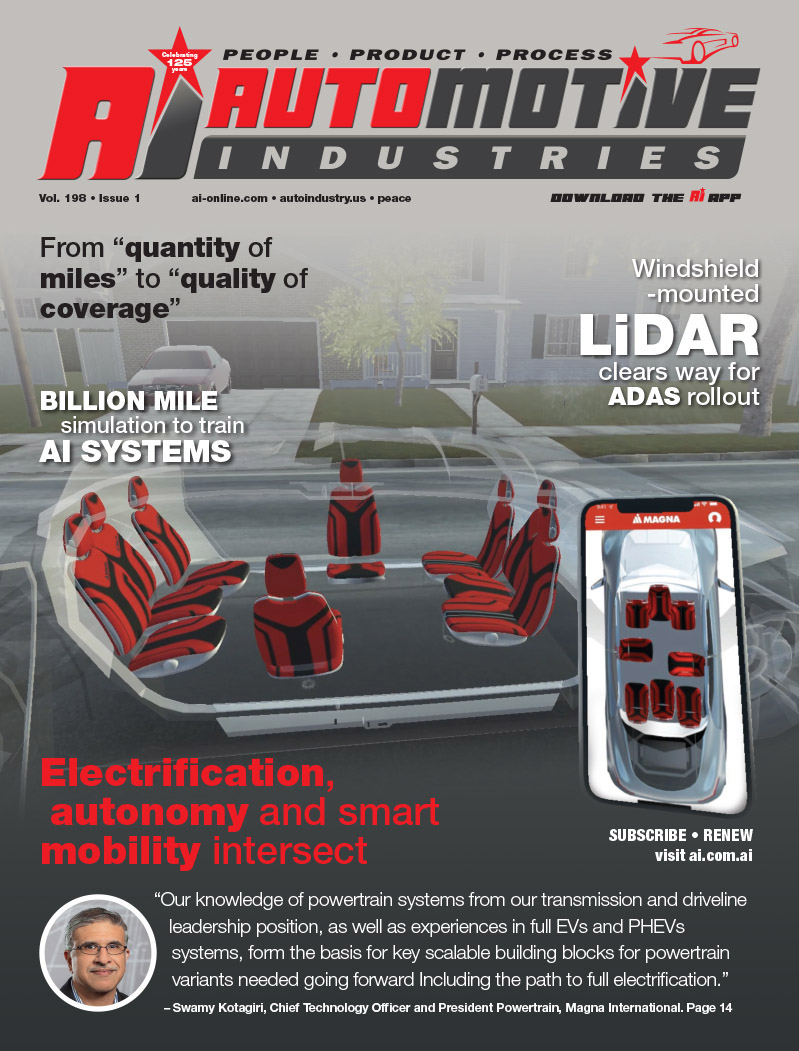
The German CT CoreTechnologies GmbH develops computer-aided-design (CAD) data conversion software. Established in 1998, the company’s customers include those in the automotive, aviation and consumer goods industries. Some of CoreTechnologie’s clients include Daimler, Chrysler, MAN, Bosch, TRW, Johnson Controls, Airbus and Boeing. The company opened a branch in Detroit, USA, last year, to tap the huge automotive market there – especially for its 3D_Evolution software package which is used by a number of automotive companies.
For example, Continental Automotive Systems, a global supplier of chassis, powertrain and brake systems, chose 3D_Evolution for worldwide implementation of its automatic data exchange system as well as the advanced healing and feature recognition capabilities. Continental Automotive Systems implemented the 3D_Evolution package to enhance its ability to provide critical 3D design data to its factories around the world. The world-wide introduction of 3D_Evolution began in January 2006 and was extended to the US in mid-2006.
Similarly, Webasto Automotive, a global supplier of roof systems, moveable body systems, and temperature management systems, chose 3D_Evolution for its automatic data exchange and migration system. By using the software’s advanced healing and feature recognition capabilities, Webasto Automotive enhanced its ability to provide critical 3D design data to its plants and suppliers around the world in any CAD format required, either as a parametric model or B-REP solid. During an intense six month evaluation of many software packages including Proficiency, Theorem, Open DXM, and CATIA’s internal exports, 3D_Evolution was found to maintain the highest degree of accuracy over all.
Christian Donitzky of Webasto AG said: “3D_Evolution is providing Webasto with the necessary advanced migration tools to facilitate data between CATIA V4, CATIA V5 and Unigraphics, and also the ability to convert them to such formats as step, sat, x_t, jt, rf and vice versa with our supply base in a loss-free data environment. On average, we are saving over 90 per cent in rework time associated with model clean-up. As an example, with one of our suppliers, we were able to turn a 15 hour job around in less than 1 hour. The quality of the software is very good. The internal functionalities to reduce open faces and incipiencies raises the quality of the models and does not change the geometry’s initial design. With these advanced tools we are seeing dramatic improvements in our data migration and interoperability with our suppliers. The easy access, the large variety of formats and the quality of the results make 3D_Evolution the optimal solution for our data translation needs.”
The 3D_Evolution software is faithful to the policy of CoreTechnologies – To save time and simplify work by seeking innovative solutions more constantly, easily and powerfully. The company showcased its latest version of 3D_Evolution at Euromold in 2007.
CoreTechnologies Inc. tells Automotive Industries about the 2008 version of 3D_Evolution.
What’s new in 3D_Evolution 2008?
In the latest version of 3D_Evolution 2008 CAD (Computer Aided Design) conversion software, CoreTechnologies is proud to present its enhancements to the feature-based kernel for the conversion of CAD models with a full history tree and parametric. CoreTechnologies has also enhanced its software in cooperation with demands from its 350 clients in advanced healing kernel, simplifier, and FEM tools for mid-face generation, as well as offset solids. 3D_Evolution’s powerful de-featuring capabilities have bridged the gap between CAD and CAE (Computer Aided Engineering) departments globally. When you have completed a feature-based translation, 3D_Evolution has the ability to use an automated model comparison for validation. CoreTechnologies has taken away the chore of the engineers/designers, allowing them to focus on the core design. A lot has been achieved with 3D_Evolution 2008, providing all the more reason to go into detail illustrating these new functions and modules.
Feature-based as a standard
The standard feature-based module of 3D_Evolution includes native interfaces. This allows the conversion of CAD models with history and parametric, without the need to access the license of the source CAD system. CAD models between the prevalent systems such as CATIA V4, CATIA V5, SolidWorks, Pro/E and Unigraphics can be converted with a full history tree (known as a parametric model). Native interfaces read not only the B-REP data, but also the history and parametrics of the CAD models directly from the native data. Thanks to this exclusive technology, the seamless transfer of all information is achieved. These algorithms guarantee a smooth and automatic generation of the model by the target application. During conversion, the feature-based kernel also implements the adaptation and optimization of the assembly structure, feature and related parameters, attributes, B-REP geometry, as well as optimized process exactly adapted for the respective target system. Specifically for CATIA V4 models, the linearization of the tree and the recognition of hole features is possible, so as to adapt the tree structure to the procedure of modern CAD systems. The automatic generation of the models in the CAD-systems occurs automatically through CoreTechnologie’s Plug-ins integrated in the respective target systems.
The new feature-based kernel is absolutely unique to CoreTechnologies. Imported skins, volumes and solids are first adjusted through healing functions without losing parametric, which is useful in the case of mixed models, since the necessary basis for the safe generation of feature operations, based on import solid, is created. With the integrated compare function, the resulting geometry can be compared to the source model. Potential discrepancies greater than the user-defined tolerance are documented through a log file and are highlighted in the graphical user interface of 3D_Evolution.
New healing function
The new healing function automatically replaces interoperability, ensuring effective data translations for all CAD-Systems. The 3D_Evolution conversion engine supports all primary CAD formats such as CATIA, Unigraphics, Pro/Engineer, SolidWorks, Robcad and many more, allowing the user to access the data without the CAD system licence. This function heals surfaces within seconds through new faces, at the same time correcting edge curves and basic surfaces. The user selects the surface to be replaced, and the rest of the operation runs fully automated. Even if the model initially shows many corrupt surfaces, the mistakes detected by the integrated VDA Checker can be repaired through this function. The well known healing functions for the removal of over-lapping and gaps, as well as the stitch function for the generation of continuous transitions between faces, have been accelerated through algorithm optimizing.
Intellectual Property protection – Simplifier with new functions
The 3D_Evolution Simplifier Module can, with the push of a button, generate a bounding geometry of individual parts or assembles. It thus automatically calculates the bounding geometry of single parts and assemblies. This is indispensable for the protection of intellectual property or even for the generation of simple models for VR and Digital Mock-up. The simplifier module automatically simplifies 3D models. Features such as drill holes, cavities, or grooves are closed and simplified. The removal of the model’s complexity will drastically reduce the file size in a matter of seconds, making it ready for assembly studies, manufacturing studies or FEM calculations. New bodies that, following simplification, are completely surrounded by other bodies and therefore invisible in assembly, will be automatically deleted. Users of 3D_Evolution can generate a script to repeat the process in batch mode.
FEM de-featuring module
Automatic finite element mesh generation of CAD-generated data has been a goal of finite element meshing codes for years. However, the lack of accuracy and the amount of detail in the data have made this a daunting task. In essence, the CAD data needs to be de-featured to overcome accuracy deficiencies and to remove excessive detail. The new de-featuring module includes removing fillets, holes, round offs, and chamfers. This tool has added value in preparing the model for meshing, CFD (Computational Fluid Dynamics), durability and other CAE analysis. What took hours can be completed in minutes! Through parameters, the de-featuring function can be flexibly configured such that radii or chamfers can only be considered for a definite size for de-featuring. Through the internal script language, this function can be adapted to the integration of an automated process.
Geometrical model comparison
With the Advanced Compare function, the geometry of two 3D models can be compared. 3D_Evolution can record geometric differences exceeding user-defined tolerance, and display this on the model in a special 3D_Evolution viewer format. The whole process can also be run in batch mode and for complete indices, whereby an HTML-log data lists the results for all models. The generation of the viewing model showing the discrepancy in detail occurs only when discrepancies are actually present. The comparison can be run interactively for single models as well, with the calculation period being very minor, resulting in hardly any waiting time.
Offset solids in batch mode
In close cooperation with the German automotive industry, a new Offset function has been enhanced. The so-called skins (for example, in CATIA V4) are endowed in automatic mode with measurements, then converted into CATIA V5 native format as solid models. 3D_Evolution requires no CAD licenses for the process, since all prevalent CAD formats can be natively read and written. The desired material thickness is selected in batch mode directly from the source data. The healing guarantees that mistakes and inaccuracies are first adjusted on the skin prior to Offset. After Offset, the system runs another analysis and, if necessary, independently runs a further healing-operation. Automation, process security and model quality can be realized through 3D_Evolution healing functions.
Companywide deployment through Web interface
Companies are looking for ways of automating the engineering chore of translation with advanced healing, geometry simplification, and de-featuring. With the new Enterprise Batch Manager and a normal Web browser, all users of a company network have equal access to the 3D_Evolution batch mode. Users are able to individually define conversion tasks in heterogeneous Windows, Linux and Unix operation surroundings, to be handled in a central job list. In case of extensive amount of data conversions in the shortest amount of time, several computers in the network can distribute the data for the defined conversion. The enterprise Batch Manager uses the resources optimally, distributing the conversion tasks on the single machines without any time delay.
More Stories
What to Do After a Motorcycle Accident to Protect Yourself
Injured in a Motorcycle Crash? Talk to an Attorney Now
Danisense launches ‘Online Calibration Portal’ to offer brand agnostic calibration services for current transducers and smoothen the whole process