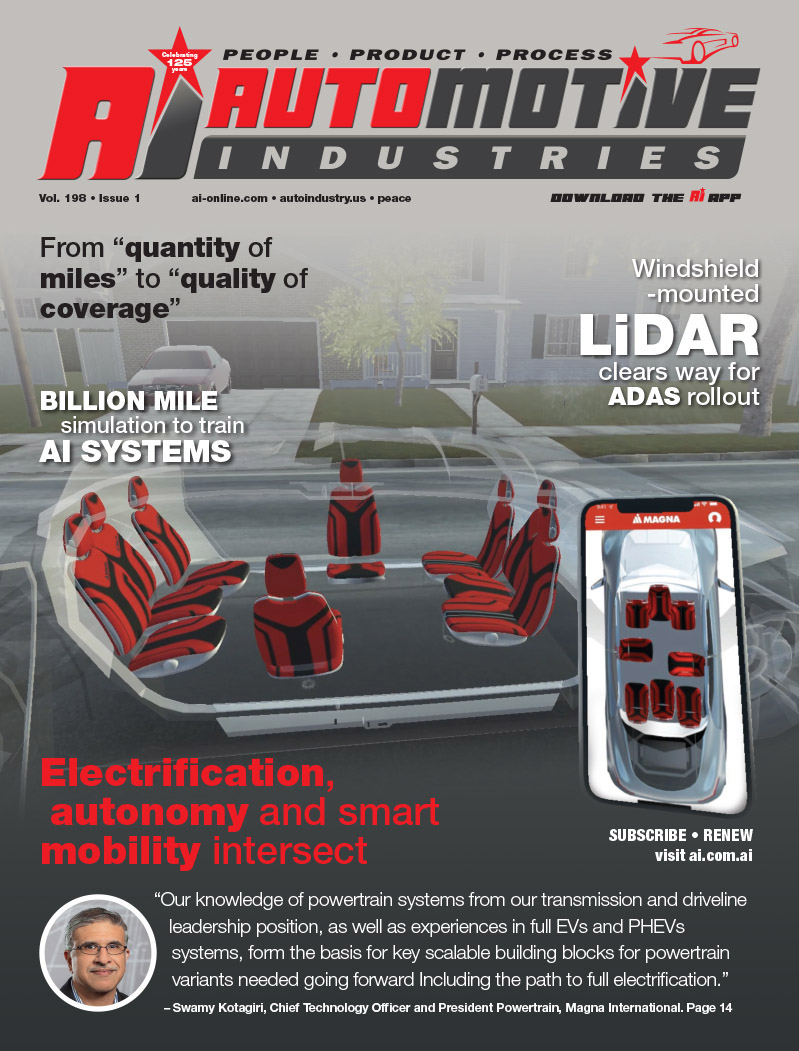
Safety, Performance and Reliability are the three attributes required of the battery pack in an automotive application. Battery management in automotive applications goes far beyond just managing the battery cells and keeping the pack healthy, it involves ensuring the safe operation of the pack, interfacing to the load and keeping the battery working under ideal conditions over its life time, according to Danish company LiTHIUM BALANCE.
The “brains†of the battery pack is the Battery Management System (BMS), which has to detect problems and notify the rest of the system. It does not manage the battery in isolation, but communicates with other systems such as motor controllers which provide information and give warnings, or by controlling other devices such as chargers.
Automotive Industries (AI) asked Lars Barkler, CEO of LiTHIUM BALANCE, how the company ensures that its BMS is robust enough to handle the harshest of conditions.
Barkler: With a lot of design and testing! There are two main culprits for hardware failures: vibration and electromagnetic interference (EMC). The BMS needs to withstand vibrations at all frequencies and in all directions. Any attached “legged†component such as a large capacitor or resistor becomes a potential point of failure in vibration. In addition, if the board flexes then it will peel off any surface-mounted components. Our s-BMS has always been made exclusively with surface mount components. We have tested them extensively on all three axes to ensure that a properly mounted board can withstand the expected vibration loading. On the EMC side, things are a lot trickier as you need to look at radiated noise as well as conducted noise sources and once noise gets through to the PCB you have no idea of the consequences. In short, you need to ensure that noise does not get onto the PCB.
AI: So how do you prevent this?
Barkler: A good example would be countering noise radiated directly to the PCB. We use six-layer PCBs, which means you have two copper planes shielding all of the traces on the board preventing the electromagnetic field from inducing any noise in the circuitry. We do other things as well such as adding low pass filters to all inputs on the BMS
AI: You have completed around 200 separate projects over the last four years, how have you managed this?
Barkler: We developed a multi-track approach to engineering support. There is a library of documentation which provides the majority of support. Those customers who need more can preorder a block of support hours, while those wanting customization and help in designing and procuring the complete system can purchase an engineering project from us. This has meant our engineers sometimes sleeping in the customer’s workshop. At other times all that is needed is to be at the other end of the phone to support the customer.
AI: What do you see as the key to survival in this business?
Barkler: We have survived due to a number of things, we are not dependent on any single industry and we have enough experience to spot “rational†projects, rather than the fun ideas and possibilities that Li-Ion technology opens up. Blue sky thinking does have its place, but we focus on helping our customers and developing solutions or technologies that there is an actual demand for.
AI: Going forward, do you believe there is a future for independent battery management suppliers?
Barkler: We believe that there is a future in what we do because our customer base grows year-on-year. There has been a revolution in electric propulsion systems over the last decade or so. Now all of the technologies such as motors, motor controllers, electrical steering pumps and good quality batteries are commodities that you can buy. This has lowered the entry barriers to the electrification of many applications, especially in mobility. So now it makes sound economic sense to run electric buses for town centre shuttle services rather than paying for expensive trams or light railway systems. Electric airport buses and even electric airplane tractors all make sense economically already, and the list just keeps getting longer. These specialist applications stay under the radar of the Tier 1 suppliers.
More Stories
Cybord warns of dangers of the stability illusion
Automotive Industries interviews Bahar Sadeghi, Technical Director, Car Connectivity Consortium (CCC)
Hexagon’s MAESTRO reinvents CMM systems through digitization