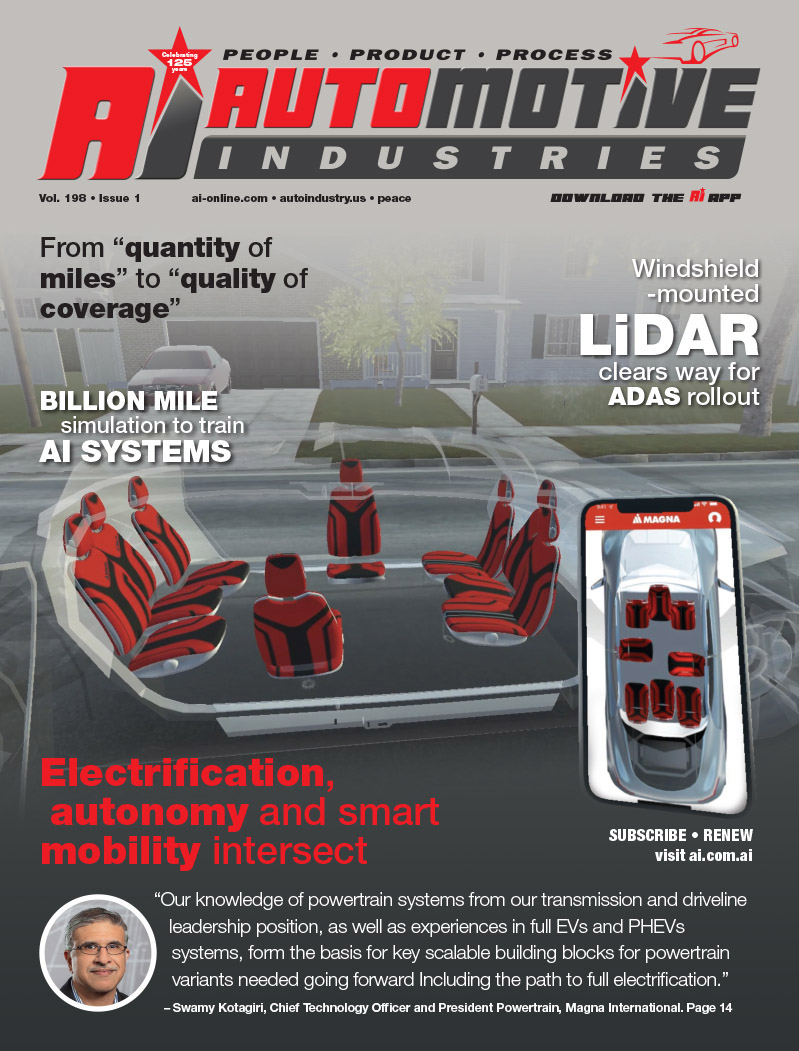
New developments in the area of fuel injection systems, ignition, valve train and ancillary systems from Delphi Corporation will help European manufacturers of gasoline engines meet growing demands for reduced CO2 and other tailpipe emissions without the cost and risk of radically different technologies. The new systems are part of Delphi’s broad portfolio of powertrain technologies for gasoline, diesel, hybrid and alternative fuel vehicles.
Helping OEMs meet tomorrow’s technical challenges at manageable cost
“Our strategy is to help vehicle manufacturers meet their emissions targets at minimum cost and with minimal technical risk by offering a portfolio of both revolutionary and evolutionary technologies,” explains Delphi Powertrain Systems engineering director, Europe gasoline engines, Dr. Sebastian Schilling. “Delphi’s understanding of the interdependencies of systems at the whole vehicle level gives us tremendous insight into their interactions, helping us see where the most cost-effective benefits can be achieved and allowing us to support a wide range of emissions control strategies.”
Delphi’s portfolio of technologies for gasoline engines includes port fuel injection, homogeneous and stratified gasoline direct injection (GDi) and compressed natural gas (CNG), new Multi-Charge Ignition, and the new electrically driven cam phaser (e-Phaser). “Whatever the engine technology strategy, we have systems that can simplify implementation, reduce costs and help deliver greater efficiency,” says Dr. Schilling.
New Multec(R) fast solenoid injectors provide high-performance GDi with lower cost and weight
Delphi offers two GDi injector strategies to meet today’s market
demands: a family of Multec inwardly opening multi-hole injectors for homogeneous combustion, and the Multec 20 outwardly opening injector for stratified engines. Both types of injectors are operated by conventional solenoid technology, which offers a significant cost advantage. Delphi’s Multec 20 Fast Single Coil solenoid injector, designed specifically for spray stratified lean combustion applications, provides outstanding spray and fuel injection performance at a significantly lower cost and lower weight than conventional piezoelectric technology. Spray-guided combustion has higher requirements than homogeneous direct injection for spray stability and penetration, fuel atomization, and the capacity for precisely controlled, closely-spaced multiple injections in order to produce the desired mixture distribution for robust flammability at the spark plug gap. To fulfill these requirements current production injectors use piezoelectric actuation in conjunction with an outwardly opening valve. Delphi’s Fast Single Coil injector maintains the performance benefit of the piezoelectric systems over conventional injection technology without the additional cost associated with the piezoelectric actuator and high voltage electronic driver circuits. Basically the same control system hardware can be used for the Multec family of injectors for homogeneous programs, and Multec 20 injectors for stratified applications. Both Multec types of injectors feature best-in-class NVH (Noise, Vibration, Harshness), which is important because it saves the vehicle manufacturer the cost and weight of additional noise reduction materials.
“By 2017, we expect a 40:60 split in the gasoline market in Europe between port injection and direct injection,” says Dr. Schilling. “GDi is essential for the accelerating trend toward downsized turbocharged engines as by cooling the charge it allows higher boost levels or a higher compression ratio. This results in a more fun-to-drive experience with better fuel economy.”
Optimized and cost-effective new CNG injector
“To support vehicle manufacturers considering alternate fuels such as CNG, which can reduce greenhouse gas emissions by as much as 25 percent, Delphi is developing an injector that is optimized for the unique chemical and physical properties of this low lubricity fuel,” says Dr. Walter Piock, chief engineer advanced powertrain. “A further benefit is that the new CNG injector can be driven by a typical gasoline ECM (Electronic Control Module) which enables low cost implementation. The planned introduction date is toward the end of 2011.”
New Multi-Charge Ignition optimized for GDi
Stratified charge GDi engines offer great potential — up to 20 percent part-load fuel savings compared with conventional gasoline engines. However, these engines can present significant challenges for the ignition system. Modern spray-guided combustion concepts have very short time intervals between injection and ignition. They also have highly varying fuel mixture concentrations close to the spark plug, which makes ignition more difficult. To address these issues, Delphi developed Multi-Charge Ignition which features single coil-per-cylinder control and fires the spark plug quickly and multiple times per combustion event to enable optimized combustion. The result is a significant improvement in both emissions and fuel consumption. It also offers the potential for switching to smaller and lighter ignition coils. Delphi’s Multi-Charge Ignition also helps decrease emissions at cold start and provides a more robust and smoother engine run at critical operating conditions. Additionally, it allows manufacturers to take full advantage of a stratified system by enhancing the lean burn process.
New electrical cam phaser (e-Phaser) for precise control even at engine start
Delphi will introduce e-Phaser, a new electrically driven variable cam phaser to provide vehicle manufacturers with another advanced valve train strategy that will help reduce emissions and fuel consumption. Compared with hydraulic cam phasers, e-Phaser delivers faster response times and an increased operating range, which enables precise and fast control from engine start. In stop-start and hybrid vehicle programs, the e-Phaser moves the camshaft to a preferred position before engine restart to help achieve short and smooth starting. Delphi’s new e-Phaser will also contribute to the continued development of homogeneous charge compression ignition
(HCCI) technology, which will further reduce fuel consumption and NOx emissions. Applied in conjunction with variable valve lift, Delphi’s e-Phaser will give engine designers the necessary control of part-load cylinder filling and help smooth the transition between the different operating regimes that are characteristic of HCCI engines.
Reduced power consumption with Delphi’s compact new brushless fuel pump
As well as supporting advances in combustion control, Delphi is developing a wide range of ancillary systems that will reduce parasitic losses and help engines work more efficiently. Building on more than 50 years’ experience in fuel handling systems, Delphi is introducing a new fuel pump, using a next-generation brushless motor architecture to deliver reliable, uninterrupted fuel flow at system pressure, high efficiencies, improved durability, wide-ranging fuels compatibility and a 1-2g/km CO2 reduction. Delphi’s brushless fuel pump is expected to enter production in 2012.
The higher power efficiency of the brushless motor, combined with the reduced pump speed when engine demand for fuel is low (for example at idle), significantly reduces the unit’s power consumption compared with conventional technologies. “The major challenge was to design a high efficiency brushless motor that can operate in a variety of fuels
— gasoline, diesel, alcohol mixes and even contaminated field fuels
— with a cost effective small package size. This is a significant achievement for the Delphi team,” says Delphi’s global sales director for fuel handling and evaporative systems, Jose Morente. As a result, Delphi’s brushless fuel pump allows the power consumption to be reduced by approximately 36% (or more, depending on application) thanks to the elimination of friction caused by brush to commutator interface in conventional pumps and the fuel pump controller, which runs the fuel pump at lower speeds to precisely match the engine demand. This latter feature virtually eliminates the need to handle recirculating fuel, which translates into evaporative emissions reduction as the fuel tank temperature is kept as low as possible.
“Delphi’s goal is to help OEMs meet the most challenging technical objectives at manageable cost and low risk,” concludes Dr. Schilling. “Our technologies and our high level of application engineering, supported by our global network of technical centers, will help them significantly reduce emissions without compromising quality, performance or customer satisfaction.”
ABOUT DELPHI POWERTRAIN SYSTEMS
Delphi’s powertrain technologies provide robust solutions to complex challenges, helping its customers develop vehicles that offer outstanding performance, refinement and emissions. They include multi port injection and gasoline direct injection systems; common rail and rotary pump diesel systems in a range of capacities and, for heavy duty diesel applications, electronic unit injectors and electronic unit pumps. They are complemented by innovative fuel handling, evaporative emissions, transmission control, valve train, and after-treatment solutions.
For more information about Delphi, visit the Virtual Press Room is at www.delphi.com/media.
More Stories
Avery Dennison PSA tapes support rapid evolution of EV batteries
Speira brings research, politics and business case makers together
Automotive Industries (AI) Newsletter April 2025