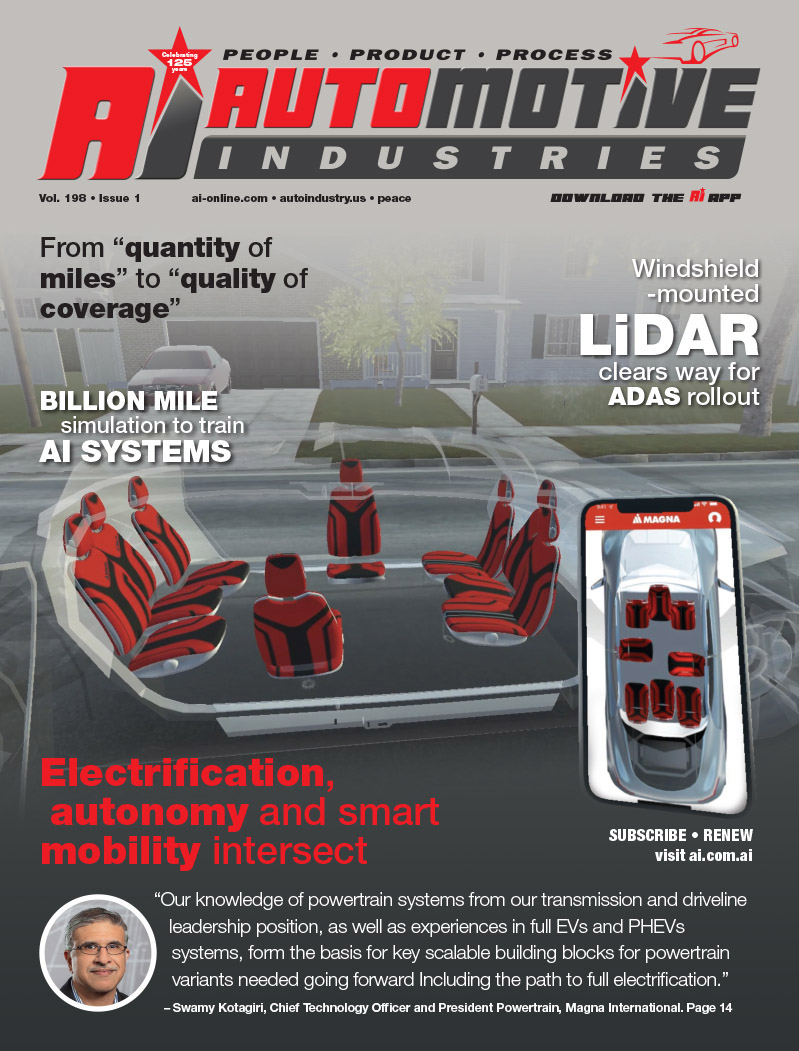
The inventor of lean manufacturing continues to improve the process.
Were James Womack and his M.I.T. research team to update their influential study, “The Machine that Changed the World,” the story’s ending would remain unchanged: Toyota Motor Corp. is still the world’s most efficient carmaker. Content would differ, however, as Japan’s leading carmaker continues to reinvent itself and, in the process, reinvent the industry.
Since 1990, when the five-year project was completed, Toyota has nearly doubled global sales and more than doubled earnings; boosted overseas production by 300 percent, thus reduced exposure to exchange rate fluctuations; and raised the bar on quality.
![]() |
Workers build one of eight models at Tsutsumi final assembly. |
![]() |
The Tsu sumi paint line has been shortened by 30 percent, doubling capacity to 20,000 units. |
Similarly, J. D. Power & Associates reported in its 2004 “Initial Quality Study” that Toyota’s Lexus brand had one-fourth fewer problems than the next closest nameplate. Equally impressive, J. D. Power’s 2003 “Vehicle Dependability Study,” which evaluated quality after two years of ownership, gave nine Toyota and Lexus models first-place finishes. Meanwhile, Toyota’s Tahara plant, production site of three Lexus models, ranked first for the third consecutive year in J. D. Power’s global plant survey. Against this backdrop, Toyota produces more models and has more model launches in more countries than any carmaker in the world: last year the total came to around 60. And since the late 1990s, the company has brought on stream more than a dozen new plants, including engine and casting facilities, and plans to open at least half a dozen more over the next five years.
“It is absolutely phenomenal the way Toyota manages complexity,” says Lance Ealey, senior automotive analyst at Cleveland’s Freedonia Group. “This gives the company tremendous leverage in providing products in micro-segments. In an industry where the automobile has largely become a commodity, differentiation is critical,” he says, then adds: “Managing complexity is the way to cost-effectively offer differentiation.”
Kosuke Shiramizu, Toyota executive vice president in charge of manufacturing and quality management, says production of many model variants in small lots offers carmakers the best chance for success in today’s market. “In the current competitive environment, it would be unwise to target (yearly) sales of 100,000, even 50,000 units for a single vehicle type,” says Shiramizu (see interview). “That would be a huge mistake and, frankly, is the biggest difference between today’s market and the past.”
Among the highlights of the latest rendering of Toyota’s ‘lean production’ system:
- In die-making, Toyota has reduced lead time to engineer and manufacture die sets for large body panels to 1.7 months, from 3 months two years ago, and expects to reach 1.5 months by the end of this year. The time period is shorter for smaller dies (for smaller stampings). In the coming three years, the automaker plans to introduce the new diemaking process at overseas plants in North America, Europe and Southeast Asia. Toyota believes there is a direct correlation between engineering lead time and production startup cost. Thus a 50 percent reduction in lead time, Toyota’s target two years ago, is projected to result in a nearly equivalent saving in tooling expenditures with each new model launch going forward.
- In molding and forging, the company has introduced smaller, faster equipment enabling it to reduce line length, energy consumption and, most importantly, investment. At its Kamigo engine plant, Toyota installed significantly smaller die casting, forging and injection molding equipment which contributed to a nearly 90 percent investment savings.
- In welding, the automaker has completed installation of its “global body line” at more than 20 plants (a total of 35 lines) since the “flexible” welding system debuted at Toyota Motor Vietnam in 1996 and two years later at the automaker’s Takaoka plant in Japan. Installation of 12 more lines, bringing the total to 47, is scheduled over the next three years including Toyota plants in China, Czech Republic, Mexico and the U.S. (in San Antonio, Texas). The global body line has enabled Toyota to reduce tooling investment for new models by an estimated 70 percent and floor space by half.
- In painting, Toyota has shortened the paint line at its Tsutsumi plant by 30 percent to 8,530 ft. and intends to further reduce line length to 6,562 ft. by the end of this year, at which time, because of other process improvements, it will double monthly capacity to 20,000 units from 10,000 today. The result: one of two lines currently in operation will be phased out.
- In final assembly, Toyota reorganized part of the main line at its Tsutsumi assembly plant last August. Under the new scheme, components are brought to a staging area where they are sorted and fed direct to the line or made into modules then brought to the line, eliminating much of the clutter that traditionally builds up inside the plant. The result: line length has been cut in half and the number of models produced has been increased to eight. Toyota plans to introduce the process gradually over the next few years in Japan although management says it will take longer overseas.
![]() |
Smaller die casting, forging and injection molding equipment contributed to a nearly 90 percent investment savings at Toyota’s Kamigo engine plant. |
Meanwhile, Toyota has accelerated the complicated process of consolidating platforms which should have a further impact on the company’s cost structure. Although details are still sketchy, management confirmed plans to reduce platforms to fewer than 10, down from over 20 five years ago.
Toyota is also beginning to see results from its “CCC21” cost-cutting initiative. Now in its fourth year, the undertaking (which stands for Construction of Cost Competitiveness for the 21st Century) sought and is getting an average 30 percent cuts from key suppliers of some 170 components that comprise over 90 percent of the company’s parts budget. Management is now gearing up for round two.
David Smith-Tilley, director of European consulting for Global Insight, expects to see “moderate to significant” bottom line effects from platform reduction which, considering that the automaker is already making record profits, is significant. “Everyone strives to catch them,” says Smith-Tilley. “The problem is they never stand still.”
To illustrate the sort of activities taking place in the Toyota supplier group to meet CCC21 goals, Denso Corp. targeted 40 components and systems for redesign and re-engineering including fuel injectors, fuel pumps, airconditioners, starters, alternators and airbag ECUs. Already the leading volume supplier of many of these components, the company believes it has become the cost leader as well.
In the case of air conditioners, Denso succeeded in reducing size and weight by an average 20 percent from 1998 to 2002. This had a nearly equivalent effect on lowering cost and/or increasing functionality. The company now plans another 20 percent size and weight reduction by 2007, while adding features and upgrading performance at same or lower cost.
Meanwhile, Denso has introduced a “cell” manufacturing structure at its sprawling car heater/air-conditioner plant in Nishio, Aichi Prefecture, that enables it to cost-effectively adjust both line length and automation levels in relation to demand. Monthly, Denso produces 600,000 heaters and combination heater/air-conditioner units. In total, more than 200 heater and air-conditioner variations.
By simplifying design and processes (for example, converting to “snap-on” fasteners for plastic casings), it now takes only three days to reconfigure the assembly line, compared to three months before, at a fraction of the cost. Other Toyota suppliers, Aisin Seiki Co., Koyo Seiko Co., Sumitomo Wiring Systems Ltd., Tokai Rika Co. Ltd. and Toyoda Gosei Co., have been equally resourceful in bringing down costs.
Toyota executive vice president Katsuaki Watanabe, chief architect of the CCC21 initiative, does not feel another round of 30 percent cuts is possible without fundamental changes in vehicle design and production methods. “But if we pursue modular design and reduce platforms,” says Watanabe, “we can lower costs further.”
Refocusing on the big picture, analysts expected the automaker to report a fiscal 2003 operating profit of $15.4 billion when it closed its books this March. Not only would this be the largest profit in Toyota’s 67-year history, it would be the largest in the auto industry’s history. And most observers feel the next five years will see even more black ink. Fueled by growth in global sales to 9 million units, up from 6.5 million last year including subsidiaries Daihatsu Motor Co. and Hino Motors Ltd., Tokyo analysts feel earnings could double to $28.8 billion by the end of the decade.
With prospects for higher profits and sales, Toyota can be expected to boost R&D spending well above last year’s record level of $6.6 billion, enabling it to continue to position itself strategically in various environment, safety and information technologies such as hybrid and fuel-cell vehicles, lane-deviation and frontalcollision avoidance systems, and advanced telematics such as its ‘G-Book’ service.
Meanwhile, the automaker continues to be the industry’s richest with nearly $28.8 billion in the bank while its market cap, hovering around $130.7 billion, is more than that of GM, Ford and DaimlerChrysler combined.
Koji Endo, director of equity research at Credit Suisse First Boston Securities (Japan) Ltd., says nothing seems to phase Toyota. “Two oil shocks in the 1970s, export restraints and the yen appreciation in the 1980s, a second round of yen appreciation in the mid-1990s, and the company keeps getting stronger,” he says.
Not that Toyota is without problems. Its brand is weak in Europe; margins are small though improving in Europe and Japan; and styling, never a strong suit, is regarded as competent but uninspired. Moreover, the company, despite a huge buildup of production capacity in North America, remains vulnerable to exchange rates. Analysts feel that were the yen to rise to $1=Y90 levels, as it did in the mid- 1990s, the automaker could dip into the red.
Toyota also faces growing competition in Japan where, despite holding a nearly 30 percent market share (almost 40 percent including Daihatsu and Hino), at least two domestic competitors, Nissan Motor Corp. and Mazda Motor Corp., have begun to make small inroads.
In fact, if current trends continue, Toyota’s domestic rivals could become formidable, global competitors particularly in Southeast Asia, China and the Americas. Already in fiscal 2003, Nissan, Honda Motor Co., Suzuki Motor Corp. and Daihatsu, along with truck makers Isuzu Motors Ltd., Nissan Diesel Motor Co. and Hino, were expected to report record earnings, in some cases following record profits the previous year. And Mazda, now responsible for the basic engineering of two key Ford platforms, was on course to report near-record profits while steadily improving its own model lineup.
And Japanese competitors have not been idle in the all-important manufacturing area. Over the past three years, Honda invested an estimated $952 million to modernize and standardize its global manufacturing structure resulting in interchangeable lines at more than 10 plants around the world for main models like the Civic, Accord, CR-V and Fit.
Nissan, with the opening of its new Canton, Miss., assembly plant last June, began deploying a new flexible welding line called “hybrid” IBAS that cuts tooling costs in half for each new model launch. The system is smaller and less costly than the first-generation IBAS (intelligent body assembly system) which debuted at Nissan’s Tochigi plant in 1989. Management plans to install the new system at all major plants by 2006. Nissan also has been a Japanese leader in modular production including front-end and center modules for upscale cars like the Skyline, Murano and 350Z.
Unlike Toyota, the automaker invites key suppliers into its plants to handle the module making operation. Management feels it can better control quality in this fashion while keeping labor costs in check as these will be borne by companies like Calsonic Kansei Corp. and Kasai Kogyo Co. Ltd., two Nissan module makers.
Mazda is also looking to trim costs by increased use of modules, but potentially more significant is its expanded role in Ford’s platform strategy. The U.S. automaker plans to adopt the Mazda 6 architecture for as many as 10 new models to go on sale from 2005 and, more recently, has assigned its Japanese partner the lead engineering role for the next-generation “global B car” which will include the Fiesta, Fusion and Ikon.
In this context, the Hiroshima-based carmaker announced in March that it would proceed with the next stage of its “digital innovation” program in hopes of reducing re-work during product development while enhancing quality — in part to deal with extra work resulting from closer ties with Ford, Mazda’s largest shareholder. The planned investment for the three-year period beginning this April is $132 million.
More Stories
Extend Your Range, Maximize Your Storage with FRDM’s 45 Gallon Combo
How to Install a Ford Bumper Yourself (Step-by-Step Guide)
How Artificial Intelligence Could Revolutionize the Car Insurance Industry