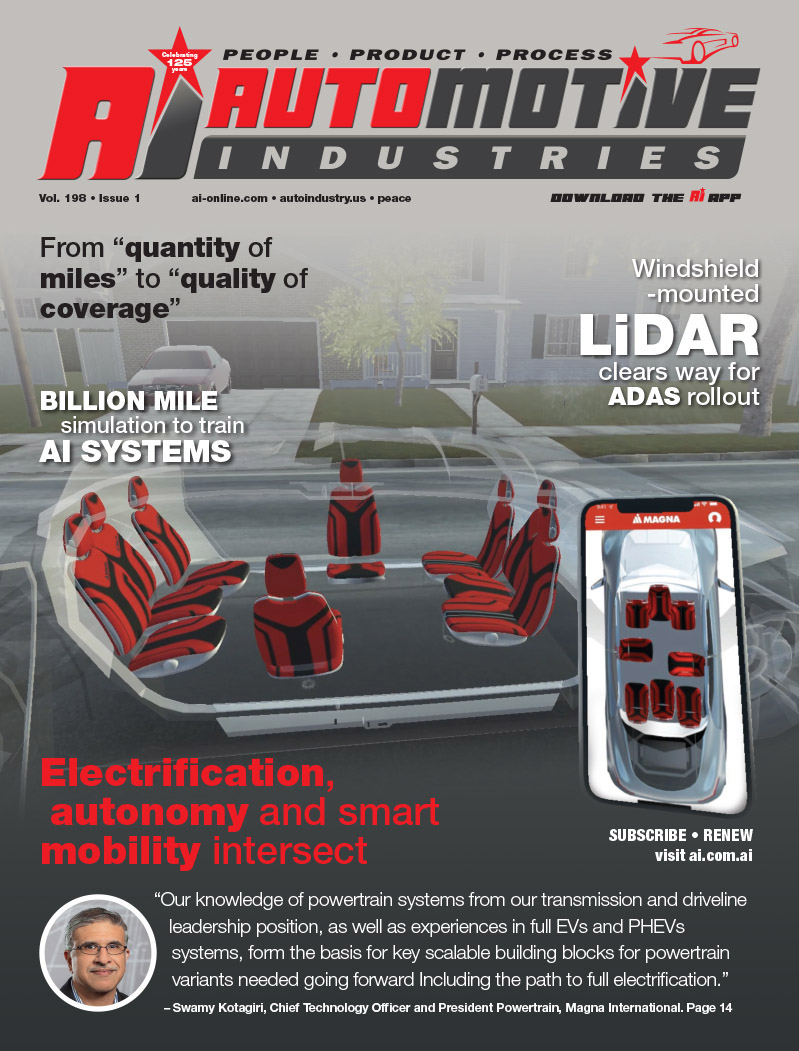
GM’s Mid-size truck VLE Tom Wallace talks quality trucks.
![]() |
Tom Wallace |
AI: Given the company’s increasingly successful launches in recent years, GM’s new Global Manufacturing System (GMS) launch process appears to be working. Describe it for us.
TW: Our process uses a discipline during launch to make sure we’re satisfied with the quality. There are planned batches, or “buckets,” of builds. You build a certain number of vehicles for a week, then you don’t build for a week and evaluate the previous week’s build. In the first bucket, we might build only five very early nonsalable “manufacturing validation” units to see if the plant works and what they look like when the first few come together in the plant.
The launch team first goes through a series of criteria: how risky is the program, how many new parts, how much new manufacturing? They evaluate all that and come up with an assessment of how many non-salable and salable buckets they should build, and how much time they should have between buckets. Leadership approves it, and that becomes the plan.
Then you set up timing with your suppliers and tell marketing when you’ll be ready, and you follow the plan. For this vehicle — with a new plant, new general assembly, new body shop, new work structures, new materials handling system — we decided we needed seven or eight buckets and 100 vehicles in the final one. With all the variations, we probably need 100 to get them all. SSR, a niche vehicle, had fewer, and we did the Buick Ranier in three buckets. Each bucket has more vehicles in it, and the first few are non-salable. We’re learning on those and might have some parts that are not quite ready, not totally validated. We’ll build them using prototype parts, so they might not be certified as legal.
AI: Legal in what sense?
TW: Legal in that all the certificates are done, FMVSS certificates done and signed, emissions and fuel economy done and approved by the government.
As we progress, we learn. By the fourth or fifth bucket, we may be up to 20 a week. A leadership team — about five of us — comes together and looks at how the build is going. How do the parts look? Are all of them certified? Where are your certificates? What is your validation status? We go through a quality gate, with 20 or 30 very specific items, and it takes several hours. If the answers to all those questions are positive, those vehicles are deemed salable. We put VINs on them to allow us to sell them, and we build salable vehicles the following week. But those are still not dealerordered vehicles.
The next couple of buckets go into press fleets and a Captured Test Fleet (CTF). CTF vehicles are legal, salable, owned by GM and driven by specific GM drivers who have to put a minimum number of miles on them per week and do very extensive reporting. If anything goes wrong, they have to call it in within 24 hours.
Meanwhile, we’re continuing to build buckets of vehicles and using ongoing validation data from engineering, assessment from manufacturing and input from the CTF to decide when we’re ready to accelerate to dealer and customers orders. The same leadership group gets together again, looks at the data, goes through a very disciplined quality valve and says, “Yes, we’re ready to pull the trigger next Monday.” That is called Start of System Fill (SSF).
In some programs, we’ll build as many as 200 salables before going to System Fill, depending on the size of the program and how many plants we have. These are put into test fleets, evaluated and eventually go to auction — inspected and upgraded — as used vehicles.
AI: How much can you deviate from the plan? Can you go to SSF sooner if it’s going well or build more buckets if it’s not?
TW: That’s where we put the judgment in. It’s a complicated vehicle — 2,500 parts and more computing power than the first moon shot — and we do get surprises. Say you have seven buckets planned, and you build Bucket Four and find maybe five problems. Some are supplier quality, some engineering, some manufacturing, they could be anything. You might say, “I want those fixed by Bucket Five in two weeks.” And the organization goes after them. But one turns out to require a four-week die change. You can delay Bucket Five two weeks, or you can say, “I want that fixed in Bucket Six.” Then we’ll build Bucket Five to determine that we got the other four corrected, and we’ll take the risk of this one problem not being fixed until Bucket Six.
On the other hand, if everything in Bucket Four is perfect, we may decide that we don’t need Buckets Five and Six and go right to System Fill.
AI: Once you get past the first few, what is the typical bucket size?
TW: It depends. With each bucket, we increase the line speed to give the operators time to learn their jobs at an ever increasing rate. The first day, one an hour. Next day, two an hour. Bucket Four, maybe 20 an hour. Bucket Five, maybe 30 an hour. By the time you get to Bucket Six or Seven, you could be at 100 or 150 vehicles at close to production line speed. In the last bucket, you want a very good sample because after that you’re going right into System Fill.
AI: A bucket of 50, 100, 150 vehicles represents a lot of money, so making a decision to build one more bucket has a big financial impact.
TW: Not in the whole life-cycle scope of the program. We absolutely must have first-class, high-quality vehicles right out of the chute. There is no cost too big to ensure quality at introduction, so the cost of one bucket more or less doesn’t compute.
More Stories
8 Best Plastic Welding Techniques for Automotive Manufacturing
5 Big Reasons to Choose LED Bulbs for Your Car Headlights
How much does it cost to ship a car on Amtrak Auto Train?