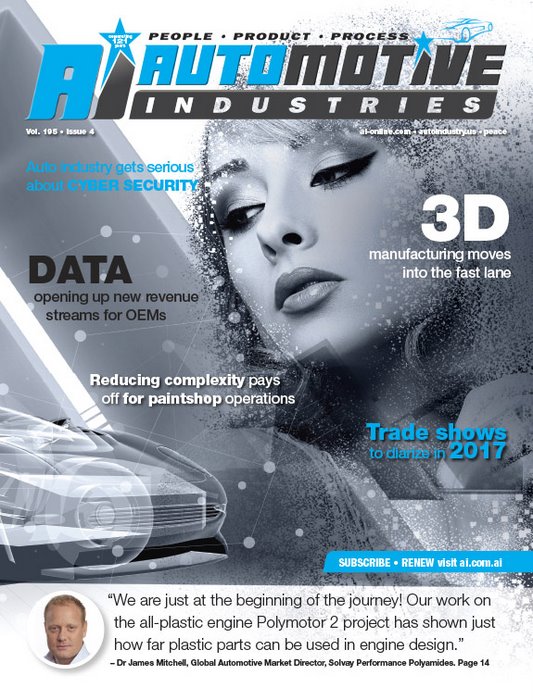
One of the enduring transformational trends in the auto industry is the move towards producing more environmentally sustainable vehicles while preserving power efficiency and driving pleasure.
In the process OEMs and Tiers are inventing the technologies of tomorrow for “green vehicles” – such as Hybrid Electric Vehicles (HEV) and autonomous cars. In this “greenolution” the plastic industry has a key role to play in supporting manufacturers to significantly reduce the CO2 footprint of vehicles by reducing weight.
The latest advances in plastic technology were put on display at K2016 hosted in Dusseldorf, Germany.
International chemical group Solvay showcased its latest high-performance polymer solutions for metal replacement in today’s down-sized, turbocharged automotive engines. The technology included 3D printing powders, polyamides providing environmental benefits, thermal performance materials and advanced solutions speeding up the development process of new applications.
Automotive Industries (AI) asked Dr James Mitchell, Global Automotive Market Director, Solvay Performance Polyamides, what role Solvay is playing in the future of the engineered plastic car.
Mitchell: As a major player in polyamide based performance materials, Solvay is working on a myriad of different applications to help lightweighting and CO2 reduction. These are being developed in close and inclusive collaboration with OEMs and Tiers to help them bring the solutions to market in an efficient way. We are continuously working on products and solutions for 2025 and beyond. This leads us to be at the forefront of innovation.
AI: What are the applications for Solvay’s performance polyamides?
Mitchell: Lightweighting is a key target area for the automotive sector, and one in which Solvay is able to provide global solutions. Charge air coolers (CACs), air intake manifolds (AIM) and radiator end tanks (RETs) are large volume key applications for polyamide use.
Solvay is working on improving the heat and chemical resistance of its grades to enable further integration and functionality of the end parts. On high thermal performance side our teams developed the new Technyl® REDx series which are able to self-strengthen and actually become more resistant over time at elevated temperatures. This patented breakthrough technology enables further downsizing of engines using turbo systems. On the other hand, we are also improving existing solutions for chemical resistance. An example is Technyl® D218CR V33, which offers OEMs design flexibility in the reuse of exhaust gasses without worrying about corrosive acid condensates.
Auto electrical and electronics applications are also increasing rapidly. Parts such as sensor housings, connectors, chargers, battery components and circuit breakers are required to function correctly during the lifetime of a car or truck. However, the engine compartment of a vehicle is a harsh, dirty and hot environment which can play havoc with auto electronic systems. Over the years we have gained extensive knowledge in our consumer electrical and electronics market which we are now able to put to work in the automotive industry. This expertise enables us to offer a family of highly stable fire retardant and electrically resistant products. These materials are formulated to contain the least possible percentage of metal particles in order to eliminate the possibility of contact corrosion leading to electrical faults.
AI: Tell us a little about the new products you showcased at K 2016.
Mitchell: There were three core messages:
- More Protection with our high performance fire resistance range of Technyl® One products
- More Freedom with our range of Sinterline® Technyl® polyamide 6 (PA6) powders for SLS 3D Printing prototyping and functional small runs
- More Future with our launches of Technyl® REDx for high thermal requirement for auto turbo systems and our new Technyl® 4earth® eco-friendly polyamide 6.6 (PA6.6).
Technyl® 4earth® grades are the result of the Move 4earth® revolutionary patented process. This technology has been designed to transform technical textile – initially post-production airbag wastes, into high-quality PA6.6 grades while reducing environmental impacts. This complements Solvay’s Technyl® Force portfolio of engineering polymers. We have a number of new applications developed at customers on high performance parts using this product range.
Move 4earth® is one of several Solvay initiatives supported by the European Commission as part of its LIFE+ program, demonstrating the company’s ongoing strong commitment to sustainable development.
AI: What is the significance of the 60 years of performance and innovation of Technyl®?
Mitchell: Technyl® is a brand that has transcended the ages. It is a benchmark in terms of quality, reliability and innovation. We are 60 years young and just getting going! The launch of our Technyl® Force group of super heroes portraying our key competencies in metal replacement, thermal management, fluid resistance and fire retardancy highlights how we are focusing the brand on the most relevant challenges on our end market.
AI: How far can lightweighting be pushed?
Mitchell: We are just at the beginning of the journey! Our work on the all-plastic engine Polymotor 2 project has shown just how far plastic parts can be used in engine design. Thanks to our latest predictive simulation software (MMI® Technyl® Design), prototyping (Sinterline®) and part testing (APT) services, we already can work on the next generation of lightweighting applications to take us to 2025 and beyond. If we look at how plastics are used today in sports cars and imagine similar parts being used in standard commercial cars, the list of potential opportunities is endless.
More Stories
What to Do After a Motorcycle Accident to Protect Yourself
Injured in a Motorcycle Crash? Talk to an Attorney Now
Danisense launches ‘Online Calibration Portal’ to offer brand agnostic calibration services for current transducers and smoothen the whole process