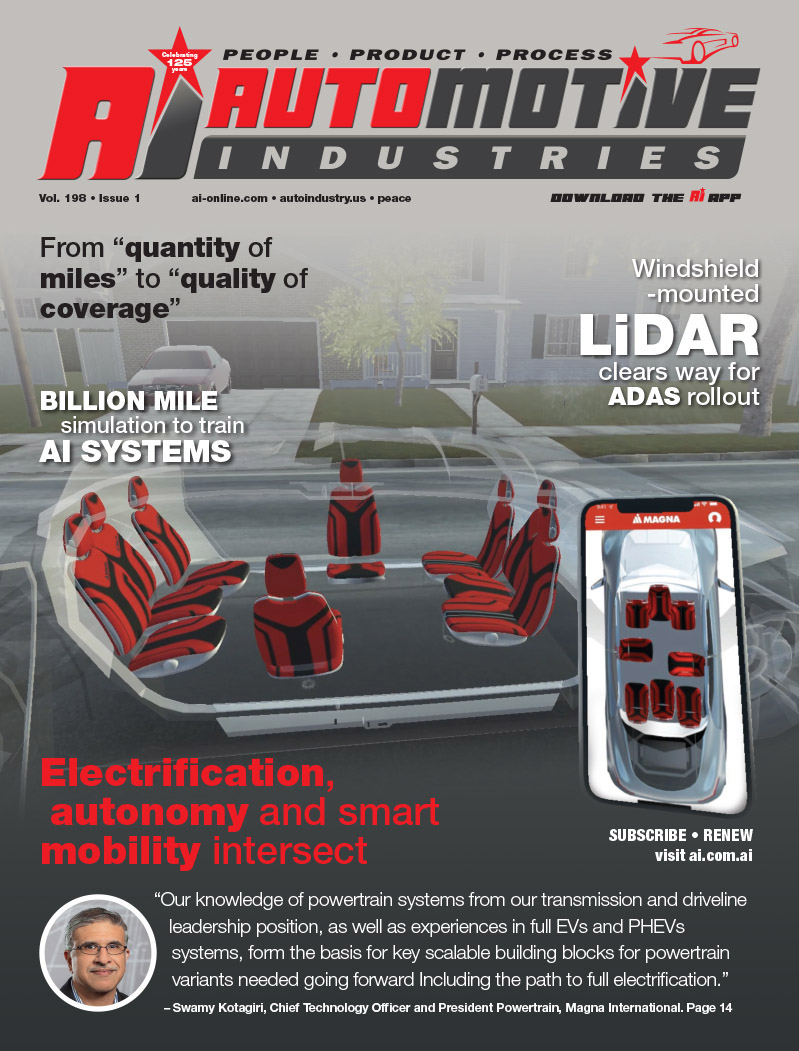
Aluminum panels with more formability than steel allow for complex-designed closures at high volumes. Quick Plastic Forming makes it possible.
If you were the proud owner of a V-8- powered 2000 Oldsmobile Aurora, consider yourself special. The aluminum decklid on your Aurora V-8 was made by a process called Quick Plastic Forming (QPF), part of a pilot program that has culminated in the manufacture of aluminum liftgates for the 2004 Malibu Maxx.
![]() |
The all-aluminum, one-piece Malibu Maxx liftgate weighs about half as much as a steel and composite unit. |
The term ‘plastic’ has nothing to do with polymers, but refers to the plasticity or ductility of aluminum when processed under certain high temperature conditions.
The Quick Plastic Forming process involves heating an aluminum sheet and using air pressure to form it against a heated die. Aluminum sheet blanks are sent into a preheater and brought to a temperature of 450 to 500 degrees C.
As the aluminum softens, it actually sags in the middle, similar to a piece of plastic that is being vacuum-formed. The hot aluminum sheets are transferred into a hydraulic press and clamped against an electrically heated die where a continuous force of warm air, at 500 psi, pushes the aluminum against the top die. Once the parts are formed, they are transferred to a cooling fixture and indexed along mesh belts until they are brought down to handling temperature.
There were several technical challenges that had to be dealt with, such as finding a way to uniformly heat the aluminum sheet, transfer it into the press and remove the hot part from the press and keep it stable while it is cooling. “We’re very good at getting from math to the tool,” says Jim Schroth, a GM scientist and member of the development team, “but the key is getting it out of the press and down to temperature.” Alan Taub, executive director science laboratories GM research and development, says that GM has created an extensive intellectual property portfolio, with more than 40 patents issued or pending.
![]() |
Aluminum liftgate panels will be formed by two QPF presses at GM’s Metal Fabricating Center in New Hudson, Mich. |
![]() |
Malibu liftgate panels travel down a cooling conveyer. |
That allows for more complex, single-piece closure designs that increase structural stiffness while taking weight out of the vehicle. Another benefit is that there’s less spring back which requires fewer die tryouts “We can basically go from math modeling to part in single iterations with this technique,” Taub says. “So it lessens die development time.”
In most cases the process uses single-sided tooling, at much lower pressures than conventional stamping, reducing tooling costs as well. “Lower cost tooling allows us to go after very eye-catching designs in low volume vehicles,” Taub says. “At the same time, because of the metallurgical process breakthroughs we’ve had, we can go after volumes as high as 100,000 using the same technique.”
GM launched QPF last year with two forming cells in GM’s Metal Fabricating Center in New Hudson, Mich., that will produce the Malibu liftgate.
The original plan called for a two piece liftgate outer made of steel with an SMC polymer exterior panel.
Using QPF, the liftgate outer can be made of one piece of formed aluminum that not only increases stability but reduces overall weight from 39 lb. to 20 lb.
Taub says the system can produce up to 100,000 liftgates a year, with the ‘sweet spot’ being around 60,000. GM has no plans of going beyond the 100,000 mark. “If you go above 100,000 units,” Taub says, “it makes sense to go back to conventional stamping due to the cycle times.”
Schroth says that cycle times for QPF are comparable to cycle times for polymers. And while he won’t give the actual cycle time for forming the Malibu’s liftgate, he will say that the patent talks about cycle times at two to five minutes per part, but adds that there are certainly applications where they would like to go lower than that.
“We can support volumes up to this 100,000 range, but we’re not close to the six strokes a minute of a traditional stamping operation,” Schroth says. Paul Krajewski, of the GM development team says that a finer grain aluminum alloy could be molded faster. If the aluminum suppliers can make a business case for creating these alloys, then you could see cycle times come down even more.
GM is using 5,000 series 50/80 aluminum, an alloy used in the aerospace industry that has very fine grain which allows for the molding of complex parts with deep draws. Alcoa, in a joint development agreement with GM, has spent the last three years working on improving the alloy used for the QPF process as well as improving other processes involved in the manufacture of QPF panels.
Because superplastic behavior requires a certain grain structure, automotive steel doesn’t lend itself to the process, though GM has made some progress in the lab in forming magnesium sheet.
“I think what you’re going to see both in GM and the competition,” says Taub, “is the end of single material, single process for all the key structural black metal and exterior panels. We’re in a hybrid material type of process world.”
Since this process relies heavily on math-based analysis, that same math-based analysis can be used with several different material processes to determine which one will best fit the part that’s being made.
“We have a process in the company that looks at the entire bill of materials in terms of body build, both GM and the supply base, on every single panel and black metal component on the vehicle,” says Taub. “And we’re in the position to mix the materials and mix the process for the particular product.”
Though GM has built an entire body out of QPF panels, the process will only be used to produce closures in the near future. “The inner panels will benefit most from this technology,” says Schroth, “because in an engineered vehicle structure, there’s actually more complexity in the parts that you don’t see, than in the ones you do see.” But right now GM is the only one who will benefit from QPF.
“At present,” says Taub, “our decision is that this is GM’s proprietary technology used in house.”
More Stories
RAM Trucks in Toronto: Why CarHub North York Chrysler Delivers the Best Experience
Buying Car Insurance in Toronto? Don’t Make These Rookie Mistakes
Extend Your Range, Maximize Your Storage with FRDM’s 45 Gallon Combo