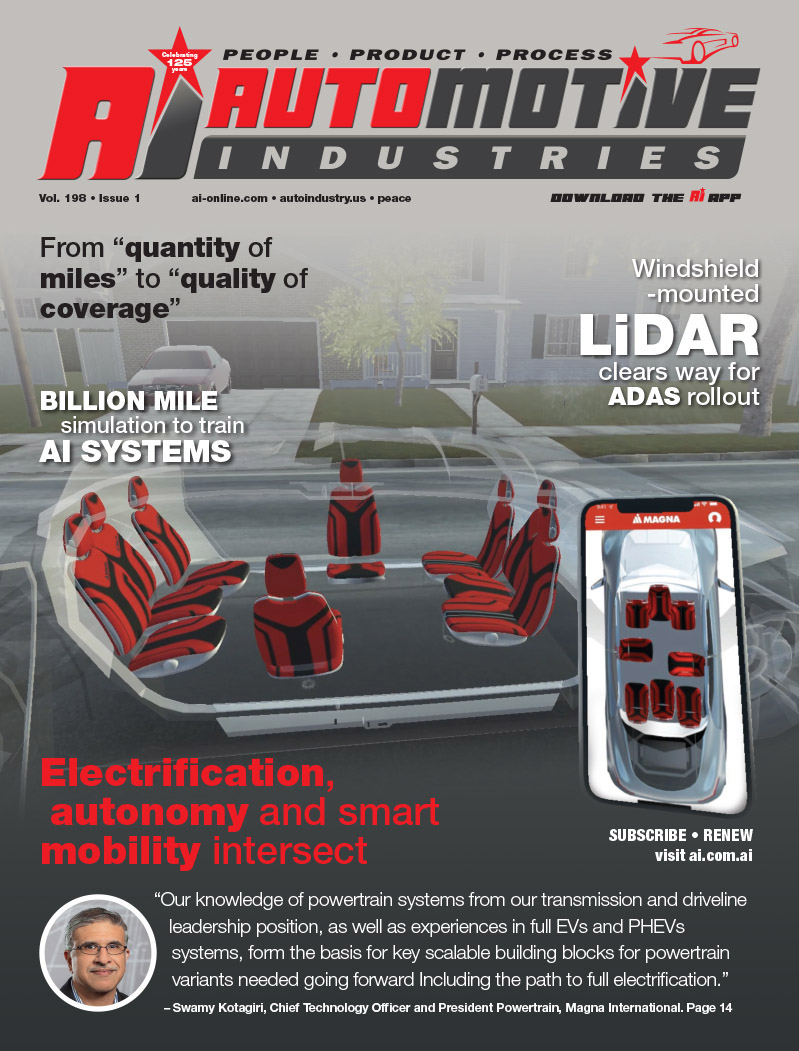
Dutch company SMS Stamp Tool Technologies started operations in 1958 as a small tool company. Today, it is a leading designer and manufacturer of high speed, complex discrete and modular progressive tools. The company’s products are used by some of the world’s best known companies in the automotive, electronic, semi-conductor, consumer article, medical and photo industries. SMS is a specialist in the CAD/CAM manufacturing of high performance stamping tools.
According to the company, the trend towards continually updating production processes effects the design of progressive tools, where innovation is the key word for optimizing tool concepts, tool life and production speed. Trying to keep up with customer requirements, SMS tool design is based on a compressed modularly built concept with a reduced number of production steps. In this concept the materials used for cutting parts plays a significant role in the performance of the tool.
Most tools are designed in carbide, but with the integration of ceramic cutting parts (for example zirconium oxide) in stamping tools, the yield profit has a dual effect; a significant tool life improvement with a factor 3 till 5 compared with carbide and an important environmental effect resulting in a reduced use of stamping oil. The company says that by virtue of increased durability, ceramics are ideal in a wide range of progressive tools for stamping high production volumes where long operating times are required. The application of ceramic components in lead-frame tools compared with carbide, results in a four- till fivefold tool life improvement realizing extra million strokes between each grinding interval and a significant reduce of maintenance costs and production loss.
Ceramic is also an ideal material in tools for stamping copper and non-ferro materials. SMS won the European Engineering Award and the Micron d’Or for the development of ceramic in lead-frame tools in 2002.
A sister company of SMS, Worldwide Tooling Service or WTS was founded in 1997 and specializes in the CAD/CAM manufacturing of precise tool- and mould components, in tool maintenance and overhaul.â€The idea behind the separation was serving our clients with emergency turnarounds for components in breakdown situations and short lead times for spares and tool components,†says a blurb on the SMS company website.
According to the company, the bulk of the carbide and ceramic punches produced by SMS and WTS have an accuracy of ± 0,001 mm. This is because SMS uses automatic profile grinding which is one of a kind in the world. This system is also environmentally friendly since it is designed as a complete closed system and therefore keeps grinding dust and liquid out of the air.
SMS says that it maintains quality control at each phase of manufacturing to ensure all parts are made to specifications. Using sophisticated automatic measuring equipment, SMS quality engineers are responsible for incoming as well as outgoing inspection. Quality is a priority in all operations and statistical process control (SPC) is operational throughout the factory. There is continuous program for quality improvement and the factory floor is completely scheduled on JIT, OTD and zero-defect norms. SMS’s facilities in the Netherlands is TUV certified NEN-EN ISO 9001. Some of the products SMS manufactures include lead-frame tools, power-frame tools, connector tools, progressive dies, fine-blanking tools, tool components and smart integrated turnkey project solutions for metal-plastic combinations.
Automotive Industries spoke to Frits van der Pol, president and chief executive officer of SMS Stamp Tool Technologies.
AI: How much of your business comes from automotive clients?
Roughly speaking, about 30% of our turnover is directly linked to the automotive industry. Indirect around 50%, if we consider that our products which we deliver to several other types of industries, as connector and semiconductor, will be delivered to automotive clients also. This percentage seems risky, but because we are involved in so many markets, the percentage per client is not more than 8 till 10%.
AI: What are some of SMS’ products that are aimed solely at automotive customers and how has R&D helped develop these products?
Stamped parts produced with fine-blanking dies are solely used in automotive industries for car parts as steering/gear mechanism, seats, safety belts, etc..SMS designs, manufacture and deliver production equipment in accordance to customer product requirements. The product design comes from the customer, the production equipment design from SMS or in co-operation.
For tool designs and material, the SMS R&D facility is involved in optimising existing or developing new stamping and process techniques and materials. Some of these projects are in European connection or directly linked to customer’s undersigned with an NDA.
AI: Are your customers mainly European or do you have a strong presence globally? Please give us details about exports.
A couple of years ago, our main market was the semiconductor industry globally. Because of severe market fluctuations, price erosion and a disappointing rate of exchange, most semiconductor-related companies transferred their facilities from Europe and the USA to the Far East. SMS has decided to reduce this market share till about 5% anticipating for shorter life cycle and time to market of products for new upcoming markets.
Based on a strong EURO, our main base is Europe with a focus on automotive for 30% and other types of industries as connector, consumer, medical, health and semiconductor nicely divided.
Globally we export about 5% to the USA and the Far East. The main focus is still Europe, with a percentage of 45% outside The Netherlands and 55% locally.
AI: Do you have any plans to open new SMS facilities in other countries? If so, where?
Taking our goals for the coming years in new products for upcoming European markets into account, we have start up plans to increase our activities as a first tier supplier in Europe. The home base of SMS stays in The Netherlands, but we are focussing ourselves in starting up joint ventures or subsidiaries globally. This will be effective within a couple of years. Due to the present stage of negotiations,w e are not able to discuss or to determine the exact location.
AI: What are some of the new technologies SMS is working on and when will they be available commercially?
Plans, which we have started last year, are based on a “three-stage rocket†principle.
In co-operation with customers, we are developing new stamping technologies for three specific types of industries, which should results in faster production speeds and less operational costs.
Based on our experience in supplying turnkey product life cycle solutions for metal plastic combinations, we are also developing new types of materials and processing techniques in this particular field.
From our operational side, the daily focus is on a strictly lean manufacturing-machining basis in order to stay ahead of competition. In this way we are able to supply customers with logistic advantages, leading to a reduced stock and fast deliveries of components in according to a supermarket principle.
More Stories
Sonatus – The industry is shifting gears to software
Cybord warns of dangers of the stability illusion
HERE building trust in ADAS systems