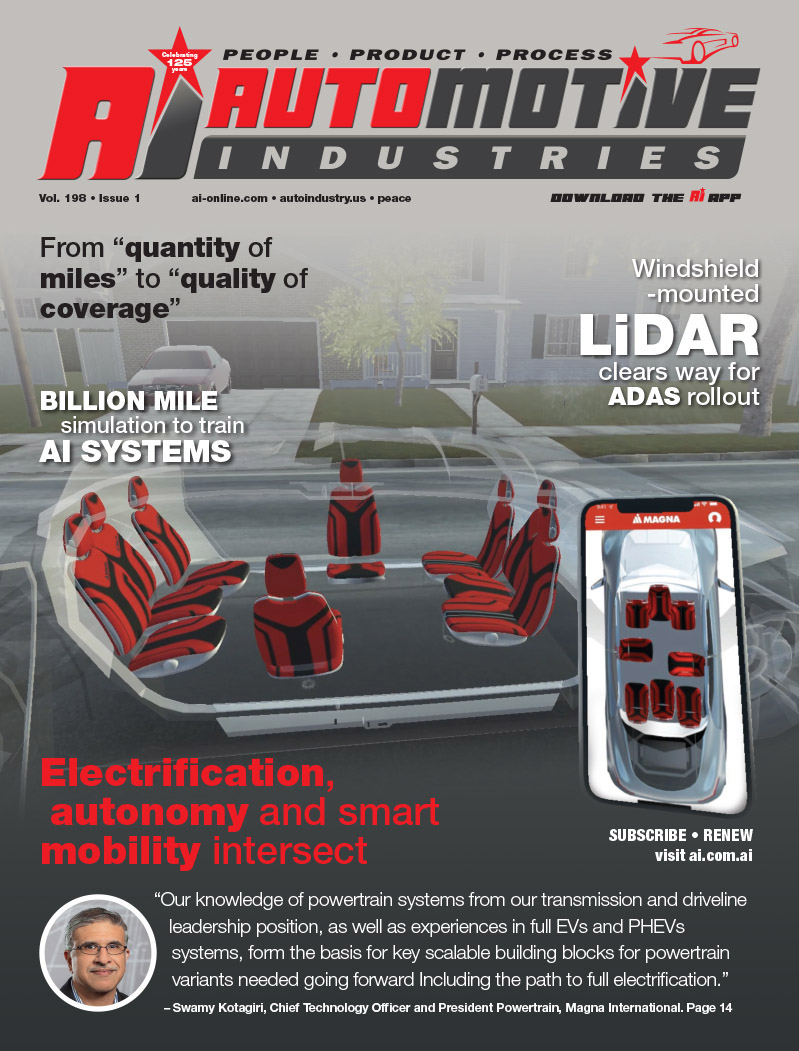
The 10-year old Gomecsys BV, is best known for its GoEngine, which offers 30 to 50 per cent reduction in fuel consumption and CO2 emissions without compromising power output. The Netherlands-head quartered company has invented and patented both a 4 in-line and a 2 in-line variants of the GoEngine.
The GoEngine’s fuel efficiency comes from the fact that it uses a specific piston movement every 720 crankshaft degrees. This optimizes the movements for all four engine strokes. A normal engine has a piston movement that is the same and repeating every 360 crankshaft degrees and cannot be modified in any way. Also the compression ratio of normal engines is not variable.
“With the GoEngine we have put an eccentric between the crankpin and the big end of each conrod. This eccentric is driven in a specific path by a gear. With the crank in bdc position (bottom dead center) the eccentric will be on the lower side of the crankpin giving an increased expansion stroke or on the higher side of the crankpin giving a reduced intake stroke. With the crank in tdc position (top dead center) the eccentric will be on the right or left of the crankpin resulting in the tdc position for the piston on tdc firing and tdc gas exchange. The increased expansion stroke makes that 5 to 10% more force and thus energy is put in the piston adding torque to the crankshaft. This results in a 5 to 10% higher engine efficiency. An additional advantage is that exhaust temperatures will be around 100 degrees C less,†says the company.
Another feature of the GoEngine is its variable compression ratio or VCR technology which is also related to the piston movement within one engine cycle over 720 degrees. Unlike normal engines where the efficiency reduces along with the load, the GoEngine is still efficient at lower loads. “The GoEngine with its fully variable compression ratio can however achieve extreme downsizing without compromising CR and thus engine efficiency. In this way the best of both worlds can be achieved, on one side running low loads at very high CR and running very high boost pressure (up to 3 bar) with low CR at high and full load. Extreme downsizing can be realized in an effective way using VCR technology and can reduce fuel consumption up to 30 per cent,†says Gomecsys.
Another unique feature of the GoEngine is that it is the only engine that does not need valve pockets because of the lowered tdc gas exchange at high compression ratio. The piston crown design makes for the optimum combustion because it does not have to be compromised by valve pockets. Usually, engines have camphasers to adjust the camtiming of the intake- and exhaust valves. To accommodate different camtiming strategies valve pockets are created on the piston crown so the valves have freedom to move when the piston is in tdc gasexhange.
Gomecsys initially developed a new type of rotary engine when it was founded in 1997. The next year saw the GoEngine being invented and since then, this engine became the core focus of the company.
Automotive Industries spoke to Bert de Gooijer, technical director at Gomecsys BV.
AI: How far is Gomecsys with the development of the GoEngine demonstrator engines?
The last 3 years we have invested a lot in the development of the demonstrator engines. The 2 inline engine is ready for demonstrations in a KIA Picanto and shows a fuel reduction of 40%. The 4 inline engine is still in development on the dyno. Although we already have good part load efficiency results of the current prototypes we have been going through an important development phase this year. The new system still has the same functionality as the current engines but it has 4 important advantages, 1) the friction level will be even better because the eccentric bearings and the gears run at half the crankshaft speed instead of 1,5 times, this is a reduction of 66%. 2) Longer piston strokes are possible within the same inner block space. 3) The activation of the VCR system is really simple and effective. 4) Modification of any block to suite the GoEngine cranktrain is reduced to a minimum, because the ringgears are no longer carried by the block.
We have just signed off new development projects for a new 2 and 4 inline engine which will be equipped with the latest state of the technology. These engines have to run in January 2008, and will be showed in demonstrator cars (the 4 inline in a new Mercedes C200) at the Engine Expo in Stuttgart.
AI: Is the GoEngine VCR system also useful for diesel engines.
We are looking into this at the moment; it seems that there is some interest to change the compression ratio on diesel engines. The driver is not fuel efficiency but more NOx emissions. Diesel engines run with lower CR then ever before to reduce NOx levels but you cannot go to low because at a certain level they just won’t start anymore. Because of the much higher combustion peak pressures of diesel engines we will have to run the GoEngine technology for diesel engines with smaller eccentrics to reduce gear load to the same level as on the gasoline engines. This is not a big problem because the CR values still can be varied between 12 and 20.
AI: Why is HCCI considered the Holy Grail by the car makers for the petrol engine?
HCCI has important advantages on both fuel efficiency and NOx emissions. However HCCI needs superfine control of end of compression temperatures. With variable compression ratio you can realise a first stage of control to approach close to where you need to be. The superfine control can then be realised by internal EGR. Here is where the GoEngine shows a big advantage because there is an automatic internal EGR percentage at part load, which can be fine-tuned by variable valve timing per cylinder.
The lowered piston tdc at gas exchange makes it possible to use extreme valve strategies without the need of big valve pockets.
AI: Please tell us a little about the modelling for fuel optimal control of a variable compression ratio.
We run our prototype engines with just one fuel/ignition map; compression ratio is a function of the map as is the camtiming and others. Every point in the map has an optimum CR somewhere between 8 and 16, there is an offset for different fuel qualities which can be controlled by the knock strategy. In general the VCR control is comparable with normal camtiming control; we also use a camphaser type actuator on our new system.
AI: How unique is the GoEngine’s VCR technology with a true 720 degree cycle?
To our knowledge it is unique on the world. We have seen a lot of different piston movements over one crank revolution of 360 degrees but not over 720 degrees, and the 4 stroke engine is all about a 720 degrees cycle.
The overexpansion is a very important feature that increases work delivered to the pistons. In combination with late intake closing we can even run expansion ratios as high as 20.
AI: Which automotive companies have evinced an interest in the GoEngine?
We are in contact with several major car/engine manufacturers worldwide, we will deliver demo engines for 2 and 4 inline engines next year based on original oems engines.
It’s good to see that after 10 years of developing we are at a point that we can offer oems a serious system that works in theory and in practice.
AI: Why did you develop a 2 inline engine?
When you look into extreme downsizing then the 2 inline is the logic way to go. It replaces small 4 inline engines like a 1 liter 4 inline. A small 4 inline is just inefficient and expensive; you won’t develop a 2 liter V8 for the same reason.
It’s not for nothing that Fiat is coming back with a 2 inline turbo engine; it’s a win-win concept. Less moving parts, less weight, less space, bigger cylinders thus more efficient, and without increased production cost. 2 inline boosted engines can replace 4 inlines up to 100 bhp. In addition to this a VCR system works best on an (extreme) downsized engine. The 2 inline GoEngine concept matches perfect with a 2 inline engine. This saves fuel as much as 40% compared to 4 inline engines with the same power output and without a cost penalty for both manufacturer and buyer. And you don’t need batteries etc. This is a solution that can really help to reduce CO2 emissions on a global scale tomorrow, it’s available and simple.
More Stories
How Modern Power Management Enhances Connected Fleet Tech
Automotive Industries interviews Bahar Sadeghi, Technical Director, Car Connectivity Consortium (CCC)
Avery Dennison PSA tapes support rapid evolution of EV batteries