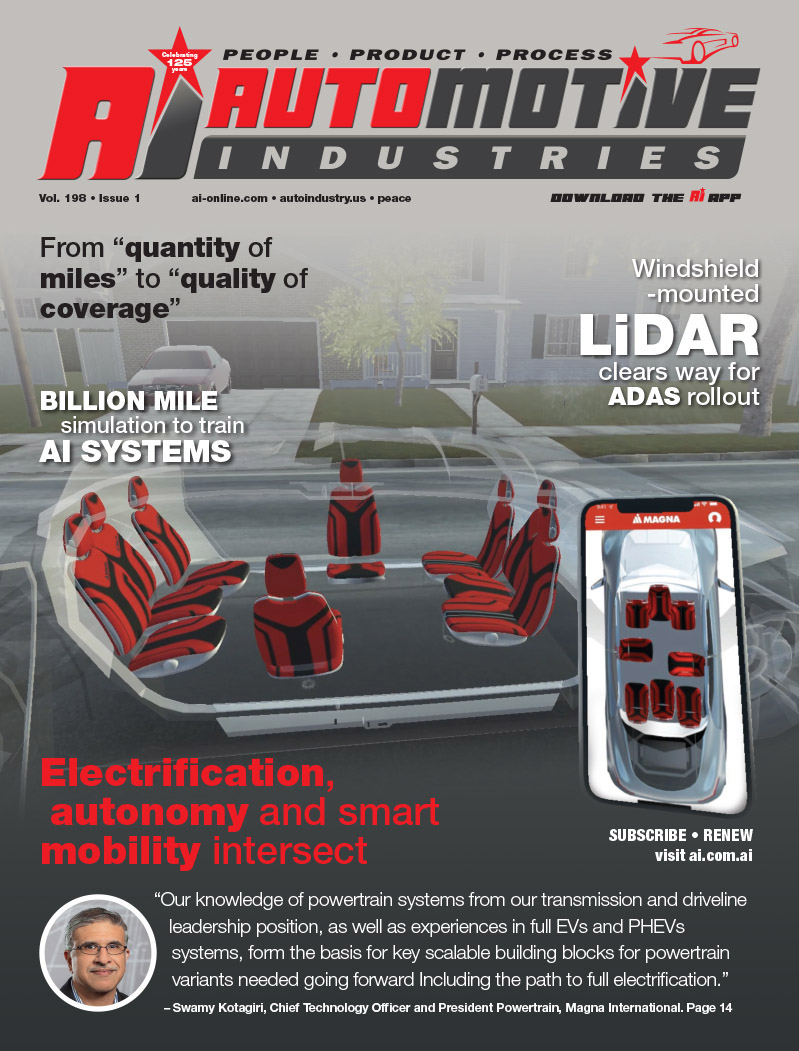
Patented in the United States in 1957, selective catalytic reduction of noxious exhaust gases using ammonia as the reducing agent is now coming into its own.
Development of SCR technology continued in Japan and the US in the early 1960s, with research focusing on less expensive and more durable catalyst agents. Urea SCR systems use diesel exhaust fluid (DEF) as a reductant. DEF is typically a blend of 32.5% urea and 67.5% deionized water. It is injected into the diesel exhaust stream ahead of a SCR catalyst. When the urea makes contact with the hot exhaust gases, ammonia (NH3) is released. The ammonia initiates a reaction where NO and NO2 molecules are broken down (reduced) into nitrogen, oxygen, and water. One of the biggest challenges has been that DEF freezes at 120 F (-110 C). The Norma Group, a global market leader in Engineered Joining Technology, is one of the pioneers in the use of automotive urea fluid transport systems. It recently launched the next generation of electrically heated urea pipes designed to overcome the problem of DEF freezing.
Automotive Industries (AI) asked Thomas Kraus, vice president business development Europe, Middle East and Africa to tell us more about the new system.
Kraus: Creating a new generation of urea transport systems is the logical consequence of our tag line: “Customer Value through Innovation”. During the market implementation of our first generation of electrical heated plastic urea tube systems – which was already a big step compared to heated elastomer systems – our engineers gained valuable experience about the disadvantage of externally heated urea lines. Based on this knowledge, they started to develop a solution that combines the advantage of plastic tubes with their narrow space geometries and low weight with the features of short de-icing times and low electrical power consumption.
AI: How does this compare with what is available?
Kraus: Standard electrical heated urea transport lines as they are used in the market today are designed with the electrical heating element on the outside of the transport tube or hose. This means that the heat is not where it is needed, as you have the transfer the heating power through the wall of the hose or the pipe into the urea fluid. As elastomer hoses and plastic tubes are excellent insulators, a lot of power gets lost, which leads to longer de-freezing times, which is a key feature of the system that the OEMs need to minimize. We turned this around. Our heating element is now directly in the urea fluid. This means that the heating rod is in the inside of the transport pipe. This required the development of a now patented Quick Connector to establish the electrical connection from outside to inside the tube system.
AI: What are the advantages of the new generation of Normaflex urea systems to the customers?
Kraus: First, it needs to be mentioned that our modified Quick Connectors still fit to the standard SAE spigots. Therefore, no changes are necessary to the customer interfaces. The free diameter inside of the transport pipe is still the same as in the old versions, without an increase in the outer diameter. This means the pipe has the same flexibility as a standard nylon fluid pipe and can be formed accordingly. Furthermore, the pressure loss is similar to externally heated systems.
Due to the fact that the heating element is directly inside the media, we were able to reduce the power consumption by about 50% versus standard systems on the market. In addition, the heating time can also be considerably reduced. Another big advantage is that can we partially avoid heating the Quick Connectors – which reduces power consumption, weight, complexity and also costs. Further cost reductions were achieved by the fact that we can use our standard pipes and quick connectors, and therefore our manufacturing technology. This results in a very high manufacturing process stability from the very beginning, which from a quality point of view is an important aspect.
AI: What were the biggest challenges?
Kraus: As the urea fluid has a very low viscosity and the tendency to creep out of every possible void, the sealing of the heating rod at the interface to the Quick Connector proved challenging. In the end, by following the proven sealing design of the SAE J0244 interface, we were able to establish a robust seal between the heating rod and Quick Connector.
AI: What are the next steps?
Kraus: The Normaflex Urea GEN2 pipes have already been in winter and summer tests at various global OEMs. Some of the approval tests are still ongoing, but we are also in the middle of the first series launch, which is going to happen in September 2011. After that, our PD department will start a new project to develop UREA GEN3, as we already talked with some of our customers about additional features that are needed achieve EURO6 and EURO7 solutions.
AI: What other products and systems does your company offer?
Kraus: Besides the standard clamping and connecting technology of approximately 35,000 articles for all kinds of industries, trades and private fields of application our Engineered Joining Technology business unit develops individual as well as standardized solutions for emission control, cooling, air intake & induction, ancillary systems and industrial fluid connector applications. For our customers in industries like passenger vehicle, truck and heavy equipment, engine manufacturing, railway, aviation, ship building and white goods manufacturing, we offer individually developed solutions. Clamps, couplers, connectors and fluid transporting pipe systems are set up from our modular system of components. The broad knowledge of our engineers based in our technology centers in EMEA, Americas, and Asia creates a basis for design-to-cost solutions, while supporting our customer’s requirements to meet new legal requirements while downsizing their internal combustion engines or implementing alternative drives like hybrids or electrical motors.
More Stories
Hexagon’s MAESTRO reinvents CMM systems through digitization
Speira brings research, politics and business case makers together
Automotive Industries (AI) Newsletter April 2025