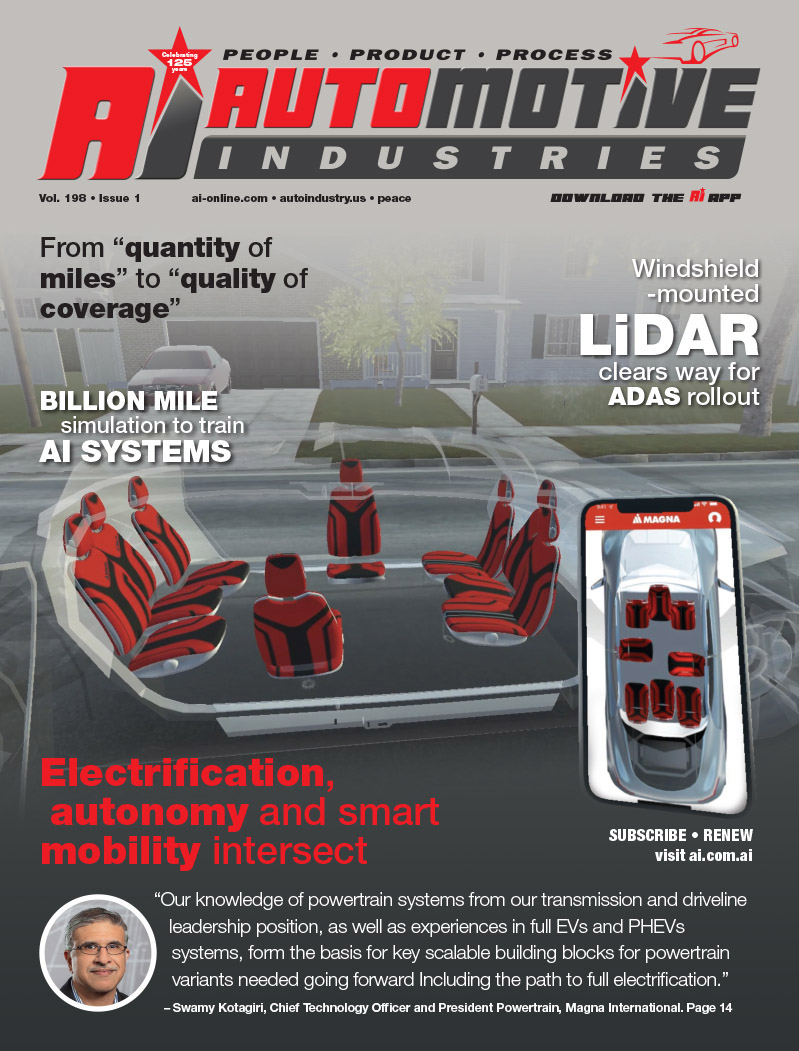
Innovations in materials heavily influence the utility and growth of additive rapid prototyping and manufacturing technologies. Elgin, IL-based DSM Somos, a pace setting global marketer of rapid prototyping materials, has prolifically commercialized seven products within the last twelve months.
In March this year, , DMX-SL™ 100 – a breakthrough stereolithography resin designed to move the SL process closer towards direct manufacturing applications due to its high-durability was introduced. “DMX-SL is very different from traditional SL resins. Toughness combined with stiffness, a hallmark of engineering plastics has historically represented a limitation of the SL process. With an impact strength up to 80 J/m, yet a flexural modulus ranging from 2000-2400 MPa and up to 20 per cent elongation at break, this new chemistry platform has opened a new frontier for the SL process—plus,†said Brian Bauman, product manager at DSM Somos.
Industry experts agree, Tom Sorovetz, Rapid Prototyping Manager at Chrysler, LLC in Detroit, MI states “DMX-SL is leaps and bounds above most of today’s current stereolithography resins. This material has the stiffness similar to the various ABS-like resins currently available; however, the impact resistance has increased almost four fold. This is a very important achievement because now you can use the SL part directly when higher impact resistance is required instead of having to create secondary tooling and vacuum cast parts.â€
Mark Jones, SLA Manager at Laser Reproductions in Gahanna, OH, says: “DMX-SL is rigid yet bendable—the perfect combination. Its impact reliability is much more than semi-rigid or rigid materials currently on the market. I’ve doubled parts over with no breakage. Compared to typical SL materials, DMX-SL is heads above the competition.â€
Though stereolithography has successfully been used to date for some specific direct manufacturing applications such as hearing aid shells, jigs/fixtures for product assemblies and interior products such as custom lamp shades, its widespread use has been limited by material properties. Therefore, while SL resins perform well in rapid prototyping applications, their usefulness in direct manufacturing to date has been restricted to products without demanding toughness requirements. “Current SL resins on the market—and there are over 40 between Somos and other suppliers— are more brittle than traditional engineered plastics such as polypropylene, ABS, polycarbonate and nylon. In addition, SL parts often become even more brittle over time, which is unacceptable for direct manufacturing applications. With the introduction of DMX- we see this paradigm shifting,†says Bauman.
In September this year, DSM Somos’ DMX-SLâ„¢ 100, drew crowds at the Time Compression Technologies’ UK Rapid Product Development and Rapid Manufacturing Event. The exhibition attracted more than 2000 visitors from across the globe. “What makes DMX-SL so exciting to engineers is the extreme durability of the parts it creates. This marks the first time an SL material has been able to match the strength of sintered resins in many applications while still offering SL accuracy and detail resolution.,†said Eva Montgomery, marketing manager at DSM Somos . DSM Somos is quick to qualify that while DMX-SL comfortably competes with sintered thermoplastics relative to stiffness and toughness, there are other conditions such as heat resistance that prevents direct substitution for sintered materials in all applications.
While DMX-SL 100 represents a paradigm shifting innovation, DSM Somos also invests in advancing the capabilities of established RP material types such as clear ABS-like resins popular for automotive lens prototyping, fluid flow analysis and assembly fit testing. WaterShed® XC 11122 a near colorless version of its WaterShed® 11120 material was introduced in November 2007 as well as a new acrylic – like high clarity material, WaterClear Ultra 10122. Colorimetric testing has demonstrated that WaterClear Ultra is now the clearest SL resin available on the market today. “WaterShed XC delivers the exceptional functionality and versatility of the top selling WaterShed 11120, but produces parts that look more like true, clear engineered plastic. WaterClear Ultra delivers parts resembling acrylic with extremely high clarity, virtually zero color and high dimensional accuracy. Whether somebody chooses WaterShed XC for it’s functionality or WaterClear Ultra for its clarity, based on testing both resins have significantly less color than other clear SL resins on the market, making prototyping of clear parts much easier,†said DSM’s Bauman.
Industry users of these materials agree, “WaterShed 11120 performs like ABS but looks more like glass with a slight green tint. WaterShed XC maintains all the great performance properties, but without the color. This makes it highly suited for parts such as lenses or clear covers for automotive, medical and consumer product applications. We see it as a huge improvement,†said Mike Primavera, president of the New York based Dynacept. Shawn Zindroski, President of rapid prototyping service bureau Morpheus Technologies in California states, “The clarity and all around surface quality of WaterClear Ultra is phenomenal. In the past, headlight inner lenses needed to be made out of milled acrylic but with the extreme transparency of WaterClear Ultra we can now make them via the stereolithography process. This reduces turnaround time for my clients and opens the door for more clear part applications.â€
Both the WaterShed XC and WaterClear Ultra products build on DSM Somos’ patented clear resin technology, and use the DSM Somos Oxetane Advantageâ„¢. This is an advanced chemistry platform that produces parts with outstanding water and solvent resistance and high dimensional stability.
Automotive Industries spoke to Jim Reitz, business manager at DSM Somos.
AI: What kind of breakthrough does DMX-SLâ„¢ 100 signify for the automotive industry?
DMX-SL is the first resin in what will be a new Somos family of products. It is a material that behaves more like a typical engineering plastic, meaning the material is stiff and tough with a yield characteristic typical of tough engineering thermoplastics. While these properties move SL in the direction of rapid manufacturing, we expect to see continued utilization in prototyping to take advantage of SL process benefits such as accuracy and surface aesthetics combined with durability associated with sintered materials With DMX-SL automotive design engineers can cost-effectively produce durable RP parts with an excellent surface finish, this can reduce overall product development time because the stereolithography process is faster than many RP methods and with a reduction in finishing times due to DMX-SL, the time advantage increases even further.
We do work closely with engineers to ensure that the total DMX-SL properties and limitations of are understood to enable proper utilization of this new material type.
AI: Please tell us a little about the industry applications (including automotive, aerospace, and medical and telecommunications) of DMX-SLâ„¢ 100.
Introduced less than nine months ago, DMX-SL is fast becoming a best seller for many service bureaus across all industry segments in applications that require stiffness and benefit from robust toughness. Thin walled DMX-SL parts behave like polypropylene because of the high level of flexibility, but thicker walled parts behave more like ABS (stiff and tough), in addition, finished parts can be screwed and tapped readily. Engineers are using DMX-SL to produce prototypes normally reserved for FDM or LS or even replacement of cast urethane prototypes (eliminating a production step). For prototyping, DMX-SL is targeted for applications such as dashboard assemblies, equipment housings, duct work, connectors, electronic covers and snap fit designs that would have traditionally utilized other slower or less accurate RP methods however, because of the newness of these materials and the nature of prototyping, engineers are reluctant to detail some of the more interesting applications. As a response, DSM Somos is sponsoring a design contest that will allow showcasing of generic designs that utilize the performance benefits of DMX-SL (log on to www. DSMSomos.com to learn more. )
AI: Please tell us a little about how DSM Somos was created and the progress it has made since then in developing RP materials.
Since the late 1980’s, Somos has been a pioneer in the development of RP materials. (The Somos name was derived from Solid Object Modeling System).Somos began as an R&D sponsored start up business within DuPont. In 1999, DSM Desotech a world leader in UV-curable coatings purchased Somos. DSM’s focus on product innovation has facilitated the collaboration by the DSM Somos’ research and development team with the resources of our corporate DSM Research group, based in the Netherlands. DSM Somos has become a world leader in the development of innovative rapid prototyping or RP materials and an active proponent of new application growth for these materials in rapid tooling, metal clad composites ( MC2 â„¢) and investment casting. DSM Somos pioneered clear ABS like SL materials (2001), reinforced composite SL materials (2003) and DMX-SL 100 (2007)
AI: How has your ProtoFunctional® range impacted the use of SL in the automotive industry?
Growing the stereolithography market through technology development has always been a cornerstone of DSM Somos’ business strategy. Our reputation as a leading materials technology innovator has been built both upon market firsts such as the first, clear ABS-like resin used to prototype lenses, the first high-temperature composite resin for scale model wind tunnel testing and the first highly durable resin to replace cast urethanes. We have also developed tailored formulations for higher throughput that speeds the prototyping process and contributes to better RP equipment asset utilization. Through ongoing advancements in line with our customers needs, Somos continues to drive the capabilities of the SL process forward. Ultimately we believe that future will involve the mainstream application of stereolithography for mass customization and low volume end-use production. In many of the other commercial RP processes, you will find little competition in materials. Perhaps Somos’ greatest impact on the automotive industry’s use of stereolithography as a prototyping accelerator is the competitive environment that we have actively cultivated, encouraging continued innovation and continuous improvement.
AI: What impact do you think WaterShed® XC 11122 and WaterClear Ultra will have on the automotive industry? Please give us an example of how your technologies have been used by an automotive manufacturer.
According to our colorimetric testing, WaterShed XC and WaterClear Ultra are the clearest resins on the market today and lenses made from these materials look exceptional. The high clarity and lack of color of these resins allows them to replace cast urethanes or even milled acrylic in certain applications. This again reduces product development time and costs. Because of the water and solvent resistance of the WaterShed family of materials, models have been used for fluid flow analysis of gases and liquids.
More Stories
Meet Rita Case – recipient of 2024 NAMAD Lifetime Achievement Award
How Much Can You Save Annually by Switching to Energy-Efficient Rotary Solenoids
Navigating the Electrifying Future of Automotive Batteries – Insights from Focus CEO on Lithium, Graphene, and Emerging EV Tech Trends