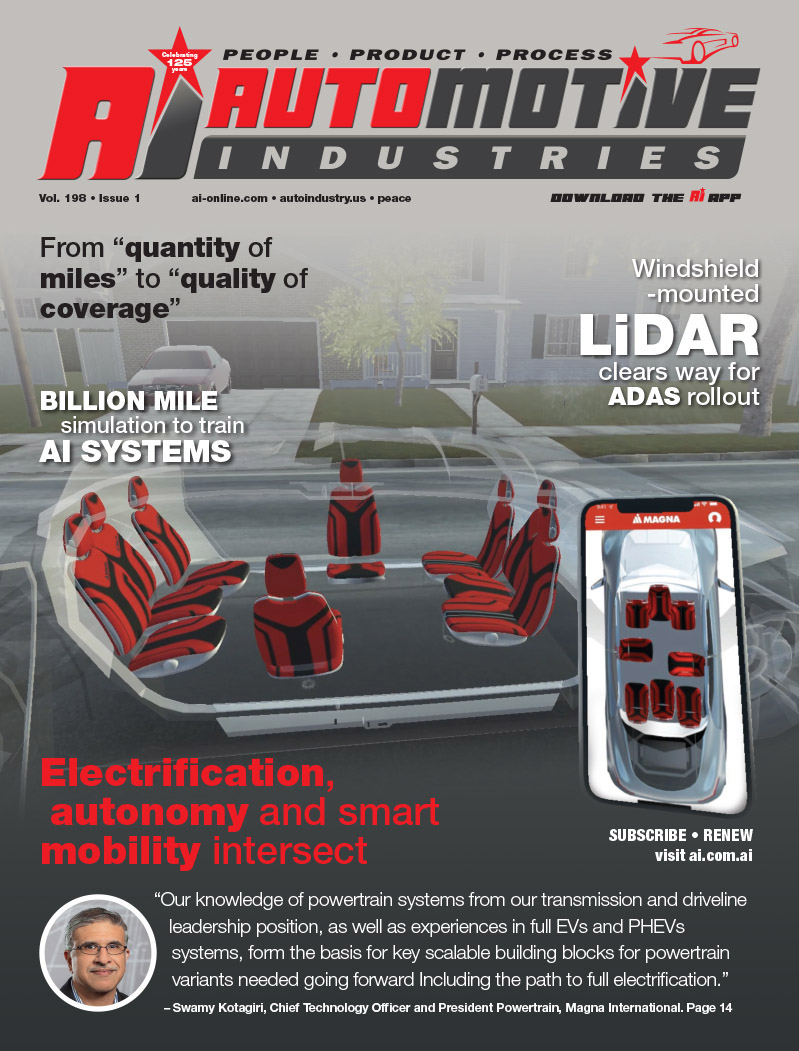
At this year’s Dürr Open House all of the Dürr Group’s business units presented their innovative technologies to industry experts. The in-house exhibition hosted by Dürr every two years took place with the motto: “Efficiency in the handling of energy and resources”.
EcoBell3: Maximum performance – lowest complexity
The most important new model launch in application technology is the EcoBell3, a new generation of atomizers for the electrostatic application of water-based paints in conjunction with external charging. The performance of this atomizer surpasses its predecessor by far. Its new features not only lead to minimal losses during color changes and shortened color change times, they also offer new process technology options. The most important element, however, is that the EcoBell3 is equally suitable for both interior and exterior painting. This was achieved by a very compact electrode ring. With it, the atomizer represents the ideal synthesis between high performance and process flexibility on the one hand, and the lowest complexity on the other.
The use of EcoBell3 offers the user considerable benefits. In one of the first orders with this atomizer for a sports car manufacturer, both interior and exterior painting were combined in one zone – the planned capacity of the plant allowed this. The benefit resulting from this was a significant reduction of plant length as well as the number of robots, and hence a reduction of the investment and operating costs. If a division of the interior and exterior painting scopes is needed for different zones – and this is certainly the norm in a paint shop – the use of EcoBell3 allows the work scopes to be distributed among all the robots in a way that optimal utilization takes place. In addition, this opens up the possibility of degrade functionality. This means that the failure of one robot in the painting scope can be covered by the remaining robot – a function that makes the so-called backup zones with manual application superfluous. This also significantly reduces plant length and operating costs.
An important application area for the EcoBell3 is the painting of bumpers and plastic components. From the application perspective, the bumper joins the demands of exterior and interior painting in one component. Large surfaces must be covered along with detail areas which partly include some very complex geometry that can only be realized with plastic parts. The painting process is made more difficult by the fact that the individual parts are usually positioned closely together on the product carrier and the cycle times are very tight. This application requires a compact, powerful atomizer with a high flexibility with respect to jet shaping, and the ability to paint continuously without interruption. The EcoBell3 optimally meets these conditions.
The EcoBell3 is only one component, albeit a very important one, of the overall “painting robot” system. This consists of the robot itself, as well as the integrated application technology. Together with the new linear color changer, the EcoLCC, and the compact dosing pump, the robot features a very slender arm that is ideal for applications with reduced accessibility. The application technique, as already described in detail, is designed for all painting tasks, an electrical potential separation system is not needed. High transfer efficiency and minimal color change loss are other important features of this simple and compact overall system.
The atomizer plays a vital role in today’s painting process. The EcoBell3 offers many advantages and possibilities, and not least it makes a significant contribution to the efficiency in the handling of energy and resources.
Ecopaint RoDip V – maximum maneuverability in the third dimension
In the field of painting equipment technology, Dürr has introduced a new variant of its high performance Ecopaint RoDip dip-painting process. The RoDip process optimizes the process of dipping, flooding and draining by rotating the entire car body. It is thus optimal for the transport of automobile bodies along the process line in the pre-treatment (PT), cathodic electrocoating (EC) and body washing processes.
In addition to the earlier variants RoDip M, with a drive chain on both sides of the tank, and RoDip E, with an electric drive positioned on one side, the new RoDip V offers maximum mobility in the third dimension. RoDip V has a vertical axis – which the V stands for – and thus significantly increased mobility. The vertically adjustable axis allows the car body to move particularly flexibly in freely programmable dip curves through the tank. This means that the car body can be rotated with RoDip V, but it does not have to be, and it is otherwise open to all curve shapes. Thus RoDip V means the greatest flexibility in the coating of all types of chassis shapes.
Another positive element of the vertical axis: the car body can be positioned over the dip tank at its own optimal draining angle. It is adjustable to all angles between 0 and 90°. This leads to higher quality and less rework. As with RoDip E, RoDip V is furnished with an electric drive positioned on one side, and is thus easily accessible from the opposite side in case of maintenance. The unit has a conveying drive and a separate drive for rotation. The transport unit is positioned via a path measuring system. A wireless signal is used to communicate with the controls.
For different technical requirements, capacities, and car body styles – Ecopaint RoDip M, E and V provide the appropriate solution for each application. Which of the three models to use depends mainly on capacity and flexibility requirements. All three technologies can be used for plant capacities of more than 100 units per hour. The RoDip variants differ economically depending on their production rates. The robust, mechanical RoDip M is more suitable for high production rates over 40 units per hour and the electric RoDip E is better for medium and smaller rates under 40 units per hour. Ecopaint RoDip V is especially interesting for special cases such as small production capacities or specific car body requirements. For truck cabs the choice between linear or rotary movement can be very helpful due to their relative difficulty in draining. In addition, RoDip V guarantees high flexibility with future model changes.
At its seventh open house in Germany from 12 to 19 March, Dürr made presentations to customers, business partners and journalists. The program included product demonstrations, lectures and discussions. It began with an expert forum on the topic of “sustainable production processes”, for which Dürr had its own in-house experts in addition to bringing high-profile speakers from the automotive industry. Volker Germann, head of chassis design at Volkswagen, reported on organic production processes at the second-largest automaker in the world. Dr. Fritz Mezger, who as Head of Paint Shop Planning at Mercedes-Benz is responsible for painting, presented innovative technologies and standards that will come into use in the future at the Hungarian plant in Kecskemet. Dr. Hans Schumacher, Managing Director of Dürr Systems GmbH, gave an overview of the most important new Dürr products. Dürr CEO Ralf Dieter stressed the main goal of Dürr’s R & D strategy: “Each product innovation from Dürr must be measurable by its contribution to lowering the customer’s unit costs. In this way energy efficiency is becoming ever more important.”
Dürr is a mechanical and plant engineering group that holds leading positions in the world market in its areas of operation. It generates about 80% of its sales in business with the automotive industry. It furthermore supplies the aircraft, machinery, chemical, and pharmaceutical industries with innovative production and environmental technology. The Dürr Group operates in the market with two divisions. The Paint and Assembly Systems division supplies production and painting technology, especially for car bodies.
Machinery and systems from the Measuring and Process Systems division are used in engine and transmission manufacturing and in final vehicle assembly, among other areas. Dürr has 47 business locations in 21 countries worldwide. The Group achieved sales of € 1.6 billion with approximately 6,100 employees in 2008.
More Stories
Hexagon’s MAESTRO reinvents CMM systems through digitization
Avery Dennison PSA tapes support rapid evolution of EV batteries
Speira brings research, politics and business case makers together