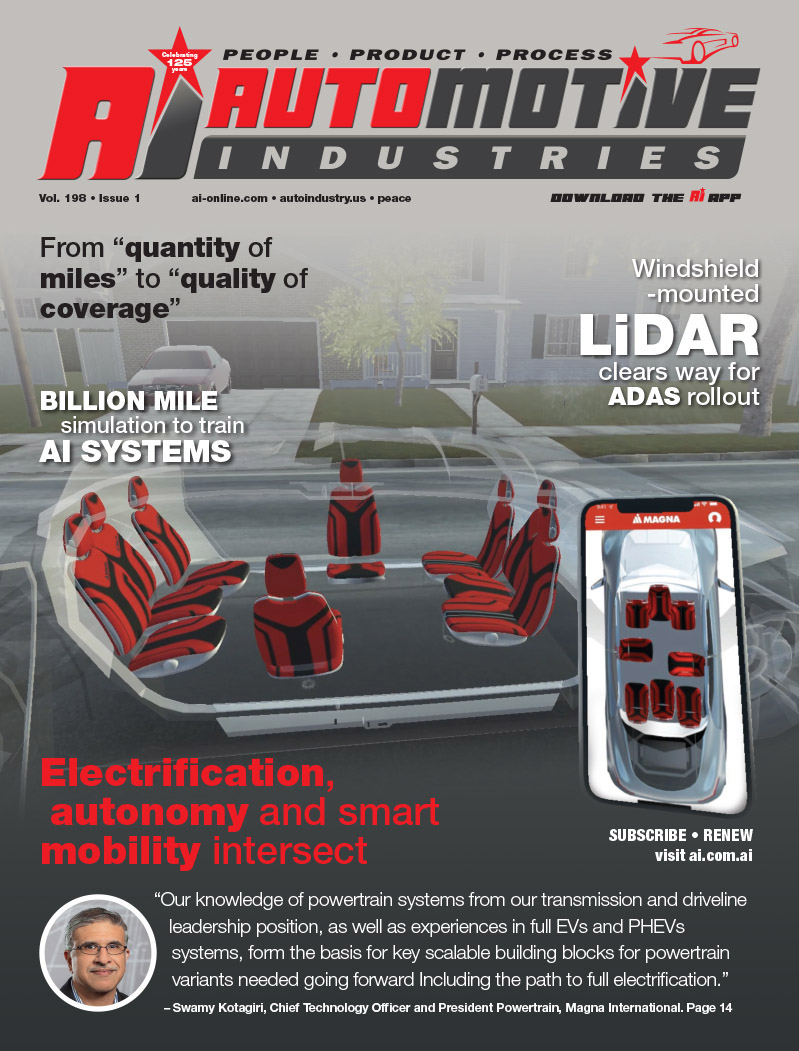
The USD 2.2 billion, Korean firm Alantum, develops innovative substrates for the automotive industry. One of these is alloy foam which is used in exhaust after-treatment and alternative energy applications. Alloy foam is a lightweight, flexible, permeable and stable in its form – even at high temperature. The company says that the main strengths of the Alantum solution, when compared to traditional catalyst carriers, lie in its material’s flexibility and the fact that with the very high surface area of Alantum’s alloy foam, less substrate material is required to achieve the same performance results. Less substrate requires less catalyst. Less catalyst means less platinum use, which translates into significant cost savings.
Alantum’s alloy foam is based on either an iron or nickel metal foam and converted to an alloy foam using Alantum’s patented production process. “Several properties of the alloy foam can be tailored according to the customer’s need and/or desired specification, including pore size, foam thickness, sheet length, and composition of the catalytic coating (washcoat). However, the alloy foam can also be supplied without any washcoat. The foam can also come pre-shaped or sintered together in a stack. In addition to the pore sizes listed below, other pore sizes are available upon request. The possibilities with Alantum’s alloy foam are endless,” says Alantum.
Alantum, is a subsidiary of Korea Zinc and Korea Nickel Corporation. In June this year, Alantum started the construction of a new alloy foam plant in Ulsan, South Korea. The plant is scheduled to be operational by April 2010 and will have an annual alloy foam production capability of 500,000 m². Alantum’s alloy foam is used in diesel oxidation catalysts where the alloy foam acts as the catalyst carrier. The substrate also filters soot. The company says that compared to current market solutions, alloy foam offers a better exhaust gas distribution and turbulent flow.
Alloy foam is also used in diesel particulate filters. “A DPF with Alantum’s alloy foam as a substrate has a number of unique characteristics. In addition to the obvious requirement of collecting soot, the absorption rate of soot/particles is adjustable by the number of layers of foam. A system using alloy foam would be much lighter in weight when compared to existing filters. It is a closed system (no blow-by) with a filtration rate that can be customized to the customer’s demand and specifications. In fact, efficiency increases over a system’s lifetime,” says Alantum.
Alantum’s alloy foam is also used in mufflers in a silencer application. The foam provides a higher noise and sound absorption rate in comparison to the current market solution of glass, mineral, and steel fiber-based materials in mufflers. Alantum’s alloy foam also has retrofit applications which allows for performance tailoring in such specifications as efficiency and pressure drop. The company says that systems using alloy foam are service-free, highly durable, have no ash accumulation or blow off, and allow for design flexibility (integration of a DOC/DPF combination), and a less overall system cost.
Alantum’s alloy foam is a critical material for the supercapacitator project being undertaken by the University of Michigan and the Fraunhofer Institut für Fertigungstechnik und angewandte Materialforschung (IFAM). The principal goal of the proposed project is to design and construct a high power, high energy density prototype supercapacitor using metal foams from Alantum and nanostructured early transition metal carbides and nitrides being developed at the University of Michigan. Supercapacitors are expected to efficiently deliver energy and power in a space that is currently not well served by other electrochemical storage and conversion devices including batteries and fuel cells. State-of-the-art supercapacitors employing carbon electrodes can reach energy densities of 5-6 Wh/kg at power densities of 700 W/kg. Higher power and energy densities are needed for use in hybrid electric and plug-in hybrid electric vehicles.
Automotive Industries spoke to Winfried Doelling, managing director of Alantum Europe GmbH.
AI: How has Alantum’s alloy foam benefitted the production of diesel particulate filters?
WD: Alantum has pioneered the development of Alloy Foam Diesel Particulate Filters which are engineered for unmatched durability, low maintenance and highest filtration performance. Generally, the outstanding material characteristics of Alloy Foam allow for tailored solutions for many applications and fit into tightest installation spaces.
AI: Tell us a little about the iron and nickel-based alloy metal foam solutions from Alantum for the automotive industry.
WD: Besides our Retrofit DOC/DPF products, Alantum is currently focusing on several new OEM substrate solutions in collaboration with multi-national first-tiers in the EU, Korea, US, as well as China.
AI: What are some of the new applications of Alantum’s alloy foam for the automotive industry?
WD: The latest Alantum engineering-focus lies in Iron-based alloys which are extremely heat resistant and bear great advantages for various applications in gasoline exhaust treatment.
AI: What role do you think alloy foam will play in automobiles of the future?
WD: Alloy foam will play out its great material advantage to gain a significant market share in the classic exhaust treatment sector. In addition, special high temperature resistant applications will open up new technological opportunities for aftertreatment systems. Lastly, the use of Alloy Foam in fuel cells as well as supercapacitors will ensure its pivotal role as the material of choice for alternative drive concepts.
AI: How critical is the University of Michigan and IFAM’s supercapacitor project for alternate-energy-fuelled cars and what role has Alantum played in this project?
WD: The Supercapacitor project is a technological innovation for short term electrical energy storage in a small physical volume. Supercapacitors are expected to become a core component of (hybrid) electric drive concepts. Alantum is supporting this international R&D project with alloy foam development and material expertise.
More Stories
Avery Dennison PSA tapes support rapid evolution of EV batteries
Speira brings research, politics and business case makers together
Sensor Fusion and the Next Generation of Autonomous Driving Systems