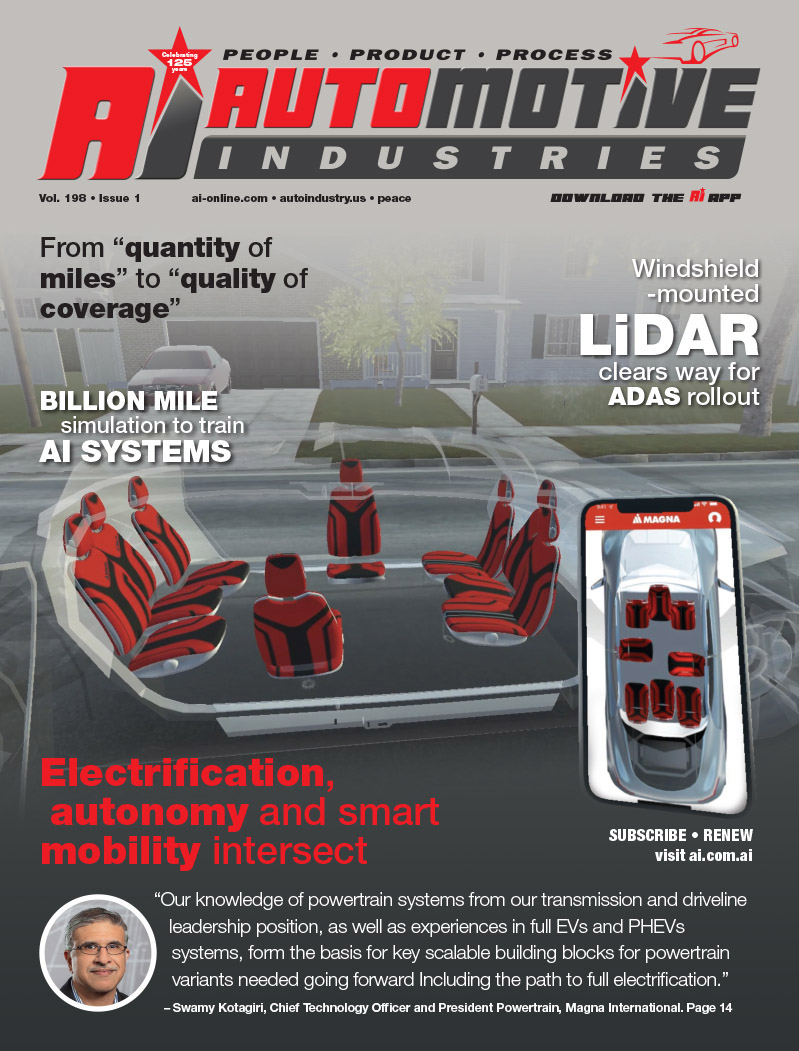
Italian company ITT Motion Technologies has announced that its friction materials development and distribution division is the preferred supplier of front axle brake pads for the 17- and 18-inch high performance braking systems of the new BMW 5 series. The company will produce about 400,000 brake pads per year for this platform for the next six years, both for Original Equipment and Original Equipment Service.
ITT Motion Technologies is the transportation division of the ITT Corporation. With over US$600 million of revenue, it is a lead supplier of brake pads and shock absorbers in the automotive and public transportation sectors. Its global coverage includes facilities and technical centers in Europe, US, Japan, South Korea and China, and an advanced R&D center in Italy – allowing the group to become the international manufacturer’s preferred partner.
Automotive Industries (AI) asked Salvatore Torrisi, president of ITT Motion Technologies, to describe the main characteristics of the new brake pads, and explain the benefits of ITT’s solution to the OEM and the end customer.
Torrisi: Among the main characteristics of the brake pads is that they have reduced vibration and noise levels and a high-level of performance and comfort, both in standard and stress conditions.
AI: At what stage were you involved in the development process?
Torrisi: Immediately after BMW had chosen the brake supplier, ITT began working on the development. The project began in late 2006, which led to the introduction of the latest 7 series in 2009, followed by the new 5 series.
AI: What was the biggest challenge in meeting BMW’s high technical standards and safety criteria?
Torrisi: BMW standards are always highly targeted and precisely defined both for safety as well for comfort. To comply with these stringent requirements in all conditions and in several vehicles requires a constant and continuous focus during the development of the project and the phase of production launch, as well as a high flexibility of the development team. As BMW focuses a lot of attention on vehicle testing, ITT needed to ensure we had the correct development team, with each and every testing engineer and testing driver requiring special training and certification.
AI: What other products are in your product portfolio?
Torrisi: ITT had the first material release more than 10 years ago, starting with the rear axle Duo Servo shoes for the old series 1 and 3. From that moment, thanks to the optimal technical relationship we created and the precise BMW specifications and testing procedures, ITT won many projects, being able to cover BMW’s needs completely. From a presence in the old 5 series to the X5/X6, from the Mini Cooper to the Mini Colorado, from the old 7 Series to the BMW X3 and now with the new Series 1 and 3, ITT is a well recognized BMW development partner. To be able to supply the main safety component for such a prestigious vehicle manufacturer as BMW is a very important achievement for ITT.
AI: What prompted ITT’s decision to open a Research & Development Center in Frankfurt in November 2010, and how will it help strengthen your position in Europe?
Torrisi: In the mid-1980s, ITT decided to have a technical presence in Germany to support our customers, and we opened our first center in Bad Camberg in 1986. The decision to have a new R&D in Frankfurt is mainly due to the need of increasing our space for project management and testing. It is a major investment that confirms our commitment to the automotive industry. It will provide significant additional capability that will fuel our new product development plans and ensure continuous product and technology leadership to benefit all our customers, and will boost our ability to serve and grow in the mass transit business.
AI: What new materials and technology can we expect from ITT in the future?
Torrisi: There are currently many open projects related to electric or hybrid vehicles with the major European car manufacturers focusing on these new applications. ITT Motion Technologies is working with them on these future developments, and the first platforms will arrive on the market within the next two years. ITT Motion Technologies is providing pads to some car manufacturers to develop electric and hybrid vehicles and tests are in an experimental phase.
Moreover, to be competitive and a leader in the worldwide friction material market, we assigned specific resources to develop new formulations to be in line and anticipate any restriction on copper use. The new task for our R&D department is to develop – in conjunction with the customer testing – a deep study of copper’s role in friction materials, the release of 5% copper friction material and also the release of a copper-free materials class.
This activity has become a major topic in Europe, mainly for German car manufactures because of their US exports, and we expect results will be available by the end of 2010.
AI: What other programs are you working on at present?
Torrisi: Being a LowMet friction products leader was not enough for ITT Motion Technologies. That’s why we focused on Non-Asbestos Organic (NAO) products, which are increasingly used in automotive brake pads, especially in the US market. A growing number of automakers, led by the Japanese OEMs, have recognized NAO brake pads are often the best option for smooth, assured, quiet braking under a variety of driving conditions. NAO ceramic brake pads are now the fastest growing segment in the aftermarket pad category.
More Stories
Avery Dennison PSA tapes support rapid evolution of EV batteries
Speira brings research, politics and business case makers together
Automotive Industries (AI) Newsletter April 2025