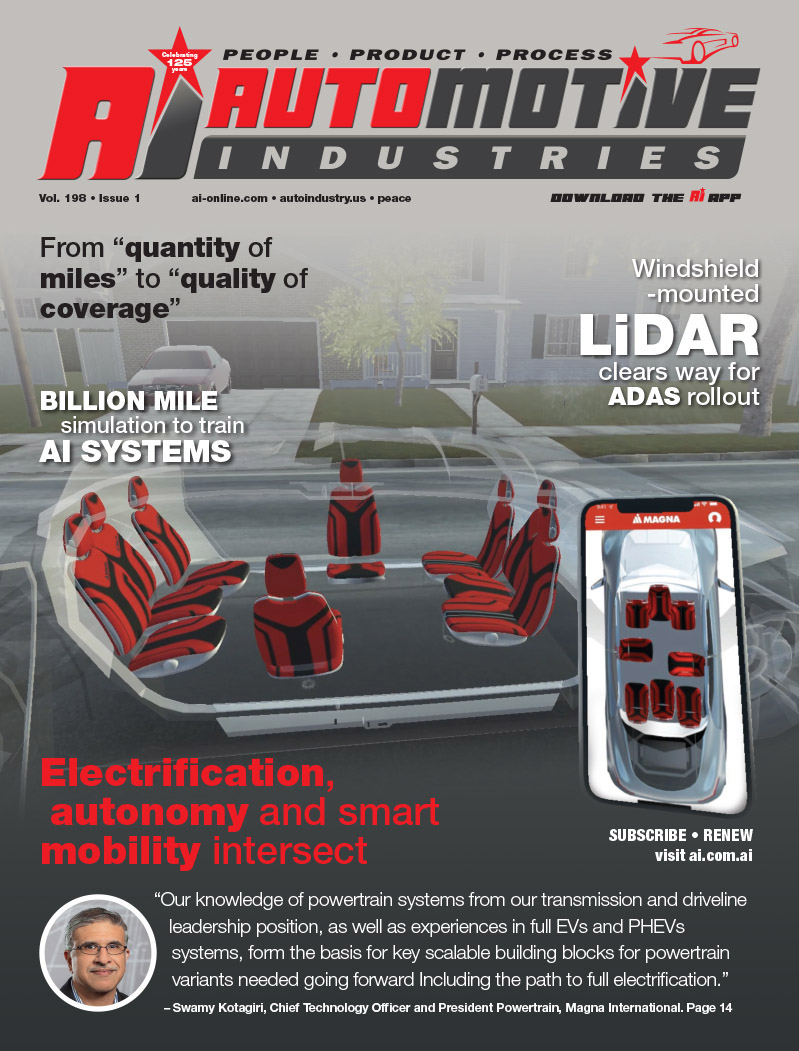
Dr. Taylan Altan is a professor at Ohio State University and director of the Engineering Research Center for Net Shape Manufacturing. He has spent over 30 years in metal forming and has a degree from the Technical University in Hannover, Germany, as well as a master’s degree in Mechanical Engineering from UC Berkeley and a PhD in ME, also from UC Berkley.
He was originally exposed to tube hydroforming at a conference in Germany. A grant he garnered helped to start the Engineering Research Center. The center then became involved with developing a consortium for tube hydroforming and has now begun to look more seriously at sheet hydroforming.
Dr. Altan took some time out of his schedule to talk to Automotive Industries about the many facets of sheet hydroforming coming to industry and also discussed some of the companies involved with it currently.
Q: When did you shift your focus from tube hydroforming to sheet hydroforming?
A: I am still in the process. Sheet hydroforming is nothing new — it’s just a question of whether it can be brought to industry. People had been asking us about sheet hyrdoforming based on the fact we’d been doing work with tube hydroforming so it was logical to approach us about sheet as well. Mostly we did simulations for people and in our own laboratory and working with some of our own tooling. Rather than water, we chose a more viscous material because it was easier to get a seal. In most cases sheet hydroforming wasn’t cost effective but there are some companies using it. It’s important to look at what’s going on around the world.
Q: Are you familiar with the Amino Corp?
A: Yes, they are making parts in Japan for Toyota. Also, I think in Canada now they are building a plant, they will make parts for very low volume production for General Motors. They are a small family owned company who is very innovative. Their niche in Japan had largely to do with aftermarket parts. They are to my knowledge, at least, until very recently, the only company that will make parts on a production basis. Small volume is still production, after all. A lot of others looked and thought perhaps this (sheet hydroforming) would be useful for prototyping.
Q: What do you see as a big advantage to sheet hydroforming?
A: The advantage is you need only one die. The other is just heated rubber or fluid. Therefore if you have a low volume of production this process makes sense.
Q: Do you see cycle time as the big problem in bringing sheet hydroforming to industry more readily?
A: Cycle time is a big problem because cycle time in these presses is one of the reasons why it makes sense to only use this process for low volume production. The average is one part per minute. Hard dies offer faster cycle times. You don’t want to attempt high volume with this process. I understand that the top of the Maybach is produced by Schuler this way. So that’s another production application but as you can see they are limited production applications.
Q: Are there any other inherent drawbacks to the process?
A: Another issue is this: in order to form the part properly you have a punch, a solid punch and on the other side you have liquid. Now you need to keep the liquid under pressure so that liquid pushed the metal against the punch. At the same time, you want to draw the material over the die holder. So the problem is you want to have the sheet draw in because the more you draw in, the more material you have, the more complex parts you can make. As you do this, leakage is a big concern. This is why many people use flex forming because they can use a membrane to push against the metal which prevents the leakage. However, then you have a finite number of uses from each membrane, which can also become a cost issue. Also the use of a membrane prevents making parts with a lot of definition. There is a technological issue to solve. Techniques must be developed to properly design the blank holder to avoid the leakage.
The wide use of this process depends on several factors. One is the robustness of the process, itself because you don’t want to be in the business of making scrap parts. Hard dies are a proven process where the amount of failed parts can be projected. With hydroforming we still don’t know enough about the technology. We’re currently working with a company in Germany to figure out the proper design for the die holder.
Q: Based on the inherent drawbacks of the process, would you say the proliferation of automotive models will lend itself to further uses of hydroforming?
A: It could help, yes. That is what the people who build these presses are dreaming about. The desire for unique designs may also lend itself to hydroforming. High end sports cars may also be a sensible market for such a technology since companies that produce them don’t have high volume demands.
Q: What actual parts would you think make the most sense to be produced from a sheet hydroforming process?
A: I would say outer panels as well as inner panels could be done. You can create a very good surface finish, for one thing. You can also make a product in one die which is advantageous. And a cost savings could be levied there due to a need for fewer dies. I remember visiting Audi a while ago and seeing them experiment with hydroforming for prototype models using a 3,000 lb. press.
More Stories
Buying Car Insurance in Toronto? Don’t Make These Rookie Mistakes
Extend Your Range, Maximize Your Storage with FRDM’s 45 Gallon Combo
How to Install a Ford Bumper Yourself (Step-by-Step Guide)