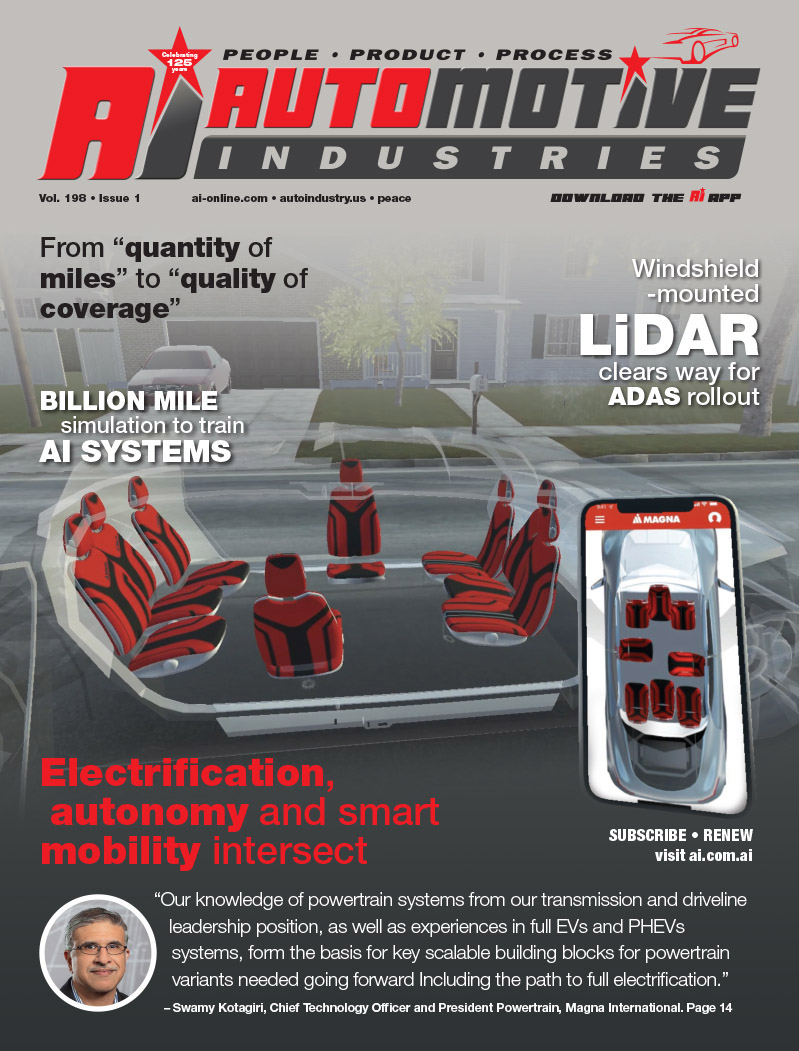
We take tires for granted, perhaps too much, but if we learn that tires are at least part and parcel the cause of an accident in which we are involved, we suddenly become very interested. Both from the designer’s point of view and the one servicing them, it is an excellent idea to be aware of recent developments in tire technology.
In this article the following topics are presented:
– Trends and future possibilities of direct tire-pressure monitoring system (TPMS)
– From direct TPMS to the Intelligent Tire
– Electric vehicles: New requirements for tires’ rolling resistance
– Environmentally-friendly or ‘green’ tires
– Requirements for heavy duty vehicle tires (embedded in other sections)
– Test methods for rolling resistance, rolling noise & wet grip
To appreciate how far and fast tire technology has been advancing, it is worthwhile to see where tires started and what they looked like even a couple of decades ago. Robert William Thompson invented and patented the pneumatic tire in 1846, but it was not until the 1880s that John Boyd Dunlop literally taped these tires to bicycle wheels. So successful was this that he produced these tires in1888 and patented the product in 1889. Numerous developments in clincher rim technology, cotton reinforcing rods, and rim beads occurred, resulting in the first automobile tire in 1895. In 1904 one could get a mountable tire that included cord reinforcement. By 1924, pneumatic tires had completely replaced the solid ones. Synthetic tires came on line in 1937, followed by radial tires in 1946 for Europe, and rayon belted ones, along with tubeless tires the following year. Through the 1960s, other materials were introduced, such as nylon and fiberglass. Regulations started catching up with these advances, with the U.S. Department of Transportation (DOT) mandating an identification code be stamped on each tire. Since then, information has become quite detailed, showing the load range, type of tire, size, conditions under which it can be used, and so forth [1].
The basic tire was about to under much further change, starting in the mid-1990s, especially with respect to how tires were to be monitored.
Trends and future possibilities of direct tire-pressure monitoring system (TPMS)
Current (2011) state of TPMS
To appreciate what the future holds for tire pressure monitoring system (TPMS), we need to review what exists now. When the first TPMS was developed for Porsche in the mid-1980s, it used a sensor-battery-receiver system, where sensors were mounted some place on the tire, such as the valve stem, rim, or tire cavity. The receiver would be inside the car and be connected to appropriate display equipment. Radio frequency (RF) units received the data created by the sensor and sent it to the receiver, which, in turn, activated a warning light. More modern versions have four to five transmitters (including one for the spare), and the receiver can be integrated with other electronic equipment, such as remote keyless entry units or body control devices. Commercial unlicensed ultrahigh frequency (UHF) normally is used (315 or 434 MHz in Europe). Some receivers get information from tires having a unique serial number, thus avoiding confusion in picking up signals from sensors mounted on surrounding tires. When the warning light is on in a steady state, the tire is under-inflated or not inflated at all. There also could be a fault in the TPMS system, itself, if the tire does have the proper pressure.
Several issues arise in sensor design and location design. First, if the sensors are mounted on the outside of the tire in plain view, such as on the valve stem, thieves can steal them, and they also are the source of unevenly distributed weight, making the tire subject to shimmying, vibration, or other malfunction. Mounting the sensor on the back of the valve stem eliminates the theft problem, and the balancing issue can be reduced with miniaturization, such as in the development of micro mechanical systems and systems using nanotechnology. Sensors also can be incorporated into a band mounted on the inside part of the tire’s rim. However, RF can be blocked or negatively affected by carbon or ferrous content in a tire, making specially manufactured tires necessary. This also limits a car owner’s range of choice in tires, making it more expensive, as is the case with most specialty items.
Alternatives to a TPMS have more than one receiver or antenna that enables the vehicle to discern the particular wheel transmitting data. The vehicle’s computer contains in its database information on the tire’s pressure at the time of manufacture, as well as serial number. Other systems have a radio frequency identification tag (RFID) mounted on each tire that uses 125 KHz to send information at any time to the TPMS. When the ignition switch is turned on, each tire is polled sequentially for information so the driver can identify any tire with problems. This sending of data obviates the signal collision problems associated with the “low-end” systems described above. This “high line” system uses a magnetic field detected by the low frequency (LF) antenna in the TPMS. On-board computers will “re-learn” the data for each tire that may be changed or if there is sensor replacement. While the high line systems tend to be more expensive, they save battery power and give information right at car start-up. Still, other systems use the intensity of the UHF signal (such as the sensor being mounted in the front set of tires or the rear set) as a basis for unique tire identification and other data transmission.
Sensors, themselves, transmit data regarding information not about only the tire’s pressure but also its direction, temperature, tire identification number, and speed of rotation, as well. The pressure, temperature, and tire rotation data are sent as analog signals, which then are converted to digital data for processing. As a note on pressure, it is not reported directly (hence, “direct tire pressure sensors” is somewhat of a misnomer), but as a result of a computation from data obtained about the slow or rapid changes in pressure, indicated by the tire’s state, such as rotation and temperature. Measuring the pressure directly has been deemed too complex and possibly risky, such as issues with the instability of sensor locations.
The environment in which the sensor is placed is one of changing temperature, moisture, and contamination levels, thus placing stress on sensors and batteries. Using batteries presents a number of problems associated with the use of these power storage devices, in general. Battery saving devices, such as improved materials and computer chips that can optimize power usage (commonly about 250μW), have improved, but the problem still remains not only of battery life, which is about 7-10 years, but the disposing of the huge number of batteries produced each year for the TPMS systems. Changing a tire can be traumatic to the sensors and the batteries, as well, so the more times the tire is extracted from the rim, the greater chance the apparatus can be damaged, hence necessitating repair or replacement. Coupled with the usual problems resulting from dead batteries, such as the tire going flat “old style” without the driver being warned, are liability issues. If a driver is dependent upon the system and it fails due to battery problems, the resulting damage can be subject to litigation.
The fact that the sensors and receiver can be made as an independent TPMS system make it amenable to being an after market package that can be installed on older vehicles. This is in line with TPMS being mandatory in the United States for all vehicles manufactured from 2007, onward, as specified by 49 CFR Part 571 Federal Motor Vehicle Safety Standards (FMVSS) [2]. Europe is mandating TPMS in car models from 2012-onward. Starting in 1 January 2013, all South Korean passenger cars will have to have a TPMS, but all existing vehicles will have after 30 June 2014 a TPMS, even if it is retro-fitted. Japan is expected to follow Europe.
In contrast to direct pressure measurement, indirect measurement of tire pressure is accomplished through the characteristics of the tire, itself, such as speed of rotation. An under-inflated tire has to rotate faster than a properly inflated one to maintain vehicular speed, as the covered distance is the same. On a newer TPMS, tire under-inflation can be detected by whether and how the tire vibrates. These systems can be integrated with anti-lock braking systems (ABS) and have the distinct advantage of eliminating sensors in the tires. However, the driver must recalibrate the system by pressing a button on the dashboard. If the tire is under-inflated, the TPMS will not give an accurate report. The regulatory status is mixed, it complying with some laws but not others.
Problems are in store for heavy vehicles, as TPMS doesn’t work well. Not only are there standardization issues, but the very length of trailers raises problems with long-distance transmissions. Battery life is compromised because of the complexity in repairing flats. That the truck loads have to be distributed safely requires more tires, thus raising equipment costs. Retreading is done more on tractor-trailers, another factor limiting sensor life. Truckers will allow for slow leaks, thus affecting accurate tire pressure monitoring. Currently a lot of monitoring is done by pass-through truck stations that report issues to truck drivers.
An issue with TPMS is how accurate it will be with “run-flat” tires, those on which a vehicle can be driven at greatly reduced speeds and distances – enough to get to a repair station. How accurate will the TPMS be in reporting the need for tire repair? Research is ongoing with respect to this question.
Future of TPMS
A primary development will be more countries adopting regulations requiring vehicles have a TPMS system as well as strengthening existing ones [3]. Aside from regulations and standardization, work will proceed in making batteries more efficient, as well as extending the power and range of transmitters so as to guarantee accurate data transmission. As to power requirements, batteries have been a stumbling block, but there is nothing to say that solar power cannot be used. Properly mounted cells can supply that power directly or recharge the batteries. RFID tags are found everywhere and are easily mass produced at low cost. Hence, it can be expected that they will supplant sensors whenever possible, or sensor technology will be further miniaturized and integrated with RFIDs.
To date, the primary emphasis on TPMS has been on passenger vehicles. TPMS will work on heavy vehicles, and systems are marketed, but tire changing complexities and conditions reduce sensor life. Increasing the range of receivers because of the length of the trailers involves more efficient power generation and battery life. Research is progressing on how to make TPMS more amenable to heavy vehicles [4]. However, there does not seem to be a rush for truckers to fit TPMS because of the cost versus benefit [5].
The primary focus on new development of TPMS is energy efficiency and self-regulating, or “intelligent” tires, covered in the next section.
From direct TPMS to the Intelligent Tire
We have alluded to intelligent tires above in describing the detection of tire conditions other than pressure. In fact, it is common to find “TPMS” equated with the term “intelligent tires”. TPMS is a special aspect of intelligent tires – pressure monitoring, although people will include other functions, such as tire speed as a part of the system. Hence, there is an overlap in the concepts. Part of the issue is when TPMS started emerging in the latter part of the last century; it was thought that any self-monitoring was regarded as “intelligent”, way far removed from manually measuring pressure.
Strain, temperature, wheel loading, acceleration, friction, tire wear, and shape are other factors that researchers intend to monitor with emerging technology. Ideally, not only every condition of the tire would be known but there would be ways of correcting or adjusting the tire to make it last longer. A tire that grows on its own, however, seems rather out of the question.
Sensors, power sources, data transmission, and data processing and analysis are the core of TPMS development and improvement. For indirect measurement, there are strain gauges, fuzzy logic, and Kalman filters. (Kalman filters predict a value, and estimate its uncertainty. There is a computation of the weighted average of the initial and predicted value and the measured value [6].) Wheel slip, tire load, and velocity, wheel vibration, concentrically of the tire, and rotational speed to measure tire-road friction are measurement aspects that can be integrated with sensors already in the ABS. Measurements of engine torque (such as with an injection time or manifold pressure gauge) can be used to help determine road surface conditions. Global Positioning System (GPS) and velocity data have been proposed as a way of determining vehicle position movement, as in slip angles [7]. Acoustic wave sensors and piezoelectric sensors are other techniques to measure tire conditions. Acoustic waves travel across surfaces and conform to surface features. The wave will change, for example, when it encounters an object on the surface or a hole or dip. Both surface features, as well as mass can be detected. Acoustic energy can be transformed into electrical energy by piezoelectric devices. In nature certain materials, such as quartz and even cartilage in bones develop an electric charge when placed under pressure. Acoustic waves create pressure and can cause piezoelectric material to create electrical energy. Conversely, the electrical energy can cause these substances to produce acoustical energy from the mechanical forcing of air waves. Sound travels across the surface of a tire and other parts of a car body, and this can activate a sensor which, in turn can transmit an appropriate amount of electrical energy to be processed and interpreted by a computer. Embedding sensors within the material, itself, can enable not only tread wear but integrity of tire construction by detecting irregularities such as cracking, holes, and deformities. The more irregular the surface there is, the more irregular the wave will be. Wave irregularity, then, means irregularity in material [8].
Some considerations in future intelligent tire directions
So, we have gone some distance from the original TPMS, basically a way of continuously monitoring tire pressure from inside the vehicle, to measuring tire condition – tread wear, balance, and even condition of construction. It is only a matter of being able to adjust the tire itself or its environment – an adaptive system – to make a system completely “intelligent”. Adaptive systems are a major hallmark of higher intelligence. Of course, we must think about what can be changed to extend tire life. Certainly, changing from summer to winter tires should involve a way that sensors can detect the change and alert the driver accordingly [9]. If a tire is not robust, then we have to ask what can be done so as not to place undue strain on it.
For example, in considering how to create an adaptive system, if an increase in temperature is detected, can a cooling system be activated to alleviate the heat? Claims are being made that tire pressure can be maintained while the vehicle is moving by an on-board tire pump [10]. Balance may be achieved by physically adjusting weights along slides embedded in the tire. Research is progressing in that direction [11]. Changing engine speed via gearing in automatic transmissions or through regulating the engine speed which is more amenable to better tire wear might be in order. Toe-in can be adjusted to extend tire life [12]. One might consider controlling wheel slip via the braking system so as to extend tire life [13]. As a wild speculation, self-sealing technology might be extended so as to have a reservoir of organic material, or the tire, itself (in the manner that a wound heals itself in an animal), grow into a puncture in an already organic tire. Below, we will see that already such tires are on the horizon.
Electric vehicles: New requirements for tires’ rolling resistance
Gasoline-powered vehicles ultimately will have to be replaced by an alternative method of power, as the world’s supply of oil is following Hubbert’s Peak Oil model [14]. A tire’s rolling resistance becomes an even more critical factor, simply because any increased resistance means more of a power drain on the batteries, thus limiting the driving range even further.
Rolling resistance essentially is how the tire and surface on which it rolls interact to slow down the speed of rotation. According to the U.S. Department of Energy (DOE) 5-15% of the fuel consumed by a light duty vehicle is traceable to rolling resistance [15]. Words like “drag” or “friction” are also used to describe the retardation. Numerous factors can affect rolling resistance, (more about which will be said further down in this article):
– road surface condition – affected by road materials, weather, liquids on surface, etc.
– surface of tire – smooth to rough (tread depth and design as major factors)
– tire width – naturally or caused by tire pressure
– tire composition – types of rubber – smooth, hard, degree of flexibility
– speed of rotation
– tire/wheel radius.
Obviously the smoother the surfaces of the road and tire, the less friction there will between the tire and surface, thus lessening friction and increasing the possibility of the tire sliding across the surface. Rough or soft surfaces increase friction, let alone noise for the former. On one hand, the greater the drag, the more fuel or battery power is required by the vehicle. On the other hand, of course, there is an optimum amount of friction to be able to control the vehicle. Terry Gettys, director of the research and development process of the Michelin Group, stated: “Fundamentally, designing tires for electric vehicles is not different than for engined vehicles [16].” While, there are certain factors that need to be taken into account, such as thermal regulation, the general thrust is to reduce the rolling resistance as much as possible [17]. Rolling resistance of tires for electric vehicles is about .055 [18].
As all these factors affect the manageability of a vehicle, it can be expected that there is a plethora of legislation worldwide to address the situation. While automobile manufacturers will install low rolling resistance tires to meet U.S. Corporate Average Fuel Economy (CAFE) standards, there is no requirement concerning what tires a motorist must use to replace them. However, installing tires that have a low rolling resistance, according to the DOE, can save 1.5%-4.5% in fuel consumption [19]. States like California are investigating way that tire manufacturers and distributors need to inform the consumer about ways of selecting tires that offer the best fuel economy. Already, they have a rolling resistance tire regulation, one that went into effect July 2008, and more may be on the way [20]. As of 14 January 2010, heavy trucks and trailers were required to have rolling resistance tires [21]. Europe has followed suit [22], and in November 2012 a rolling resistance rating system will be mandatory [23]. China, seeing the need to conform to these regulations may opt to follow, as it not only deems safety important but wants to be able to sell tires overseas.
Environmentally-friendly or ‘green’ tires
“Green” tires can mean many things, such as making them contribute to fuel efficiency by reducing rolling resistance and being integrated into an intelligent tire system, described above. It also refers to re-cycling them into objects or using them in the construction of other things, such as in buildings and roads. Hence, to be clear, one should specify what they mean by “environmentally friendly” or “green”. Otherwise, these are just catch or marketing phrases designed to placate persons concerned about how tires are contributing to environmental degradation.
It does not take much imagination to think of all the billions of worn out tires about landscapes throughout the world. Since the time they were made in the last decade or so of the 19th century, people have thought of ways of recycling them, ranging from flower pots to fences. We see them used to make buildings, sandals (such as the well known cases of the Vietnamese during mid part of the last century), and other articles of hard rubber. They are ground up, melted and mixed with asphalt to make longer lasting roads that reduce sound. The deleterious part of tires, besides their inherent cluttering of the landscape and inability to biodegrade comes in the form of hazards, such as tire fires, which not only produce great volumes of harmful smoke but can last years. They are ideal breeding grounds for insects, and their filling up landfills is legend. Aside from making objects from old tires, an early way of re-using them was re-treading. This was an acceptable solution for tires used a lower speeds and temperatures, but for heavier vehicles and in hot weather, the adhesive would not be strong enough to hold the new tread. Even with more modern bonding techniques, there are still problems, as one can see simply by driving along any major highway in the world. Nevertheless, whatever re-treading that does occur does recycle some of the tires. Rather than producing tires of the same material that does not meld back into the environment in a “friendly way”, manufacturers have sought to create them from other materials.
Tires were originally made from natural rubber, but just before World War II synthetic rubber was produced by BF Goodrich, and since then, to make tires more durable and with better quality (including reducing rolling resistance), other materials, such as silica have been mixed in. Vegetable processing oil, as well as plant fibers is replacing the petroleum based substances in tire manufacture. By 2013 Sumitomo Tire is hoping to produce a tire with no petroleum content. Yokohama and Michelin are following suit. Goodyear is using micro-organisms to create isoprene, which is chemically the same as the petroleum-based variety, thus eliminating a dependence upon oil. Oregon State University is working on organic substances to replace the silica [24].
Does using a vegetable-based material to get away from petroleum mean that the tires are biodegradable? Apparently, if they are made from potatoes, as students at Warwick University had them made, they are [25]. However, an internet search under “biodegradable tires” will indicate that everybody is not rushing to make tires that are demonstrated to be biodegradable. Yet, the option apparently exists, based on the Warwick project.
Want to learn more about current technologies
and developments in tire technology?
Visit our Download Centre for more articles, whitepapers and interviews:
http://bit.ly/tire-technology
References (Subject is indicated by URL – accessed 11 June 2011)
[1] http://en.wikipedia.org/wiki/File:Tire_code_-_en.svg
[2] http://ecfr.gpoaccess.gov/cgi/t/text/text-idx?c=ecfr&tpl=/ecfrbrowse/Title49/49cfr571_main_02.tpl, http://www.autos.ca/auto-product-reviews/product-review-nvision-tire-pressure-monitoring-system-tpms, http://www.nhtsa.gov/cars/rules/rulings/tpmsfinalrule.6/tpmsfinalrule.6.html
[3] https://docs.google.com/viewer?url=http://ec.europa.eu/enterprise/sectors/automotive/files/safety/presentation_tyres_en.pdf&embedded=true&chrome=true
[4] https://docs.google.com/viewer?url=http://www-nrd.nhtsa.dot.gov/pdf/esv/esv21/09-0551.pdf&embedded=true&chrome=true
[5] http://www.iru.org/cms-filesystem-action?file=en_Resolutions_Technical%20affairs/010_tyre-pressure-monitoring-systems.E.pdf
[6] http://en.wikipedia.org/wiki/Kalman_filter
[7] http://www.mdpi.com/1424-8220/8/12/8123/pdf, p. 8
[8] http://en.wikipedia.org/wiki/Surface_acoustic_wave
[9] http://www.yesanswer.com/intelligent-tire-pressure-sensors-facilitate-changing-a-tire.html
[10] http://www.wheelpumpcorp.com/
[11] http://www.patents.com/us-7814781.html
[12] e.g., http://www.indiamart.com/company/2251343/products.html
[13] http://us.linkedin.com/pub/dir/Bharat/+/us-28-Cleveland%2FAkron,-Ohio-Area, http://ieeexplore.ieee.org/xpl/freeabs_all.jsp?arnumber=1174058 , https://docs.google.com/viewer?url=http://www.itk.ntnu.no/ansatte/Johansen_Tor.Arne/thesisIdarPetersen.pdf&embedded=true&chrome=true
[14] http://en.wikipedia.org/wiki/Hubbert_peak_theory, http://www.hubbertpeak.com/, http://www.princeton.edu/hubbert/the-peak.html
[15] http://www.afdc.energy.gov/afdc/vehicles/fuel_economy_tires_light.html
[16] http://green.autoblog.com/2010/06/02/challenge-bibendum-michelin-execs-explain-why-the-company-cares/
[17] http://evaosd.fartoomuch.info/library/design.htm
[18] https://docs.google.com/viewer?url=http://hal.archives-ouvertes.fr/docs/00/52/75/46/PDF/ICEM_2006_HADDOUN.pdf&embedded=true&chrome=true
[19] http://www.afdc.energy.gov/afdc/vehicles/fuel_economy_tires_light.html
[20] http://www.nrdc.org/media/pressreleases/031002.asp, http://koleso.topof.ru/en/news.php?pID=4689 http://www.energy.ca.gov/transportation/tire_efficiency/index.html , https://docs.google.com/viewer?url=http://www.energy.ca.gov/transportation/tire_efficiency/documents/2009-04-08_workshop/presentations/5%2520-%2520Rating%2520System%2520Presentation%25204-8-09%2520-%2520Tim%2520Robinson.pdf&embedded=true&chrome=true
[21] http://www.truckinginfo.com/news/news-detail.asp?news_id=69025&news_category_id=3
[22] http://www.etrma.org/public/activitiestyreg.asp
[23] http://www.bettertyres.org.uk/why-better-tyres/eu-legislation , http://www.ityre.com/en/main/news/item/8378/
[24] http://www.nytimes.com/2010/06/20/automobiles/20TIRE.html , http://en.wikipedia.org/wiki/Tire#History , http://www.autotropolis.com/driving-smart/worlds-first-green-tires-on-sale-now.html , http://www.technewsdaily.com/green-tires-could-slash-oil-needs-0353/
[25] http://www.treehugger.com/files/2007/03/potato_car_make.php
About IQPC:
IQPC provides tailored conferences, large events, seminars and internal training programmes for managers around the world. Topics include current information on industry trends, technical developments and regulatory rules and guidelines. IQPC’s conferences are market leading events, highly regarded for their opportunity to exchange knowledge and ideas for professionals from various industries.
IQPC has offices in major cities across six continents including: Berlin, Dubai, London, New York, Sao Paulo, Singapore, Johannesburg, Sydney and Toronto. IQPC leverages a global research base of best practices to produce an unrivaled portfolio of problem-solving conferences. Each year IQPC offers approximately 2,000 worldwide conferences, seminars, and related learning programs.
More Stories
Automotive Industries (AI) Newsletter April 2025
Bangkok International Motor Show 2025 – The Talk of Sensuous Automotive
Dürr Systems on paint supply: The foundation for high coating quality