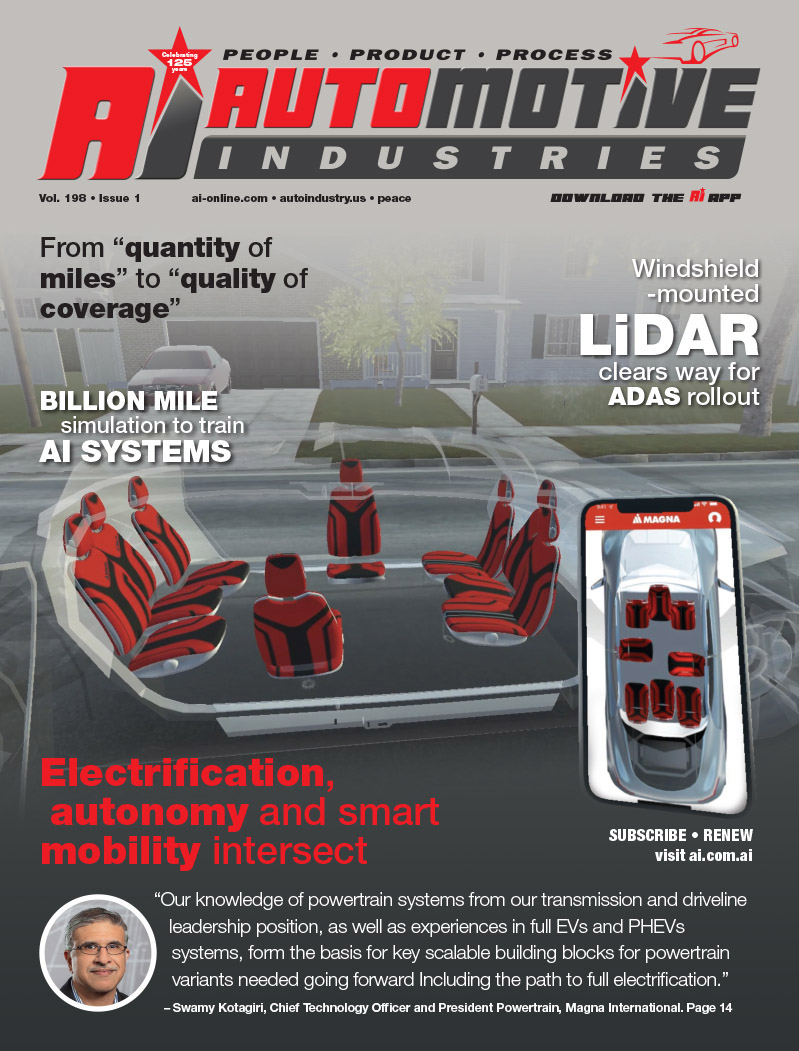
One Billion gallons of ethanol per year by 2012 are projected from a (near $1 billion) new technology facility being constructed in the Sonora desert area of NW Mexico by Mexico-based BioFields. 1000 gal capacity transparent bioreactors have five inputs: Algae, sunlight, CO2, nutrients and seawater. Outputs are: ethanol, oxygen and freshwater.
The things not needed for the process developed by Algenol Biofuels, Inc. Baltimore, MD, are arable land, harvesting, large amounts of fossil fuel, fossil based fertilizer or lots of fresh water. Algenol estimates the energy balance, i.e., the ratio of energy out vs. energy in will be greater than 8:1 which compares with 1.35:1 for corn ethanol.
Algenol explains that energy from the sun through photosynthesis produces simple sugars inside algae cells which, concurrently with enzymes, produce ethanol. Extremely fast growing algae renews the sugar supply.The cost is said to be less than for any other U.S. fuel.
The Sonora facility operator, BioFields, whose initial major customer is reported to be the Mexican oil company, Pemex, is licensed by Algenol to market its ethanol product to anyone. Initial production in 2009 is planned for 100 million gal/yr.
Among interesting data developed by Algenol and made available to Automotive Industries by spokesperson, Evan Smith, is an ethanol production rate already achieved of 6000 gal/acre/yr expected to reach 10,000 gal/acre/yr by the end of 2008 and later to 25,000 gal/acre/yr although 40,000 is said to be the theoretical maximum. Algenol data reports this compares with 370 gal/acre/yr for corn ethanol and 850 gal/acre/yr for sugarcane ethanol. The 6000 gal/acre/yr production rate is based on test operation of a prototype 1000 gal. bioreactor unit
Remarkable advantages of the system are total elimination of any need for eitther food crop or cellulosic raw material and ability to use non arable land where saltwater is reasonably available. Treated manure is among sources of nutrients. The process does not sequester CO2 but rather consumes CO2 which is drawn from the atmosphere. 1.5 million tons of CO2 are consumed per 100 million gallons of ethanol. The process can intake industrial CO2 such as from fossil fired electric utilities to enhance efficiency of the process.
More Stories
Automotive Industries (AI) Newsletter April 2025
Bangkok International Motor Show 2025 – The Talk of Sensuous Automotive
Earn GHG reduction values through MOL Pure Car Carrier “Book and Claim (B&C)” service