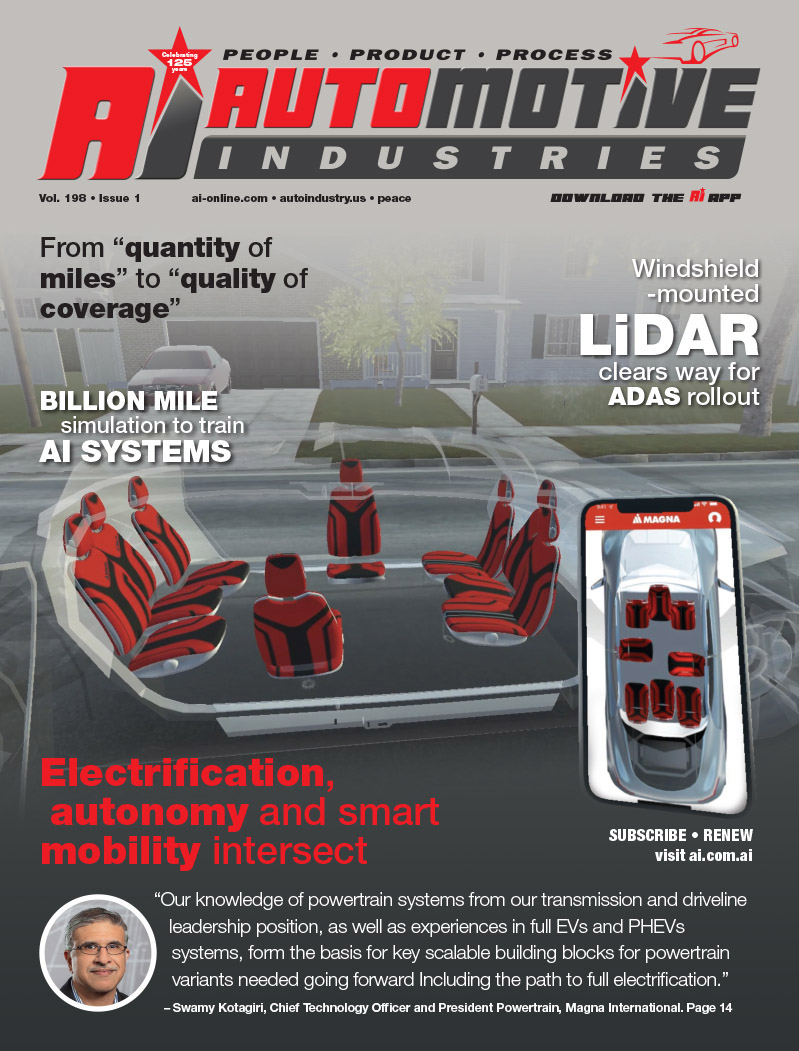
A mid sized car costs about $3000 to produce, total production time (in Asia) of 24 hours.
Doesn´t that just blow your mind? Think of the humongous number of cars produced annually, think of the millions of people working to make them, think of the amount of effort invested in this industry in just about every corner of our planet.
Now add to the equation words like Just-In-Time and Lean Manufacturing, Cost reduction and Warranty costs; in order to make things a bit more spicy, add a crazy pace of progress – ABS, Air bags, ESP, Crash management…and the humanly ever-want-more nature that puts a legendary 25 year old Ferrari GTO far behind my baby sister´s new Golf.
What you get is an acute and perpetual need to stretch the limits and find ways to do the impossible; we want things better, safer, stronger and at the same time – cheaper, more reliable and service free.
In many cases, technology simply gives up, saying “that’s it! You can´t squeeze any more out of me”, you simply cannot make the product lighter, still answering the structural and safety requirements. These ever so often cases are junctions with two main optional directions – one is to fire the development team and let the production run as is for the next ten years, the other is to break the mold, create a new way/product/process by changing the rules;
Revolution is a word I do not like, it smells of dead leaders and burned parliaments – CHANGE however is a wonderful word. You usually find change helpful to a single problem or maybe two, but if you are fortunate enough – you come across a change that facilitates a bundle of parameters – a LEAP…Let´s use electricity to light our homes and streets instead of gas – Man, this is something!
Pulsar is the leading force in the niche of metal joining by the use of electro magnetic pulse, the technology is well known and established – it is based on Solid State Cold Welding and was not invented by Pulsar. Remember fuel injection was a thing of Formula 1 cars and how nowadays you cannot find a car without it? Well, at very much the same level, Pulsar has perfected the process of Solid State Cold Welding to a level such that it can be done with an affordable, small footprint machine, operated by every floor shop worker and serviced by the plant´s maintenance guy.
The principle of Solid State Cold Welding is based on the fact that the internal structure of metals is such that enables joining at the atomic level when certain process parameters are achieved (for elaborated explanations about the technology, please refer to http://www.pulsar.co.il/FileServer/fbabdc01393bc241f6c05f2aa8d0c011.pdf ). In lay terms, if you put two atoms of metal close enough and force them together to overcome the natural repelling force they apply to one another – they will start sharing an electron and be combined forever – didn´t they say love is very similar to hate?
This procedure is being operated for years in a process called Explosive Welding which is basically utilizing explosives to accelerate one piece of metal towards a second one, thus forcing them to collide. When the right parameters are achieved, geometry, velocity and pressure, the effect is perfect welding (one might call it fusion) of the two pieces and is used to produce, for examples, large plates for the construction of marine vessels. The uniqueness of Solid State Cold Welding is the lack of use of heat (in Explosive Welding, the explosion is far from the welding area, used only for accelerating the piece) – this avoids the so many problems you usually encounter when using traditional, heat based, welding technologies.
Most traditional welding techniques are very straightforward – you simply apply a lot of energy to two pieces of metal placed side by side, causing them to melt. The melted portions of the two pieces are getting “mixed” and then cooled down together – creating, in fact, one piece. There is only one “small” problem – heat distorts metal, so the welded area is dramatically weaker, corrosion sensitive and deformed. Not only that but you also end up inducing a lot of the energy and products of the process into the environment – heat, radiation, smoke, gas and sparks. Many of the more advanced techniques are trying to minimize these effects, usually by making the heat source more focused, as in laser, but minimizing just leaves you with a lesser effect – you do not eliminate the problem.
Solid State Cold Welding offers one extreme advantage that traditional methods can never achieve, due to being a cold process; it can weld dissimilar metals, Aluminum to Stainless Steel, Copper to Aluminum, many combinations have been successfully welded to date. This capability opens new horizons for engineers – imagine a driveshaft made of an aluminum tube, welded to steel yokes – the welding process is fast as lightning, the end product is 2Kg lighter, perfectly balanced and does not require any cleaning, straightening or dynamic balancing.
If there is a heaven for Engineers – this is the way of getting there.
Pulsar has invested over 100 man-years in the development and perfection of the same process, only using another, friendlier, source of energy for generating the acceleration – we use electromagnetic fields. In order to generate the same level of acceleration as in explosive welding, Pulsar´s equipment discharges a large amount of electricity through a unique set of conductive elements and into an electrode, a coil. This specially designed coil is constructed of a proprietary material to produce the maximum possible magnetic field out of any given current. Pulsar´s IP extends all across the process and equipment with a focused set of targets – manufacturability, repeatability, reliability, efficiency, cost and production rates. Pulsar´s equipment can pulse every 4 seconds (if your feeding system can handle such pace…) and can keep doing it 50,000 cycles with a single coil. The cost of a weld is primarily derived from the coil´s cost and is 20 to 40% lower than any conventional welding method.
In commercial production, Magnetic Pulse Welding (MPW) has numerous applications where quantities are large; all are tubular forms varying from 6mm to 150mm in diameter. HVAC (Heating, Ventilating and Air Conditioning) is one segment of automotive that considerably benefits from MPW. In most cases material is being saved due to the reduction in wall thickness (not necessary any more because there is no heat to absorb in the welding process) and furthermore, the repeatability of the process reduces the cost of quality inspection. Taking Before and After pictures of a production line, one will notice dramatic changes after the integration of an MPW unit –
• The degreasing (cleaning before welding) unit is absent – no need for it now since MPW is much less sensitive.
• The Welding unit is producing 5 or 6 units a minute (manual mode) instead of 2 or less a minute as before.
• There is no special screen to shield from radiation.
• The ventilation shaft is missing – no smoke here.
• The worker is not wearing shields or protection gloves – he is putting the parts in and out of the MPW unit with bare hands.
• If you look at his pocket, you won´t find a special certificate for being specially trained to operate welding equipment – you might find a smaller paycheck (to his regret).
• There is no cooling station after the welding unit and the post welding cleaning station is gone.
• The testing unit is working at a faster pace and there are no parts for rework in a box next to it.
• In fact, the rework station is gone and nowhere to be found, you might find two bad parts after a shift of producing 1500 because the operator misplaced a component.
But the big change is at the headquarters where budget allocations for warranty costs are lower and the fast ROI of the capital equipment is 10 months instead of the regular 16. The reduction of peripheral costs of the line is apparent, less scrap; lower cost of components – this summarizes the great benefit of MPW –
You produce higher quality of products at a lower cost!
In some cases, MPW completely replaces other techniques such as brazing and sealing of canisters by replacing a hemming or rolling unit; Pulsar´s state of the art equipment can also be used for crimping and forming. Unlike any other mechanical crimping, Magnetic Pulse Crimping (MPC) applies the force in perfect 360 degrees uniformity, in a split second and ultra precision. Many applications benefit from MPC – crimping cable lugs by MPC for example will cause a marginal welding and 100% compression of the cable. Manufacturers using MPC for this application indicate that products show 40% increase in mechanical strength and conductivity as well as better resistance to corrosion and heat shock.
It is important to remember – MP based technology is a non-contact technique with the ability of applying enormous pressure with extreme accuracy and repeatability. Forming is performed by a single side die, crimping elements have no moving parts, break the mold, change the rules – remember?
Pulsar´s process is different, it is a leap from the regular technologies to another domain, a domain where things that were not possible before are made possible – a domain were structural elements can be constructed from different materials, utilizing the best of Steel and the best of Aluminum in the same organic element, a domain where the weak point in a sealed container is not the weld, but the tube itself.
Welcome to the future.
May the pulse be with us
A mid sized car costs about $3000 to produce, total production time (in Asia) of 24 hours.
Doesn´t that just blow your mind? Think of the humongous number of cars produced annually, think of the millions of people working to make them, think of the amount of effort invested in this industry in just about every corner of our planet.
Now add to the equation words like Just-In-Time and Lean Manufacturing, Cost reduction and Warranty costs; in order to make things a bit more spicy, add a crazy pace of progress – ABS, Air bags, ESP, Crash management…and the humanly ever-want-more nature that puts a legendary 25 year old Ferrari GTO far behind my baby sister´s new Golf.
What you get is an acute and perpetual need to stretch the limits and find ways to do the impossible; we want things better, safer, stronger and at the same time – cheaper, more reliable and service free.
In many cases, technology simply gives up, saying “that’s it! You can´t squeeze any more out of me”, you simply cannot make the product lighter, still answering the structural and safety requirements. These ever so often cases are junctions with two main optional directions – one is to fire the development team and let the production run as is for the next ten years, the other is to break the mold, create a new way/product/process by changing the rules;
Revolution is a word I do not like, it smells of dead leaders and burned parliaments – CHANGE however is a wonderful word. You usually find change helpful to a single problem or maybe two, but if you are fortunate enough – you come across a change that facilitates a bundle of parameters – a LEAP…Let´s use electricity to light our homes and streets instead of gas – Man, this is something!
Pulsar is the leading force in the niche of metal joining by the use of electro magnetic pulse, the technology is well known and established – it is based on Solid State Cold Welding and was not invented by Pulsar. Remember fuel injection was a thing of Formula 1 cars and how nowadays you cannot find a car without it? Well, at very much the same level, Pulsar has perfected the process of Solid State Cold Welding to a level such that it can be done with an affordable, small footprint machine, operated by every floor shop worker and serviced by the plant´s maintenance guy.
The principle of Solid State Cold Welding is based on the fact that the internal structure of metals is such that enables joining at the atomic level when certain process parameters are achieved (for elaborated explanations about the technology, please refer to http://www.pulsar.co.il/FileServer/fbabdc01393bc241f6c05f2aa8d0c011.pdf ). In lay terms, if you put two atoms of metal close enough and force them together to overcome the natural repelling force they apply to one another – they will start sharing an electron and be combined forever – didn´t they say love is very similar to hate?
This procedure is being operated for years in a process called Explosive Welding which is basically utilizing explosives to accelerate one piece of metal towards a second one, thus forcing them to collide. When the right parameters are achieved, geometry, velocity and pressure, the effect is perfect welding (one might call it fusion) of the two pieces and is used to produce, for examples, large plates for the construction of marine vessels. The uniqueness of Solid State Cold Welding is the lack of use of heat (in Explosive Welding, the explosion is far from the welding area, used only for accelerating the piece) – this avoids the so many problems you usually encounter when using traditional, heat based, welding technologies.
Most traditional welding techniques are very straightforward – you simply apply a lot of energy to two pieces of metal placed side by side, causing them to melt. The melted portions of the two pieces are getting “mixed” and then cooled down together – creating, in fact, one piece. There is only one “small” problem – heat distorts metal, so the welded area is dramatically weaker, corrosion sensitive and deformed. Not only that but you also end up inducing a lot of the energy and products of the process into the environment – heat, radiation, smoke, gas and sparks. Many of the more advanced techniques are trying to minimize these effects, usually by making the heat source more focused, as in laser, but minimizing just leaves you with a lesser effect – you do not eliminate the problem.
Solid State Cold Welding offers one extreme advantage that traditional methods can never achieve, due to being a cold process; it can weld dissimilar metals, Aluminum to Stainless Steel, Copper to Aluminum, many combinations have been successfully welded to date. This capability opens new horizons for engineers – imagine a driveshaft made of an aluminum tube, welded to steel yokes – the welding process is fast as lightning, the end product is 2Kg lighter, perfectly balanced and does not require any cleaning, straightening or dynamic balancing.
If there is a heaven for Engineers – this is the way of getting there.
Pulsar has invested over 100 man-years in the development and perfection of the same process, only using another, friendlier, source of energy for generating the acceleration – we use electromagnetic fields. In order to generate the same level of acceleration as in explosive welding, Pulsar´s equipment discharges a large amount of electricity through a unique set of conductive elements and into an electrode, a coil. This specially designed coil is constructed of a proprietary material to produce the maximum possible magnetic field out of any given current. Pulsar´s IP extends all across the process and equipment with a focused set of targets – manufacturability, repeatability, reliability, efficiency, cost and production rates. Pulsar´s equipment can pulse every 4 seconds (if your feeding system can handle such pace…) and can keep doing it 50,000 cycles with a single coil. The cost of a weld is primarily derived from the coil´s cost and is 20 to 40% lower than any conventional welding method.
In commercial production, Magnetic Pulse Welding (MPW) has numerous applications where quantities are large; all are tubular forms varying from 6mm to 150mm in diameter. HVAC (Heating, Ventilating and Air Conditioning) is one segment of automotive that considerably benefits from MPW. In most cases material is being saved due to the reduction in wall thickness (not necessary any more because there is no heat to absorb in the welding process) and furthermore, the repeatability of the process reduces the cost of quality inspection. Taking Before and After pictures of a production line, one will notice dramatic changes after the integration of an MPW unit –
• The degreasing (cleaning before welding) unit is absent – no need for it now since MPW is much less sensitive.
• The Welding unit is producing 5 or 6 units a minute (manual mode) instead of 2 or less a minute as before.
• There is no special screen to shield from radiation.
• The ventilation shaft is missing – no smoke here.
• The worker is not wearing shields or protection gloves – he is putting the parts in and out of the MPW unit with bare hands.
• If you look at his pocket, you won´t find a special certificate for being specially trained to operate welding equipment – you might find a smaller paycheck (to his regret).
• There is no cooling station after the welding unit and the post welding cleaning station is gone.
• The testing unit is working at a faster pace and there are no parts for rework in a box next to it.
• In fact, the rework station is gone and nowhere to be found, you might find two bad parts after a shift of producing 1500 because the operator misplaced a component.
But the big change is at the headquarters where budget allocations for warranty costs are lower and the fast ROI of the capital equipment is 10 months instead of the regular 16. The reduction of peripheral costs of the line is apparent, less scrap; lower cost of components – this summarizes the great benefit of MPW –
You produce higher quality of products at a lower cost!
In some cases, MPW completely replaces other techniques such as brazing and sealing of canisters by replacing a hemming or rolling unit; Pulsar´s state of the art equipment can also be used for crimping and forming. Unlike any other mechanical crimping, Magnetic Pulse Crimping (MPC) applies the force in perfect 360 degrees uniformity, in a split second and ultra precision. Many applications benefit from MPC – crimping cable lugs by MPC for example will cause a marginal welding and 100% compression of the cable. Manufacturers using MPC for this application indicate that products show 40% increase in mechanical strength and conductivity as well as better resistance to corrosion and heat shock.
It is important to remember – MP based technology is a non-contact technique with the ability of applying enormous pressure with extreme accuracy and repeatability. Forming is performed by a single side die, crimping elements have no moving parts, break the mold, change the rules – remember?
Pulsar´s process is different, it is a leap from the regular technologies to another domain, a domain where things that were not possible before are made possible – a domain were structural elements can be constructed from different materials, utilizing the best of Steel and the best of Aluminum in the same organic element, a domain where the weak point in a sealed container is not the weld, but the tube itself.
Welcome to the future.
May the pulse be with us
More Stories
Venti Technologies Wins Multiple Pinnacle Awards for Innovation and Achievement in Technology
Launch of AltaScient.ai: New horizons for Risk and Sustainability Analytics
Expert Tips on Detailing a Car