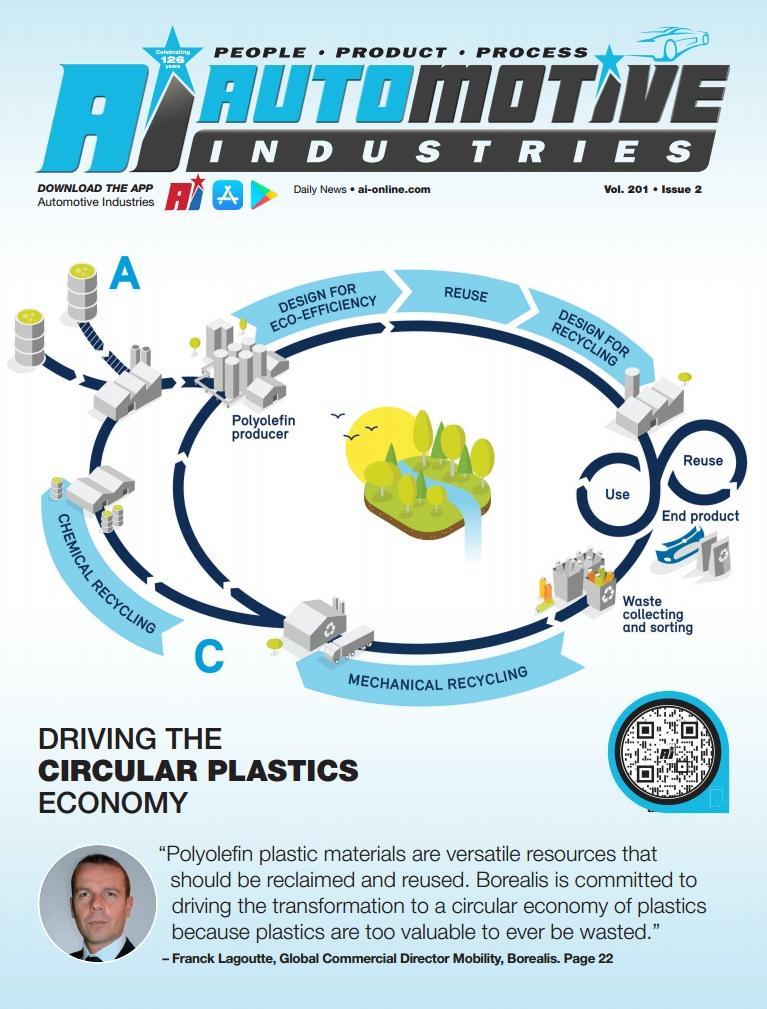
Nothing beats plastics for versatility, safety and durability. However, these very qualities can make plastics an environmental burden at the end of life.
Leading plastics company Borealis has set itself ambitious targets for making plastics more sustainable through recycling. The objective is to maximize value and efficiency across many lifetimes, minimizing its impact on the planet, the company says.
Automotive Industries (AI) asked Franck Lagoutte, Global Commercial Director Mobility, Borealis, how the company is using recycled content.
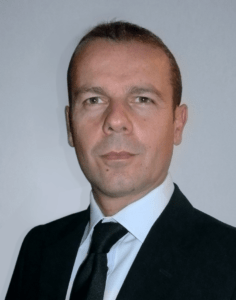
Lagoutte: Borcycle™ M is our transformational technology for mechanical recycling that gives polyolefin-based, post-consumer waste another life. This technology is a key enabler to considerably increase the use of post-consumer recycled polymers in the automotive industry and reduce the environmental footprint of high-quality aesthetic interior trim and cladding parts, for example.
Our Borcycle™ M grades feature close to virgin-like mechanical performance, excellent surface aesthetics, high scratch resistance, low volatiles, fogging and odor levels. The purity of the mechanical recycled polymer fraction allows the manufacturing of molded in color parts even for very bright colors without the need for surface treatment like painting or the use of film back injection molding technology.
AI: What is Fibremod™?
Lagoutte: Borealis Fibremod™ compounds consist of high performance short and long fiber-reinforced polypropylene materials designed to meet the needs of automotive manufacturers. They provide a complete spectrum of mechanical and chemical resistant properties, to offer cost efficient solutions through weight saving, parts integration, processing efficiency and reduced energy and material consumption.
The e-powertrain is a focus area for Fibremod family, where Borealis has developed a new product portfolio with six different halogen-free flame-retardant polypropylene compounds for lithium-Ion batteries.
AI: What other progress is being made in the development of high-performance recycled PP compounds for automotive applications?
Lagoutte: Polyolefin plastic materials are versatile resources that should be reclaimed and reused. Borealis is committed to driving the transformation to a circular economy of plastics because plastics are too valuable to ever be wasted.
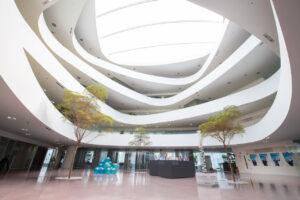
We use our expertise to develop and implement circular economy solutions with added value for our customers in all industry sectors. The Bornewables™ portfolio of polyolefin products are made of renewable-based feedstock derived entirely from waste and residue streams such as used cooking and vegetable oil (and thus not in competition with the food chain).
The ISCC PLUS accreditation of Bornewables grades is based on the mass balance method that allows the customer to track and quantify the effective renewable content at each manufacturing step. Our customers can replace fossil fuel-based feedstock with an identical volume of sustainably sourced, renewable feedstock – without extra switching costs, and while maintaining the same high application quality.
AI: How quickly is the industry adopting this technology?
Lagoutte: For interior, exterior and under-the-bonnet applications, our customers typically start with mechanical recycled PP solutions. As they become more confident that the products meet their performance requirements, they start using other circular solutions, such as our chemical recycling (Borcycle™ C), and bio-feedstock PP (Bornewables™).
We expect that market demand for circular solutions to grow as the industry strives to comply with legislation in the face of limited resources. That is why Borealis secured up-stream supplies with the corresponding feedstocks.
AI: What is next for Borealis and Borouge?
Lagoutte Underlying the Borealis Strategy 2030 is an evolved purpose: “Re-inventing Essentials for Sustainable Living.”
A strategic evolution centered on sustainability: The sustainability targets cover GHG emissions, energy use, flaring, and circular economy products and solutions for Borealis polyolefins and hydrocarbons businesses.
Greenhouse gas (GHG) emissions: Borealis aims to reduce its Scope 1* and Scope 2* emissions from 5.1 million tons (base year 2019) to less than two million tons by 2030. Plans include increased use of electricity from renewable sources and carbon capture projects which will come on stream in the second half of this decade. The reduction target includes divestment of the Borealis nitrogen business, which comprises fertilizers, technical nitrogen, and melamine.
Energy consumption: In 2021, around 25% of the electricity Borealis used in its operations was derived from renewable energy
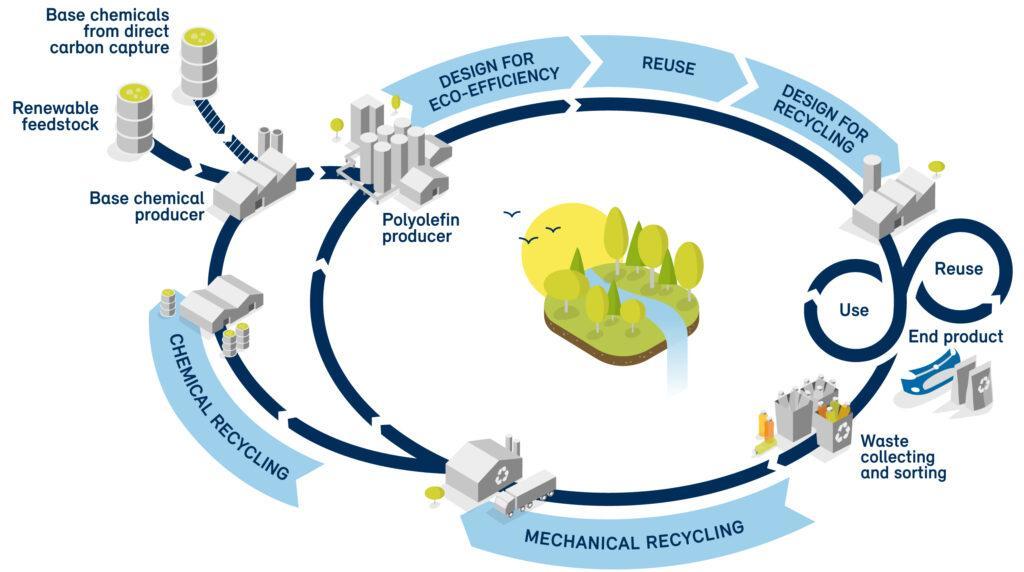
sources such as wind and solar power. By 2025, the share of renewables in the electricity mix will increase to 40%. By 2030, 100% of the electricity used in its polyolefins and hydrocarbons operations will be of renewable origin.
Circular economy products and solutions: Around 100 kilotons of products currently manufactured by Borealis in Europe are circular. These include recycled and renewable polymers and chemicals as well as renewable hydrocarbons. By 2025, Borealis targets a six-fold increase in the share of circular products and solutions, or 600 kilotons. By 2030, the volume of circular products and solutions is set to reach 1.8 million tons globally, turning plastic waste into a valuable resource.
Expansion and transformation: The Borealis Group’s aspiration to become a truly global player has begun with global expansion, including Borouge 4 (UAE), Baystar (US) and Kallo (Belgium). The Strategy 2030 emphasizes the importance of serving the rapidly growing Asian market and expanding the Borealis Group footprint in North America. Additional strategic partnerships as well as mergers and acquisitions are planned. Organic growth opportunities in the form of newly established operational facilities are also under consideration.
- Scope 1 are direct GHG emissions that occur at the source and are controlled by Borealis
- Scope 2 are GHG emissions stemming from the generation of energy purchased by the company
- Scope 3 are indirect GHG emissions that are a consequence of company activities but occur from sources outside or not controlled by the company.
Award-winning technology
Borealis received two awards at the 21st Society of Plastic Engineers (SPE Central Europe) ceremony held in October 2022.
The first was for an industry-first all-thermoplastic tailgate made from Borealis Fibremod™ PP Long Glass Fiber (PP LGF) for the latest Volkswagen Multivan. It was developed through collaboration between Borealis and Magna.
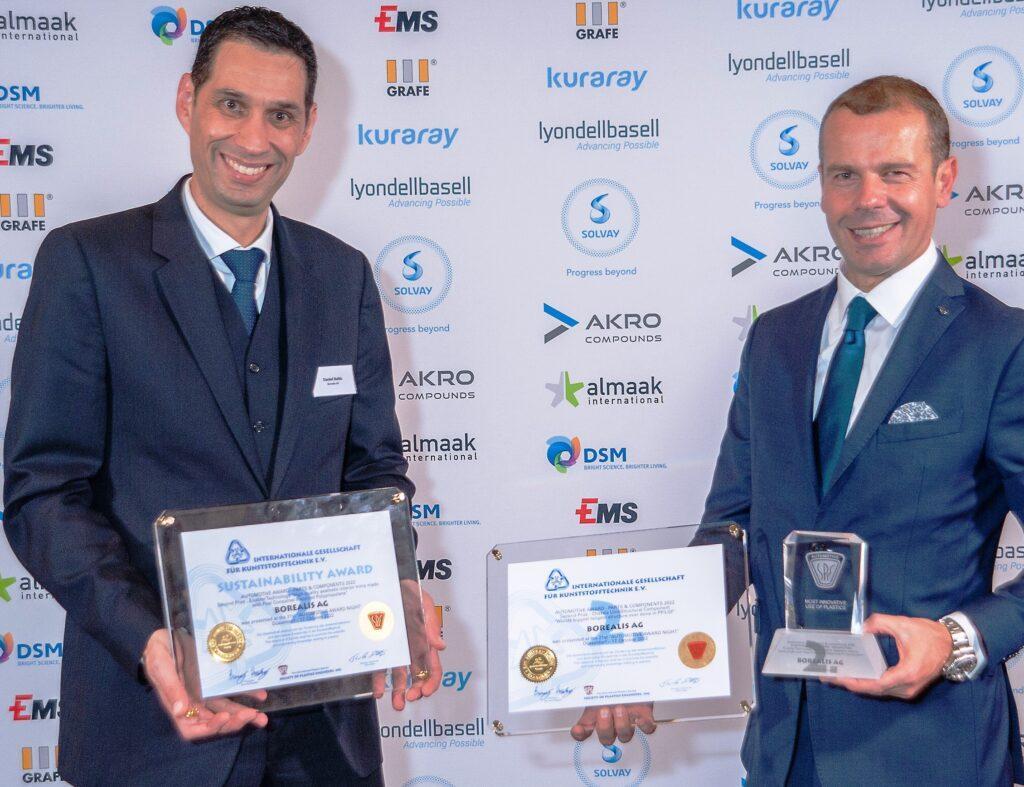
“The Fibremod™ portfolio of lighter-weight polypropylene (PP) compounds gives Tier 1 suppliers and OEMs the freedom to design and manufacture more sustainable and lightweight solutions for their increasingly electric fleets,” said Borealis in a statement issued at the awards.
Fibremod GB416LF was tailored for use in tailgate carriers and visible structural parts. The high-flow, 40% fiber-reinforced material, meets stringent emission and mechanical performance requirements, and can eliminate the need for additional surface finishing steps such as painting, making it an even more sustainable.
Leading Tier One supplier Magna used Fibremod GB416LF to ensure that a range of challenging demands on this part could be met. The tailgate consists of several components; the outer frame and the inner part made of Borealis Fibremod GB416LF, glued together to meet the design and load requirements.
Painted exterior parts are glued to the tailgate structure as well. As a loadbearing part, the tailgate must be extremely robust in order to withstand static and dynamic loads. Part of the tailgate also lies in the vehicle’s interior, meaning compliance must be assured for emissions, fogging, and odour.
Finally, to achieve overall weight reduction for the new Multivan – which weighs around 200 kg less than its immediate predecessor – the tailgate itself must also be lighter. Using Fibremod GB416LF enabled Magna to meet these challenges head-on.
The second award was for advanced mechanical recycling technology which enables the use of “yellow bag” plastic waste for the manufacture of high-quality aesthetic interior parts which comply with OEM requirements.
The technology is seen as a key enabler to considerably increase the use of post-consumer recycled polymers in the automotive industry and reduce the environmental footprint of up-market aesthetic interior trim and cladding parts. It contains 30% by weight post-consumer recycled PP. The high purity of the polymer makes it suitable for the manufacture of molded color parts without the need for surface treatment.
More Stories
Is Your 70 Series Land Cruiser Underperforming? Here’s How to Unleash Its True Potential
What to Do After a Motorcycle Accident to Protect Yourself
Injured in a Motorcycle Crash? Talk to an Attorney Now