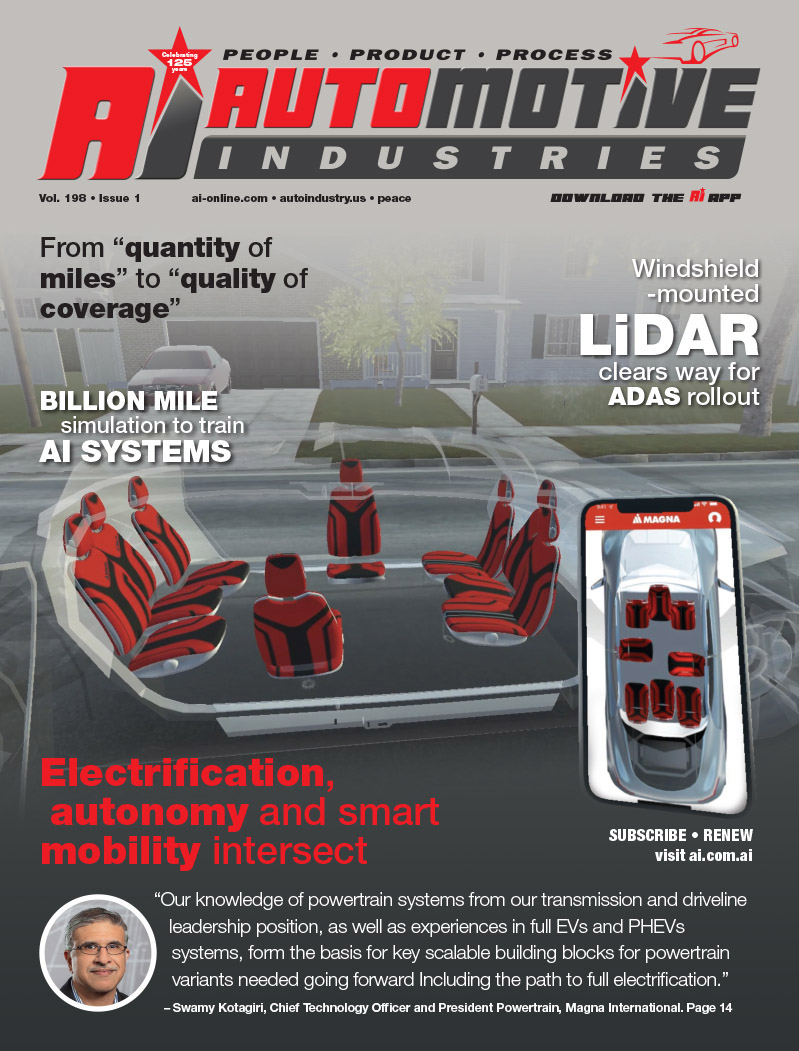
It sounds too good to be true: significantly higher fuel economy, greatly reduced NOx and particulate emissions, and the ability to run on today’s fuels. Homogeneous-charge, compression-ignition (HCCI) engines combine the very best gasoline and diesel engine properties. This alternative combustion process, which uses lean mixtures ignited without a spark or flame front, has been under study for more than 25 years. The late Smokey Yunick touted his version of this technology in the pages of Popular Science magazine more than 20 years ago. Momentum behind HCCI research is now building so rapidly that every major engine manufacturer and a consortium of five engineering schools backed by Department of Energy funding are pursuing this path to low emissions and high fuel economy. Powertrain experts believe HCCI could be the internal combustion engine’s last gasp before fuel cells take over. More than a dozen different names have been used to describe what is now called HCCI. In 1979, engineers at the Nippon Clean Engine Research Institute in Japan perfected a cleaner, more efficient two-stroke using what they labeled Active Thermo-Atmosphere Combustion for use in a 14-horsepower portable generator. Concurrently, Toyota engineers determined through spectroscopic analysis that HCCI chemistry and ignition were fundamentally different from the normal spark-ignition combustion process. Both were more reminiscent of what would be seen in conventional engine experiencing auto-ignition (detonation). Smokey Yunick called his approach hot vapor injection.
Gasoline HCCI
Like the name says, fuel and air are well mixed throughout every region of the cylinder. Time-lapse photos taken through a window in the combustion chamber reveal no localized high-temperature flame front; instead, there are hundreds of evenly distributed specks of light with HCCI, indicating spontaneous combustion of the entire charge. High exhaust-gas dilution and lean mixtures greatly reduce peak temperatures and heat-transfer losses. The extra EGR also facilitates running the engine virtually unthrottled, minimizing pumping losses. Thermal efficiency gains come from squeezing peak combustion temperatures into a narrow window timed for maximum energy release during the expansion stroke. The potential is diesel-engine fuel efficiency — 15-20 percent gains over today’s gasoline engines — with NOx emissions so low that reduction-catalyst after-treatment is unnecessary.
Unfortunately, HCCI works better in theory than in practice. Achieving sufficient thermal energy late in the compression stroke to trigger auto-ignition consistently is the most serious challenge. The diesel approach of using a high compression ratio was an obvious avenue for investigation but researchers quickly discovered that ratios beyond 12:1 cause severe knock during full-load operation. Other concerns are excessive rates of pressure rise and the combustion-generated noise associated with too-high compression. Today, there’s agreement that elevated compression ratios are not well suited to smooth HCCI operation.
A more practical avenue is using high levels of EGR to supply the desired thermal energy. A strategy called recompression traps exhaust in the cylinder by closing the exhaust valve early. Another approach called rebreathing captures exhaust after it has left the cylinder. The intake valve can be opened briefly during the exhaust stroke, the exhaust valve can be opened slightly during the intake stroke, or exhaust can be recycled by simply postponing the exhaust valve closing. Researchers have investigated all of the above possibilities, including mixes of recompression and rebreathing; many have been proved effective.
Achieving the necessary homogeneous fuel-air charge is relatively easy using early injection of the fuel into the intake port to maximize the time available for mixing prior to combustion. But researchers also discovered that late injection directly into the chamber is the best means of triggering combustion without a spark. Direct injection avoids premature ignition, thereby facilitating a higher compression ratio. Varying the injection timing during the compression stroke is also an effective means of balancing the amount of NOxversus HC and CO emissions produced.
Several fuel-injection schedules have been investigated. Injecting fuel into retained and compressed exhaust gasses prior to the intake stroke commences the chemical activity that results in auto-ignition at the end of the compression stroke. A secondary fuel injection event has also been used to trigger combustion, though emission levels suffered with this method. Trying every possible avenue, experimenters have even used a spark plug to initiate a flame that burns a portion of the charge which in turn drives the remainder into auto-ignition. Results were mixed with this strategy. Mitsubishi engineers experimented with a 6-stroke gasoline engine using two combustion processes: a stratified ultra-lean combustion triggered a second HCCI combustion phase. NOx reductions and fuel efficiency were good but the operating range was limited to light-load conditions.
Unfortunately, power density is lower with HCCI than with gasoline engines running with stoichiometric air-fuel ratios. But the greater unsolved problem is that HCCI operation is not yet possible during engine warm-up, at very light loads, and at idle because exhaust energy is too low to trigger auto-ignition during these conditions. A second concern is that peak combustion temperatures well below the threshold of NOx formation result in incomplete oxidation of the fuel and air. As a result, HC and CO emissions can be 50 percent higher than today’s spark-ignited gasoline engines. A third dilemma is exhaust temperatures too low for proper catalytic converter function.
Full-load operation is also problematic. With spontaneous combustion occurring very late in the compression stroke over very few degrees of crankshaft rotation, peak rates of pressure rise and engine noise are intolerably high. Internal components can be damaged by excessive loads. Extending HCCI operation into the full-load regime has not yet been possible. To stretch the range where HCCI is practical for gasoline engines, researchers are attacking several fronts. Stop-start operation is one way of avoiding the troublesome idle mode. Cylinder shutdown shortens the time the engine operates lightly loaded. Pulse-flame jets are under investigation as a means of controlling combustion timing.
Diesel HCCI
HCCI research for diesel-fueled engines began a decade ago with emphasis on NOxand particulate matter (PM) reductions. As is the case with HCCI gas engines, auto-ignition occurs at multiple points throughout the combustion chamber. Emission reductions come from burning a homogeneous mixture of diesel fuel and air at lower than normal temperatures. Typically combustion begins below 2000 degrees F and ends before constituents reach 3000 degrees F avoiding the 3500 degree F threshold of NOx formation.
Successful diesel HCCI operation depends on a precise thermal balance. High temperature intake air is necessary because diesel fuel is slow to vaporize. But since auto-ignition temperatures are relatively low, it’s difficult keeping a hot, compressed mixture from lighting off prematurely.
Three means of combining fuel with air have been investigated. Fuel can be injected into the intake manifold. Mixing prior to autoignition can also be achieved by direct injection well before top dead center. A third approach is later than normal injection with high levels of EGR used to postpone combustion. A fourth strategy is to use water injection to slow the temperature rise in the combustion chamber, thereby delaying ignition until the charge is well mixed.
Experiments with premixing have successfully cut NOx emissions by a factor of 100. Unfortunately, fuel economy losses are so significant that this is not a fruitful avenue for further research.
Mitsubishi engineers had better luck with early direct injection and supercharging: 90 percent NOx reductions, minimal smoke and fuel consumption similar to a normally aspirated diesel with retarded timing. Nissan introduced a late direct-injection HCCI-like diesel for sale to Japanese customers in 1998. High swirl intake ports and a torroidal combustion bowl facilitate rapid fuel and air mixing. NOxemissions and noise are both substantially reduced by HCCI operation up to one-third peak torque and half maximum speed.
Toyota engineers have achieved HCCI combustion up to half-load and half-speed in another diesel engine offered for sale since 2000. This engine combines early and late injection to achieve low smoke and reduced NOx emissions.
Ongoing Research
Homogeneous-Compression Charge Ignition A. Fuel and air are well mixed throughout every region of the cylinder. B. Ignition is made up of hundreds of evenly distributed specks of light with HCCI, indicating spontaneous combustion of the entire charge. C. The potential is diesel-engine fuel efficiency with 15 to 20 percent gains over today’s gasoline engines with NOx emissions so low that reduction-catalyst aftertreatment is unnecessary. ![]() |
To move HCCI out of the lab and onto the road, dual-mode engines will probably be necessary. That will permit blending the benefits of this alternative combustion process with conventional operation for those regimes were HCCI is less beneficial and/or impractical. Research indicates that direct injection and low compression ratios will facilitate mode switching. In the diesel category, HCCI can eliminate the need for NOx and PM aftertreatment during light-load operation. During high loads, the exhaust can be routed through appropriate traps and reduction catalysts. Oxidation catalysts will still be necessary in both gas and diesel engines for HC and CO mitigation.
The University of Michigan’s professor Dennis Assanis, who directs a multi-university HCCI research consortium, expects dual-mode engines to appear soon. He notes, “HCCI is a nearer alternative than the fuel cell. The HCCI engine can burn all fuels, including hydrogen.” So perhaps IC engines aren’t quite ready to go the way of buggy whips after all.
For additional information on this subject, see SAE publication PT-94 “Homogeneous Charge Compression Ignition (HCCI) Engines.”
More Stories
End-of-Life Vehicle Management Trends in New Zealand: What’s Next?
Fleet Management Made Smarter with Diagnostics Tools
Best Wheel Size for Off-Road Adventures: What People Get Wrong