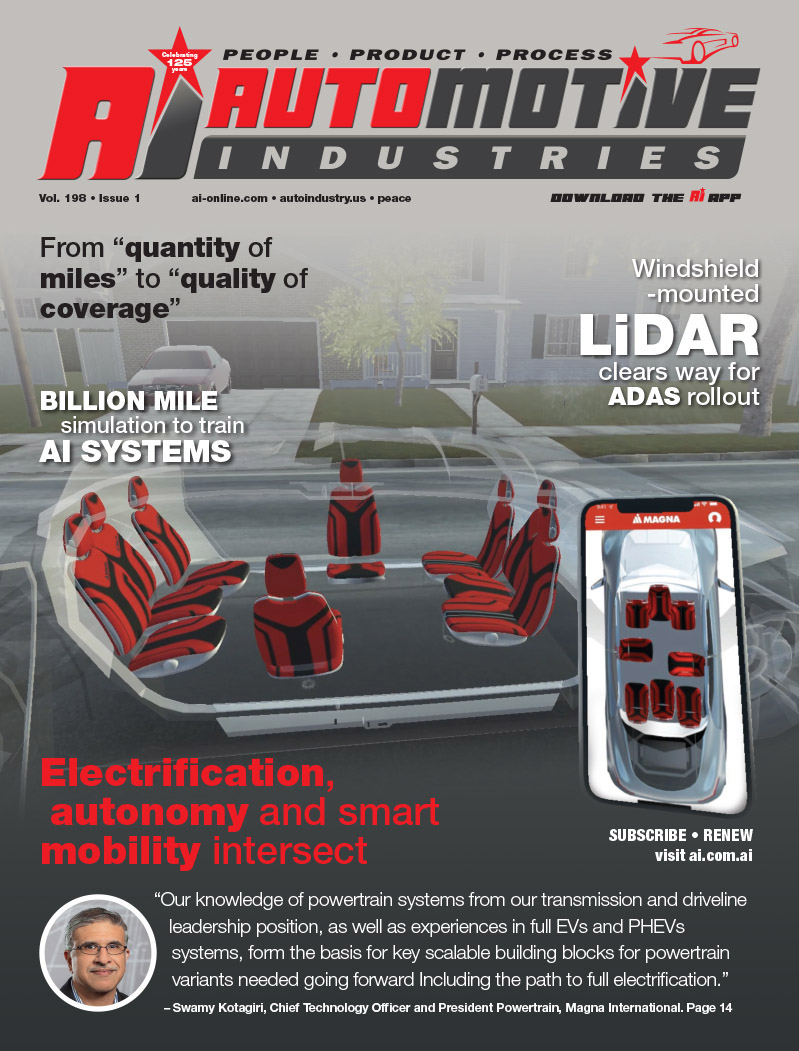
Three vehicles incorporating materials from TenCate are on display at the AutoRAI 2009. These are the KG-1 Concept from KesselsGranger DesignWorks (Eindhoven, NL) at the Dutch Design Lounge, the Go-4 Dakar off-road vehicle from the HAN University (Arnhem, NL), and the DUT racing car from the DUT Racing Team of the Technical University of Delft (NL).
Thanks to its broad technological base – which derives from a combination of textile technology and related chemical processes – TenCate is able to create innovative materials. These new materials are known as ‘smart textiles’ and ‘advanced composites’.
Composite materials from TenCate are frequently used in space and aerospace industries. With these materials TenCate responds to the trend to build lighter planes that use less fuel. The same trend becomes more current in the automotive industries. Next to composite materials, high-tech textiles could play a role in the near future.
The existing activities of TenCate concentrate on the development and production of distinctive materials within its sector ‘Advanced Textiles & Composites’ (protective fabrics, materials for space- and aerospace, and antiballistic protection) and sector ‘Geosynthetics & Grass’ (materials for infra and the environment, and synthetic turf).
Space and aerospace
The origin of composite material lies in the space and aerospace industries. Nowadays the very latest aircraft, such as the Airbus A380, fly with advanced composites. Much of this modern aircraft is made using composite. Carbon or glass fibres are reinforced with synthetic resins and compressed into an extremely strong, lightweight material. TenCate was in at the start of this development and produces materials for aircraft, satellites and spacecraft.
Automobile industry
The overall aim is to make forms of transport ever lighter in weight, without forfeiting safety or the strength of the structure. New materials make new design possible. This often relates to shapes and structures that could never have been achieved with aluminium or steel. The result is a reduction in fuel consumption and noise nuisance. High-tech textiles also offer a solution. The KG-1 Concept from KesselsGranger DesignWorks is based on these. The question is to what extent these developments will be used in the automobile industry and what new concepts lie ahead of us. Three answers can be found below.
KG-1 Concept
In the Dutch Design Lounge the KG-1 Concept is presented by KesselsGranger DesignWorks (Eindhoven, NL). This sports car was designed around the human body. The driver sits in an active position, the passenger in a passive one. The semi-integral body and frame can be produced using carbon fibre-reinforced material. This light, strong composite offers considerable savings in weight and greater mechanical strength. It is already being used in the structural parts of, for instance, ultra-light racing bicycles.
A mesh of protective fibre is stretched around the composite frame like a second skin. It is sufficiently elastic, and yet extremely strong. This high-tech textile can already offer numerous functional characteristics. It can for instance be made water-repellent, dirt-repellent, heat-resistant, fire-retardant, UV-stable and perforation-resistant. It can also be provided with high visibility characteristics or even a luminous capability.
Go-4 Dakar
The Go-4 Dakar off-road vehicle is intended to take part in the toughest rallies in the world, such as Le Dakar in 2010. The HAN University (Arnhem, NL) has been working on this project together with more than 30 partner companies, including TenCate. Knowledge sharing, innovation and the environment are of central importance to the more than 100 students who are participating. The aim is to finish just behind the professional factory teams in the toughest of rallies.
TenCate fabrics based on aramid, glass and carbon fibres have been incorporated in the Go-4 Dakar car. Laminating several layers of fibre with synthetic resin to form a whole has produced an extremely strong and rigid structure. Laminated composite parts are five to eight times stronger than steel and thus also stronger than aluminium. An additional advantage is the low weight of the composite materials, and this saves fuel: the body weighs a mere 70 kilos.
DUT Racing Team
The DUT students Racing Team from the Technical University (Delft, NL) takes part in the international Formula Student every year. The racing cars are assessed on speed, safety, costs, reliability, design and road handling. Each year the DUT racing car is improved and updated as regards design, style, construction procedure and execution. Carbon fibre from TenCate plays a crucial role in this, thanks to its low weight and the ease of machining the material.
Provided they are well designed, the chassis and plating made of carbon fibre can be many times lighter than those made of aluminium or steel. Carbon fibres can be laid parallel to the forces, which allows major savings on material, thus again reducing weight and fuel. At the same time carbon fibres provide enormous freedom of form during design. The DUT Racing Team, for instance, also use carbon fibre to make the fuel tank, air intake, supporting arms, steering wheel and catch cans
More Stories
8 Best Plastic Welding Techniques for Automotive Manufacturing
5 Big Reasons to Choose LED Bulbs for Your Car Headlights
How much does it cost to ship a car on Amtrak Auto Train?