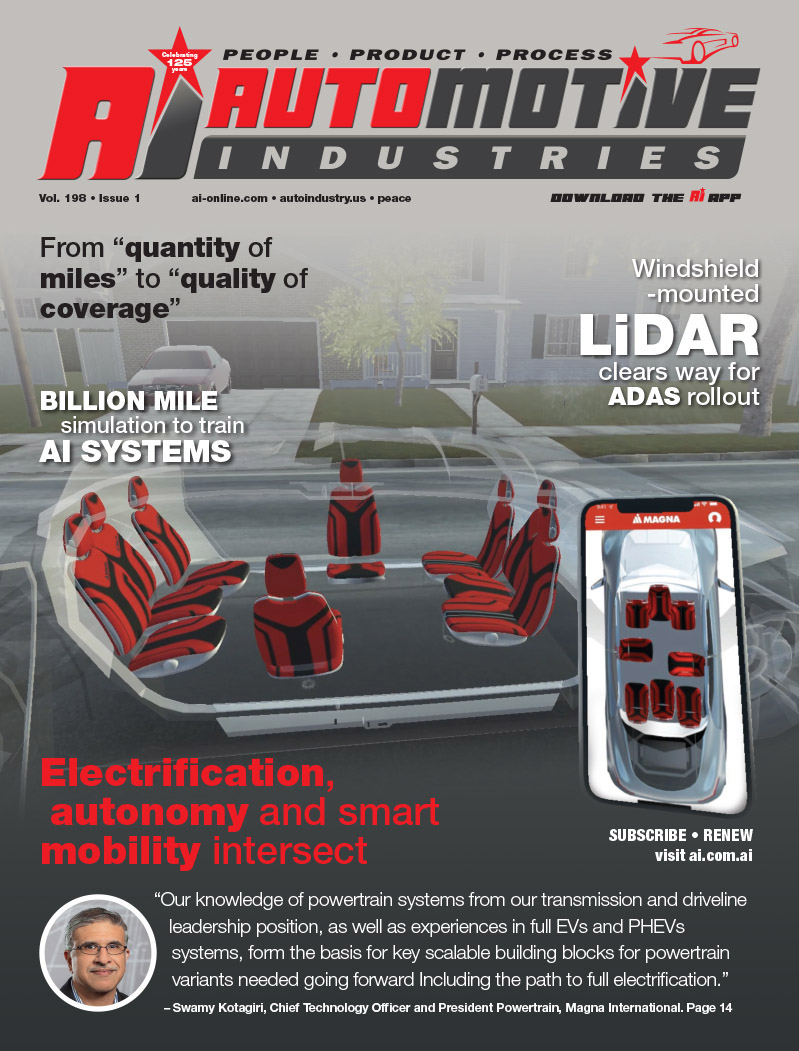
When you’re responsible for moving freight for Target (TGT: NYSE), you better be “on target” with your operations to keep up with one of the highest-volume, demanding distribution channels in the world. The Minneapolis-based retailer, which generates annual revenue greater than $10 billion through its Target, Mervyn’s and Marshall Field’s stores, uses NYK Logistics as one of its leading logistics service providers.
The main hub of NYK Logistics’ Target activity takes place at the NYK Logistics Long Beach, California facility – a mammoth 70-acre yard and transload facility featuring 1,200 parking slots and 250 dock doors. NYK is responsible for managing more than 50,000 inbound ocean freight containers from the Port of Los Angeles/Long Beach and 30,000 outbound trailers every year, coordinating on-time shipments to 22 different Target distribution centers across the United States. As further proof of
the dynamic nature and complexity of this yard, NYK Logistics operates 24/ 7 and processes more than 1,000 gate transactions daily during peak season, checking in and out containers and trailers from 11 different steamship lines and 12-15 domestic carriers.
From Golf Carts and Walkie Talkies to Wireless, Automated Yard Management
Historically, NYK Logistics relied on a “home grown” yard management system, coupled with extensive manual labor to try and manage its ever-changing yard. Yard personnel, armed with clipboards, pads of paper and walkie-talkies – and occasionally borrowing a bicycle or golf cart to reach the outskirts of the spacious facility – would constantly roam the yard, manually entering data and scanning bar codes on containers to try to keep up with the current inventory of the yard. Further exacerbating the problem was the fact that drivers didn’t always drop off their containers or trailers in their assigned parking spaces, so yard personnel often resorted to lengthy searches to find equipment they were trying to manage.
“No matter how many people we threw at the problem – we even used an old pick-up truck to expedite the data collection process – we were always a day late and a dollar short as the saying goes,” says Rick Pople, General Manager of NYK’s Long Beach operations. “And in our case, those days and dollars quickly escalate into thousands of dollars when you consider higher inventory, more labor, and lengthy yard turns.”
Selecting the Right Technology and Yard Solution
With Target’s volume steadily increasing and tapping out its facility expansion (located just seven miles from the Port of Los Angeles/Long Beach, the NYK yard and its surrounding areas are considered prime real estate), NYK Logistics decided in late 2002 to consider emerging technology solutions to manage its yard. “We had no other choice – we exhausted all other options and knew we had to embrace technology,” Pople recalls. “In hindsight, we wished that we had made the move sooner.”
Industry analysts concur. “In order to achieve significant productivity gains in high-velocity, high-volume distribution centers, intermodal facilities and marine terminals, shippers and third-party logistics providers must embrace emerging technologies that automate manual-intensive processes and provide accurate real-time data capture,” says Robert Goodwin, vice president for Gartner.
NYK Logistics did its homework and put together a long “wish list” of what this new, state-of-the-art, yard management solution would offer and deliver – and at the top of the list was real-time location information — critical for a high-velocity yard like NYK. Goals for the system included:
Increasing revenue through new business as a result of better yard throughput
Improving Level of Service (LOS) performance through timely processing of containers
Reducing costs as a result of better gate productivity, improved hostler (tractor) efficiency, and the elimination of manual yard checks
——————————————————————————–
“With WhereNet, we can execute a double transaction in less than twenty minutes. We could have never dreamed of doing that with the old system.”
Rick Pople, general manager, NYK Logistics
——————————————————————————–
The Marriage of Real-Time Location Data and Rules-Based Yard Management Software
To meet these challenges, NYK Logistics conducted a comprehensive search, analyzing dozens of vendors, and ultimately selected WhereNet’s wireless Real-Time Locating System (RTLS) and WhereSoft Yard 4.0 yard management software to better manage its operations and process more shipments with fewer resources. Deployed in less than 75 days, the WhereNet wireless system provides NYK with 100 percent accurate location information for every container, trailer, and hostler tractor within NYK’s yard. Operating as the “command and control center” of the NYK Logistics yard, the WhereNet system is enabling NYK to automate more than 90 percent of its yard operations, which has increased dock door utilization, reduced yard congestion, and increased yard throughput.
“Traditional RFID technology just doesn’t cut it for our operations. It’s not good enough to know that a trailer or container has entered our yard – we must know its exact whereabouts and status at all times. For example, during our peak pre-holiday season, it’s not uncommon that we are required to expedite a container that just arrived at the port, deconsolidate it, and transload its contents onto several different outbound trailers headed for different parts of the country. With WhereNet, we can execute this type of double transaction in less than twenty minutes. We could have never dreamed of doing that with the old system.”
In addition to taking advantage of the latest features of the WhereNet yard management system, NYK Logistics is also benefiting from the complete functionality of the WhereNet wireless infrastructure that combines both location and mobile communication capabilities in a single integrated system. With an array of 35 WhereNet wireless locating access points mounted throughout the yard, NYK Logistics has complete wireless coverage of its entire facility that includes more than 1,200 parking slots and 250 dock doors.
Upon arrival at the gate, every container or trailer gets “tagged” with a small, active radio transmitter called a WhereTag. From this point forward, NYK Logistics personnel have constant connectivity to their yard assets wherever they move about the facility. What’s more, NYK Logistics leverages this same industry standards-based wireless local area network (LAN) for mobile communications, allowing yard workers to use handheld devices and ruggedized Tablet PC devices mounted in the hostler tractors to transmit data via the WhereNet infrastructure.
Sophisticated Yard Management System Saves Time and Money
WhereSoft Yard 4.0 enables NYK Logistics to operate the most efficient deconsolidation/transload/crossdock business in the world, leveraging such features as:
WhereNet Yard Rule Manager – This configurable rules engine controls the movement of trailers and containers to dock doors, assigns parking spots within the yard, and verifies that trailers and containers being checked out are allowed to leave the yard. For example, when the WhereNet location system detects that a door is available, the rules engine automatically scans the yard for trailers that are eligible for that door and generates a trailer move request for the hostler drivers. The rules can be configured to select units based on a combination of criteria including shipment destination, unit status, unit type, unit age, commodity, carrier, hot load and more. NYK uses the rules to ensure that the lowest cost carriers are selected first for particular routes and to minimize detention by processing older containers first. The only human intervention in this process takes place when the hostler driver
receives the request via his wireless tablet PC device, “maps” the location of the requested trailer via his touch screen, and pulls the trailer to the designated door.
Fast Gate Process – Gate check-ins and checkouts are performed using mobile handheld devices and software designed by WhereNet. During the check-in process, a user enters information about the unit and driver, and then attaches a WhereTag to the container or trailer that is about to enter the facility. The system automatically attempts to find a matching Automatic Shipping Notice (ASN) and prints a ticket for the driver with instructions on where to park the unit and which unit (if any) to pick up. The ticket serves as a gate pass for the driver. Driver information is obtained
by swiping the driver’s license on a magnetic card reader integrated with the mobile printer. This data is transmitted via the wireless LAN and captured in the WhereNet database so that NYK Logistics has accurate, automated records of everyone who enters its facility. Based on driver feedback, WhereNet’s fast gate process has resulted in a 50% reduction in time spent on site to complete a double transaction.
The Glass Pipeline – The Power of Shared Data Among NYK Logistics Partners
Not only does NYK Logistics benefit from the WhereNet solution, but so do all of its partners across the logistics network. Whether it’s Target’s procurement and shipping personnel, drayage company dispatchers and drivers, domestic carriers, or even U.S. Customs officials, all of NYK Logistics partners benefit from real-time, actionable information about yard resources.
NYK Logistics also uses the WhereNet yard management solution to auto-email reports several times a day to drayage companies and domestic carriers informing them about empty containers or loaded trailers available for pick up. This real-time information enables drivers to perform round-trips a majority of the time, saving significant time and money. The WhereNet system also triggers alerts based on business rules notifying, for example, NYK equipment controllers if a container sits idle too long or if a loaded trailer is not picked up on time.
This new operational business intelligence allows NYK and its partners to better synchronize resources and activities within this “glass pipeline” by sharing and acting on critical data that is essential for moving products through the supply chain.
“With WhereNet, we essentially know the DNA of every container — what’s in it, when it arrived at the port, its location on our site, and where the contents ultimately need to be shipped,” says Pople. ” But what’s even more exciting is to consider the awesome potential of WhereNet’s technology as more ‘nodes’ are added to the network. When ocean terminals, truck yards, and other distribution centers add local area networks of their own, the shared data will become almost exponentially more powerful. Where we can take this is really almost endless.”
NYK Logistics Return on Investment
NYK realized a complete return on investment in less than one year
Eliminated 100% of costs associated with manual yard searches and data collection
Increased daily throughput of the yard by 38% during Fall 2003 peak season
Improved gate personnel and hostler productivity by 50%
Reduced domestic turn times by four hours and eliminated almost all manual communication related to the process
Reduced time spent by drivers on site to complete a double transaction by 66% – drivers never have to leave their cabs as they receive tickets upon entry instructing them where to drop their container or trailer and bills of lading upon departure for loaded trailers outbound to distribution centers
Reduced yard inventory of trailers and in the process, saved 40-60 parking spots in the yard (depending on the time of year)
Increased quantity of more profitable, round-trip transactions for drivers as the system triggers automatic emails to carriers and drayage partners notifying them when empty containers or loaded trailers are available for pick up
Increased controller productivity as the rules engines makes most of the decisions about resource allocation – the controller only needs to manage exceptions
Achieved higher level of customer service, resulting in increased revenue through new business
Provided access to real-time data by partners across logistics network drives better decisions and resource allocation
More Stories
8 Best Plastic Welding Techniques for Automotive Manufacturing
5 Big Reasons to Choose LED Bulbs for Your Car Headlights
How much does it cost to ship a car on Amtrak Auto Train?