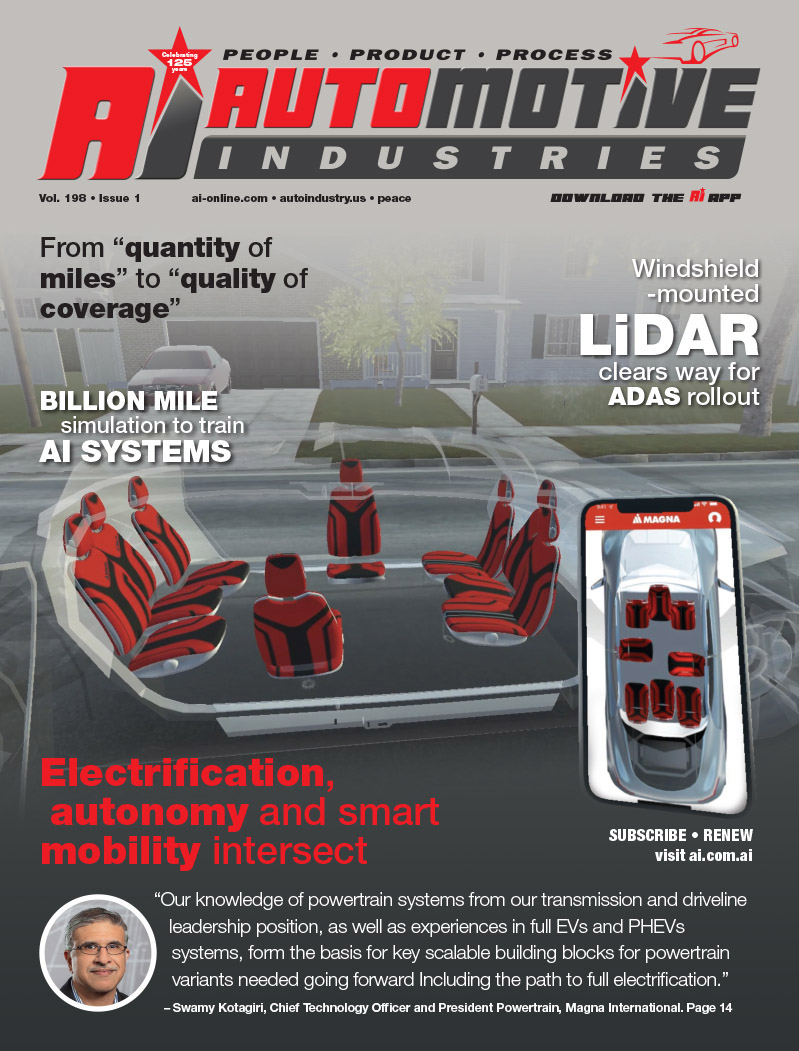
As seats incorporate more and more features, it’s challenging to find enough room to
house the corresponding mechanisms and wiring. BASF’s Engineering Plastics business
thinks it has the answer in an all-plastic seat pan.
The seat pan, which is attached to the seat track, is the part of the seat you sit on.
Most seat pans are made by taking various steel stampings and welding them together.
However, in the Chevy Trailblazer/Envoy, BASF’s Ultramid TG7S glass-fiber reinforced
nylon 6 material has made what once was an all-metal component into an injectionmolded
plastic one. What’s more, while a typical front seat cushion pan might consist
of seven different steel pieces that are welded together to make the structural part of the
pan itself (not to mention the brackets, steel frames or other attachments that are welded
on to hold various seat mechanisms and modules), the BASF all-plastic seat pan is a
single piece.
“In the project we are working on now,” says Marios Lambi, a BASF advanced development
engineer, “we were able to eliminate or consolidate 21 metal parts.” BASF says
its material will be used in an all-plastic second-row seat pan going into production
next year, and it is currently working with a tier-one supplier on a first-row seat application.
Additional advantages include:
Weight savings – a plastic seat pan can weigh up to 50 percent less than its metal
counterpart.
Design flexibility – a plastic seat pan accommodates more ways to attach and
incorporate trim, wire bundles, memory modules, heating and cooling systems,
levers and gears, transmission housing and actuators.
More room for mechanisms – packaging the complete seat in the vehicle is much
easier with the plastic seat pan because multiple parts are eliminated, seats are
thinner overall, and thus, there’s more room for packaging the multiple mechanisms
found in power seating.
So, why are only a small percentage of today’s seat pans made from plastic? Lambi
says it’s a matter of education, comfort level and investment. “This technology is not
used widely yet, because the automotive engineering community isn’t accustomed to
designing these types of components with plastics. Like everyone else, engineers prefer
to work with a material they are familiar with,” Lambi explains. “Eventually, a better
understanding of the benefits of plastic will bring a higher comfort level.”
In addition, he says the manufacturing infrastructure is set up to design with steel
rather than plastic, so it will take a little time to catch on because it requires the OEMs
to change their manufacturing processes.
“Using injection molded plastics will require a greater investment in injection molding
machines by the tier ones and tier twos,” he says. “On the other hand, there are usually
cost savings realized in piece price, or in the very worst case, the change to injection
molding is cost neutral. We have actually seen customers realize significant cost savings
because typical seat pans are made of multiple steel stampings, so you need multiple
tools. All that is eliminated with the single-piece injection molded seat pan.” H
More Stories
End-of-Life Vehicle Management Trends in New Zealand: What’s Next?
Fleet Management Made Smarter with Diagnostics Tools
Best Wheel Size for Off-Road Adventures: What People Get Wrong