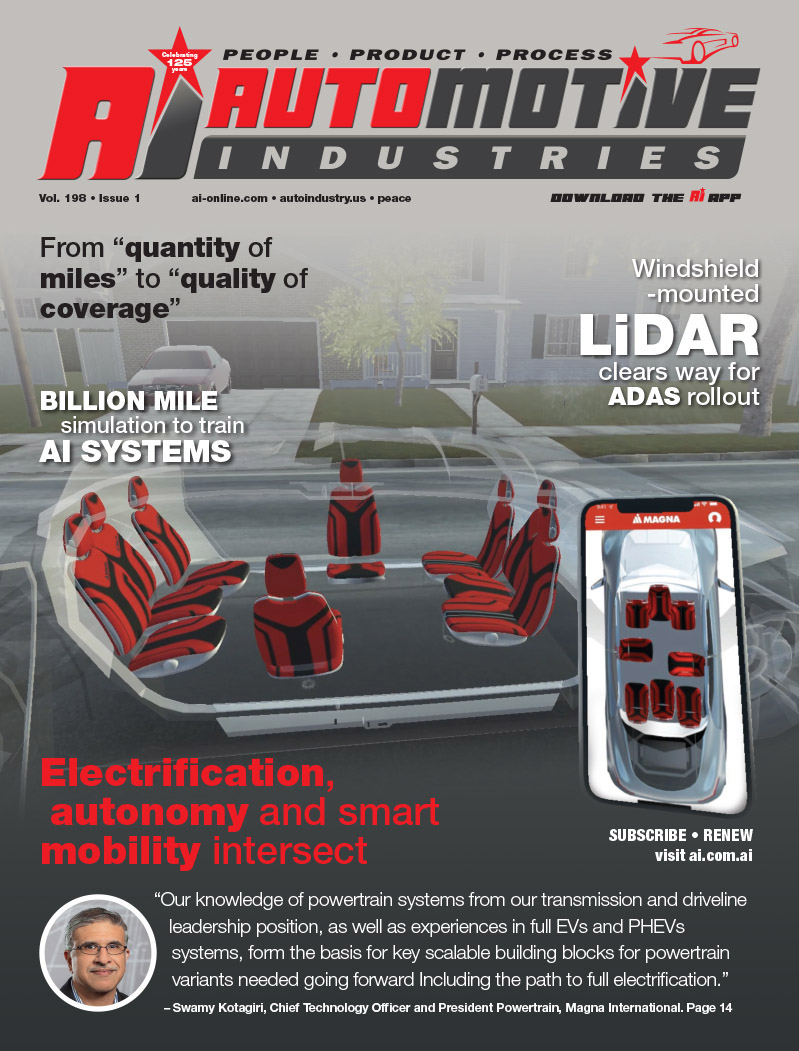
Innovation is as much about using existing applications and materials in different ways as it is developing all-new materials and combinations of materials.
One of the companies leading the innovative use of aluminum in automotive manufacturing is Hydro Extruded Solutions. Norway-based Hydro is a fully integrated aluminum company with 35,000 employees in 40 countries on all continents.
Automotive Industries (AI) asked Jonas Bjuhr, European Product Development Director Hydro Extruded Solutions, what trends he sees influencing the increasing demand for aluminum in the automotive sector.
Bjuhr: The main trend is lightweighting, for both internal combustion and electrically-driven vehicles. E-mobility is contributing to the big impact because it changes the platform design, which in turn means different solutions. It also means that there are new suppliers and that different partnerships are being formed. Another trend is safety. Aluminum components provide a number of advantages over a number of other materials.
AI: What extrusion solutions will be most beneficial to OEMs?
Bjuhr: There are different levels of structural components and parts – electrical, thermal, chassis and even the electric motor, where there is interest in extruded aluminum casings. Because a full electric vehicle has no engine in the traditional sense there is a completely different approach to design, which traditionally is dictated largely by the engine and the performance you want from the car. With electric cars you need to accommodate the batteries and to have frames to protect and isolate them from the occupants and the rest of the structure. So, there is a lot of impact on general structural applications. In addition, there are also thermal solutions that are driving more interest and creating more demand for aluminum.
AI: And in BIW?
Bjuhr: Audi and Jaguar Land Rover are the pioneers in the production of full aluminum vehicles. Now with electric vehicles there are some big changes in the philosophy of how to design BIW. We see more mixed materials solutions. I would say this is especially true for the big structural parts that help protect the occupants. Here the benefit is that the extrusion is generally cost-effective when you have a modular design. Having an extrusion with a complicated form is something that the OEMs are also interested in exploring, especially where they want to introduce more vehicles starting with lower volumes which will grow over time.
AI: What alloys and multi materials do you offer?
Bjuhr: Within that group we have a range of solutions. Many of the alloys have been used for a long time, but the trend is to develop new alloys with higher strength to ensure you can keep the form and maybe reduce weight and use it to increase performance. In addition to this we focus on recyclability. Aluminum as a material is good for recycling, for the carbon footprint and good for the world. We are introducing alloys with a higher content of post-consumer scrap. We are working on both the material properties and green credentials of the materials.
AI: How closely do you work with the car manufactures?
Bjuhr: We are working closer and closer. We are the biggest aluminum company, so we have a lot of competence, especially now that the industry is seeking new solutions for new challenges. It is also clear and very important for the car manufacturers to have good suppliers that are willing to participate in the process of finding the best solution. This is something that we are very passionate about. We have our engineers working together with our customers to advise on different solutions, different options. If we are in the loop from the early stages we can really understand what our customers need – matters such as how to combine different materials. Here you need the right joining technology to ensure the end of life sustainability aspect is taken care of properly.
AI: What are the challenges and advantages with multi materials in terms of lightweight, safety, design?
Bjuhr: One of the challenges is that the demands are higher and higher. So, we as a material and solutions company need to continue with innovation. And that’s clearly what we see in the industry. With respect to the materials we have to make sure that we get better and better. Each of the OEMs would have different priorities. Either they focus on certain types of materials because that is what they are confident with, or they can go towards multi materials. It can be steel, it can be aluminum, or it can be plastics or carbon fibers. Within each material you have different levels of extrusions and sheet components.
All this is creating some challenges as to how to combine them cost-effectively, with good performance in all the joints. Joining is really a key consideration for us, to understand how our materials can be joined to other materials for maximum use of aluminum. But, it is also important to consider how to design and take care of corrosion properties and the durability aspect. We have to understand the challenges, so we can become an even better supplier and always offer the right material and the right alloy for the component.
AI: How are new technologies such as hot metal gas forming, and new applications of friction stir welding helping to increase resilience, reduce weight and save costs?
Bjuhr: If you are an engineer, and you are working with technology development, one of the most exciting things is how the new technology can benefit the product. It is not just the possibility of the technology within itself. It’s always important to understand where the value is in introducing new things. We are one of the leaders in technologies like friction stir welding, and one of the first ones to industrialize it for other markets like marine. Now we see new possibilities in the automotive market with e-mobility. With other technologies like hot metal gas forming we open ourselves up for completely different design solutions. It allows us to form very exotic and interesting shapes, very different and more efficient. We work very closely with the customer to evaluate this form technically and cost-wise. Industry demand is increasing for higher strength components, which also creates challenges in the processing of materials and components at an industrial scale. We are getting very close to the point where we will have proven the technology for serial production of components.
AI: How does the recent acquisition of the remaining 50% of SAPA help with Hydro’s positioning globally?
Bjuhr: This is very exciting opportunity for the whole company. We are the leader when it comes to aluminum competence. It is clear to us that aluminum extrusions are not the only solution. There are lots of sheet components and other types of aluminum solutions. We have a lot of researchers, a lot of internal collaboration. We have to make sure that all the competence that we have is accessible to our customers. From that perspective this will be extremely exciting to see how we can develop and drive the use of aluminum especially in the automotive industry.
AI: In 2017 you opened a new plant in Wales to build lightweight aluminum panels for the new London Hybrid Taxi. What’s next for Hydro?
Bjuhr: We have to continue exploring new opportunities, and would like to become even stronger in automotive by getting closer and closer to our customers. We want to be involved, we want to help as much as we can, making sure that our customers can really benefit from the performance, cost and reliability of aluminum. We would continue to invest both in people and resources to supply this growth.
Components for the new London taxi fleet supplied by Norsk Hydro.
More Stories
Is Your 70 Series Land Cruiser Underperforming? Here’s How to Unleash Its True Potential
What to Do After a Motorcycle Accident to Protect Yourself
Injured in a Motorcycle Crash? Talk to an Attorney Now