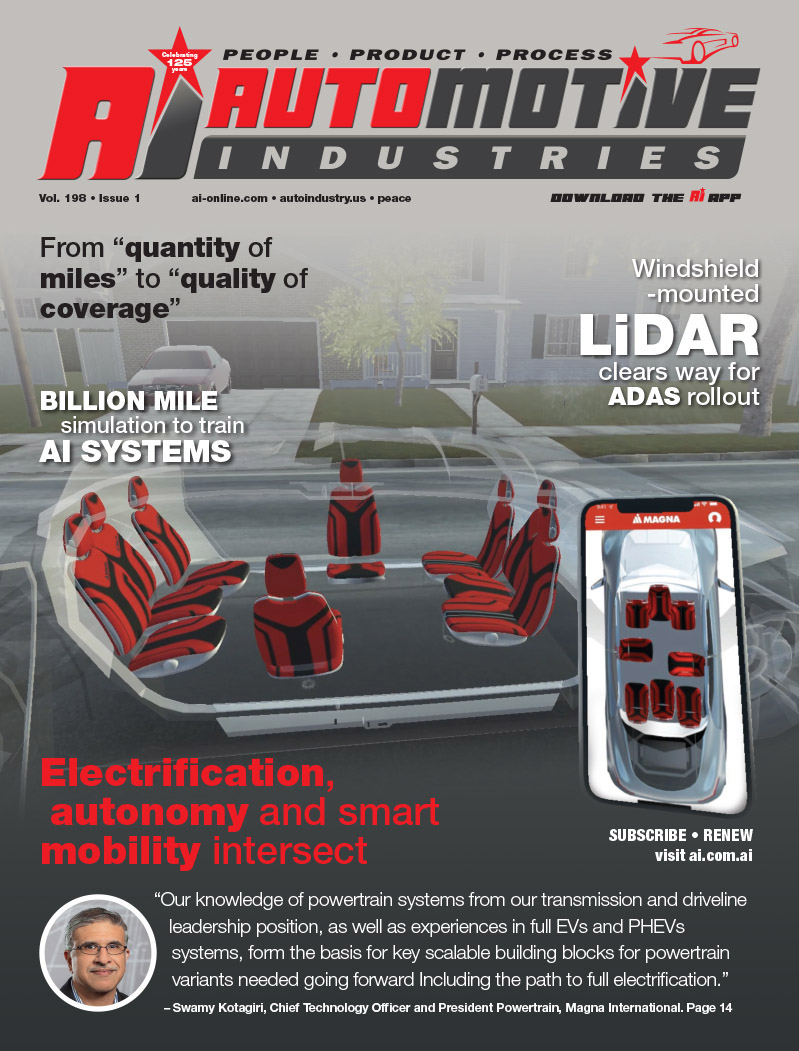
The Euro 2.8 billion Luvata is a world-leader in metal fabrication, component manufacturing and related engineering and design services. As the company proudly points out, “Wherever you are, you probably can’t look more than a hundred meters in any direction without seeing something that Luvata has been a part of.” One of the biggest markets for Luvata, which has its corporate headquarters in London, is the automotive sector. The strips, wires, spot welding electrodes, tubes and e-cooling profiles essential to heat exchangers, connectors and wire wound components used by the auto sector are manufactured by Luvata.
The company manufactures these components in both copper and copper alloys. “Due to its global growth, the automotive sector is a key priority for Luvata. Our work in the sector does not focus solely on copper and brass – we have to look at other materials like aluminum to be able to fully support the total automotive sector and utilize our skills, applications and engineering expertise,” said Jerker Adeberg, executive vice president of Luvata in an earlier interview to AI.
So when Toyota came to Luvata looking for ways to help to an increased productivity through improved manufacturing efficiencies in its automotive business, Luvata was able to help. The challenge for Toyota and Luvata was to help the car manufacturer improve the quality of spot welding in the face of the adverse welding conditions created by coated steel materials. And at the same time help Toyota reduce downtime and decrease costs.
Luvata’s solution was to work with Toyota to develop spot welding electrodes and alloys that could consistently deliver high weld-standards throughout the life of the electrode – minimizing downtime, reject welds, and waste. The unique blend of alloy composition and proprietary cold working properties enhanced performance and was particularly suited for use with coated materials. The result was superior welding products produced from dispersion-strengthened and zirconium coppers, combined with a special mechanical deformation process. Luvata welding products are marketed under the brand names of Nitrode, Z-Trode, A-Trode, Cupal, and Nitrode Composite. These products are used by leading car manufacturers including Honda, General Motors, Volkswagen, Toyota and Citroen.
Luvata says that for heavy-duty vehicles such as large trucks, construction and agricultural equipment, where low emissions are important, products with high temperature tolerance are needed; its CuproBraze® technology is helpful. The company says that its brazed copper and brass technology is extremely durable and can withstand much higher temperatures and pressures than other metals such as aluminum. “So, in the production of charge-air coolers for example, our customers have been able to push beyond usual performance limits and produce heat exchangers which are more durable, efficient, compact, corrosion resistant, repairable and environmentally friendly,” says the company.
Luvata comprises 35 companies that employ 6,500 people in 27 factories in 13 countries.
The company’s history started four centuries ago when Luvata began producing cannons in Sweden. “The Renaissance was sweeping across Europe; Leonardo da Vinci had recently finished the Mona Lisa; Columbus had just landed in America and Shakespeare was still learning to write. Since then, the Luvata has made history of its own.
Luvata changed its name from Outokumpu Copper Products in May 2006. Outokumpu Copper Products was a group of companies and technology-driven ventures integrated over many years. Today, the diverse cultures and capabilities of these companies are united under the Luvata name,” says the company.
Automotive Industries spoke to Jerker Adeberg, Executive Vice-President, Luvata.
AI: What are some of Luvata’s auto products and markets?
In addition to welding electrodes, Luvata is the leading supplier, as regards both quality and production volume, of copper and brass strips for engine cooling. Our strip products are used globally both on OEM and AM and sold to about 80 countries.
AI: How much of your business comes from the engine cooling?
About 25-30% of the sales of our Rolled Products Division come from the engine cooling segment.
AI: Please tell us about your heat transfer solutions.
We produce materials and develop solutions both to the traditional soft soldering heat exchanger market and to the brazing market, called CuproBraze, North America being the highest volume market. Our materials are used in radiators, heaters, charge air coolers, oil coolers etc.
We have been able to develop new cost saving concepts for the soft soldering process. CuproBraze materials go mainly to premium type of heavy duty segments where durability, corrosion resistance, reparability, high temperature and pressure resistance are valued. Those segments include HD trucks, mining applications, locomotives, generator sets, construction equipment etc.
One of our recent developments is copper Multiport tubes which create new opportunities for instance in oil coolers and in mobile air conditioning, taking also into account the odor retarding antimicrobial properties of copper alloys.
AI: Are you looking at expanding your engine cooling markets in emerging economies? How will your strategy be different there?
The road and environmental conditions in the emerging market areas are often very demanding. The roads can be bad, climate can be cold or hot with humidity and presence of salts, sulfuric pollutants and sand erosion, and the maintenance practice of coolant is not that elaborated.
These kind of tough conditions favor copper alloys, especially CuproBraze, over aluminum. CuproBraze has gained a wide acceptance for instance in Russia, where salting of roads to melt ice exposes automotive heat exchangers for corrosion attacks and the limited availability of spare parts in remote areas can cause expensive heavy duty vehicles standing still unless damaged parts can be repaired on site. Also India is developing great interest in CuproBraze.
AI: What are some of the new technologies Luvata is working on to help increase the eco-friendliness of vehicles?
The development of environmental regulations for vehicles results up to 50% higher heat loads to the cooling systems and the charge air cooler’s inlet temperatures are approaching 300 C. Our CuproBraze materials withstand generally higher temperatures and pressures than alternatives.
Our new anticorrosion concept raises the level of exhaust gas resistance and our copper alloy based solutions become interesting in heat exchanger applications, where stainless steel is used today. That would mean smaller and lighter units with high thermal performance.
The vehicle industry is gradually moving towards renewable energy sources. CuproBraze technology complies well with this development, according to our judgment.
More Stories
Avery Dennison PSA tapes support rapid evolution of EV batteries
Speira brings research, politics and business case makers together
Automotive Industries (AI) Newsletter April 2025