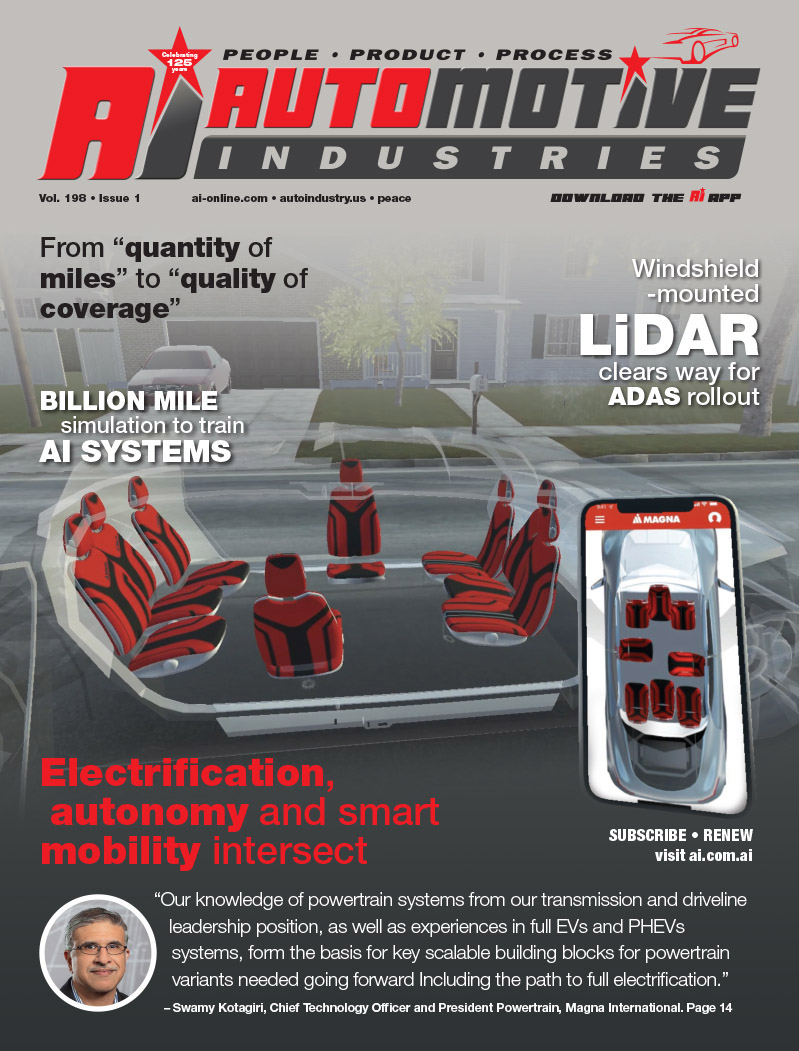
Fuel cell vehicles hit the development trail as they take the next step towards commercialization.
![]() |
Five Honda FCX fuel cell vehicles will become a part of the city of Los Angeles motor pool. The first one was delivered last December. |
Two members of the fleet have already passed another milestone. Honda’s FCX has been certified by the California Air Resources Board and U.S. EPA for daily commercial use and the first of five cars was delivered last December to the city of Los Angeles to be added to the motor pool. The Toyota FCHV received the same honors from Japan’s Ministry of Land, Infrastructure and Transport and was available for lease on December 2, 2002.
“The technology is to the point where it’s performing and in vehicles today that are essentially non-compromising, except from a price and lifetime standpoint,” says Michael Rosenberg, director of corporate relations for Ballard.
Rosenberg says that getting the cars into the hands of customers is a vital step in the development process. It not only builds reliability, but helps the OEMs understand their product including does it meet the customers needs, wants and desires? “Customers tend to do a lot more with their cars than engineers do,” he adds. “And that information comes back into your development program.”
Development will also help reduce cost. Jim Bolch, vice president, operations for UTC fuel cells, says that real world research will help in simplifying the design.
“By definition the products are probably a little more complicated than they need to be,” Bolch adds. “As you understand more about the product you start to integrate multiple parts into a single part.” Development will also allow for technological innovations, like the reduction of membrane thickness and the amount of platinum loading on the membranes.”
But both Ballard’s Rosenberg and UTC’s Bolch agree that cost will come down rapidly as volume goes up.
“Going from dozens to millions,” says Bolch, “does a lot to offset the cost.” He adds that parody right now is with the internal combustion engine.
“The numbers UTC typically hears from the OEMs is somewhere between $35 and $50 a kilowatt,” says Bolch. “That would bring it into parody with an internal combustion engine. That’s the holy grail.”
“We view the ICE as our most significant competitor,” says Rosenberg. “It’s got 100 years of development on it and they’re continuing to improve it. So we have to have a product that meets all of the performance criteria that the ICE does today and we have to do it at a price that’s competitive today.”
Rosenberg adds that if the goal is to eventually replace the ICE, then the industry will need to be able to make 52 million fuel cells a year.
“A lot of fuel cell companies today are still manufacturing their fuel cells in very small volumes and virtually by hand,” Rosenberg says.
![]() |
Ballard is already in the fuel cell manufacturing business. The Nexa power module can generate up to 1,200 watts running on gaseous hydrogen. Fuel cell powered generators can be used indoors without fear of carbon monoxide poisoning. |
Early on graphite bi-polar plates were machined by hand, engraving the pattern with a drill. It took a couple of hours to do each individual plate and there are hundreds in each automotive fuel cell. Ballard is working with Graphtech on a process that presses the plates from a moldable graphite fiber, a process that takes minutes, not hours.
Bolch says that the manufacturing rule-ofthumb with a mature product is about 80 percent material costs, 20 percent labor and overhead.
“If you look at the models of what fuel cell material costs ought to be in volume production,” he adds, “that’s out of line, because most components in a fuel cell are not really very expensive by nature with the exception of precious metal in the membranes and work is being done to reduce the amount of precious metal.”
Both Ballard and UTC see themselves as Tier 1 fuel cell suppliers to the auto industry. UTC has a number of different arrangements with different companies in terms of the amount of manufacturing content they will provide.
“We’ll provide the technology in all cases,” says Bolch. “We’re going to provide different levels of hardware depending on what the business arrangement is.”
Rosenberg has seen a change in the supply chain in the last few years.
“Two, three, four years ago we had to develop everything. We’d go to a pump supplier or a heat exchanger supplier and they’d look at us like we had four heads.”
These same suppliers see the momentum increase around fuel cells and they’re ready to invest in the development of certain parts. “It’s definitely waking people up,” says Rosenberg. “You’re seeing big companies coming to the table, companies like Dupont and 3M looking at being a component supplier for the fuel cell stack.”
If the first production-ready prototypes are just now hitting the world’s streets, how long before volumes get to the point where fuel cell cars become affordable?
“There are different views around the world,” Rosenberg says. “The Japanese government is looking at 50,000 vehicles in 2010, five million by 2020. GM has said one million vehicles by 2010 out in the hands of customers. There are studies that were done last year where they’re talking about an industry consensus of 5,000 vehicles by 2010. So the numbers vary all over the place.
It depends on whose doing the study and who they’re talking to.”
Rosenberg believes that the fuel cell is going to develop similar to the way ABS and air bags did. It will get tested in small fleets to make sure it works, and to make sure it meets customer’s demands and expectations. The next generation will increase in volume.
“By 2003 to 2005 you’ll have hundreds of cars out there in fleets,” Rosenberg says. “In ’05 to ’08 time frame it’s going to be ramping up in the high hundreds of thousands of vehicles, moving into mass commercialization around 2010. That’s the way we see it.”
Infrastructure, Storage and Hybrids, oh my.
Hydrogen is the most abundant element in the universe. It can be extracted from just about anything, reformed from fossil fuels like gasoline, coal or natural gas, electrolyzed from water or made from one of several renewable biomass sources.
In fact, hydrogen is already made in huge quantities by the fuel companies themselves. It is used in the refining of oil into gasoline. And in some processes, like the manufacturing of bleach, hydrogen is a byproduct that is vented out of the plant into the atmosphere. The problem then, is not making the hydrogen, but getting it from the atmosphere into the fuel cell, and making it available to refuel the millions of cars that some manufacturers see traveling our roads a mere seven years from now.
“Most of the gas bottle people see (fuel cells) as opening a whole new market for them,” says Phil Chizek, Ford Motor Co. fuel cell marketing manager, “and they’re willing to get in early.”
The major oil companies weren’t too interested in the technology originally, but now that it’s gaining momentum, they’re faced with losing market share.
BP, ChevronTexaco, ExxonMobil and Shell are all members of the California Fuel Cell Partnership, BP is currently looking at the feasibility of putting in some retail test applications, and Shell has spun off Shell Hydrogen, a separate company whose goal is to help build the hydrogen infrastructure. They have partnered with GM to set up a demonstration fueling station in Washington D.C.
Liquid hydrogen will be trucked in to the station, which will open this October, and will be used to fuel the six Hydrogen3 fuel cell vehicles supplied by GM.
Demonstration ride and drives will be available for legislators policy makers.
“If you’re going to have policy makers weighing in on some important debates over the next year or two years related to the hydrogen economy,” says Lawrence Burns, GM vice president, research & development and planning, “as an engineer, I think you have to kick the tires.”
The focus now is to get government policy makers behind the wheel of this new technology, admits Chizek.
“What the government brings,” he says, “is the facilitation of the refueling infrastructure, codes and standards. The Department of Energy has a $1.7 billion budget to be used to develop a hydrogen infrastructure. They’re also funding technologies for onboard fuel storage freeing up OEM research money for other things.” But Burns has a completely different view of the situation.
“If we could start over,” says Burns, “I would never let them introduce the word infrastructure at all. I would have taken it out.”
Burns is adamant that home refueling may be the way of the future.
“I think what you’re talking more about appliances than pipelines.”
Burns sees the home of the future equipped with a reformer or electrolyzer that would manufacture hydrogen for use in powering the home as well as a source of fuel for the car. “You’d have the water pumped into the electrolyzer, create the hydrogen, compress it and store it in the appliance,” says GM’s Burns. “When your vehicle comes home you’d hook it up and move the hydrogen from the electrolyzer to refuel it.”
Hydrogen on board
“I think that one of the things that are important to note,” says Mike Rosenberg, director of corporate relations for Ballard, “is that the storage equation isn’t as large as some people would make it out to be.”
Rosenberg doesn’t think that liquid hydrogen will be needed to reach the 300 mile range, a target set by the manufacturers. He adds that today’s fuel cell vehicle was’t designed for fuel cells. If vehicles were designed around the cylindrical hydrogen tanks then it could be done with traditional technology.
“I’ve seen designs of a midsize car with tanks running lengthwise down the car — two or three 3,600 PSI storage tanks which are standard industrial storage tanks, nothing exotic about them. And you can still get the range of 300 miles,” Rosenberg says.
Compressed hydrogen is the farthest down the learning curve and best customer option right now. But that doesn’t mean that compressed hydrogen will be the only option. “That’s certainly one of those things that is going to have to be resolved,” says Rosenberg, “and there are a lot of people working on it today. It’s going to depend on what kinds of technologies are decided upon for the vehicles on how expensive those tanks are going to be.”
Right now scientists are working on several ways of storing hydrogen on the vehicle, everything from compressed hydrogen, to liquid hydrogen, to metal hydride storage. Millenium Cell has developed a process called Hydrogen on Demand. A non-flammable solution of 75 percent water, 20 percent sodium borohydride and 5 percent sodium hydroxide is pumped into the vehicle. When a proprietary catalyst is added to the solution, either pure hydrogen or electricity is produced. This technology is being used on the DaimlerChrysler Natrium fuel cell minivan.
Doing the hybrid step
“There is a school of thought that says once hybrids take hold that just pushes fuel calls out further,” says Jim Bolch, vice president of operations for UTC fuel cells. “I for one don’t think that’s true. I think it’s an accelerant to move away from internal combustion vehicles.”
Bolch thinks that hybrids are a stepping stone to fuel cell technology for a couple of reasons. “When you talk about putting a fuel cell into a vehicle, it’s not just the fuel cell itself, it’s the electrical systems, motors, battery, regulation, that kind of stuff. So hybrids give you a chance to work through all of those issues. From the marketing side, it gets the public thinking about electric vehicles no matter what the power source is, and ultimately fuel cells will fit right into that,” Bolch says.
Both Honda and Toyota have had gasoline hybrids available for some time, and the rest of the manufacturers are currently working on the technology. General Motors has an extensive hybrid plan (AI, Feb. 2003, p.43). DaimlerChrysler will sell a civilian version of the Army TACOM hybrid truck called the ‘Contractor Special’ or Ram HEV available in the beginning of 2004 and Ford Motor Co. will offer a commercial version of the Escape hybrid in the second half of 2004.
Ford is using hybrid technology as a base technology for what will come in the future.
“Hybrid vehicles have a lot of crossover technology with fuel cell vehicles,” says Chizek, “and they don’t suffer from the problems caused by the lack of a hydrogen infrastructure. It also helps with economies of scale.”
The Players
![]() DaimlerChrysler NECAR 5 seats four and is powered by a Ballard fuel cell. The entire fuel cell system is built into the sandwiched floor of the extended A-Class. The electric motor puts out 65kW with a top speed of 60 mph. Gaseous hydrogen is stored in a 5,000 PSI tank. NECAR has a cruising range of 90 miles. DaimlerChrysler will be releasing a fleet of 60 vehicles starting this year to customers within the framework of cooperative ventures in Europe, Japan, Singapore and the U.S. | ![]() Ford The Focus FCV hybrid seats five and is powered by a Ballard Mark 902 fuel cell stack working in conjunction with a 300-volt Sanyo battery pack and a brake-by-wire electrohydraulic regenerative braking system, the same technologies found on the Hybrid Escape. The Mark 902 puts out 85 kW and is fed gaseous hydrogen from a 5,000 PSI Dynatech tank. Range is between 160 and 200 miles. Ford currently has two vehicles in the California Fuel Cell Partnership with a goal of five by the end of the year. They will also start low volume production sometime in 2004. | |
![]() General Motors Hydrogen3 is based on the Opel Zafira MPV, a five-seat minivan. It is powered by a Ballard fuel cell stack that puts put 80kW max with about 55kW turning the wheels. The vehicle has a top speed of 100 mph and a range of 250 miles. It runs on either gaseous or liquid hydrogen fed from a Quantum-built 5,000 PSI tank. Quantum and GM have worked together to certify a 10,000 PSI tank for use with the Hydrogen3. The storage system will improve vehicle range by 60 to 70 percent. FedEx Japan will use a Hydrogen3 delivery vehicle this year in and around the Tokyo, Japan area. | ![]() Honda The FCX seats four and is powered by a 78kW Ballard PEFC PEM fuel cell stack with a maximum power output of 80 hp. The vehicle runs on compressed gaseous hydrogen stored in a 5,000 PSI tank. Electricity is stored in a Honda Ultra Capacitor. It has a range of 170 miles. The FCX has been certified for commercial use by CARB and the EPA. The first of five lease vehicles was delivered to the city of Los Angeles in December. Honda plans to lease about 30 fuel cell cars in California and Japan during the next two to three years. | |
![]() Hyundai The Santa Fe FCEV is powered by a Series 300 UTCFC ambient pressure fuel cell. The series 300 puts out 75kW. A 5,000 PSI tanks pumps compressed gaseous hydrogen yielding a range of 100 miles at a top speed of 77 mph. According to Jim Bolch of UTC, Hyundai was so adament about the FCEV looking like the gasoline version that they made the UTC engineers hide their lap top com port inside the ashtray between the back and front seat console. | ![]() Nissan The Nissan Xterra FCV is powered by a 75kW Ballard Mk901 Fuel Cell stack that drives the rear wheels through a Neodymium Magnet Synchronous Motor. The stack is fed compressed gaseous hydrogen from a 5,000 PSI tank yielding a range of 125 miles with a top speed of 75+ mph. A Lithium-Ion battery is used for energy storage. Carlos Ghosn has said that Nissan will begin expanding their research into fleet tests in 2003, but doesn’t anticipate FCVs becoming commonplace in the market until a fueling infrastructure is in place and they become economically viable. | |
![]() Toyota Based on the FCHV-4 prototype, the FCHV seats five. Power comes from a Toyota-developed PEFC fuel cell stack that puts out 90kW. The vehicle has a range of 186 miles at top speed of 96 mph. The vehicle uses gaseous hydrogen stored in a 5,000 PSI tank. The FCHV is the first fuel cell vehicle to be certified by Japan’s Ministry of Land, Infrastructure and Transport. Toyota offered the vehicle for lease on December 2, 2002 at a cost of about $10,000 a month. | ![]() Volkswagen The Bora HY.POWER is powered by a 74kW fuel cell developed by the Paul Scherrer Institute in Switzerland. Fed by compressed gaseous hydrogen from a 5,000 PSI tank, the HY.POWER goes from 0 to 60 in 12 seconds. HY.POWER uses Supercaps, in place of batteries, that can accumulate up to 360 watt hours of energy through regenerative braking. Volkswagen recently did a durability test drive through the 6,578-foot high Simplon pass in Switzerland and Italy. | |
More Stories
RAM Trucks in Toronto: Why CarHub North York Chrysler Delivers the Best Experience
Buying Car Insurance in Toronto? Don’t Make These Rookie Mistakes
Extend Your Range, Maximize Your Storage with FRDM’s 45 Gallon Combo