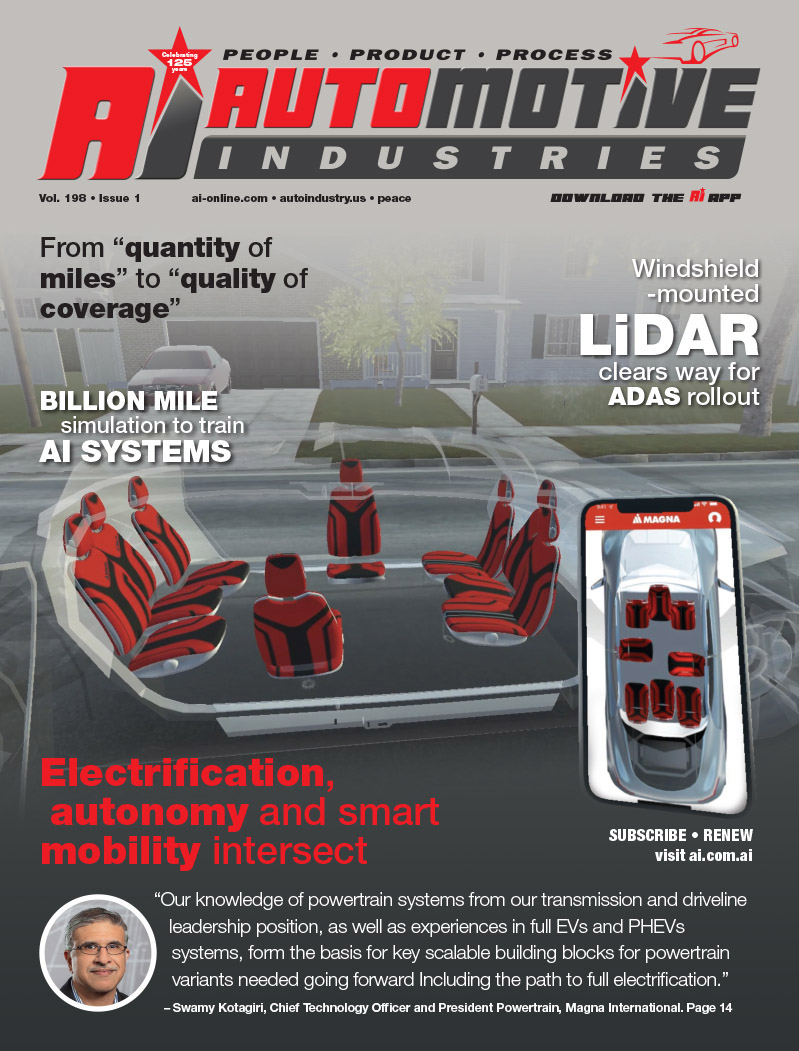
At 14:46 JST, Friday 11th March 2011, the Tohoku earthquake – the most powerful to have hit Japan – created a 33 ft wave that swept inland for up to six miles causing harrowing scenes of suffering and destruction. Datamonitor’s automotive industry analyst, Andrew Jackson, reflects on the impact and implications for the global automotive sector:
All Japanese manufacturers suffered some form of disruption with the worst hit being Honda, Toyota and Nissan. The effects have been felt world-wide. Current estimates indicate that, globally, the industry will produce three million vehicles less than expected in 2011, with Japan 1.1 million units behind target as of June. Japanese automakers have seen their production drop 30% globally as they struggle to restore manufacturing and supply systems. Current estimates suggest that the likes of Toyota will not be fully operational until the fourth quarter.
This, of course, is not the full story. Tier one, two and three suppliers which rely on one another in order to assemble their components are also suffering. Generally speaking, the factories themselves were not badly damaged. However their manufacturing capabilities have been left crippled due to lack of electricity and water. Consignments have not moved due to the damage to the road and rail infrastructure.
As the automotive industry is a major proponent of just-in-time (JIT) manufacturing, the rest of the world had to rapidly deploy triage systems to avoid a supply-chain disaster. But how did a natural disaster in Asia affect vehicle manufacturers’ assembly, for example 9,000 miles away in Detroit? According to the Federal Reserve Bank of Chicago there are thousands of Tier 1, 2 and 3 suppliers within a few hours of the motor city, and the likes of Chrysler source less than 5% of its parts from Japan. The answer is: small high-value commodities such as electronics and electrical equipment.
Of the top 100 global parts suppliers in the automotive industry 30% of suppliers are based in Japan, versus 27% from the USA. While there is a relatively balanced spread of specialisations in the US, in Japan over 45% of the 30 companies listed in the top 100 have some form of involvement with electronic and electrical components. These components are, generally speaking, small and light enabling transcontinental delivery which fits with the JIT business model and this is how the impact has been felt further afield than the Land of the Rising Sun.
An example Renesas (the product of mergers between Hitachi, Mitsubishi and NEC). Based in Japan, it is responsible for approximately 40% of the world’s supply of micro control units, and was directly affected by the earthquake. Of course, Renesas has other plants, but the transfer of production to alternative plants with spare capacity takes time, and the potential shortfall will last for up to four months until demand is met.
So why not find another supplier and simply switch to a local chip manufacturer? Again, whilst some components may well be similar with other manufacturers, in the case of engine control units (ECUs) the software that the auto assembler uses for any particular vehicle will be bespoke, and therefore compatibility cannot be assured. Furthermore, for the Japanese manufacturers based in the USA, the knock-on affect of rolling power-cuts in Japan is causing a reduction in manufacturing of parts that would directly supply a sister plant in the US, and hence disrupting production in a domestic context even further.
So what can the industry learn from this tragedy and how can we expect the future supply chain to evolve? There are several key lessons that we can draw from the events of March 11th. Firstly, those manufacturers that effectively implemented a triage system were able to isolate critical components and either assist manufacturers in resuming production, locate alternative suppliers or make adjustments to their own production schedule in order to ensure production continued. For GM, it quickly identified 118 parts that were classified critical and by mid-May had secured stable supply for all but five. Furthermore, this disaster has forced a level of communication between different tiers which has rarely been seen before – and for the benefit of everyone involved should continue.
Undoubtedly, all vehicle manufacturers will look long and hard at their procurement, and one would expect a reduction in dependency to occur where possible, and at the very least a review of whether certain critical components are being supplied in the correct quantities, by the correct supplier and at the correct intervals.
The location of manufacturing for Japanese assemblers may also change. Toyota has gone on record as saying that they will speed up their plans to locate more manufacturing “offshore”, whilst the recent decision of Nissan to invest in the United Kingdom for the design and production of the next generation Qashqai will have been made very easy due to the reduction in Japanese dependency that it will bring.
Ultimately, the earthquake and tsunami the Japanese people have had to endure is a global tragedy and no good can ever come from such a loss of life. However, the automotive industry can learn from these events, it can develop new crisis plans based on this experience and it can recover to be a stronger, more organised entity that will be poised to weather such and event when it happens again.
Which it will.
About Andrew Jackson
With a research background spanning seven years, Andrew has worked in the scientific, chemical and automotive research sectors.
Andrew has significant industry knowledge and has an understanding of the automotive sector from all aspects, including the business, engineering and consumer perspectives. He holds a master’s degree in chemistry and a doctorate in materials chemistry.
More Stories
Buying Car Insurance in Toronto? Don’t Make These Rookie Mistakes
Extend Your Range, Maximize Your Storage with FRDM’s 45 Gallon Combo
How to Install a Ford Bumper Yourself (Step-by-Step Guide)