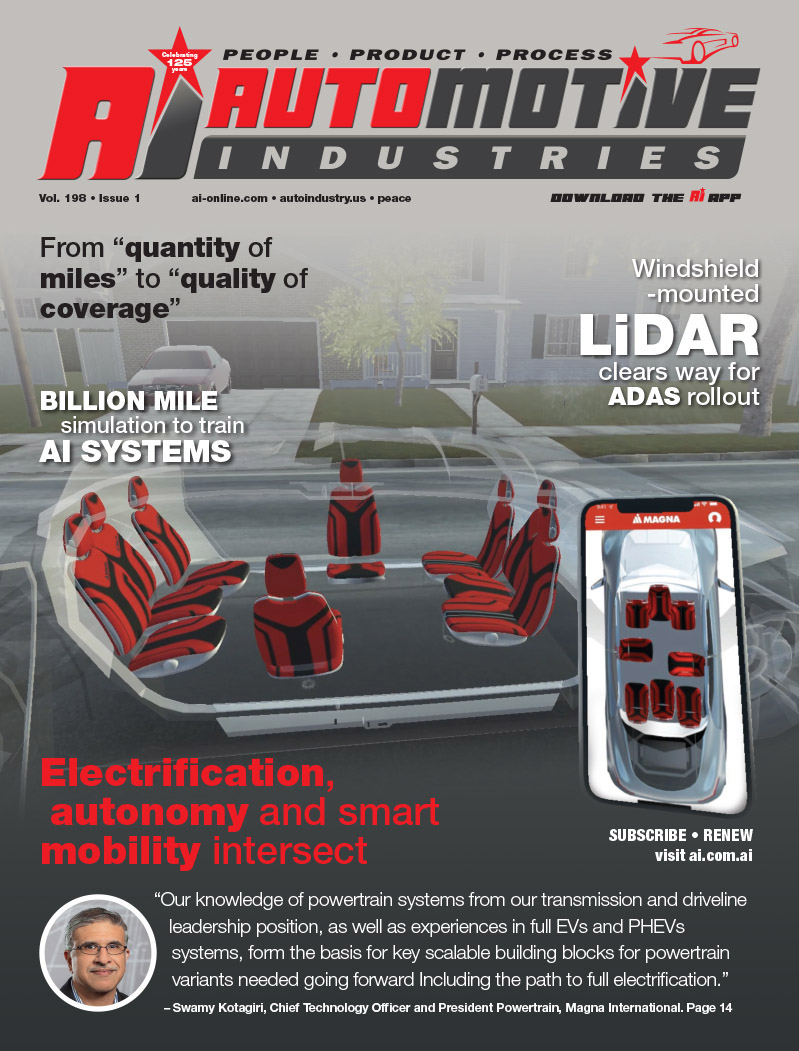
Early this year, Chrysler LLC awarded specialty glass and ceramics manufacturer Corning Incorporated its 2007 Chrysler Supplier Pentastar Award for excellence in supplying their ceramic substrates. “Corning is honored to receive this prestigious award from Chrysler. For more than 35 years we have worked together to combine Corning’s expertise in materials science and manufacturing with Chrysler’s engineering knowledge to deliver advanced exhaust after-treatment systems. We look forward to continuing our collaborative relationship with Chrysler and enabling the company to meet tightening emissions regulations well into the future,†said Thomas Appelt, vice president and general manager, Corning Automotive Technologies.
The company invented an economical, high-performance cellular ceramic substrate in the early 1970s that is now the standard for catalytic converters worldwide. Ceramic substrates are the heart of automotive catalytic converters. In 1978, Corning developed the cellular ceramic particulate filter to remove soot from diesel emissions. In addition to mobile emissions control products, the company manufacturers cellular ceramic supports which are used in stationary catalytic systems such as those used in industrial applications.
Countries around the world are working to improve air quality by establishing tighter emissions regulations. Global adoption of new and tighter regulations will, in turn, create future growth for Corning’s emissions control products. To help meet demand, the company has manufacturing locations around the world, including North America, Germany, China, and South Africa. In 2007, Corning completed the expansion of its clean-air products facility in China. The Corning Shanghai Company Ltd, which manufactures light-duty ceramic substrates, spent USD 15 million to increase its manufacturing capabilities in order to meet global demand.
“The advanced ceramic substrates manufactured at CSCL help our customers meet tightening emissions regulations. In addition, our highly skilled sales and engineering teams provide technical expertise to help design, model and test emissions control systems that enable our customers to comply with global requirements and achieve first-class emissions system performance,†said Appelt.
Corning’s advanced ceramic substrates are robust, monolithic products that deliver high performance and reduced emissions. In September 2007, Corning introduced its Celcor® 600/2 substrate, a next-generation ceramic substrate for light-duty gasoline and diesel-powered vehicles. With its ultra-thin walls, the new substrate enables reduced fuel consumption and increased engine power through low exhaust system back pressure.
Corning also manufactures particulate filters under the brand name DuraTrap® that are used in systems to remove particulate matter (soot) from diesel exhaust emissions. These filters have a cellular structure with individual channels open and plugged at opposite ends. Exhaust gases enter the open end, flow through the pores of the cell walls, and exit the filter through the adjacent channel. Soot particles are too large to flow through the pores, and they collect on the channel walls. Periodically, the filter is regenerated to consume the soot and clean the filter.
Automotive Industries spoke to Thomas Appelt, vice-president and general manager of Automotive Technologies at Corning.
AI: Please tell us a little about Corning’s advanced cellular ceramic substrates and diesel particulate filters for automotive manufacturers.
Corning created ceramic substrates in the 1970’s in response to the U.S. Clean Air Act. At the time we were trying to sell glass windshields to automakers but they weren’t interested in expensive windshield glass. They had a different challenge. They were concerned with meeting the Clean Air Act that set emissions requirements on 1975 model cars. They asked us if we could help. We did what Corning has repeatedly done throughout its 157 year history. We rolled up our sleeves and got to work.
As a result of our materials, process and manufacturing expertise, we invented the ceramic substrate. And substrates have been used ever since. Of course they have evolved over the years. Today’s very tight emissions standards require high cell density, reduced thermal mass, and low backpressure. We met that requirement by recently launching the Celcor® 600/2 substrate (expanding our portfolio of ultrathin-wall substrates) which allows car manufacturers to meet these tight standards with low backpressure and reduced system cost.
Wall-flow filters are used today but were developed in the 80’s to address health concerns regarding particulate matter. Filters are used increasingly in European passenger car applications driven by Euro 5 and future Euro 6 standards. Our filter products offer high filtration efficiency to reduce soot and to meet future particle mass and number emission standards. In addition they have to work with the engine control system. There is very strong interest in the Corning DuraTrap® AT filter and we are expanding its reach into a wide range of applications and into other areas of the world.
AI: What impact does your new ceramic substrate have on reducing emissions?
We provide an enabling technology to achieve ultra-low tailpipe emissions for gas and diesel vehicles. The Corning Celcor® 600/2 substrate has thin walls, low thermal mass, and low backpressure (low resistance to flow) to help OEMs meet the tightest standards at a low system cost.
Corning is a global leader in materials composition, structure, and properties. We continue to invest in our research and development portfolio in order to invent new materials and new manufacturing processes that address future needs for breakthrough substrate and filter products.
AI: Please tell us a little about the particulate filters Corning makes and how they have impacted the auto industry.
We developed filter technology in the 1980’s. For a long time it was for niche applications as emissions regulations did not require filters on vehicles until recently. Since that time, we continued to develop and fine tune our products. , Today, DuraTrap filters are used by leading European car manufacturers. Effective September 2009, Euro 5 standards will be in place, requiring filters on all new models sold in Europe. As a result, the automotive industry now integrates filters into the engine system. Filters are no longer just added on. They are an integral part of the development program and system architecture. Therefore, we offer to our customers design, engineering, and testing services to help them achieve their objectives for power, fuel efficiency, emissions reduction and system optimization.
AI: You have been expanding manufacturing globally – how important are your filters and substrates to the global auto market?
There are increasingly stringent standards in place in most geographic regions of the world. For example, India and China have Euro 3, and by 2010 Euro 4, standards that require emissions control products. Corning provides the enabling technology to meet those standards. China uses substrates on all light duty vehicles that are manufactured there. Our manufacturing presence in China contributed to this success as it enables local supply for the growing China market. Our products allow global OEMs to meet low emissions standards around the world.
AI: What are some of the latest technological advances in catalytic converters is Corning working on?
Our innovation leadership, including materials and process inventions, has enabled Corning to continually advance the ceramic substrate and diesel particulate filter to meet the most demanding emissions requirements. For catalytic converters, Corning’s work is focused on ceramic substrates which are the heart of the catalytic converter. We work closely with catalyst companies and systems integrators to enable system optimization. Substrate advances are to minimize back pressure, optimize geometric surface area, and lower thermal mass. We enable the catalytic converter to operate faster and more efficiently; reducing overall emissions. Our challenge is to help optimize the effectiveness of the substrate or minimize the quantity of precious metals loadings, which are expensive.
In addition, we continue to develop innovative filter solutions to optimize filter performance in light-duty diesel applications, including systems requiring NOx after treatment. Future regulations will require ultralow NOx emissions and will also impose limits on particulate number emissions. We are focusing our efforts on developing filter solutions to address these upcoming needs.
More Stories
Avery Dennison PSA tapes support rapid evolution of EV batteries
Speira brings research, politics and business case makers together
Automotive Industries (AI) Newsletter April 2025