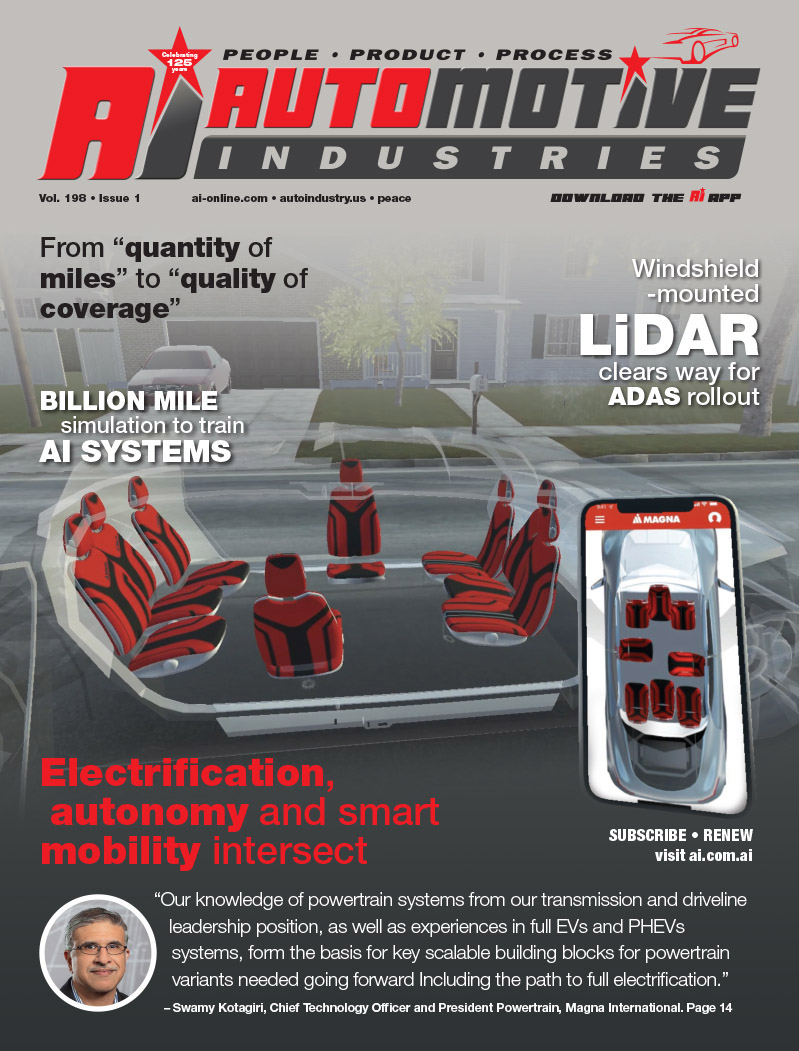
Product liability questions are of enormous importance for companies in the automotive sector, according to international law firm Clifford Chance. The company examines some of the issues for APN readers.
Defects may be categorised as design defects; production defects; and instruction defects.
There is a large body of case law dealing with these aspects, and many articles have been written on them by legal experts, but as yet there are few legal terms of reference indicating what constitutes efficient product liability risk management in practice and how a company should react if a crisis arises. Yet dramatic recall actions demonstrate that this topic is of considerable relevance. Both component suppliers and final automobile manufacturers should therefore take organisational precautions and lay down clear guidelines, in order that they can react promptly and appropriately in the case of a crisis.
In addition, under European Council Directive Article 5 of Directive 2001/95/EC on General Product Safety and national legislation passed to implement it, companies have an obligation to ensure an appropriate internal risk management system. But proper risk management is also important in order to prevent claims being made on the employees and the management in person. There have been several cases in which civil and criminal legal proceedings have been taken against employees and managing directors or boards because they acted inadequately in a crisis. A preventive risk management system could have avoided these cases.
The following observations focus on the legal implications in Europe, in particular Germany, but may also be applicable to other jurisdictions.
Product liability
Product liability cases are situations where a defect in the product creates danger to the health, life or property of the buyers or third parties. For example, if an airbag inflates during a journey, not only must the costs of the defective airbag be taken into account, but there is also a considerable danger that this may lead to an accident in which the driver or even complete outsiders suffer injury or damage. This type of case will be considered in the following section.
Preventive measures
Defects must be avoided in the area of product development, product manufacture and instruction, in order to prevent liability cases as far as possible. However, the duties imposed on component suppliers and final manufacturers are considerably wider. In particular, all those involved in the supply chain have the duty to monitor the product. As part of their active duty to monitor the product, they are required, independently and on their own responsibility, to follow up indications of potential sources of danger and to organise a suitable information system for this purpose. Component suppliers and final manufacturers are therefore required to actively monitor the market. In addition, there is the mandatory duty to monitor the company’s own operations carefully and to react to customer complaints or conspicuously frequent orders for particular replacement components (the effects of which may have safety implications). The extent of these duties to monitor products varies: the final manufacturer of a product will normally find it much easier to monitor the market and assess customer complaints than, for example, a component supplier will, and therefore it is predominantly the final manufacturer who is given the duty. However, such duties may also be imposed on the component supplier, albeit – depending on his position in the supply chain – to a limited extent. A further important means of reducing product liability risks is ensuring the traceability of the defective products. There must be the greatest possible transparency in the production process and the location and number of the products that have left the manufacturer.
As part of preventive risk management, it should also be ensured that sufficient insurance policies have been taken out. In particular, it should be determined whether the insurance policies also cover the recall actions, which are often extremely expensive. However, the most important factor is that there should be an in-depth crisis plan in the company, laying down in as much detail as possible the sequence of procedure during a crisis and the competencies within the company. The main aspects that must be taken into account and laid down in the crisis plan are set out below.
Crisis team
One of the fundamental aspects of a crisis plan is establishing a crisis team. The crisis team must be reachable at all times, in order to be able to react rapidly in the case of a crisis. In addition to the appropriate specialists, the top management of the company must also be a member of the crisis team. Admittedly, in a business system based on the division of labour even within enterprises, tasks are inevitably allocated both horizontally (for example, at the management / board level, by creating several departments) and vertically (the delegation of duties to subordinate staff). But in a crisis, the responsibility of the management / board is revived, which means that the management / board must deal with the product liability case in person; failing this, the management may be liable.
In order to preserve flexibility of decision, however, the crisis team should be as small as possible. In practice, the selection of the crisis team must be adapted to the product liability case in question. As a general rule, the team should include the following members: member of the management or board; member of the legal department; head of quality assurance; head of research and development; head of production; head of marketing; and press spokesperson.
Investigation of the facts
It should be decided which person in the company is responsible for receiving notifications of damage and who starts the procedure of investigating the facts – independently of the organisation of the crisis team. The head of quality assurance often undertakes this task.
As part of a prompt and effective reaction in a product liability case, great care should be given to the recording and analysis of the facts. The main issues are the following:
– Who reported the product liability case?
– What are the precise specifications of the product in question?
– For what reason is the product being criticised?
– Has damage already occurred?
– Are there any safety implications in connection with the product?
– Are external parties already involved (other manufacturers in the supply chain or public authorities)?
This information must be collated with all information internally available. In the ideal case, the company will already have a database containing – in particular – knowledge obtained in connection with earlier cases and failure mode analyses that have been carried out.
Evaluation
The collated information must be evaluated and analysed without delay. Whether and how far this is done by the crisis team or by subordinate staff is a question of the individual case. The problem of the large quantity of data and sources can often be dealt with by the use of appropriate software tools.
Decision making and possibilities of action
The crisis team must decide, on the basis of all the information, what measures are to be taken. As part of an overall consideration and evaluation, it must be assessed how great is the danger of damage occurring and what objects of legal protection might be affected (or are already affected). Here, the yardstick must be the avoidance of dangers to the users of the product or to third parties. The greater the danger, the more intensively and urgently must the component supplier or the final manufacturer act.
The concrete action to be taken depends very much on the individual case. In particular, it obviously depends on the position in the supply chain at which the entity with a duty to act is located. While the final manufacturer, as mentioned above, is in direct contact with the customer and therefore could make a recall or give a warning, this will often be difficult for the components supplier at the beginning of the supply chain who does not have the logistic means for such action. In the individual case, the duties of this components supplier may be reduced to warning its direct customers within the supply chain and supporting the other components suppliers involved as well as the final manufacturer. However, according to Article 5.3 of Directive 2001/95 on General Product Safety and the national legislation passed to implement it, the components supplier, the dealer and the final manufacturer may also be obliged to inform the competent authorities.
Subsequent analysis
Although the main aim is to avoid product liability cases as far as possible, there should also be an attempt to derive the greatest possible benefit from a crisis. The departments involved ought therefore, after the crisis is over, to discuss between themselves what consequences can be drawn and how product quality can be improved in future. As part of this process, consideration may be given to undertaking subsequent marketing measures in order to avoid damage to the company’s image.
Outlook
The main aspects that must be considered in a crisis are outlined above. They should be part of the crisis plan that has to be drawn up. However, it is important to note that the individual points discussed present themselves in various ways in each company and need to be examined in more detail. In addition, attention must be given to the specific implications of the national product liability law in a given country and the requirements regarding product liability. The measures to be taken in a crisis may differ. There can be no standard solution. It is therefore crucial that the crisis plan is drawn up and finalised with the cooperation of the technical specialists, management and lawyers, who are specialists in product liability law within the relevant jurisdiction.
More Stories
RAM Trucks in Toronto: Why CarHub North York Chrysler Delivers the Best Experience
Buying Car Insurance in Toronto? Don’t Make These Rookie Mistakes
Extend Your Range, Maximize Your Storage with FRDM’s 45 Gallon Combo