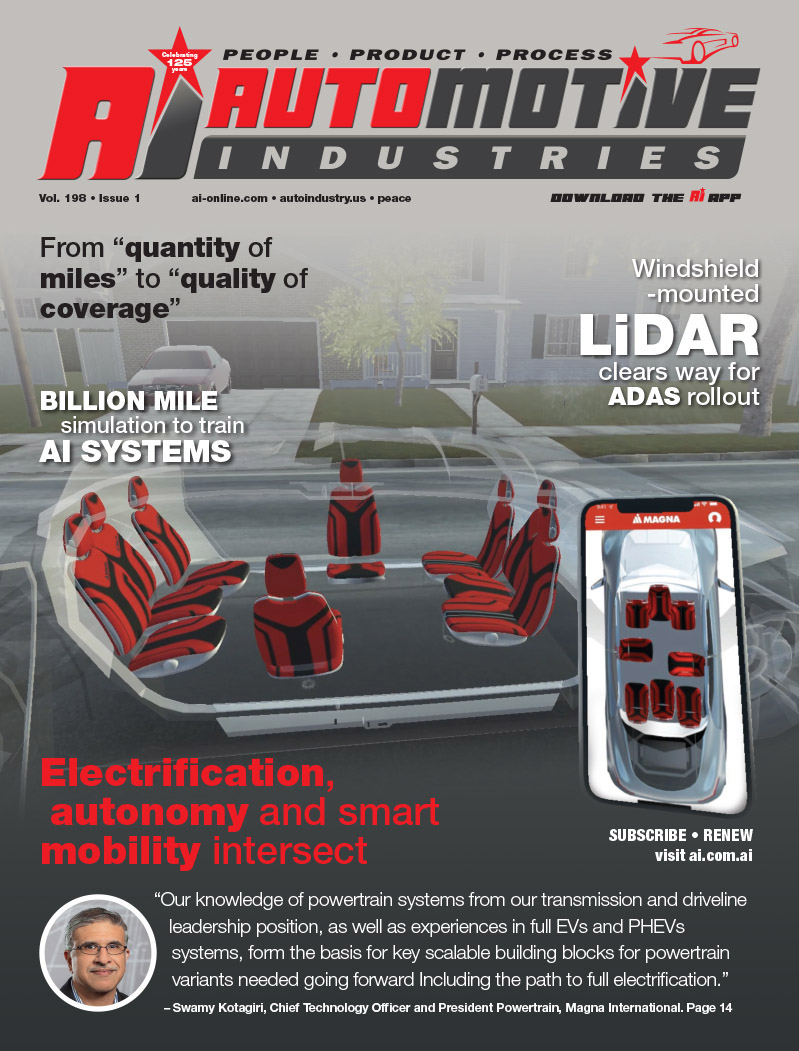
Technology developed to control heat and sound for luxury sports cars is now going mainstream as OEMs and their Tier 1 suppliers strive to comply with more stringent emission regulations.
Mannheim Germany – based Thermamax Hochtemperaturdämmungen is one of Europe’s leading suppliers of high-temperature insulation systems. Founded in 1923, its products are found in most street-legal high-performance sports cars – and a growing number of passenger vehicles. “Through the early integration of the high-temperature and acoustic insulation in the planning process, our customers save both development time and costs,” says Thermamax.
The company also helps its customers understand how individual components behave when subjected to heat and how the component and the insulation harmonize under full load by offering field simulation of the thermal conditions in the exhaust system using various insulation constructions in the in-house hot-gas test facility or thermographic recordings.
In response to the need to reduce exhaust emissions across the spectrum in Europe and other markets, Thermamax has invested over Euro 2.4-million in new machines and technologies. A large percentage of its yearly turnover is channeled back into research and development in order to improve products and employee training.
Automotive Industries (AI) asked Markus Formanski, Thermamax business unit manager (automotive) what was unique about their system.
Formanski: Basically, the principal is that we retain the heat inside the pipe – unlike the conventional heat shield, which keeps heat away from the car body. The breakthrough is that we have developed a way of providing better insulation performance with thinner insulation. Internal temperatures of up to 1,000 degrees C are kept to an external 100 degrees C by just few millimeters of insulation This means we improve performance, reduce weight and keep more heat in the exhaust – which reduces emissions and improves fuel consumption. This solves a number of problems, the most important of which is the performance of the exhaust system, which relies on high temperatures in order to meet the emission standards. Another benefit to the OEMs is that designers and engineers now have more space for other components.
What impact are the new emission regulations are having on the industry, and on Thermamax?
Formanski: It is very exciting. The regulations have transformed a “nice to have” product into a “must have” product. In many applications, the exhaust system will only meet the standards if fitted with our insulation products. What this means for Thermamax is that we have gone from a niche supplier to high-end street-legal sports cars to a much wider range of vehicles. We have invested in people, systems and equipment in order to meet this increased demand.
AI: How do your solutions help automotive OEMs meet the increasingly stringent emission norms?
Formanski: OEMs are happy to deal with us because we have a very long history. We continued to invest in new technologies and systems even during the downturn. Their attitude to us is changing because they know that some of their systems will not work without our solutions.
AI: Are there any unique challenges?
Formanski: OEMs sometimes do not see the big picture – by keeping the heat inside the pipe, we are impacting on the whole car environment. The insulation also helps deaden the sound entering the cabin. In some companies, this leads to a failure to adopt the technology quickly because of inter-departmental differences. One department does not want to have to pay for a solution which results in savings for another department.
AI: Let’s talk technology again – what is different about your manufacturing processes?
Formanski: We are different to most of competitors in that we start with the design of the fiber. Other companies buy in the fiber and build their solutions around what is available in the market-place. We do not design the fibers by ourselves, but work closely with our customers to come up with a solution. We have almost everything in-house, starting from foundation research to prototyping to the production lines for producing high volumes of textiles and metal components.
AI: How do you work with Tier 1 and other suppliers?
Formanski: We are very flexible, and set up the logistics line to suit our customers. In some cases we deliver the materials to the Tier 1 supplier, who then applies them to the parts. In others we supply the insulation. We can also supply fully assembled components just-in-time to the Tier 1 customer.
AI: How does the technology assist with sound deadening?
Formanski: We have developed a sound deadening product that is heat resistant up to 1,000 degrees C. Our products can also combine sound and heat deadening properties, and are tuned to the frequency of noise generated by the component. Gas and diesel engines produce different frequencies of noise. We achieve this by using different layers – each of which has its own task, such as reducing noise, absorbing or reflecting heat. The technology is so efficient that an OEM project team we were working with to reduce the ambient noise in a diesel-powered car was pleasantly surprised when we were able to reduce levels in a current project by up to 4dB at once – they were used to dealing in increments of 0.1dB or 0.2dB.
AI: Tell us about Thermamax’ quality control standards.
Formanski: OEMs and Tier 1 companies who work with us for the first time are pleasantly surprised at the level of quality – from the functional prototype in early stage. We are often told that the prototypes look like serial production parts. Quality begins with the sourcing of raw materials, and constant in-house testing. We have our own test benches for the materials and designs in order to reduce the time to market.
In April 2011, Thermamax was presented with the Caterpillar Supplier Quality Award for reliability and the excellent quality of the insulation components supplied. Our processes and components are certified to ISO/TS 16949:2009; DIN EN ISO 9001:2008 and module D of code 96/98/EG of ship’s gear; and EN ISO 3834-2 (welding process) quality standards, as well as the ISO14001:2008 environmental standard. In addition, Thermamax is a member of VDA, VDMA, and supplies a number of leading companies.
AI: What are your plans to expand your business to meet demand?
Formanski: Our Mannheim plant is located in the centre of Europe, and is being expanded to meet demand across the continent. We are able to assemble 300 000 components such as manifolds and turbochargers a year. High-end 3-d laser robots are being installed in order to meet the required production and quality levels. We have the ability to grow further organically – we have the people and the space. In the United States, our Chicago plant is ready for serial production, with initial capacity of 100 000 units a year. And, when there is a need to expand, we do it. We will respond to the needs of our customers.
More Stories
What to Do After a Motorcycle Accident to Protect Yourself
Injured in a Motorcycle Crash? Talk to an Attorney Now
Danisense launches ‘Online Calibration Portal’ to offer brand agnostic calibration services for current transducers and smoothen the whole process