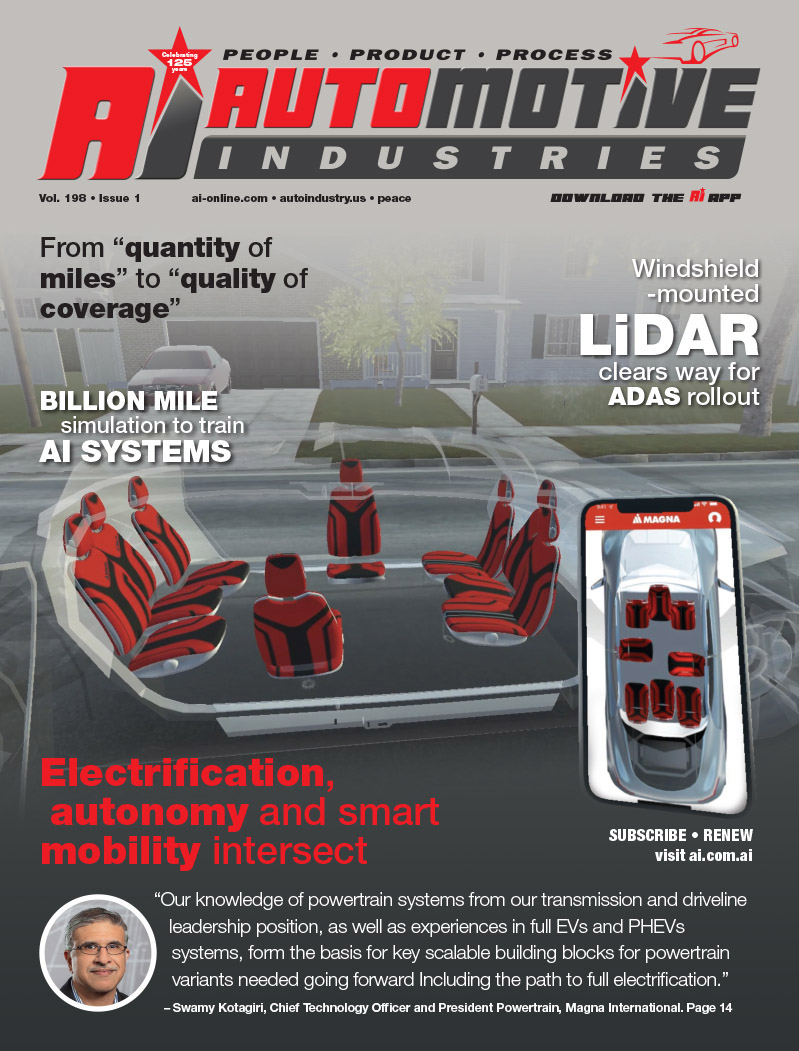
It jumped right out at us last summer as we reviewed design details on the new 6.0L Ford PowerStroke Diesel, designed and manufactured for Ford by International Truck & Engine Corporation. Hey, here is a medium duty diesel with a 500,000 mile warranty and it uses forged powder metal (PM) connecting rods. It is the first diesel in North America to employ that material for that application, but probably not the last.
A number of passenger car diesel engines in Europe also use forged PM connecting rods currently, but this is a pretty robust engine and is rated 325 hp. with 560 lbs.-ft. of torque in Ford full size pickups and vans, many for commercial vocations. But this engine is certainly produced in automotive type quantities of up to 1,060 per day from International’s Indianapolis engine factory. Certainly worth investigating, how did this program come together? The yellow brick road led us to George Lanni, director, business development and engineering and Steven Letourneau, design engineering manager at Metaldyne’s engineering center in Pontiac, Michigan. George Lanni and Steven Letourneau are with the Sintered Components group of Metaldyne.
“Discussions with International began back in 1998,” related Lanni “and we only had about eight weeks to supply prototypes. They were investigating forged PM as more a due diligence effort and I think the preliminary performance results and the prospects for total cost savings initially surprised them.
From that point, International became highly motivated about the idea and definitely convinced it was the way to go. And then, of course, they also had to sell the idea to Ford.”
As the program developed, Metaldyne ended up replacing the forged connecting rods on the 7.3L V-8, predecessor to the new 6.0L V-8. A fully developed 4.5L V-6 version of the new PowerStroke engine is currently in production limbo, but that too would employ the forged PM connecting rod if and when International and Ford eventually go through What about the mechanical properties of the forged PM rod versus the forged steel rod? “The mechanicals are equal to or better. They are in fact what you want them to be. Name it and we can match nearly any requirements. Powder metal parts always have to overcome this myth of inferiority, but it just isn’t there,” Letourneau explains.
“In this application the ultimate tensile strength is basically identical and the yield strength superior by some margin. Through the addition of manganese sulfide to the powder, we have a material that is machinable and still has a hardness in the Rockwell (C) 26-27 range. The microstructure is isotropic and lends itself to excellent machinability. We project that tool life is improved by a factor of four to one.
“But because this is a near net shape technology, there isn’t that much machining anyway, the capital cost for machining equipment is less, and the dimensional control is much improved. We’ve completely eliminated weight pads on both ends of the rods and thus the subsequent machining and processing required to meet weight specifications.” The connecting rod for the 7.3L engine is quite different from that for the 6.0L diesel.
The 7.3 rod has a straight split on the big end while the 6.0L rod features an angle split. On the small end, the 6.0L rod features teepee geometry to provide a larger bearings surface to absorb the high pressures on the underside of the piston pin. The material is a cuprous iron alloy with high carbon and a manganese with that program. sulfide additive. Copper content is approximately 3 percent. Particularly interesting, on the large end of the straight split rod the lower end cap fastens to the main part of the rod with through holes that can be drilled conventionally. But with the angle split rods on the 6.0L, the lower bearing cap mates to the main part of the con rod with cap screws secured in blind threaded holes.
“Blind holes are problematic. They trap chips and can lead to cross threading in reassembling the rod.” notes Letourneau.
With the forged PM rod we get around this completely by thread rolling instead of tapping. I think this might be a first and we were not sure we could actually do it effectively. But in any event, it works extremely well.”
Elimination of weight pad stock from both the large and small end of the connecting rod is terribly large advantage. Typically, you need to through a process of weighing the pin end mass and the crank end mass and then balance machining each end. Hardly an exact science, conn rods could instead be classified into several weight categories and then matched up assembly into a specific engine. Dealers and distributors may need various weight classes in inventory for aftermarket needs.
All this tedium is eliminated with forged PM connecting rods because the weight tolerance is so close. The 6.0L connecting rod has a target weight of 1,450 g. In forged steel, the weight variation of the pin mass would be +/- 20 g versus +/- 4 g for the forged PM rod. On the crank end, forged steel would have a variation or +/- 70 g. versus +/- 5 g for the forged PM.
Forged PM parts are growing in application they can often combine the mechanical properties of steel forgings with the costs of near net shape fabrication.
Basically, you start with a raw powder metal blend with a machining enhancer MnS); then compact it to near net shape in the green state; sinter it in a rotary hearth furnace in a nitrogen enriched neutral environment; forge it in a single stroke to full density; and then finish machine. No subsequent heat treating or stress relieving is required. The 6.0L PowerStroke is truly an interesting application, but PM rods in the overall have grown by leaps and bounds since the mid 1980s. Metaldyne has produced some 230 million of them since 1986 (more than half of that in the past five years) and claims to have market penetration just over 40 percent. OEM automakers have typically retained in house machining of critical engine components such as blocks, heads, crankshafts, camshafts and connecting rods and pistons.
The only tethers in some cases are the inertia of tradition and stranded assets.
Component suppliers are bent on taking OEMs out of some of those businesses.
Connecting rods are at the top of that list. With a potential order of magnitude improvement in costs on the line by shifting from forged steel to PM , connecting rods may move entirely outside OEM walls. Or, as is the case of the 6.0L PowerStroke, what remains inside will be minimized for machining content and maximized for efficiency.
Mechanical Properties | |||
Forged Steel | Powder Forged | ||
Yield Strength | Rp0.2 | 550 N/mm2 | 670 N/mm2 |
Tensile Strength | Rm | 1050 N/mm2 | 1030 N/mm2 |
Elongation | A5 | 10% | 11% |
Density | p | 7.82 g/cm3 min. | 7.80 g/cm3 min. |
Modulus of Elasticity | E | 206 GPa | 207 GPa |
Poisson’s Ratio | 0.294 | 0.294 | |
Core Hardness | 28-34 Rc | 21-31 Rc |
More Stories
Buying Car Insurance in Toronto? Don’t Make These Rookie Mistakes
Extend Your Range, Maximize Your Storage with FRDM’s 45 Gallon Combo
How to Install a Ford Bumper Yourself (Step-by-Step Guide)