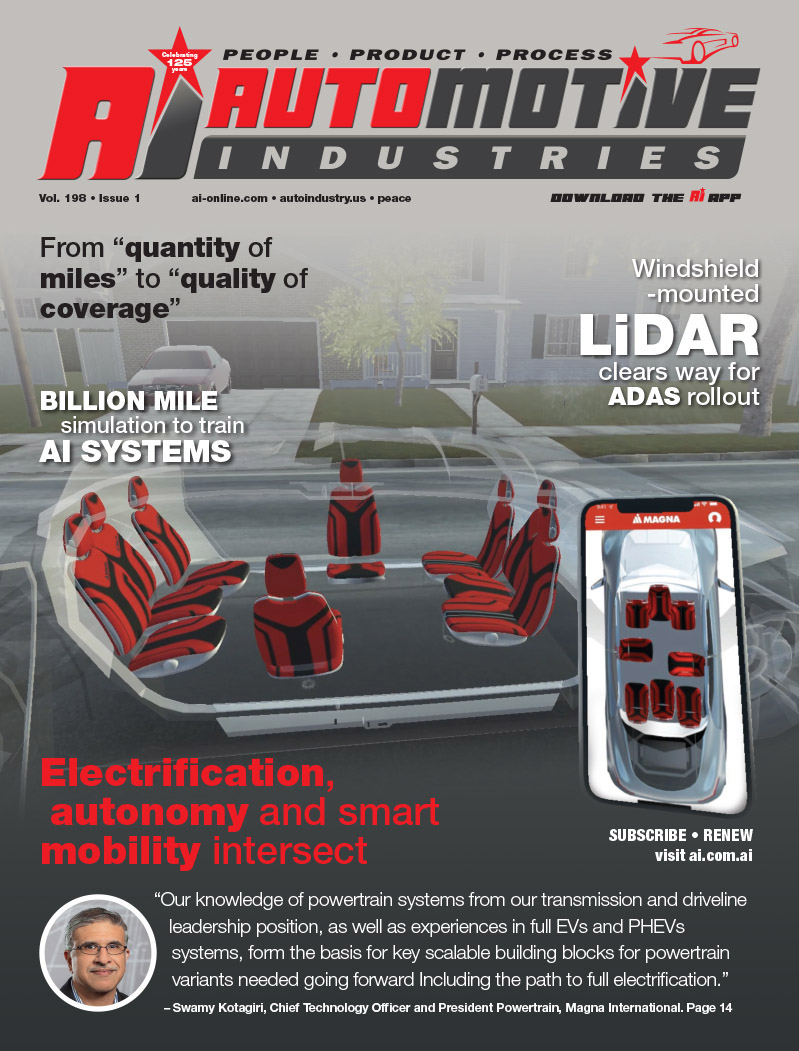
From sophisticated electronic controls to monitor and control the high-power requirements of hybrid and electric vehicles, through systems that integrate the internal combustion engine with the additional propulsion and regenerative braking of a hybrid electric vehicle, to energy-efficient air conditioning including compressors and powertrain cooling, Delphi is playing an important role in reducing fuel consumption around the world.
The company has been focusing its expertise in automotive electronics and problem resolution on the electrification of the powertrain since the early ’90s, when its engineers designed the major electronic and electrical components for General Motors’ EV1, the first modern-day electric vehicle. In the 20 years since, Delphi has grown into a major supplier of power electronics components for electric-drive vehicles. It collaborates widely with customers, suppliers, universities and governments to develop innovative technologies to further increase fuel economy, reduce emissions and help manufacturers make electric and hybrid vehicles affordable.
Delphi operates a number of technical centers, manufacturing sites and customer support facilities in 30 countries worldwide, and says it can offer efficient, robust and high-value electrified powertrain solutions to a diverse customer base.
Automotive Industries asked Gary Cameron, Delphi’s global director of Power Electronics Forward & Advanced Engineering, and recognized as one of the most influential authorities in vehicle electrification, about the company’s ongoing efforts in this area.
Cameron: It’s all about reducing energy consumption through increasing energy efficiency and, as a result, reducing dependence on petroleum fuels. It’s a global effort in both mature and developing markets, and there is an added sense of urgency because the market is looking for an immediate solution. Global energy consumption is expected to nearly double in the next 25 years, and the demands of the developing markets are expected to more than double in that time frame.
AI: We all presume technology will provide the answers. Where does Delphi fit in?
Cameron: Powertrain electrification is critical because improvements in traditional technologies, such as mass reduction, can’t get us to the major advances we need. Electrification technologies such as power split hybrids, 2-mode hybrids, and mild hybrid starter generators are the ones promising to be most cost-effective early on. If the world continues to electrify at a similar rate to the last decade, we would expect about 7% of the global fleet to be electrified in the next 10 years. This is not enough to meet the future fuel economy and emissions standards already being demanded. To get to the U.S. fleet averages of 65 mpg by 2020, the “electrified” portion of the fleet will have to increase to 25-50%. This means we need much greater market penetration starting in the next five years.
AI: That’s an aggressive goal. How can these numbers be realized?
Cameron: Well, we have to get the technology right. We also have to address the cost, and the question of how to charge vehicles without additional strain on an already stressed power grid.
Delphi is applying its expertise in automotive electronics, thermal management, and electrical architecture to develop technologies and robust mass-production processes to address both technology and cost.
AI: What are some of the products and technologies Delphi is developing?
Cameron: In the area of propulsion, Delphi is developing high-efficiency power inverters to control and drive electric motors in these new powertrains, along with high-voltage battery packs and battery controls. We have DC-to-DC converters to control and convert power from the high-voltage battery systems to the 14V load needed by traditional electronic components like lights and entertainment systems. One of our latest products is the on-board battery charger that allows convenient grid “refueling” electronically. We also are developing various methods for connecting the vehicle to the electrical grid more conveniently and cost-effectively.
AI: What makes Delphi’s approach to power electronics unique in the industry?
Cameron: We understand the market trends very clearly, and we have a heritage in
high-volume, high-quality, high-value design and manufacturing that goes back almost 100 years. We also know how to take current products and processes and use them as building blocks for new power electronics. Combine this with our state-of-the-art component and system testing facilities around the world, and you will find that Delphi has the ability to design, validate, and manufacture extremely high quality automotive power electronics.
AI: Tell us why your new inverter technology represents a breakthrough?
Cameron: Our new inverter, designed to power electric motors in hybrid and electric vehicles, is based on a key patent for power semiconductor packaging that provides a superior thermal solution for high-voltage and high-current power switching. Its power silicon packaging cuts size, weight and – importantly – cost while increasing its overall reliability and lifespan. The packaging eliminates wire bonds and enables higher current and power density. When combined with double-side cooling, the design reduces the power semiconductor area and results in an inverter that is 30% smaller than current versions. By providing a variety of options in the design, the power inverter can be customized to meet specific customer requirements.
AI: Tell us about Delphi’s wireless charging system that is currently in development?
Cameron: The Delphi system offers more practical and flexible installation than traditional inductive systems, and doesn’t require precise positioning. It safely and efficiently transfers power over significantly larger distances and can adapt to natural misalignment that can happen during vehicle parking. The system uses the newly developed highly resonant magnetic coupling technology, and the charging source can be embedded in a parking lot or garage pavement, and can work with vehicles over various ground clearances. We are integrating this technology into electric vehicle architectures, and have equipped multiple test vehicles with the system.
AI: How important are partnerships to Delphi?
Cameron: It’s a challenge to fund technology and process development when the market for electrified vehicles is still relatively small. On the other hand, that market isn’t going to grow until we have the technologies and processes that make electrified vehicles more affordable. So we must work collaboratively to resolve the relatively high investment and cost equation during this low-volume start-up phase. To address this challenge, Delphi is partnering with the U.S. Department of Energy (DOE) and other industry and government organizations to share the up-front costs and risks as we work to create more energy-efficient and compact power electronics for high-volume – and lower-cost – production.
AI: Can you tell us more about these initiatives?
Cameron: The largest is a Delphi investment of US$89.3- million, which is being matched by US$89.3-million from the DOE, for development of low-cost, volume manufacturing of power electronics in the United States for electric drive vehicles. We installed a new power electronics manufacturing facility in Kokomo, Indiana, as part of our efforts.
This builds on two earlier programs. One is a cost-sharing grant in which Delphi is leading an industry-government team to develop the next-generation propulsion inverter for hybrid vehicles. The project includes Dow Corning, GeneSIC, General Electric, Argonne National Laboratory, Oak Ridge National Laboratory, and the National Renewable Energy Laboratory. The other is a US$6.7-million cost-sharing award by DOE’s Advanced Research Projects Agency – Energy. Through it, Delphi and its partners (International Rectifier and Oak Ridge National Laboratory) are working to improve efficiencies and reduce the size and cost of power electronics. Delphi also has additional R&D support from the governments of Singapore, Luxembourg and Germany.
AI: You personally were named by Automotive News as one of the 100 most influential people in the world of electric-powered vehicles. Tell us about that.
Cameron: I was really humbled to be recognized with this award, as was my colleague, Randy Sumner, who is director of Global Hybrid & Electric Vehicle Business & Technology Development for Delphi’s Electrical/Electronic Architecture division. We were thrilled to be named along with President Obama and top leaders from many of our customers, including BMW, Daimler, Ford, General Motors, Nissan, Renault, Toyota and Volkswagen. The award program really recognizes how many talented and innovative people it will take to make the electric and hybrid vehicle markets a reality. And Randy and I believe our awards acknowledge the accomplishments of the Delphi team of talented and innovative engineers and technicians who work on power electronics technologies and products. We are supported by a management team that wants us to participate in solving the challenges of fuel efficiency and emissions. I’m excited to continue to work in this area.
More Stories
What to Do After a Motorcycle Accident to Protect Yourself
Injured in a Motorcycle Crash? Talk to an Attorney Now
Danisense launches ‘Online Calibration Portal’ to offer brand agnostic calibration services for current transducers and smoothen the whole process