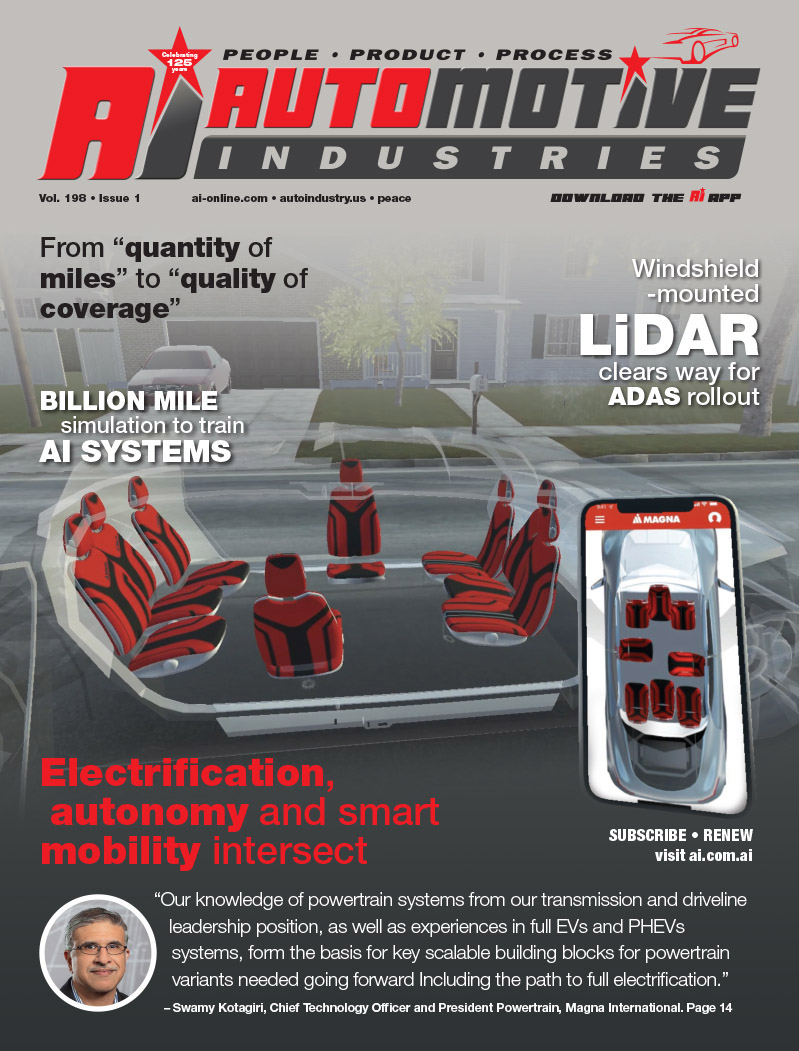
Once confined to the digital world, the term and concept of “convergence” is now being found in the nuts and bolts of automotive design and manufacture. Where the digitization of signals led to voice, data and video converging on shared pathways to end up on the same device, convergence in the physical world of motor cars comes from a shared need with the aviation industry to shed weight, optimize energy use and improve safety.
This is not really new – during the World War II years, Automotive Industries was called “Automotive & Aviation Industries”.
This could well be the next wave of convergence following on the still evolving connected car. The convergence of information technologies has translated into the “connected car” for the Millennial generation. High speed in-vehicle data connections and fail-safe computing power are also needed to manage the engine, transmission, suspension and a myriad of other factors in real time. One of the results of the addition of leading edge information technology (IT) into the design mix is that the doors were opened for a new generation of Tier 1 suppliers, which have adapted telecommunications and data management systems to meet the needs of the automotive industry. These new entrants have found a particularly strong niche in the electric and hybrid vehicle segments.
Technology is also coming from the aviation industry. Systems once considered too expensive and too complex for anything on the road other than perhaps Nascar, Formula 1 or ultra-sophisticated (read “expensive”) cars is making its way into suburban runabouts. ABS brakes are one example. They were developed in 1929 for aircraft use by French designer Gabriel Voisin.
What we are now seeing is a convergence of technologies when it comes to the bodywork and cabling within cars, airplanes and even satellites. Designers of all three are faced with the same challenges – shed weight, increase strength and reduce costs.
Aluminum alloys, which have been used in aircraft since the 1930s, are working their way down from the high end to runabout bodies. They are, of course, already found under the hood in engine components.
Aluminum has particular appeal for OEMs as it is both lighter than steel and relatively easy to recycle. With governments around the world starting to hold manufacturers responsible for the full lifecycle of the products they sell, recyclability is an important consideration.
Aluminum has competition in the form of carbon fiber. It was first used in aircraft manufacture in the 1940s, and has since made its way through the aerospace and sports industries into automotive design and manufacturing. World polymer production overtook that of steel in the 1970s. Scientists are working hard on replacing synthetic polymers with sustainable and renewable organic polymers. Growing your own hoods, bumpers and other body parts beats having to rely on fossil fuels as a base. The use of organic polymers by the auto and aerospace industries is, of course, well established – the rubber in the tires, hoses and other fittings comes from trees.
What all this means is that automotive designers and their suppliers should perhaps be keeping a constant watch on developments in the aerospace industry. Steel, for a start, has been phased out wherever possible in order to save weight. We are also seeing the first hybrid and electric aircraft taking to the skies. Here is an industry which is accustomed to being at the leading edge of technology, and its suppliers could well be in a position to challenge the traditional dominance of established Tier suppliers to the auto industry.
On the flip side, the trend cuts both ways. Developers of power plants, electronic systems and body parts for the auto industry could find that they have a new market in aerospace. Hence, for the first time, this edition of Automotive Industries features an aircraft
More Stories
8 Best Plastic Welding Techniques for Automotive Manufacturing
5 Big Reasons to Choose LED Bulbs for Your Car Headlights
How much does it cost to ship a car on Amtrak Auto Train?