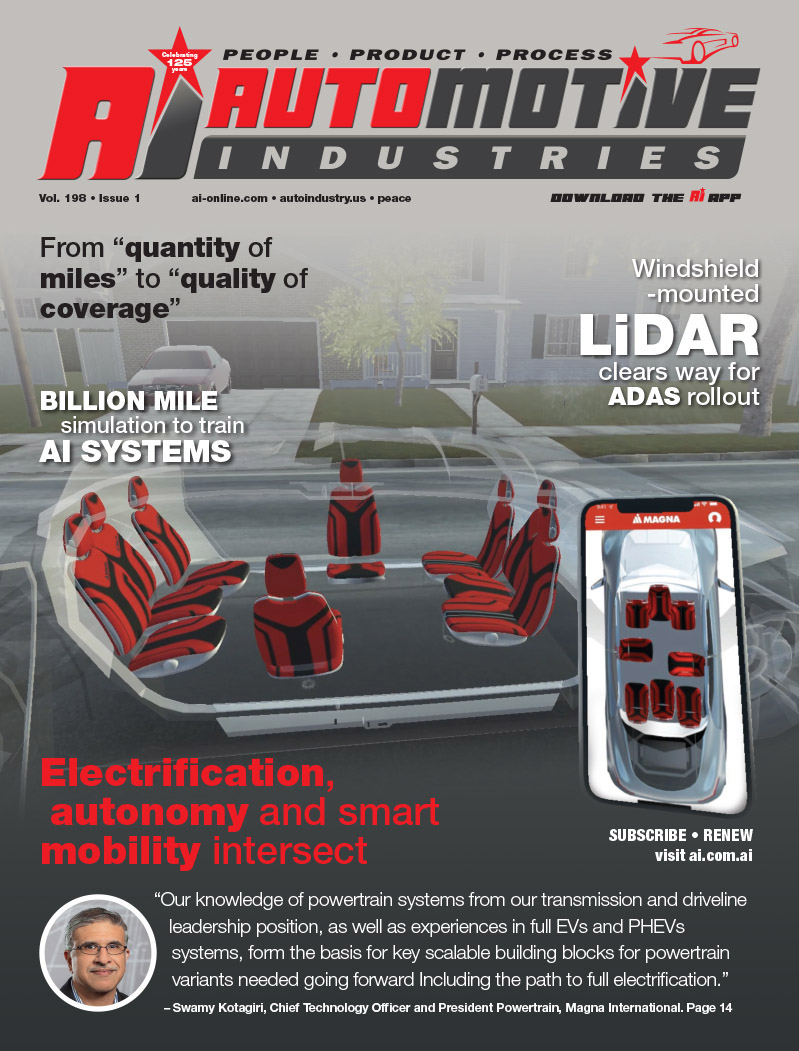
Invensys Process Systems (IPS), a global technology and consulting firm, today unveiled its Immersive Virtual Reality Process technology, a next-generation human machine interface (HMI) solution that will revolutionize the way engineers and operator trainees see and interact with the plant and the processes they control.
When it becomes commercially available later this year, IPS expects Immersive Virtual Reality Process to deliver a wide range of client benefits that will help improve plant safety and security, ensure environmental and regulatory accountability, and increase production and efficiency while controlling feedstock and material costs. Energy, chemical, oil and gas, and other vital process industries will also be able to apply the technology to meet the knowledge-management, training and retention challenges they encounter in the face of an aging and dwindling industry workforce.
IPS’ Immersive Virtual Reality Process can create a three-dimensional computer-generated representation of either a real or proposed process plant. Via a stereoscopic headset, users enter a totally immersive environment in which they can move through the plant in any direction. Such freedom is made possible because the virtual environment is rendered at 60 frames per second, significantly faster than what can be achieved by traditional, non real-time rendering.
“The ability to simulate complex processes in connection with virtual actions allows the user to directly experience an environment that changes over time, making it more effective at transferring skills learned in training to the work environment,” said Maurizio Rovaglio, director, IPS global consulting. “And because rarely performed volatile tasks such as plant shutdowns can be rehearsed in a stable, realistic environment, users and operator trainees have the opportunity to learn and make mistakes without putting themselves, the community or the environment at risk. In addition to that, using computer models of real equipment allows endless experimentation without ever taking the equipment off line, mitigating risk to production as well.”
IPS will make Immersive Virtual Reality Process truly realistic by applying its proprietary DYNSIM(TM) software to emulate the plant environment, linking process simulation models with physical-spatial models to create virtually any scenario that a user could encounter in real life. The inherent flexibility of IPS’ technology results in fast and economical program configuration.
The company’s new solution has been designed for a wide range of scenarios, including process design, maintenance engineering and plant safety, and IPS expects Immersive Virtual Reality Process to be widely used in the next generation of process training programs.
“Immersive Virtual Reality Process is another example of IPS developing and delivering innovative solutions that help our clients solve their most critical business issues,” said Tobias Scheele, IPS vice president of advanced applications. “The solution continues to be tested in a variety of installations, and we are beginning to realize its full potential and value-add possibilities. When it becomes available in the second half of this year, we believe it will provide immediate, far-reaching benefits to clients spanning the process industries.”
For more information and to see a video demonstration of Immersive Virtual Reality Process, please visit www.ips.virtual-plant.com
About IPS (Invensys Process Systems)
Invensys Process Systems (IPS), headquartered in Plano, Texas, is a global technology, software and consulting firm leading significant change in process manufacturing, plant optimization, business operations and enterprise performance. IPS clients are some of the world’s most important industrial organizations — companies that operate large oil refineries; plants that process chemicals, gas, LNG, power, pharmaceutical and minerals; and pulp and paper mills. IPS solutions, used at over 50,000 locations around the globe, include field devices and controls from Foxboro and Triconex, advanced applications from SimSci-Esscor, operations management from Avantis, and the world’s first truly open enterprise control system, InFusion(TM).
More Stories
Sonatus – The industry is shifting gears to software
Cybord warns of dangers of the stability illusion
HERE building trust in ADAS systems