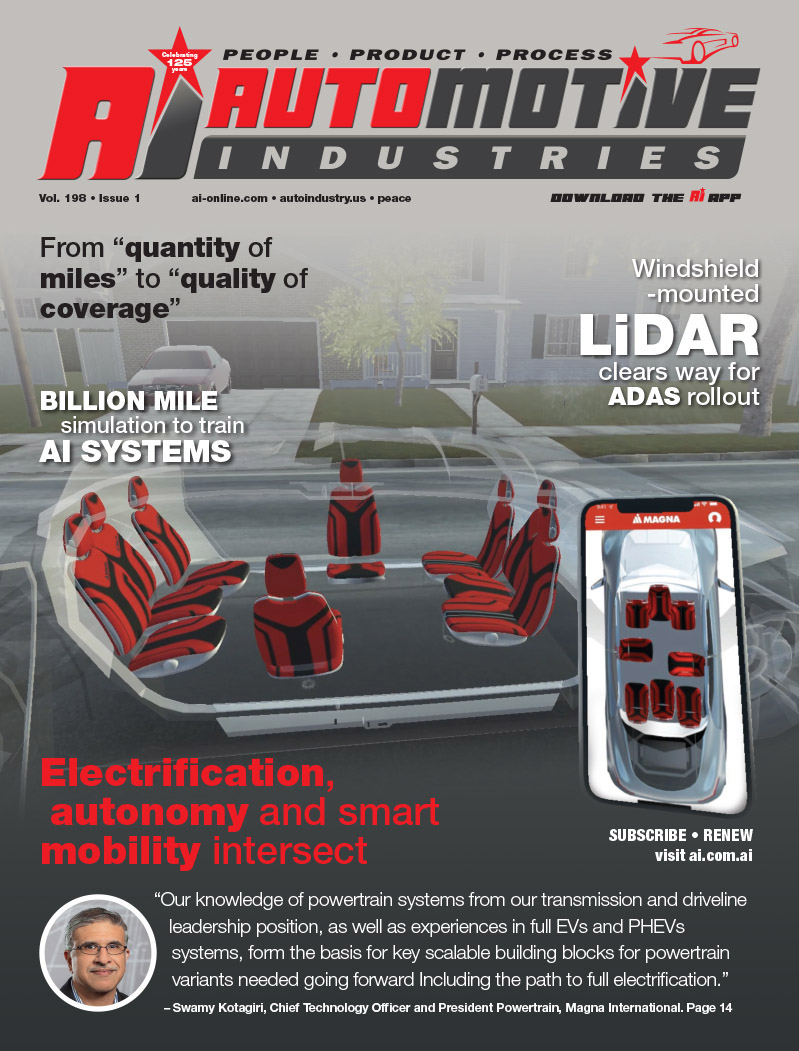
Molding a Ford GT
Bayer’s RRIM molding system creates the front and rear fascias for Ford’s supercar.
Bayer Material Science teamed up with Moon Roof Corporation of America and Advanced Technologies AG to supply front and rear fascias on Ford’s GT.
One of the paramount differences between so-called supercars and regular sport cars are the material choices. The lastest Ford GT program was in line with this ideology and chose Bayer Material Science’s Bayflex 180 RRIM (reinforced reaction injection molding) system to create several of the vehicle’s components. In the case of this particular material it was chosen for its weight, rigidity and heat resistance.
![]() |
The Ford GT supercar sports front and rear fascias, rocker panels, rear bumper cover and spoiler molded by Bayer using a new reinforced reaction injection molding system. |
The inherent heat resistance was also a big consideration given the proximity of the rear fascia to the GT’s engine and exhaust system.
The parts are molded by Moon Roof Corporation of America and have an average thickness of about 3 mm. Moon Roof injects the Bayflex system at low-pressure into a closed, two-piece mold.
Once the parts are molded, they are then sent from Moon Roof along to Advanced Technologies AG. Upon arrival the fascias are post-cured, power-washed, primed and sent along to the paint facility and then to the assembly line.
What’s RIM?
Polyurethane reaction injection molding (RIM) technology was developed in the late 1960s by Bayer AG. Since then, the technology has evolved as more product designers and manufacturers have learned to tap the capabilities of RIM for a growing range of products. The universal physical characteristics of polyurethane RIM parts are high strength and low weight. Like thermoplastic injection molding, RIM is a plasticsforming process that uses molds to form parts.
RIM is not as a specific resin with defined properties, but as a process capable of achieving a broad range of properties.
The polyurethane RIM process uses polyurethanes to produce molded parts. The polyurethanes begin as two liquid components, like “the pellet” form of most thermoplastics. These liquid components — an isocyanate and a polyol — are developed in two-part formulations, often called polyurethane RIM systems. Depending on how the polyurethane RIM system is formulated, the parts molded with it can be a foam or a solid, and they can vary from flexible to rigid. Part density can vary widely, too, with specific gravities ranging from 0.2 to 1.6.
At the heart of the polyurethane RIM process is a chemical reaction between the two liquid components, which are held in separate, temperature-controlled feed tanks equipped with agitators.
From these tanks, the isocyanate and polyol feed through supply lines to metering units that precisely meter both components, at high pressure, to a mixhead device. When injection of the liquids into the mold begins, the valves in the mixhead open. The liquid reactants enter a chamber in the mixhead at pressures between 1,500 and 3,000 psi, and they are intensively mixed by high-velocity impingement.
From the mix chamber, the liquid then flows into the mold at approximately atmospheric pressure. Inside the mold, the liquid undergoes an exothermic chemical reaction, which forms the polyurethane polymer in the mold. Shot and cycle times vary, depending on the part size and the polyurethane system used.
An average mold for an elastomeric part may be filled in one second or less and be ready for demolding in 30-60 seconds. Special extended gel-time polyurethane RIM systems allow the processor enough time to fill very large molds using equipment originally designed for smaller molds.
The RRIM process’ main difference from the RIM process is the addition of minerals to the polyol blend. The front fascia is reinforced with mica while the rear fascia, rocker panels, rear bumper cover and the spoiler are reinforced with wollastonite to enhance the stiffness and strength.
More Stories
8 Best Plastic Welding Techniques for Automotive Manufacturing
5 Big Reasons to Choose LED Bulbs for Your Car Headlights
How much does it cost to ship a car on Amtrak Auto Train?