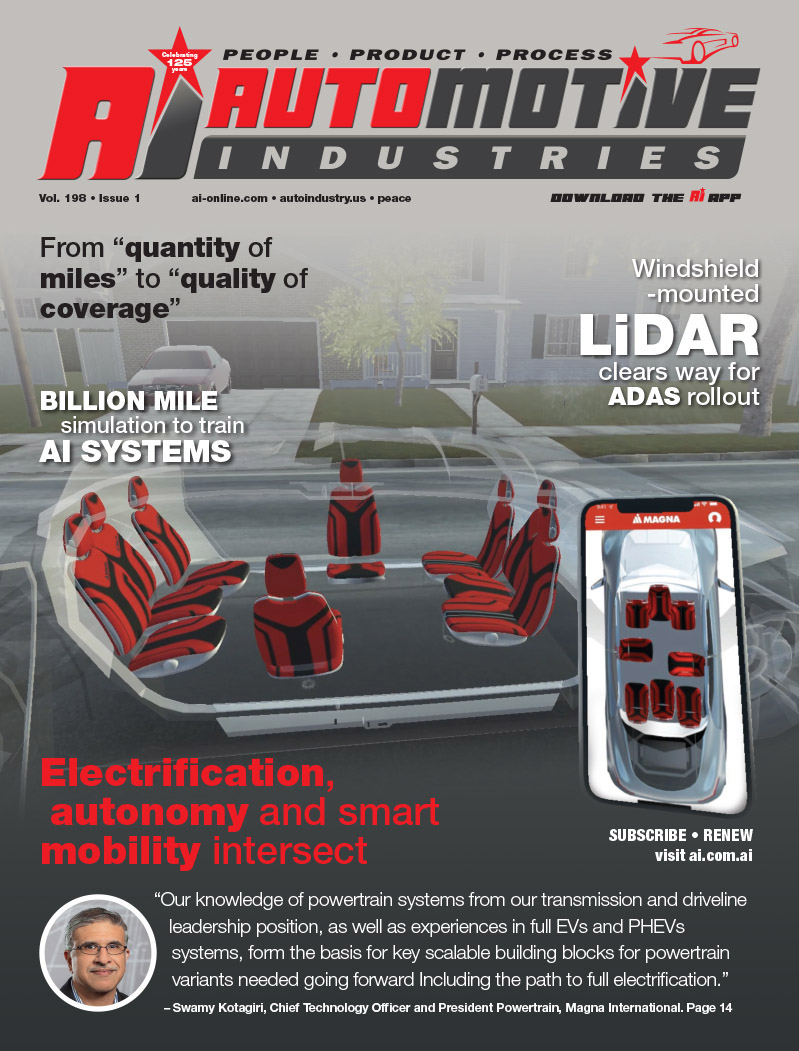
The perennial top challenge facing the automotive industry is cost, say 24 percent of attendees. Alternate powertrain technologies and vehicle safety were selected as the number one challenge by 18 percent and 13 percent, respectively (survey results attached). “These are still the ‘Big Three’ overall vehicle enhancement needs for the industry,” said Chris Murphy automotive director – Americas, for DuPont Automotive Performance Materials. “Interestingly, even though cost remains the top concern, it’s declining — not because it is not important — but because it is now a prerequisite: getting a new technology heard requires a cost advantage first.”
To illustrate how the supply chain can come together to deliver cost- effective consumer-facing technologies, Murphy referenced the new, much acclaimed Delphi Active Energy-absorbing Steering Column, which taps several DuPont materials in applications ranging from a critical C-shaped bushing that provides the ability to control the telescopic motion of the steering column in a frontal collision, to a retaining strap and break-away capsule that supports the steering column at the dash. “The opportunity to work with Delphi early in the development cycle allowed us to fully understand the demands of the application and — importantly — the right materials to make this critical safety component,” said Murphy.
Going global
New to the survey findings this year is the addition of “globalizing the supply base” as the number one strategy to strengthen the auto industry: 16 percent selected this, up from just 7 percent in 2004. “Many of us in the industry have been global for quite some time, but our work in the past few years has been to become more ‘glocal’ in our approach to helping customers,” said Murphy. “That is, we are using our global networks — and strengthening them with new investments — to deliver customer-focused solutions locally to global customers.”
In the past year, DuPont has announced several new global automotive facilities:
– Two new manufacturing sites (DuPont(TM) Zytel(R) HTN high-performance polyamide and DuPont(TM) Vespel(R) parts and shapes) in Singapore
– New production lines at the existing Shenzhen, China site
– Capacity increases in Savli, India
– A new design center in India and testing facilities at Savli
– R&D Center in China
– DuPont Automotive Center and an automotive coatings facility in Japan
Vehicle Safety
Nearly half the SAE attendees say vehicle safety is a “very important” attribute that consumers are willing to pay for. Fuel efficient/environmentally friendly vehicles were selected as very important by 40 percent and styling by 39 percent, according to the survey results.
Occupant detection, airbags, collision avoidance are the three safety system advances that will receive industry attention and resources. On the horizon is the Transportation Bill — today only 14 percent expect this emerging legislation will impact the industry; in five years, 33 percent expect an impact on the industry.
“There is no question anymore with all the data we’ve seen that ‘safety sells,'” said Michael L. Sanders, global director for DuPont Automotive Safety. “While passive safety improvements are still necessary, the development focus is clearly on active, electronic safety systems such as radar and electronic stability control (ESC) in crash avoidance. DuPont is engaged in supporting these systems with microcircuit materials, high performance thermoplastics and more.”
Powertrain Technologies
Not surprisingly, alternatively powered vehicles will have the greatest impact on the industry over the next 5-10 years, say 35 percent of attendees. “The question of which technology will dominate still haunts the industry, but some clear trends are emerging,” said Gianluigi Molteni, DuPont Automotive Global Powertrain segment manager. “Optimizing the gasoline engine — two years ago the top strategy — is quickly giving way to work in hybrid electric and diesel engines while fuel-cell development remains active at a longer development timeframe.
“Overall, the focus is to improve performance and productivity,” Molteni continued. “That’s often when we at DuPont Automotive are engaged because we can help on both dimensions with programs that can — for example — improve air flow using 3D blow-molded air ducts or enhance durability with high- temperature resistant materials. Also, our leadership in European diesel applications can be leveraged here to help speed programs and improve performance.”
Cost – the Perennial Challenge
While cost issues challenge the industry, it also helps drive innovation and collaboration, said Murphy, referencing a new color standards process created by DuPont, color partner Clariant and the EWCAP (Electrical Wiring Component Application Partnership) division of the United States Council for Automotive Research (USCAR), which represents DaimlerChrysler Corp., Ford Motor Co. and General Motors Corp. in collaborative research. The guidelines are designed to standardize and streamline the number and variety of colors for connectors to simplify both manufacturing and quality control. “In effect, it’s a faster, simpler way for the value chain to deliver connectors to the end user and take cost out of the system,” said Jim McCutcheon, DuPont Automotive technical consultant.
“There’s no doubt that everyone in the industry is experiencing dramatic changes in technology and in the way we work with each other,” said Murphy. “But by working collaboratively to address intense challenges we can surface innovative, sustainable solutions.”
More Stories
Will Cars Function Like Smartwatches in the Future?
K 2025: The Power of Plastics! Green – Smart – Responsible
Automechanika Shanghai 2024