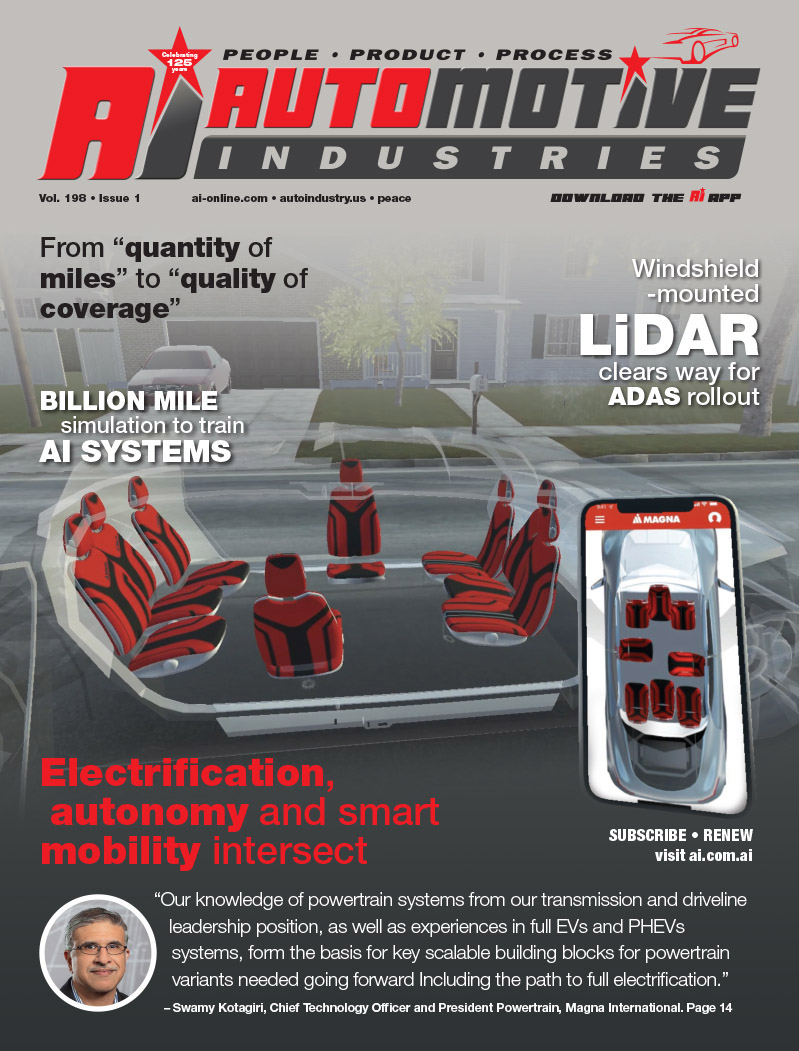
IPs Come Back In-house
![]() |
The new Toyota Harrier will have an IP built in-house at the Kyushu assembly plant. |
Only two holdouts: Nissan and Fuji. All others including Toyota, Honda and Suzuki assemble IPs on sublines in their main assembly plants. In most cases, they also produce the plastic shells.
One of the best examples of the Japanese approach can be seen at Toyota’s Kyushu plant, home of the new Harrier SUV (soon to be produced at Toyota Motor Manufacturing Canada as the Lexus RX330). There, some 100 components (including fasteners and screws) are brought to a U shaped subassembly line continguous to the main assembly line. These are assembled by a team of 10 workers stationed along the 40-meter line (20 meters on two sides).
Instrument panel shells are brought to the front of the line on a hanging rack from the plastic molding shop within the plant’s 262- acre site. The plastic shell is then attached to a rotisserie-like holder, facilitating parts assembly on both sides of the unit. Other components components including the car audio system, instrument cluster, airbag and wire harnesses are delivered to the side of the line in boxes.
Matching the line’s labor force are 10 main assembly processes. The first involves installation of the audio system and air-conditioner controller.
Then the assembled instrument cluster, supplied from Denso Corp.’s Takatana plant, is fitted into the instrument panel; the instrument cluster. This is followed by installation of dashboard wiring, the airbag holder, air ducts and metal clamps. Assembly time is around one minute per station, thus around 10 minutes in total.
After the assembly is completed, the instrument panel is carried by conveyor to an AGV whereupon it is automatically loaded and transported to the main trim line for installation in the car.
Toyota cites concern about damage from handling, packaging and trucking as the chief reason for assembling instrument panels inhouse rather than relying on suppliers. In a rare exception, the automaker’s main supplier of airbags and weatherstrip, Toyoda Gosei Co., Ltd., supplies assembled IPs for the Voxy and Noah passenger vans and Premio and Allion sedans.
Nissan, a proponent of modularization as means to bring down costs, purchases assembled instrument panels from Calsonic- Kansei Corp., while Fuji buys them from Shigeru Co., Ltd., a longtime supplier near the company’s Ohta and Yajima assembly plants.
Neither Calsonic-Kansei nor Shigeru produce instrument panel shells but outsource them from Hitachi Chemical Co., Inoac Corp. and others. Similarly, several affiliated assemblers of Toyota, Honda and Mitsubishi purchase shells from suppliers including Inoac.
This article was provided exclusively to Automotive Industries by J•REPORTS, a new information service offering in-depth coverage of automotive technology based in Tokyo. For additional information about this and other studies and prices, contact jreports@attglobal.net
More Stories
8 Best Plastic Welding Techniques for Automotive Manufacturing
5 Big Reasons to Choose LED Bulbs for Your Car Headlights
How much does it cost to ship a car on Amtrak Auto Train?