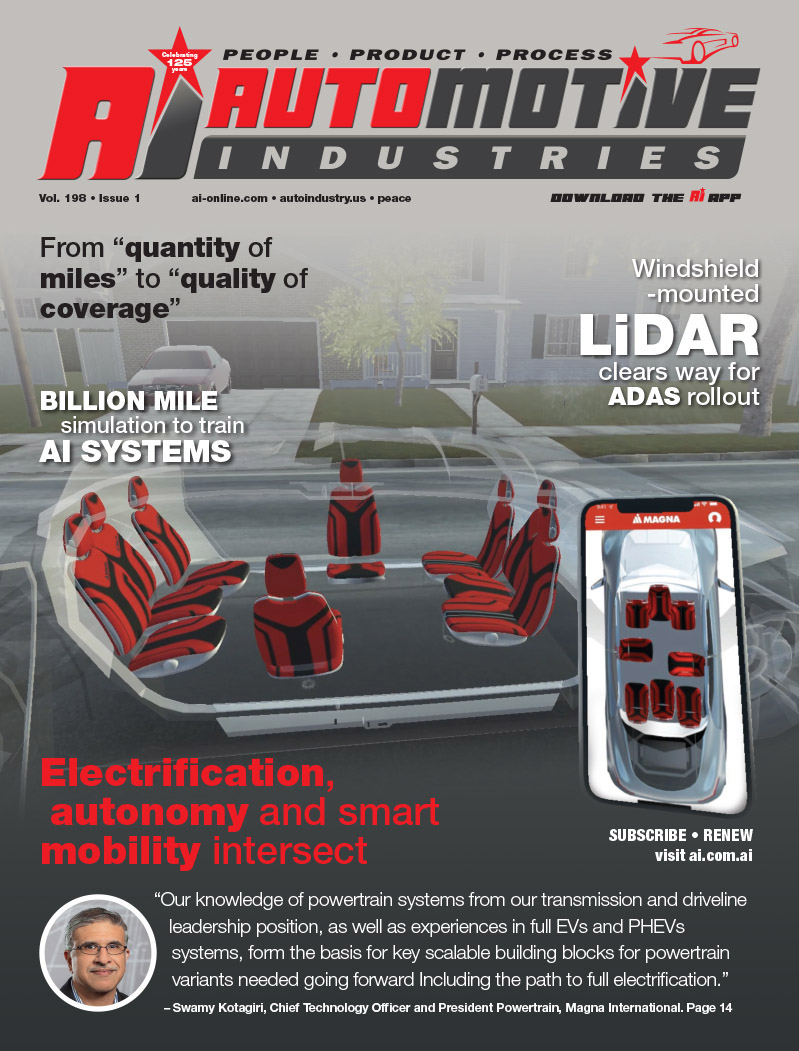
The Finnish Radiator Manufacturing Company Ltd (Finnradiator), manufactures radiators for the automotive market. Established in 1926, the company’s focus has been on the design and production of various types of tailor-made radiators for heavy-duty trucks and off-road vehicles such as agricultural and construction vehicles. It sells its products mainly in the Scandinavian, Central European and Japanese markets. Finnradiator offers a range of radiators – most of which can be customized to a specific requirements. “At the moment we have both traditional copper-brass soft soldered production line and CuproBraze line for manufacturing different types of radiator and heat exchanger cores, also a variety of different reservoirs, fasteners, and components are manufactured in our own production facilities. All coolers are carefully manufactured according to the customer’s measurements,†says the company.
In 2004, Finnradiator, which also is known as Suomen Jaahdytintehdas Oy or SJT, adopted the CuproBraze® copper/brass brazing technology. The company acquired a midsize-volume-production brazing furnace and purchased additional capital equipment in 2005, leading to today’s debut of the complete production line. The durability of CuproBraze® heat exchangers was the main reason why the company adopted the technology. In addition, CuproBraze® heat exchangers typically provide the advantage of smaller size and/or greater heat rejection compared to any of the alternatives.
“In the past year, it became clear that CuproBraze® would have to be a part of our product offering. We made an extensive study comparing aluminum brazing with CuproBraze®. We noticed in particular that aluminum charge air coolers would have problems at elevated operating temperatures. Cuprobraze® is the only way to meet coming requirements economically, without the need for pre-coolers for the charge air coolers,” said Hannu Vetikko, managing director of the company in 2004 in a press statement.
The CuproBraze® production facility went online in March 2006. The company says that the CuproBraze® technology helped it meet the challenges set by stringent European Union emission norms. The CuproBraze® Alliance predicts that one million brazed copper-brass heat exchangers in service by 2007.
Apart from radiators, the Finnradiator also makes heater cores and fan shrouds. “We manufacture different radiator systems according to customer needs. The production of radiator systems includes the planning and manufacturing of a complete module, as well as assembling the finished system. Careful planning of the system chassis and frame ensures the compatibility of the different parts. The system can be finished off with a variety of fan shroud solutions,†says the company.
The company is headquartered in Suolahti, in Central Finland. The company’s production facilities have received the ISO-9001: 2000 and ISO 14001: 2004 quality certifications. Founded in 1926 by three tinsmiths, Finnish Radiator Mfg Co primary focus was radiators for the automotive industry, but as technology advanced the company quickly moved into other applications including charge air coolers, heaters and fabricated sheet metal products.
Automotive Industries spoke to Hannu Vetikko, managing director of the Finnish Radiator Mfg Co Ltd.
AI: Please tell us a little about your company’s cooperation with Luvata and SHAAZ.
Luvata has been our raw material supplier for years. As we started to build our CuproBraze production line, co-operation went even deeper. During these last three years we have discussed almost daily about CuproBraze with company Luvata. Luvata has given us major support in knowledge of brazing process and CuproBraze material properties. With company Shaaz we have discussed about radiator technology and shared our experiences of CuproBraze.
AI: How has the CuproBraze® technology improved your production – are all your products made using this technology?
Compared to the copper-brass soft soldering process, which we still have parallel to CuproBraze line, I must say that we are now at much higher level from a technical point of view. Both product and production performance are much better than two years ago when we started the CuproBraze project. During this autumn 95 % of radiator cores will be manufactured in this new line.
AI: How did the CuproBraze® help your company make products that met EU requirements?
The production itself is environmental friendly because it eliminates the use of hazardous wastes, toxic substances and consumes a lower amount of energy. Also brazing furnace is equipped with an after-burner unit, it removes unwanted chemical emissions from the exhaust. With our CuproBraze charge air coolers our customers can meet the EU requirements without using any pre-coolers. The CuproBraze materials are much stronger compared to aluminium. CuproBraze also gives higher thermal performance and strength without changing the size of core.
AI: Please tell us a little about your company’s automotive client list and how you keep up with their customization requirements.
Our main focus is in manufacturing of radiators and heat exchangers for heavy-duty trucks and other off-road vehicles. Our customers typically manufacture construction or agricultural vehicles (tractors, harvesters, and forestry vehicles), mining equipments, marine engines, defence vehicles etc. All coolers are designed in co-operation between our design department and customers. This requires good communication and relationships; our focus is in open discussion. I think this is the only way to get to know our customer requirements.
AI: What are some of your future plans to take your company’s business to new markets?
Finnradiator is continuously exploring the export markets for possible new customers for CuproBraze coolers. Our biggest advantages are flexibility and speed. We strongly believe that also foreign customers appreciate these features. We have increased our advertising and marketing in foreign media in order to get more visibility for the company. I believe in future Finnradiator will be strong in charge air cooler market and also in power plant business.
More Stories
What to Do After a Motorcycle Accident to Protect Yourself
Injured in a Motorcycle Crash? Talk to an Attorney Now
Danisense launches ‘Online Calibration Portal’ to offer brand agnostic calibration services for current transducers and smoothen the whole process