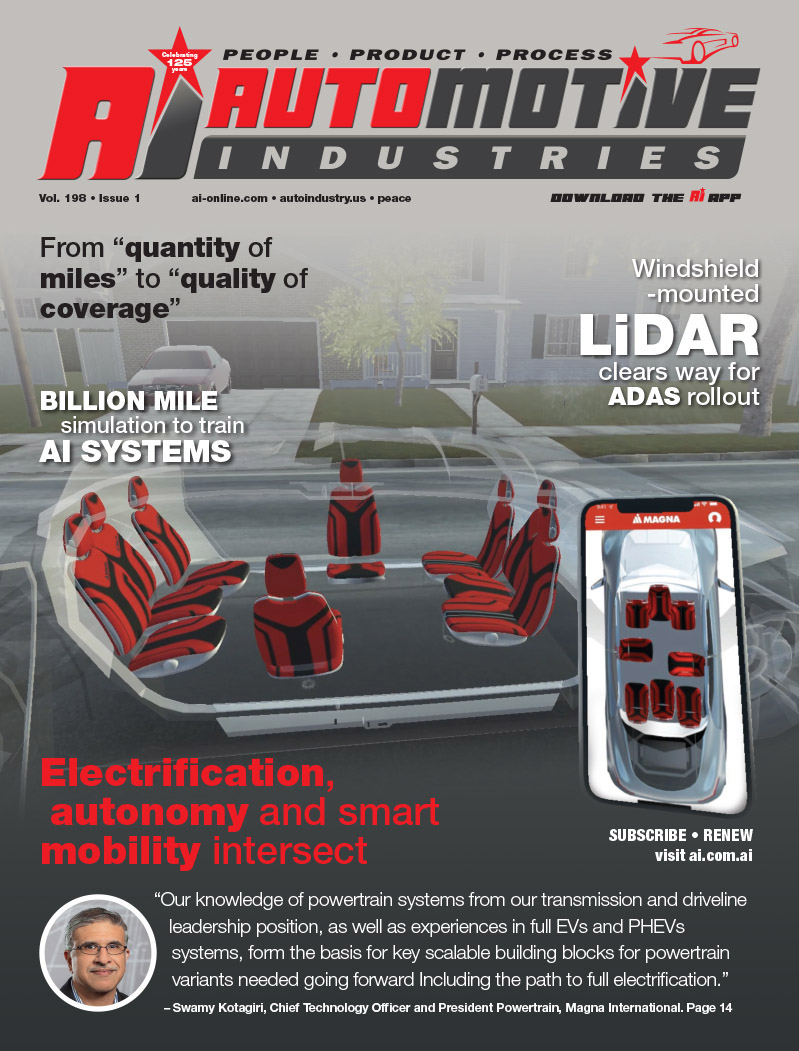
Today’s cars provide engine power equivalent to the muscle cars of the 1960s but produce 95 percent lower pollutant emissions. Despite this progress, the next decade will witness a dramatic increase in the complexity of automotive design. Future engine development will be dominated by balancing tradeoffs between emissions control, fuel flexibility, improved combustion control and overall fuel economy. As more stringent emissions regulations will continue to drive many of the technology shifts, fuel changes will complicate design choices. For example, adoption of fuels with high ethanol content may reduce particulate emissions, but may also prompt new regulation of pollutants, such as aldehydes. Fuel composition also impacts the effectiveness and energy penalty of exhaust-aftertreatment systems. The increasing complexity and multiplicity of these tradeoffs drive up the cost of testing and verification for any new design. As with any engineering field, the more complex and costly that testing becomes, the more valuable accurate models are to the design process.
Historically, having accurate models for engine combustion has been an elusive goal. The workhorse simulation tool for most engine designers was computational fluid dynamics (CFD). CFD tools have advanced in recent years to more accurately address fluid mixing under turbulent-combustion conditions. However, they continue to lack sufficient chemistry detail to reliably predict emissions, ignition and fuel effects. Though empirical approaches toward understanding these effects have been “good enough” in the past, the challenges ahead dictate that accurate prediction of chemistry-related phenomena will be paramount to an efficient design process. This means moving away from empirically based global-combustion models and moving toward molecular-based fuel-combustion mechanisms.
To accelerate the development of more advanced fuel-combustion models and simulation methods, the industry joined together three years ago to form the Model Fuels Consortium. Fuels and engine manufacturers supporting the consortium include Toyota, GM, Chevron, and the Dow Chemical Company, as well as twelve other companies interested in advancing the use of simulation toward managing engine and fuel design tradeoffs. The Consortium guides technology development to address the following needs:
1. Definitions of model-fuel blends to represent commercial fuels in simulation. Real gasoline, diesels, or biodiesels consist of hundreds of chemical components. An effective approach to representing these fuels in simulation is to identify a “model fuel” that contains a handful of chemical compounds chosen to provide a best match to the real-fuel behavior. To address fuel effects in design, model-fuel mixtures can be designed to match characteristics of a corresponding commercial fuel, including heat-release rates, auto-ignition timing and emissions characteristics. The process of matching a model fuel to a commercial fuel should be automated for effective use in engine design
2. Validated reaction mechanisms for model-fuel components and their mixtures. The use of model fuels in engine simulations requires accurate reaction mechanisms for combustion of each of the molecular fuel components, such as heptamethylnonane or alphamethylnapthalene. Outcome predictions of combustion phenomena in advanced engines require an accurate representation of both low- and high-temperature kinetics, at boosted pressures. While modern, rule-based, auto-generation methods provide the needed elementary chemical-kinetic mechanisms for fuel-component combustion, component mechanisms must be validated over the wide range of conditions that occur within the engine cylinder.
3. Automated mechanism reduction for targeting simulations to a specific
application. Automated mechanism generation often results in very large mechanisms that may contain more detail than necessary for a specific application. So targeted mechanism reduction goes hand in hand with mechanism generation in order to get the size of the chemistry description down to the minimum detail required for a specific study. Accurate reduction over a range of conditions is key.
4. Advanced solution strategies for solving coupled chemical kinetics and fluid transport. CFD solution algorithms, though effective at solving fluid-mechanical problems, are not designed to resolve the trace chemical species inherent in emissions and ignition predictions. New approaches to coupling chemistry and fluid transport within the engine are therefore required. In addition to the use of reduced mechanisms that target a narrow range of conditions, alternatives include different ways of overlaying the detailed kinetics simulation with the geometry-resolved fluid-transport simulation. Coupling methods include table-lookup strategies, time-scale separation methods, use of multi-grid/multi-zone models and the use of advanced numerical algorithms for chemistry resolution.
At the heart of the MFC work is the assembly of a database containing detailed kinetic mechanisms, which have been carefully validated to meet the requirements of modern engine simulation for a palette of model-fuel components. Software tools that use this database match street-fuel properties, such as octane number and heating values, with a recommended composition of model-fuel components. A mechanism for the model-fuel blend is tested under engine-like conditions using computationally efficient kinetics simulation, and then reduced to its minimum size using a number of automated mechanism-reduction strategies. Utilities to generate and access fuel-specific and application-specific look-up tables allow indirect use of the validated fuel models in CFD simulation. In addition, a new, commercially available multi-zone engine model, software, allows direct use of the detailed kinetics while still considering stratification in a homogeneous-charge compression-ignition (HCCI) engine. Inclusion of more chemistry in engineering simulations is further facilitated by innovative solver technology that speeds simulations by more than a factor of five in many cases, which can mean days of savings for each calculation. In addition to this work, the existence of the consortium has fueled collaborations with academic and national-laboratory research efforts that have further accelerated the technology development. Advances in mechanism-generation and mechanism-reduction tools in the research community, for example, further augment the practicality of using molecular-based fuel models in simulation.
The past decade has proven the importance of engine design tools as the automotive industry responded to the challenges of providing a product with great performance at low emission levels for gasoline and diesel fuels. The next decade will be even more of a landmark as companies work to maintain a high level of performance, while continuing emissions reductions with the growing usage of a wider variety of fuels.
For more information visit: http://www.modelfuelsconsortium.com
More Stories
Automotive Industries (AI) Newsletter April 2025
Bangkok International Motor Show 2025 – The Talk of Sensuous Automotive
Earn GHG reduction values through MOL Pure Car Carrier “Book and Claim (B&C)” service