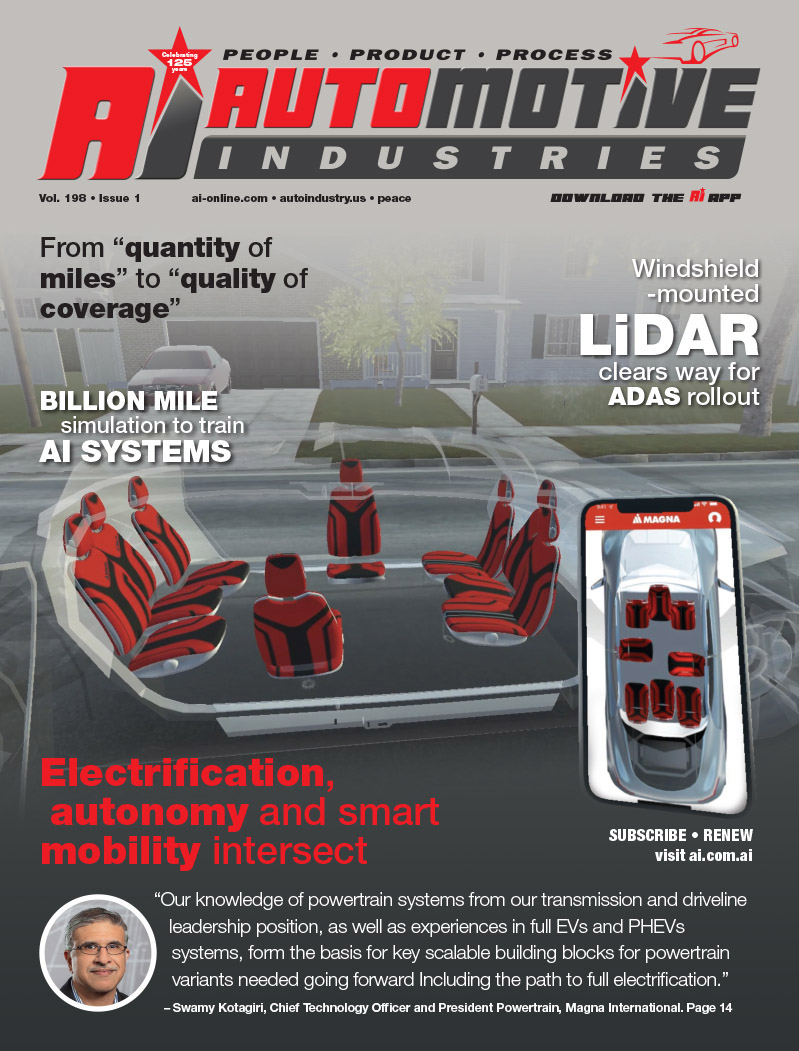
In recent years, the demand for hybrid-electric and fully electric vehicles has increased enormously. The development of such vehicles is a significantly more complex task than designing conventional cars because they incorporate many different engineering domains into a single system. At the same time, competitive pressures are forcing auto manufacturers to come up with new designs faster than ever before. The industry is turning to math-based physical modeling techniques which allow engineers to accurately describe the behavior of the components that comprise the system and the physical constraints on the system. These model equations are then used to develop, test, and refine designs very quickly, and without the expense and time required to build physical prototypes.
The system equations for this multi-domain model of a hybrid-electric vehicle are generated automatically by MapleSim, and are accessible to the researchers for analysis and improvements to the design.
One of the most important components of a hybrid-electric or fully electric vehicle is the battery itself. Having a good virtual model of the battery is essential so that both battery behavior and the physical interaction of the battery with all the other components are properly reflected in the model. Because the battery plays such a vital role in the vehicle, capturing these interactions is essential to designing an efficient, effective electric vehicle.
Dr. Thanh-Son Dao and Mr. Aden Seaman are working with Dr. John McPhee, the NSERC/Toyota/Maplesoft Industrial Research Chair for Mathematics-based Modeling and Design, to develop high-fidelity models of hybrid-electric and electric vehicles, including the batteries. They chose MapleSim, multi-domain physical modeling and simulation software from Maplesoft, because they have found the symbolic approach in MapleSim to be an effective way to develop simulation models that have fast real-time speeds for hardware in the loop (HIL) testing and very high fidelity compared to models created in conventional modeling tools.
Battery Electric Vehicle (BEV) Model
Lithium-ion batteries are a good choice for electric vehicles, as they are light and provide more power than other common types of batteries of the same size and weight. Batteries in vehicles are subject to periods of high current draw and recharge and large temperature variations, which can have a significant effect on the performance and lifespan of the batteries. To capture these effects, Dr McPhee and Mr. Seaman needed a model of lithium-ion battery chemistry over a wide state-of-charge range, widely varying currents, and various temperatures. Starting with the electric circuit battery model of Chen and Rincón-Mora, they implemented the components in MapleSim, using a custom function component to represent the nonlinear relationship between the state of charge and the electrical components. They modified the battery equations to simulate a battery pack that is composed of series and parallel combinations of single cells. Next, they developed a power controller model in order to connect the battery pack to a motor. They then incorporated a one-dimensional vehicle model into the model. The simple vehicle model drives on an inclined plane, which is in turn controlled by a terrain model.
A drive cycle model was included to control the desired speed of the vehicle. The resulting differential equations, generated by MapleSim, were simplified symbolically and then simulated numerically.
A variety of driving conditions were simulated, such as hard and gentle acceleration and driving up and down hills. The results were physically consistent and clearly demonstrated the tight coupling between the battery and the movement of the vehicle. This model will form the basis for a more comprehensive vehicle model, which will include a more sophisticated power controller and more complex motor, terrain, and drive-cycle models.
Hybrid-Electric Vehicle (HEV) Model
Dr. McPhee, Dr. Dao, and Mr. Seaman used MapleSim to develop a multi-domain model of a series HEV, including an automatically generated optimized set of governing equations. The HEV model consists of a mean-value internal combustion engine (ICE), DC motors driven by a chemistry-based NiMH battery pack, and a multibody vehicle model.
They chose a Ni-MH battery because of its widespread use in hybrid-electric vehicles. They used a chemistry-based modeling approach that captures the chemical and electrochemical processes inside the battery. With this modeling approach, they could modify the physical parameters of the battery as needed to meet their overall design requirements for the vehicle. They modeled the battery inside MapleSim by placing the governing equations of the battery processes directly inside MapleSim custom components.
MapleSim automatically generated an optimized set of governing equations for the entire HEV system, which combined mechanical, electrical, chemical, and hydraulic domains. Simulations were then used to demonstrate the performance of the developed HEV system. Simulation results showed that the model is viable and, as a result of MapleSim’s lossless symbolic techniques for automatically producing an optimal set of equations, the number of governing equations was significantly reduced, resulting in a computationally efficient system. This HEV model can be used for design, control, and prediction of vehicle handling performance under different driving scenarios. The model can also be used for sensitivity analysis, model reduction, and real-time applications such as hardware-in-the-loop (HIL) simulations.
“With the use of MapleSim, the development time of these models is significantly reduced, and the system representations are much closer to the physics of the actual systems,” said Dr. John McPhee. “We firmly believe that a math-based approach is the best and quite possibly the only feasible approach for tackling the design problems associated with complex systems such as electric and hybrid-electric vehicles.”
More Stories
Acoustic sensor systems and Fraunhofer measurement technology for in practical testing ͏
OSI Systems Receives $10 Million Order for Cargo and Vehicle Inspection Systems
Mitsubishi Electric Automotive America Launches Guardian Generation 3 Trial with Seeing Machines in North America