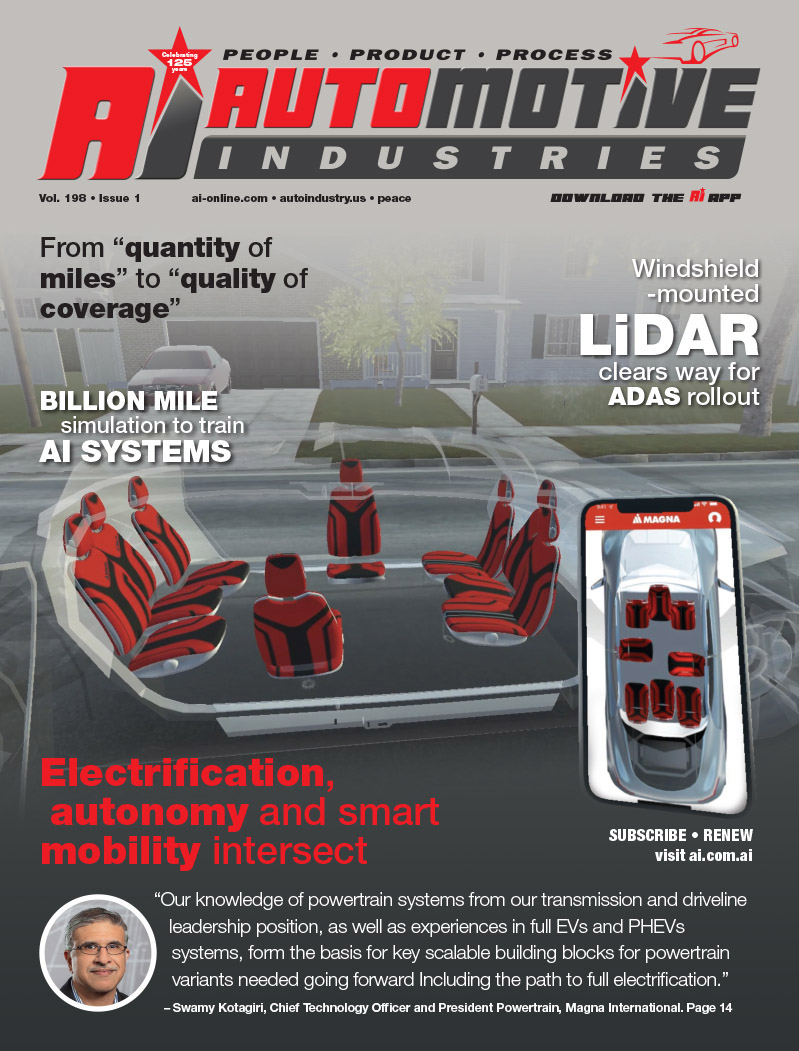
Regulators around the world are enforcing the reduction of all emissions from vehicles – with the focus being widened from the tail pipe to other sources such as the brake pads.
Automotive Industries (AI) asked Paola Salusso, Global Sales Leader BMW for ITT Corporation, what the biggest challenges are for brake designers and manufacturers in meeting OEMs technical standards and safety criteria.
Salusso: Safety criteria are definitely the first target to be met, there is no room for compromise. Starting from that point, many other OEM technical standards have to be fulfilled in order to meet performance standards under the harshest conditions. But the biggest challenge ultimately is to guarantee that safety and performance are delivered by noise-free brakes. In that sense brake pads are the one component that may help solve complex noise issues involving all axle components, which include the suspension, disc and caliper.
AI: What does your range of brake products include?
Salusso: ITT develops and manufactures brake pads for passenger cars, as well as light and heavy-duty commercial vehicles. The friction material for the brake pads is generally L-met as used in the higher speed market Europe or nonasbestos organic (NAO), which used in markets like USA or Asia.
AI: What are the main benefits of ITT’s solutions to the OEMs and end customers?
Salusso: ITT’s know-how, experience and high flexibility combine to help solve almost any problem, even within a very short time frame. This allows our customers to meet the project deadlines. ITT is also called in to solve problems which others can’t. In addition, ITT’s unique production concept makes it possible to move from the prototype stage to mass production by simply increasing the volumes, with manufacturing taking place at plants around the world.
AI. On that subject, how do you support the global needs of OEMs?
Salusso: Our main customers are global players, and we have to support them globally. In the most important markets we have set up commercial offices close to the global customers. In addition, outside of our traditional European market, we have technical centers at Novi in the United States and Wuxi in China). These provide local support to customers to ensure faster response times and quicker development of solutions to meet local challenges. We leverage on our global presence and know-how by replicating our high standard service model with the flexibility to adapt it to best fit local markets culture and needs. An example is our newest factory in China. Within two years of opening we already have a fully functional R&D structure with prototyping, dyno testing and vehicle testing departments. Testing is done by following our standard procedures and also by developing tailor-made tests and procedures that best fit local customers’ needs.
AI: Which projects/ platforms are you working on at present?
Salusso: Being one of the top five global brake pad suppliers, ITT is involved in almost all major upcoming OEM projects. But, what has changed is that there needs to be a separate approach for each of the projects. This is different to the platform projects of the past due to the fact that most vehicle manufacturers have introduced modular toolkits, which make it essential to participate from the development stage, as the decisions have far greater impact on volume production. One of the most important new platforms is the development of copper-free brake pads, which will be required by new legislation in US market starting from 2021. Thanks to its historical proactive approach, which aims at anticipating environmental, health and safety legislation requirements, ITT is today one of the leaders in copper-free brake pads technology, not only for US, but also for the European market. Mass production started in 2014 – or six years ahead of the legislative requirement.
AI: At what stage do you get involved in a project?
Salusso: The official involvement generally starts with the request for quotation (RFQ), but most of our customers start talking to us early in the design phase because of our proven range of friction materials. This gives them a higher level of confidence when introducing a new car or new brake systems. Using proven technology reduces the variables that could generate problems. As a result, customer satisfaction is higher.
AI: What new materials and technology can we expect from ITT in the future?
Salusso: ITT is continuously working on friction material improvements regarding performance, noise and wheel dust. As already mentioned, ITT has started the roll-out of the new copper-free materials, which greatly reduce environmental impact. Generally speaking, one of the major drivers of innovation in our sector over the past 20 years has been environmental, health and safety legislation. So, we expect this to remain one of the major areas of innovation in the future, with the focus on “greener” materials. At system level ITT is investigating possible contributions of our products to the major technological trends of automotive industry, such as fuel economy, active safety and diagnostics.
AI: What is your strategy for development of products for the electric vehicle market?
Salusso: We are already manufacturing brakes for electric cars. Technologically, the brake pads are not very different from standard applications. Thanks to this experience we believe that in the short term we have the technology and products required for hybrid/electric cars. In fact, the use on this kind of vehicle of new systems such as “vacuum-less boosters” or kinetic energy recovery systems (KERS) is placing the focus on particular product characteristics. Last, but not least, we have to highlight that on a full electric vehicle, noise-free solutions become even more important as there is no masking of sound by the combustion engine. So, we think there will definitely be a dedicated product.
AI: What is the key differentiator for you between the conventional cars and electric vehicles?
Salusso: Speaking about brake pads the key differentiator now is coming from new features that are affecting the overall brake system. In particular the KERS system that recovers kinetic energy during the brake application is working in a “blended” mode with a traditional brake system. This requires specific characteristics of, for example, friction levels and friction level stability. On the other hand, KERS limits the use of standard brake technology under certain conditions, which in turn increases the risk of the build-up of rust on the disc and the resultant noise or disc grooving. So, we are looking at different and dedicated product characteristics, which deliver the same levels of safety as with a traditional braking system. Looking at the medium to long term future of this type of car we can see the introduction of full electronic braking backed up by a hydraulic fail-safe system.
AI: What is the market potential?
Salusso: We are still a Europe-centric company, and over the past few years have become the main original equipment supplier in Europe. But, working in partnership with our customers, we have successfully developed brake pad solutions for markets out of Europe, such as the USA, China, and Japan. So, we intend to use our capabilities to grow outside Europe with our traditional partners – as well as with new ones.
More Stories
Acoustic sensor systems and Fraunhofer measurement technology for in practical testing ͏
OSI Systems Receives $10 Million Order for Cargo and Vehicle Inspection Systems
Mitsubishi Electric Automotive America Launches Guardian Generation 3 Trial with Seeing Machines in North America