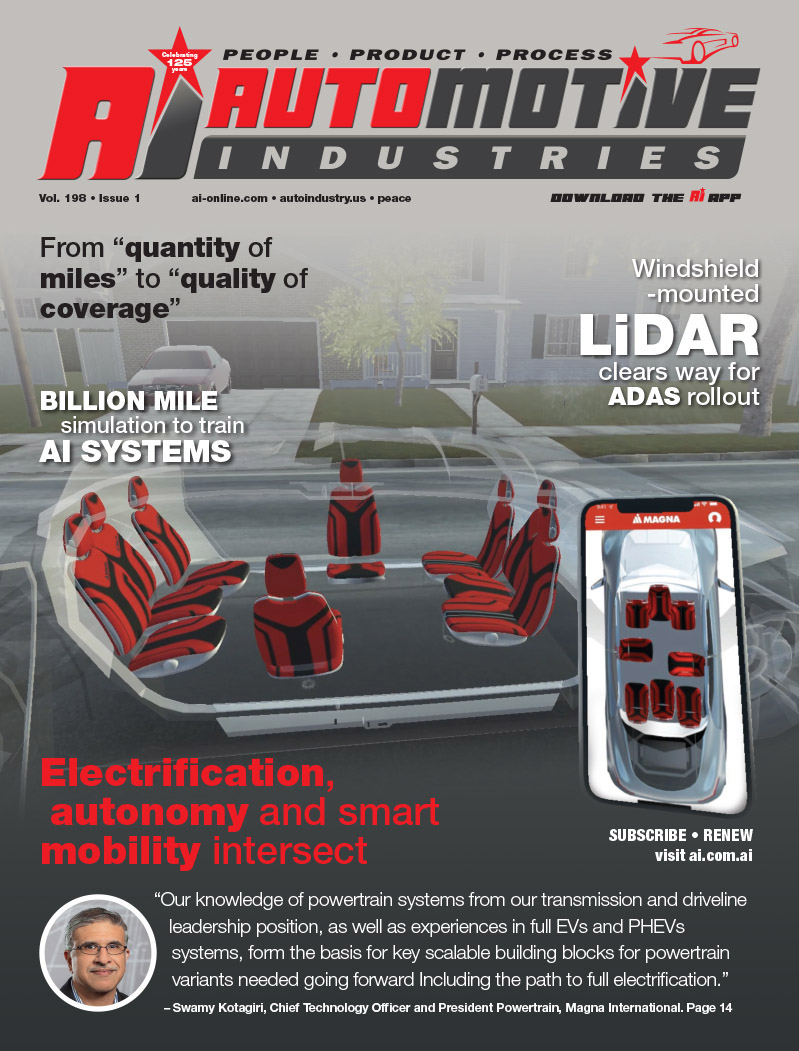
Vehicle capacity is one of the great mysteries of this industry. It seems that everyone counts it differently — much of the time to prove a particular point. Be it Wall Street, Washington, the Big Three or the Japanese OEMs, the measurement of the capacity to build vehicles conjures up confusion for most.
The way we see it, vehicle capacity and the measurement of it is quite simple. Straight time capacity is the classic measurement. What is the highest annual capacity without overtime for a given facility? Each facility has a different maximum line rate on two shifts for a given number of regular workdays per annum. In some cases, 3-crew or 3-shift formats are considered. Maximum capacity integrates the legal overtime capability with straight time capacity. For a manufacturer to simply slice a production shift from a facility is not a cut in capacity. Instead an analysis requires one to ask the basic questions of who, what, where, why and when to understand vehicle capacity dynamics. Each facility has a unique build process, labor history, geographic advantage/disadvantage, structural issues and political importance.
Possibly the most important of these factors is “who.” Each manufacturer utilizes their own build processes and shingling order to assemble vehicles with little ability to share the process with other manufacturers. Additionally, each facility is laid out to optimize this process or, as is the case with older facilities, the process is modified to optimize the existing facility, Whatever the case, the concept that vehicle capacity can be measured in its totality as if it was some large sea that ebbs and flows is ludicrous. Ill-informed financial analysts and media-types will frequently refer to “too much vehicle capacity” as if it is an industry problem. Correction folks, it is the issue of specific manufacturers. Toyota, Honda and Renault/Nissan are looking for additional capacity but are certainly not willing to assume someone else’s facility and the associated legacy costs, a suboptimal plant layout or a labor force they did not train. Ford’s overcapacity is Ford’s problem to solve — not Honda’s.
Often “what” is built at a facility underscores the stability of demand and the inherent integrated facility flexibility. A full-frame bodyshop cannot build a unibody vehicle — at least not currently. While selected OEMs are working on this ultimate flexibility it does not exist in today’s structure. This pigeonholes several facilities. Additionally, to lower investment costs, several manufacturers have restricted bodyshop and paintshop flexibility, which forces the plant to build only one platform or a range of bodystyles from a platform.
Case in point. DCX’s underutilized Belvidere, Ill., facility that builds the Neon couldn’t integrate production of its PT Cruiser platform stablemate due to paint shop issues. Instead the folks in Auburn Hills recently expanded the Toluca, Mexico, facility at a cost of $300 million. Forethought with respect to facility flexibility could have saved money down the road.
Increasingly, “where” is becoming very important. As was the case with Toyota’s new San Antonio facility, a presence in the U.S. south and the prospects of being closer to the Texas truck market were more important than locating the facility closer to the Midwest supply base. Similarly, as increased populations shift to the south and sales prospects grow in Mexico new capacity will shift in this direction. Product lifecycles and union contracts have a greater hand in determining “when” capacity is shuttered, upgraded or established. One would notice that Big Three plant closures in the U.S. and Canada have to be “negotiated into” the agreements at three or four-year national contract intervals. Incremental or revitalization investment usually only occurs when a new platform is slated for production.
Lastly, the “why” is potentially the one aspect that cannot be quantified. Canada/ U.S./Mexico politics, regional incentives and even spreading political influence take a hand in why a facility is shuttered or established. The politics surrounding plant closures during last year’s CAW/Big Three negotiations underscores this. Each of the Big 3 have or will soon close a Canadian plant while promising to maintain employment through new or expandshould employ similar trade-offs.
Vehicle capacity is more the parts and less the whole. With overall capacity rising 870,000 units in North America from 2001 to 2008, the difference resides in the mix.
The Big 3 in total are expected to shed annual straight time production capacity of 1.2 million units on a net basis while the new domestic OEMs add almost 2 million units.
Beneath the surface, the interaction of the five “W’s” determines vehicle capacity in the future. Unions, governments and communities alike will have to face facts — future survival of many OEMs will depend on effective and efficient use of production capacity in all facets of the industry. Capacity has to be restructured and reshaped — simply not drained off.
Michael Robinet is Vice President, Global Forecast Services, CSM WorldWide Inc.
MichaelRobinet@csmauto.com www.CSMAuto.com
More Stories
8 Best Plastic Welding Techniques for Automotive Manufacturing
5 Big Reasons to Choose LED Bulbs for Your Car Headlights
How much does it cost to ship a car on Amtrak Auto Train?