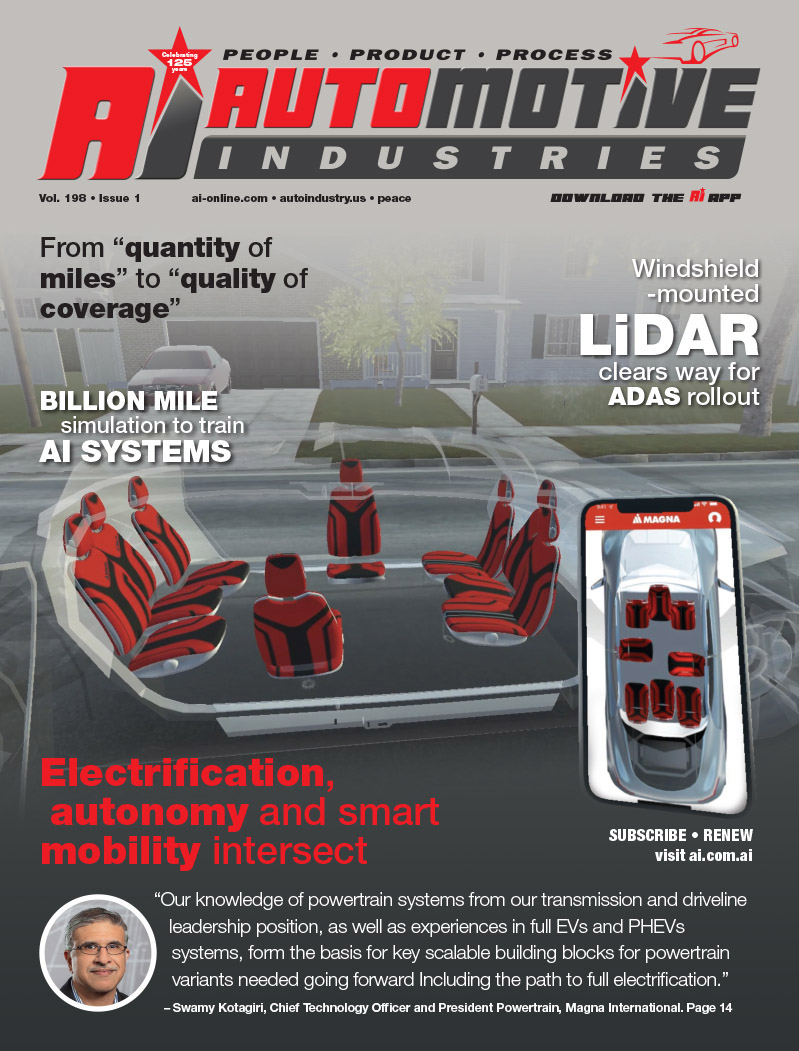
SABIC Innovative Plastics’ tough, lightweight Noryl* GTX resin was recognized today for its key role in helping General Motors’ (GM) 1987 MY Buick® LeSabre® T-Type fenders win the coveted Hall of Fame Award from the Automotive Division of the Society of Plastics Engineers (SPE®). Presented to GM for the sports coupe fenders, the award is given annually to an iconic and innovative application that has been in continuous use for more than 15 years, delivered a value proposition that could not be met by traditional materials, and has been broadly adopted within the automotive or ground-transportation industries. The Hall of Fame Award will be presented to GM in Livonia, Mich. on Nov. 12, 2009 at the 39th annual SPE Innovation Awards Gala. The SPE Automotive Innovation Awards Competition is the oldest and largest recognition event in the automotive and plastics industries.
The longstanding, global success of Noryl GTX resin fenders once again highlights the proud history of breakthrough thermoplastics technologies pioneered by SABIC Innovative Plastics. The company’s Noryl GTX resin clearly meets SPE’s Hall of Fame qualifications. It is the first use of an engineering thermoplastic on a vertical body panel: the front fenders on the 1987 MY Buick LeSabre T-Type1 sports coupe produced by General Motors Corp (GM). Fenders made with Noryl GTX resin were then quickly adapted to the Buick Reatta® sports coupe, 1988-1995 C&H platform vehicles, and in 1989-2005 Saturn® vehicle, and are now used today on a wide range of vehicles manufactured worldwide.
“We’re honored to be recognized by SPE for the major contribution Noryl GTX resin has made to the global automotive industry,” said Gregory A. Adams, vice president, SABIC Innovative Plastics, Automotive. “For more than two decades Noryl GTX resin fenders have demonstrated the value of using strong, lightweight thermoplastics for all sorts of critical automotive applications. SABIC Innovative Plastics continues to dedicate our resources and expertise to new material innovations that can follow in the footsteps of Noryl GTX resin to drive the development of newer, better next-generation applications. This award means a great deal to us, clearly showcasing the company’s role as a top global supplier of advanced materials solutions.”
Noryl GTX resin, which has been audited by environmental strategy firm GreenOrder, reduces automotive part weight resulting in better fuel economy and lower carbon dioxide emissions. It also expands design freedom for OEM designers to achieve shapes that are not possible or very difficult in metals, improves damage resistance, and lowers cost of repair. Designers and engineers are also able to meet stringent pedestrian protection norms by “designing in” energy absorbing features in new generation fenders made from Noryl GTX resin.
“SABIC Innovative Plastics is deeply involved in developing and applying, greener, lighter, and aesthetically pleasing solutions to support our customers in creating vehicles with reduced environmental impact,” said Venkatakrishnan Umamaheswaran (UV) director of Marketing, Engineering and Technology for SABIC Innovative Plastics, Automotive. “We believe there are many opportunities to use high-performance plastics in different areas of automotive design, and we stand ready to supply our material expertise that can make this a reality, as it’s done for fenders. Our greatest satisfaction comes from working side by side with customers as long-term global suppliers to help them achieve success.”
Millions of Noryl* GTX Fenders Lighten Environmental Impact
Since 1988, more than 20 million vehicles have been manufactured with fenders made from Noryl GTX resin in Europe, the United States, Japan, South America and China. Automakers that have chosen these fenders over the years include GM, Ford, Volkswagen, Renault, PSA Peugeot Citroen, BMW, Audi, Land Rover, Mercedes-Benz, Mitsubishi, and Nissan. Noryl GTX resins for fenders and other body panels offer major environmental benefits through weight-out. According to GreenOrder, because the resin is 50 percent lighter than steel, equipping all cars on the road today in Europe with fenders made from Noryl GTX resin would save 530 million liters (140 million gallons) of fuel and avoid 1.3 million metric tons of carbon dioxide emissions.
In addition to advantages such as increased freedom and flexibility to design and mold complex parts, fenders made from the new generation Noryl GTX resins can be painted in standard automotive body painting processes. The resin is intrinsically conductive and allows for online electrostatic painting without the need for an additional primer step. In day-to-day use, fenders molded from Noryl GTX resin typically resist minor dents and damage better than steel fenders. They are also typically resistant to corrosion and may be fully recycled at the end of the vehicle’s life.
For additional information on SABIC Innovative Plastics’ Noryl GTX resin, please visit www.sabic-ip.com.
About SABIC Innovative Plastics
SABIC Innovative Plastics is a leading, global supplier of engineering thermoplastics with a 75-year history of breakthrough solutions that solve its customers’ most pressing challenges. Today, SABIC Innovative Plastics is a multi-billion-dollar company with operations in more than 35 countries and approximately 9,000 employees worldwide. The company continues to lead the plastics industry with customer collaboration and continued investments in new polymer technologies, global application development, process technologies, and environmentally responsible solutions that serve diverse markets such as automotive, electronics, building & construction, transportation, and healthcare. The company’s extensive product portfolio includes thermoplastic resins, coatings, specialty compounds, film, and sheet. SABIC Innovative Plastics (www.sabic-ip.com) is a wholly owned subsidiary of Saudi Basic Industries Corporation (SABIC), one of the world’s top five petrochemicals manufacturers
More Stories
What to Do After a Motorcycle Accident to Protect Yourself
Injured in a Motorcycle Crash? Talk to an Attorney Now
Danisense launches ‘Online Calibration Portal’ to offer brand agnostic calibration services for current transducers and smoothen the whole process