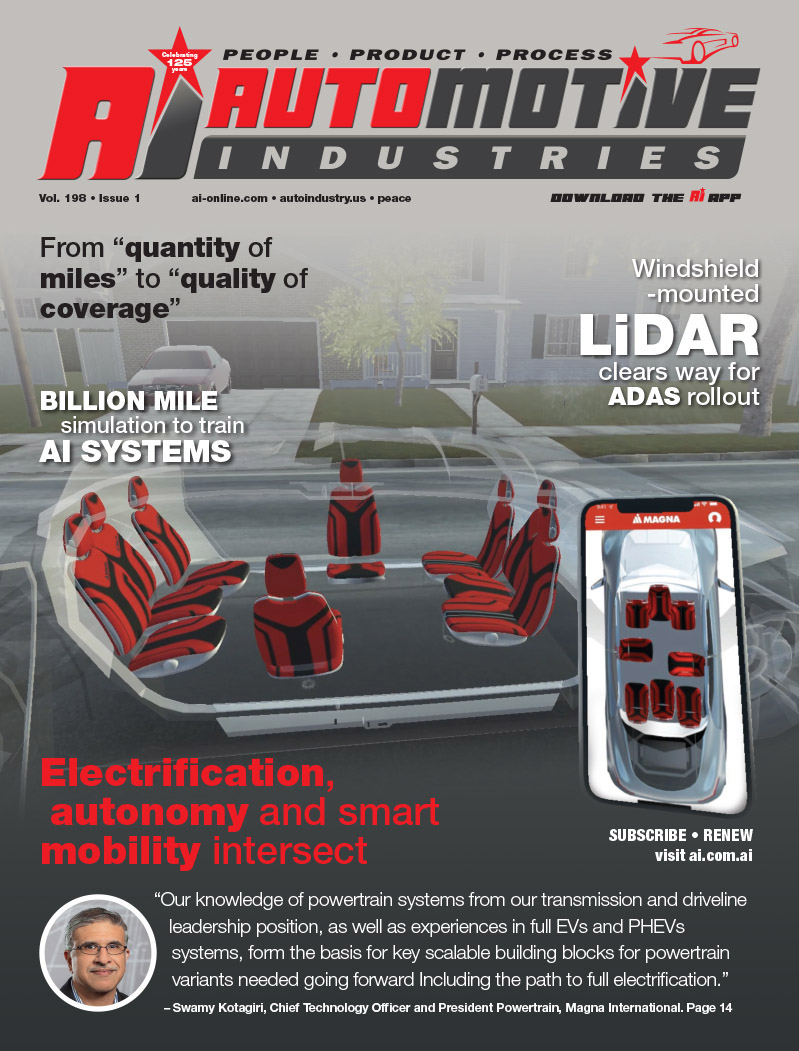
In the search for lighter, stronger more fuel efficient cars, OEMs are not only looking at new materials, but also exploring new ways to use existing materials. One of the latest innovations is plastic/metal hybrids. Plastic/metal hybrid parts are made up of a thin formed sheet metal profile supported by plastic ribbing. The plastic ribbing adds to the rigidity of the structure without a large increase in weight.
Hybrid plastic/metal components are manufactured using a standard injection molding process. The metal stampings are placed in the injection molding tool and the plastic structure is injected into the mold, holding the stampings together and creating a single unified component. This process allows designers to use metal only where it’s needed. Several metal stampings can also be ‘molded’ together, eliminating the need for welding, reducing the number of assembly steps.
![]() |
The inflatable TPU bladder (the gold cushion top) is blow-molded directly to a rigid plastic or metal seat frame (bottom) creating an integrated unit. |
After 12 years of success in plastic/metal hybrids the folks at Bayer Polymers are expanding the process into other areas. Their Thermoplastic polyurethane (TPU) blowmolded hybrid is a patent-pending process that combines rigid materials (metals or engineering plastics) with flexible materials inside a mold where the TPU bladder can be molded directly to the metal or plastic frame. TPU was chosen for its high resistance to wear and tear as well as punctures. It is also resistant to oils, grease, fuel and chemicals and remains highly flexible at cold temperatures.
Bayer sees a lot of potential for the process in automotive seating applications. Not only does the integrated bladder/seat frame assembly eliminate the need for any part assembly, reducing both manufacturing time and cost, but the inflatable bladders can be used to add function and comfort to the seat as well. By inserting a valve into the bladder, air can be pumped in or out of certain portions of the seat. These bladders could be added to the seat bolsters and sides of the seat and inflated to form a sport-seat that would wrap around the driver. Seat cushion and lumbar support could also be adjusted.
Chris Cooper, senior processing engineer at Bayer says that the process shows promise for other interior components, such as arm rests, head rests, interior door panels and headliners. The process also allows for part integration, like storage bins, map pockets and cup holders built into door panels.
A soft air-filled interior might also make the car safer. An air-filled headliner could possibly be one answer to meeting the National Highway Traffic Safety Administration’s head impact protection requirements.
“We don’t have data that would support that,” says Chris Cooper, “but it is under discussion.” The hybrid process uses existing blow-molding machines with no need for modification.
The rigid frames are loaded onto a carrier and then placed into the mold by robot. The bladder is blow-molded over the frame with mechanical interlocks, formed in the molding process, holding the structure together. The process does allow for design options such as the integration of the valve during the molding process or added as a secondary process, an optional flexible web to connect separate seating sections for adjustable chairs and even the possibility of molded- in decoration, either film or fabric.
Applications for the process include seating for all-terrain vehicles, automobiles, bicycles, lawn tractors, motorcycles, snowmobiles and watercraft.
Bayer is currently working with several non-automotive OEMs on parts using this process, and while no automotive OEMs have signed up, Cooper says that they have shown interest in the process.
In current seating applications, foam is used for support. The ultimate goal for the TPU molded hybrids is to someday eliminate the need for foam altogether, aiding in the recycling of the vehicle.
More Stories
Buying Car Insurance in Toronto? Don’t Make These Rookie Mistakes
Extend Your Range, Maximize Your Storage with FRDM’s 45 Gallon Combo
How to Install a Ford Bumper Yourself (Step-by-Step Guide)