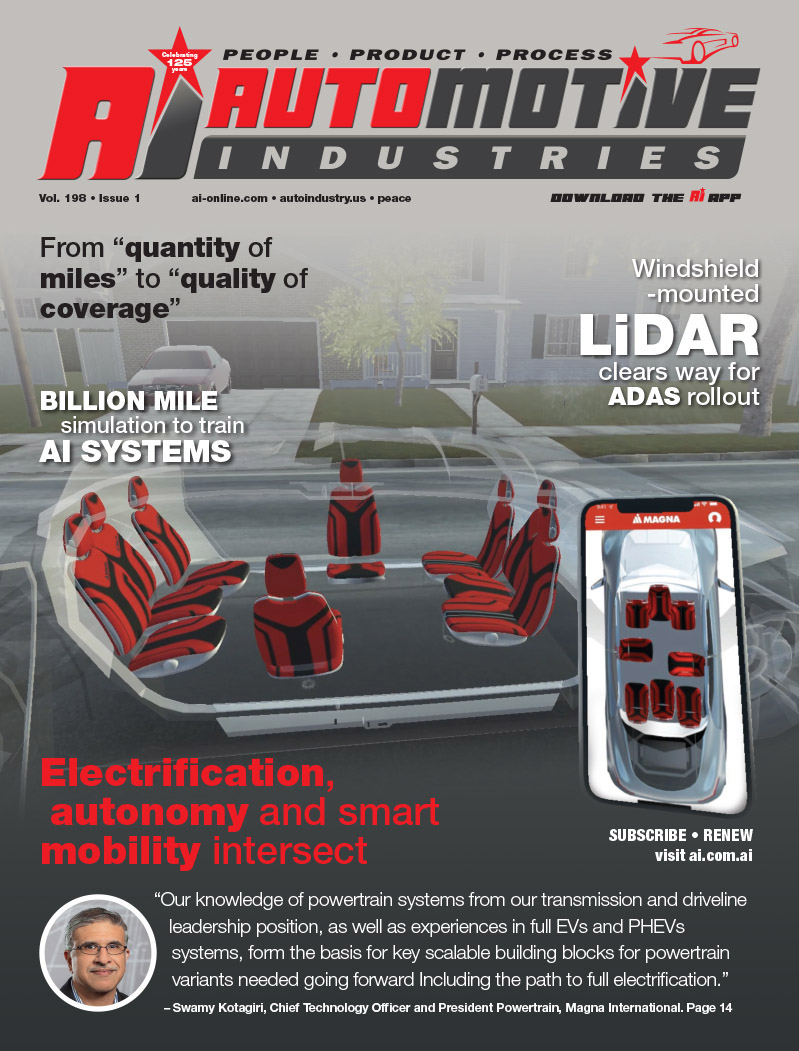
Austrian-headquartered firm Borealis is on a three-pronged mission – to cut vehicle weight through innovation, to expand global supply capabilities for the automotive industry and to strengthen global on-ground support. For the first target of making vehicles lighter, Borealis’ auto¬motive solutions offer mechanical properties, sound-dampening advantages, weight reduction and higher processing performance so providing global original equipment manufacturers (OEMs) and Tier One suppliers with a viable alternative to traditional higher density engineering plastics.
Within this focus on lightweight innovation, Borealis, together with its joint venture Borouge, is consolidating its existing product brands, such as Xmod™ and Nepol™, and introducing the new Fibremod™ brand as a benchmark for glass-fiber reinforced material. Fibremod GD301FE, for example, has been used in place of denser engineering plastics for the construction of pedal carriers and front-end carriers. This results in up to 15% weight savings and 10% lower system costs compared to a polyamide (PA) solution. The 30% glass fiber reinforced PP offers improved processing, high performance, and high stiffness with no pre-drying step. Earlier in 2013 Borealis and Borouge showcased components and under-the-bonnet applications used by BMW and Fiat / General Motors at the VDI International Conference held in Mannheim, Germany.
In 2012 the two companies introduced a new grade of polypropylene (PP) specified for use in lightweight bumper applications for two new Renault automotive platforms. High flow Borcom™ WH107AE was specified for the recently introduced Dacia Lodgy, a minivan produced at Renault’s plant in Morocco and for the Renault Twizy, Renault’s first electric car produced at its plant in Spain. Borealis and Borouge inaugurated a new PP compounding plan in Shanghai, China, in April 2010 to support global customers in Asia. The company also has two production sites in Brazil, where Borealis is currently expanding the site in Itatiba. The expansion in Brazil is taking into account a significant market growth in the future, driven by automotive and appliances customers.
At the request of OEM partners, Borealis is also expanding its Fibremod production capacity in Europe with the recent inauguration of a new LGF (Long Glass Fiber) production line in Monza, Italy. Borealis’ efforts to strengthen global on-ground support have led to the formation of dedicated Key Customer teams, providing better supply capability and support to Tier 1 and OEM customers in the automotive industry. The move is part of a consolidation of product brands and a new focus on Driving Tomorrow – which embodies Borealis’ approach of investing in innovation for lightweight solutions to benefit the global automotive industry.
Automotive Industries (AI) asked Jost Eric Laumeyer, Global Marketing Manager, Borealis Engineering Applications, to expand on the thinking behind the brand revamp.
Laumeyer: Our brands Xmod and Nepol have been very well established in the market over the last decades and are very well known to our customers. Since 2010 we have shifted our strategy towards replacing Engineered Plastics, such as polyamids with our Borealis Engineered PP solutions. Our glass reinforced PP grades are also playing a very important role in that strategy. Bundling material performances, easing product overview and enabling a strong association between a brand name and innovative products led us to the decision to create the new Fibermod brand name.
AI: What are some of the major challenges in your supply/marketing network that have impacted your automotive business? What changes have come out of these challenges?
Laumeyer: It is fantastic to see how Engineered Polypropylenes have developed over the last 30 years in automotive applications, beating other plastic growth curves. The average PP consumption per car is estimated at around 60 kg in Europe, and although PP has always created challenges from the automotive industry in the past, it has resulted in engineered innovations such as bumpers, fenders and door panels. The challenge continues and we will further contribute to solutions, especially when it comes to making cars lighter to improve fuel consumption. Here we have recently commercialized several new programs where the density advantage of Borealis PP led to lighter automotive parts as air intake manifolds, IP carriers and pedal carriers.
AI: What are some of the Borealis’ latest technologies that will help?
Laumeyer: We are focusing on getting into material areas where PP did not play a big role in the past. Therefore we upgraded our glass reinforced PP product portfolio by adding tailor-made LGF (long glass fiber) PP grades from our own in-house source in Monza, Italy. The technology we are now using in Monza is a breakthrough technology, delivering superior mechanical properties which are required in applications such as IP carriers.
AI: How would you describe Borealis’ ability to respond quickly to fast-moving developments in the automotive sector?
Laumeyer: The configuration of the PP LGF production line in Monza is a good example of how we are working within our Borealis organization. It became clear for us that we needed to develop a new LGF production technology because existing technology and products would not be able to withstand future higher product requirements. Therefore the Borealis Automotive team and our colleagues from R&D developed together a new and robust technology, which our manufacturing team translated into a large-scale production line in Monza. This is a great example of where we reacted fast to customer requirements, connected the right people together and implemented this project in 1.5 years.
AI: How do you see the market for performance polymers growing, especially today when green transport is a critical issue?
Laumeyer: The current mega trends in the automotive world are clearly visible in all of our customer visits. Lightweight materials and sustainability aspects are key deliverables for resin suppliers like Borealis. We clearly believe that our Borealis Engineered PP product offering already provides solutions to those mega trends, but the journey will go further for performance polymers like PP.
AI: How do Borealis and Borouge work together to develop technologies – does the primary responsibility for R&D lie with the parent company?
Laumeyer: We are making those developments where it makes sense. What is important is that the customer stays central in all activities we as Borealis and Borouge are doing. As our customer base is global, we need to make sure that the customer gets what is expected on time and at the required location. This needs to be coordinated between Borealis and Borouge, and should not have any impact on the customer. From both sides we are very well equipped and have the right people on board to develop new technologies and grades for our global customer base.
AI: What are some of the recent developments in plastics that you think will change the way automotive manufacturers use them?
Laumeyer: The Borealis PP offering is more and more in the minds of our customers’ design engineers, as they have the ability to push limits. Let me add a personal note to that. I started in 1995 as a design engineer in another global chemical company. At that time I was working on projects to design air intake manifolds in Polyamid 6.6 for customers. Doing this, I could not have imagined that this application could be done in PP. In 2010, when I joined Borealis, I learned that this can be done as the first air intake manifold in PP was launched by VW, using a glass reinforced PP grade from Borealis. My vision is that PP from Borealis will further support “Driving Tomorrow”!
More Stories
What to Do After a Motorcycle Accident to Protect Yourself
Injured in a Motorcycle Crash? Talk to an Attorney Now
Danisense launches ‘Online Calibration Portal’ to offer brand agnostic calibration services for current transducers and smoothen the whole process