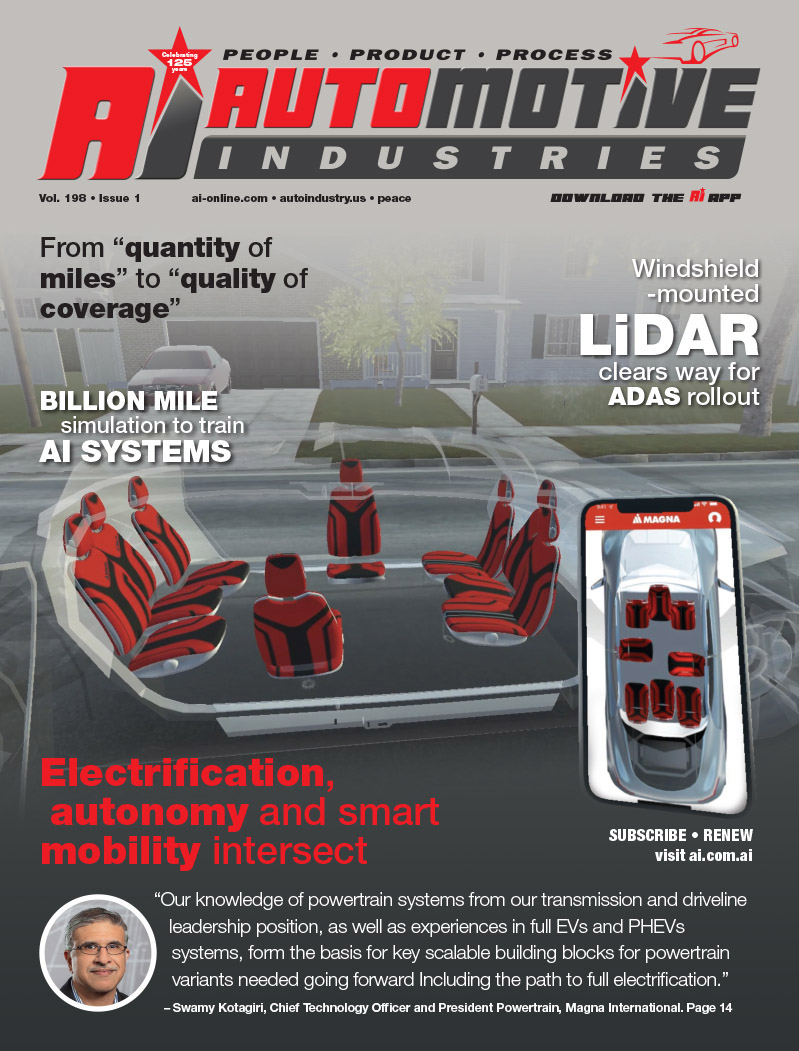
Ford F-150
![]() |
Ford’s new entry-level Regular cab now features small rear hinged doors that open to cargo space behind the seats. |
![]() |
The upscale Lariat interior is one of five interior variations offered by Ford. |
![]() |
Johnson Controls developed the unique roof-rail storage system that features snap-in, snap-out storage bins. |
Two years ago, Frank Davis assumed the chief program engineer’s role for the new F- 150 after guiding the heavy-duty F-250 line to solid success. By then the top priorities — power, prestige, and package — were clearly identified. A 180-degree twist on the alliteration inspired the Davis team’s battle cry: bigger, badder, better.
Exterior designers contributed a more aggressive hood and front fender line, wheel tracks widened by over an inch and reduced tumblehome in the cab’s roofline. In the side view, the big-bad truck look was achieved by borrowing the F-250’s notched beltline and by lifting the bed sides 2.3-inches.
Stretching the wheelbase by a nominal six inches not only yielded a bolder-looking truck, it also set the stage for major packaging improvements. Step one was sending the two-door standard cab the way of the buggy whip. The new entry-level Regular cab has been upgraded to an extended design containing a single row of seats and some handy storage space accessible through small rear-hinged doors. What Ford calls a SuperCab provides access to a compact back seat through rear-hinged doors. The SuperCrew flagship features a roomier rear seat and full-sized front-hinged rear doors. Thanks to the wheelbase stretch, SuperCab rear passengers gain half an inch of leg room while SuperCrew occupants enjoy an additional 2.2 inches of lower-limb space.
The F-150’s Dana-supplied ladder frame represents engineering advancements on multiple fronts. Side rails are fully boxed and the second of four sections that comprise each rail is hydroformed. Three out of the six cross-members are welded to both inner and outer walls of the side rails. The body is supported by large shear-type rubber mounts and hydro mounts help isolate powertrain noise and vibration from the passenger cabin. Ford claims that the new frame is an incredible nine times stiffer in torsion and 50 percent stiffer in bending than the outgoing F-150 design.
Key lessons learned, engineering the newfor- 2003 Ford Expedition eased the task of creating the new F-150. The front portion of the chassis is nearly identical. In total, Davis’s team successfully carried over nearly a third of the new pickup’s ingredients.
Packaging the front springs concentrically with their shock absorbers facilitated use of coil springs for both 4×2 and 4×4 drivelines. Retiring the torsion bars used previously in 4×4 applications was the key to adding recession (controlled rearward wheel movement over bumps) in the front suspension. As a weight savings measure, lower control arm s are now aluminum castings.
Positioning the shock absorbers closer to the wheels, both front and rear, yields more effective damping characteristics and superior body-roll control. The rear semi-elliptic-leaf rear springs were widened by half an inch (from 2.5 to 3.0-inches) as a means of enhancing stability while towing or hauling hefty loads.

To improve that vital communications link, Ford engineers shifted from a recirculating ball to a rack-and-pinion steering gear, achieving lower friction, higher system stiffness, significantly improved precision and a tighter turn circle.
Larger four-wheel disc brakes with ABS and electronic force distribution are standard. Acknowledging the importance of power in the hearts and minds of pickup truck customers, Davis shelved V-6 engines for the time being, added electronic throttle control to the faithful 4.6L “modular” V-8, and focused major attention on thrusting the optional 5.4L V-8 over the 300-horsepower hurdle.
An ingenious 3-valve cylinder head with a special long-reach, small-diameter spark plug centered in the combustion chamber between two intake and one exhaust valves is at the heart of this fortified V-8. Another interesting trick is a variable timing mechanism on the single overhead camshaft that advances and retards both intake and exhaust events together (through a range of 50 crankshaft degrees) in response to powertrain control computer commands. In concert, the advanced combustion chamber and variable valve timing developments achieve more power, lower emissions, respectable fuel efficiency and a smooth idle.
Cam covers are cast magnesium for weight savings. A drive-by-wire throttle arrangement simplifies both the enginetransmission calibration task and cruise-control hardware.
The 5.4L Triton’s intake manifold is a fivepiece molded-plastic design integrating runners, plenum, throttle body and air filter in one grand assembly. Solenoid-activated butterflies located in half of the intake runners close on demand to increase air-flow velocity and mixture motion inside the combustion chambers at low engine speeds.
Ford claims its new 24-valve V-8 is lighter, more compact and less costly to manufacture than the 16-valve 5.4L Triton it replaces. It’s also notably quieter thanks to a sandwichconstruction (two layers of steel around a viscoelastic core) oil pan and a thick layer of sound-deadening material positioned in the valley between cylinder banks. While Ford recently launched a 5-speed automatic for its heavy-duty F-series pickups and the Excursion SUV, that transmission missed the F-150 boat, at least for now. Instead, the 4-speed 4R70E was reinforced and recoded 4R75E to handle expected torque. New shift controls enhance the 4R70E’s performance when mated to the base 4.6L V-8. The two-speed Borg-Warner 908 transfer case supplied with 4×4 models features shift-on-the-fly engagement and a choice between lever and push-button shifting.
The new cabs are 75 percent stiffer in construction to ward off squeaks and rattles.
There are five trim levels initially and more to come. The XL is the bench seat, cloth or vinyl upholstery entry-level edition. The STX adds sporty style while maintaining an attractive price. The XLT, expected to account for 40- percent of total sales, offers a wide range of cab, seating and accessory options. The FX4 is built only with four-wheel drive with a choice of three cab styles and two box lengths. (One new offering is a short box with the longer SuperCab to keep overall length at a garageable 218 inches). Leather and wood trim are standard in the flagship Lariat model. Lightning, Harley-Davidson edition and other up-spiffs will roll out after the F- 150’s June introduction.
Among the new interior convenience features are roof-mounted rails to support storage bins and a DVD entertainment system. Power windows are built into SuperCab rear doors for the first time.
Instead of packing the interior with air bags (Nissan’s ploy), Ford stayed with only two bags to protect front-seat occupants during a frontal collision. They are, however, intelligent enough to deploy at two levels of intensity according to accident severity. A passenger-side sensor measures the weight of the occupant and disables activation when no or small passengers are present. Pyrotechnic tensioners pull front seat lap and shoulder belts tight immediately after a frontal impact.
Lowering the bumpers three inches and the frame one inch was aimed at reducing the F150’s aggressivity in collisions with lighter vehicles. In light of the fact that curb weight is up by more than 500 pounds — base curb weights range between 4,768 and 5,590 pounds — that’s an excellent idea. One third of the weight gain is attributable to structural reinforcements added to insure favorable results in an offset frontal collision. The other two-thirds were invested in NVH reductions and convenience-equipment additions.
Lifting the sides of the cargo box 2.3 inches increases its internal volume by a significant 12 percent. Naturally, that necessitates a taller tailgate which caused concerns about higher opening and closing efforts. Chief Body Engineer Steve Bruford and his pilot plant technicians devised a clever solution in the form of a torsion bar integrated into the left-side pivot point. Davis loved the counter-balanced tailgate the first time he experienced it and he quickly approved it for production.
While Ford’s Ontario, Canada, truck plant soldiers on with the current F-150 to keep dealers from running out of this critical product, three U.S. plants will gradually come on stream with the new model. Norfolk, Va., is already shipping units. The Kansas City truck plant follows suit in a few months. Ford’s new Rouge facility in Dearborn, Mich., will commence F-150 production in 2004.
What the F-150 lacks to the Nissan Titan in technical sophistication, it more than makes up in shear breadth of offering. Even though they’re arch competitors, the two newbies together lift the pickup truck bar to record heights. The considerable engineering effort invested in their well being won’t be missed by customers. Or, for that matter, by GM and Chrysler engineers striving to top the new standards of pickup truck excellence.
More Stories
Buying Car Insurance in Toronto? Don’t Make These Rookie Mistakes
Extend Your Range, Maximize Your Storage with FRDM’s 45 Gallon Combo
How to Install a Ford Bumper Yourself (Step-by-Step Guide)