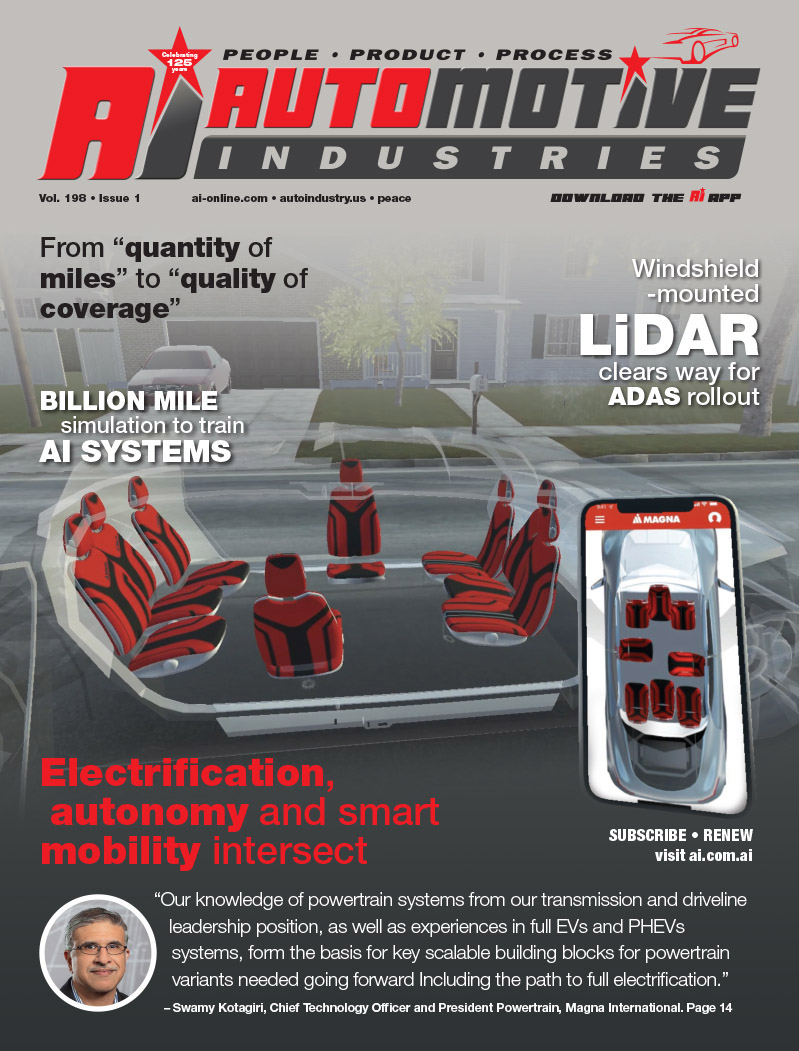
Metzeler Automotive Profile Systems specializes in the design and manufacture of automotive sealing systems for doors, windows, boots and hoods. The company uses a specialized process development centre in Tennessee to simulate complex production processes as well as test them on real production lines. A newly built European Technology Centre has allowed the company to improve its quality, speed and efficiency in the development of new sealing systems. In 2006 its turnover was approximately US$1-billion.
MAPS designs and manufactures new technologies in the areas of material development, product development, process development and testing. The Technical Rubber Systems branch of the company is one of the leaders in the manufacture and sale of rubber compounds and sheeting. It is able to develop products for specific customer requirements. These technologies do not focus exclusively on the automotive industry. In August 2006, MAPS signed a long term contract with The Boeing Company to supply Non-Textile Floor coverings (NTF) for Boeing 787 aircraft.
The rubber compounds are used in several other industries, from semi-finished products for the pharmaceutical industry to lining sheets for drinking water tanks. Ermanno Fugazza, Managing Director of Metzeler Automotive Profile Systems (MAPS) in Italy, spoke to Automotive Industries.
AI: What is Metzeler’s presence in the increasingly global automotive marketplace?
Fugazza: MAPS specializes in the design and manufacture of automotive sealing systems for doors, windows, boots and hoods. It employs more than 8,000 people and has 30 plants worldwide, from America to Europe, as well as five joint ventures in Asia. Metzeler is a European leader and major world player.
AI: How do you ensure efficiency of different applications of your sealing systems in terms of closure effort, running and water retention, as well as acoustic performance?
Fugazza: The company places high emphasis on research and development. The Group’s Technical Centers in Tennessee and Germany work on new materials, processes and products, maintaining continuous improvement across the product range. MAPS has built up country-based Engineering Application Centers to design sealing systems for new cars using the output and support of the Technical Centers. Complex production processes can be simulated and optimized on real production lines in MAPS process development centre in Tennessee. The European Technology Centre has a full range of facilities. Technical challenges faced by the research and development team are acoustics and aesthetics. We do extensive research into developing solutions for squeak and noise problems, seeking to eliminate noises between glass and sealing. The R&D team tests different kinds of coating to maximize the pleasure of touching the profiles. Safety is also researched with a focus on creating substances that permit efficient sealing but won’t trap and injure users if body parts such as fingers become caught by closing doors and windows.
AI: How do you transfer and implement process know-how and production technology between different markets?
Fugazza: The sealing systems are normally developed in Europe or North America and the transfer in China and India is based on the following: the same or equivalent process installed in the Emerging Markets Division; joint teams for the industrialization of products using the same specifications and quality level; to supply the tooling or the design to be adjusted and bought locally; training in Europe of the Emerging Markets unit technicians, and also operators if necessary; and local technical assistance to the units and the customers for the start-up. These processes have been used for the introduction of the Renault Logan in India and Iran as well as for the VW Touran, Polo and Passat in China. MAPS is currently working together with teams in Italy and India, where the same process will be used on the new Tata vehicles.
AI: Describe your partnership with Fiat.
Fugazza: There is a long time tradition of partnership with Fiat, with continuous success in all the new car launches. The basis of the partnership is the capacity to satisfactorily cover Fiat requirements. The latest example is the successful Bravo, developed in only 17 months with a strong international work in co-design with Fiat and Magna. MAPS’ Italian output also services other Italian automakers including Alfa Romeo, Lancia, Pininfarina, Bertone, Ferrari, Maserati, Iveco and Piaggio.
AI: What were your biggest obstacles in the past 12 months?
Fugazza: The raw material price increase was the most difficult issue we faced in terms of trying to balance efficiency to the customer and profitability of the company. Another issue was the concurrent launches of many new cars.
AI: What are the benefits that your project management brings to the OEMs?
Fugazza: The possibility to take advantage of the global benchmark owned by MAPS and the integrated international approach of the Application Centers. This process allows customers to benefit from the technical solutions as well as the cost reduction to capitalize the updated and advanced solutions.
AI: What new technologies will have the biggest impact on the market?
Fugazza: Aesthetics is one of the most popular requests received by customers. The use of bright versions of metal, new rubber gloss surfaces, and new varnish will be extended to medium and low segment cars.
AI: How do you see the future of your company?
Fugazza: The automotive market is quickly changing, particularly regarding the consolidation of the industry. This opens possibilities for merging and take-overs. Thus the market position, the competitiveness of the company and the strong partnership with the customers play an important role. We consider ourselves in a leading and good position to counter-face the changes and the challenges of the market.
More Stories
What You Should Know Before Filing a Car Accident Claim
Injured in a Car Accident in St. Louis? Here’s What to Do Next
Historic Sportscar Racing (HSR) and Goodyear Announce Multi-Year Partnership